OEE-Berechnung: Formel im Detail, Häufige Fehler & Best Practices
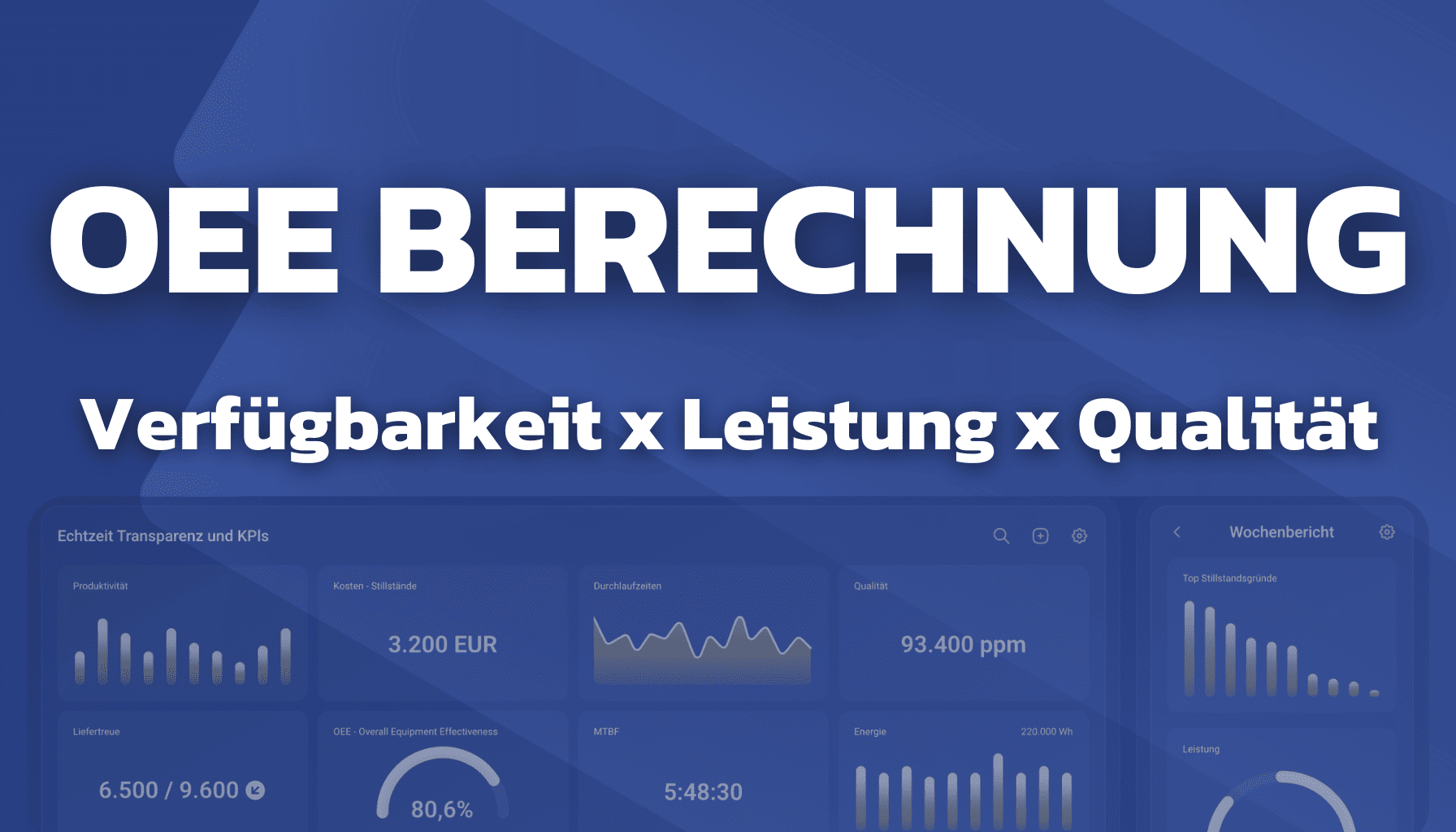
Dieser Artikel behandelt einen spezifischen Aspekt der Overall Equipment Effectiveness (OEE). Für einen umfassenden Überblick und Grundlagen zur OEE empfehlen wir unseren Hauptartikel:
Zum OEE-HauptartikelInhaltsverzeichnis
- Organisatorische Vorbereitung für die OEE-Berechnung
- Die OEE-Formel im Detail
- Verfügbarkeit berechnen
- Leistung berechnen
- Qualität berechnen
- OEE-Gesamtberechnung
- Häufige Berechnungsfehler und deren Vermeidung
- Branchenspezifische Berechnungsvarianten
- OEE-Berechnung für kontinuierliche Prozesse
- Verlustanalyse zur OEE-Optimierung
- OEE-Berechnung Industrie 4.0
- OEE Best Practices
- OEE-Berechnungstools und Software
Einleitung: Präzise OEE-Berechnung als Basis für Produktionsoptimierung
Die exakte Berechnung der OEE-Kennzahl (Gesamtanlageneffektivität) ist der Schlüssel zur systematischen Produktionsoptimierung. Anders als oberflächliche Produktionskennzahlen bietet die OEE-Berechnung einen präzisen, mathematisch fundierten Einblick in Ihre Fertigungseffizienz.
Eine korrekt durchgeführte OEE-Berechnung:
- Quantifiziert Produktionsverluste in Euro statt abstrakten Prozentwerten
- Identifiziert schleichende Leistungsabfälle bevor sie zu Ausfällen führen
- Ermöglicht datenbasierte Rüstoptimierung durch Variantenanalyse
- Liefert nachweisbare ROI-Berechnungen für Prozessoptimierungen
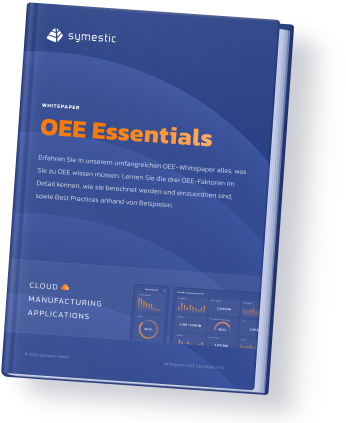
Dieser technische Leitfaden führt Sie durch jede Komponente der OEE-Berechnung mit präzisen Formeln, Praxisbeispielen und branchenspezifischen Berechnungsvarianten.
Sie erhalten das nötige mathematische und methodische Rüstzeug, um OEE als strategisches Instrument zur Produktivitätssteigerung einzusetzen.
Organisatorische Vorbereitung für die OEE-Berechnung
Bevor Sie in die OEE berechnen können, müssen einige organisatorische Voraussetzungen geschaffen werden:
1. Datenerfassungsstrategie definieren
Entscheiden Sie zwischen manueller und automatischer Datenerfassung:
Erfassungsmethode | Vorteile | Nachteile | Typische Anwendung |
---|---|---|---|
Manuell (Papierformulare) | Geringe Initialkosten | Fehleranfällig, zeitverzögert | Kleine Betriebe, Pilotprojekte |
Teilautomatisiert (Tablets) | Schnellere Erfassung | Bedarf an digitaler Infrastruktur | Mittelständische Produktion |
Vollautomatisiert (IoT-Sensoren) | Echtzeitdaten, Mikrostillstände erfassbar | Höhere Investitionskosten | Großserienfertigung, Industrie 4.0 |
2. Pilot-Anlage auswählen
Wählen Sie für Ihre erste OEE-Berechnung idealerweise:
- Einen Engpass im Produktionsprozess (Bottleneck)
- Eine repräsentative Maschine mit typischen Verlustquellen
- Eine Anlage mit wirtschaftlicher Bedeutung für Ihren Betrieb
3. Berechungsperiode festlegen
Die Auswahl der Berechnungsperiode beeinflusst direkt die Aussagekraft Ihrer OEE-Ergebnisse:
Berechnungsperiode | Typische Anwendung | Zu beachten |
---|---|---|
Schicht | Tägliches Shopfloor-Management | Hohe Datengranularität, zeigt Bedienereinflüsse |
Tag | Produktionsleitung, tägliche Steuerung | Guter Kompromiss zwischen Detail und Übersicht |
Woche | Mittelfristige Optimierung | Glättet Tageschwankungen |
Monat | Management-Reporting | Trends erkennbar, Details gehen verloren |
4. OEE-Team zusammenstellen
Ein effektives OEE-Berechnungsteam umfasst idealerweise:
- Produktionsleiter (Prozessverantwortung)
- Anlagenbediener (praktische Erfahrung)
- Instandhalter (technisches Know-how)
- Qualitätsverantwortlicher (für Qualitätsdaten)
- IT-Spezialist (bei automatisierter Datenerfassung)
OEE in Echtzeit erfassen und visualisieren
Vom Kennzahlen-Wirrwarr zum übersichtlichen Dashboard: So gelingt die professionelle OEE-Datenerfassung
Von der Theorie zur Praxis:
- Automatisierte Datenerfassung direkt an der Maschine
- Echtzeit-Berechnung aller OEE-Faktoren
- Anpassbare Dashboards für verschiedene Nutzergruppen
- Verlaufsanalysen für bessere Optimierungsentscheidungen
Die OEE-Formel im Detail: Technisches Fundament
Die OEE-Berechnung basiert auf einer multiplikativen Verknüpfung der drei Kernfaktoren:
Diese mathematische Struktur hat entscheidende Implikationen:
-
Multiplikativer Zusammenhang: Durch die Multiplikation verstärken sich Defizite in den einzelnen Faktoren. Dies macht die OEE besonders sensitiv für Schwachstellen.
-
Mathematische Eigenschaften:
- OEE-Wert liegt immer zwischen 0 und 1 (bzw. 0% und 100%)
- Der OEE-Wert kann nie höher sein als der niedrigste Einzelfaktor
- Ein OEE-Wert über 100% ist mathematisch unmöglich und weist auf Berechnungsfehler hin
- Die detaillierten Formeln:
OEE = Verfügbarkeit × Leistung × Qualität
Verfügbarkeit = Tatsächliche Betriebszeit / Geplante Produktionszeit
Leistung = (Ideale Zykluszeit × Produzierte Stückzahl) / Tatsächliche Betriebszeit
Qualität = Gut-Teile / Produzierte Stückzahl
Beispielberechnung mit Zahlen
Ein produzierendes Unternehmen hat folgende Werte ermittelt:
- Geplante Produktionszeit: 480 Minuten (8 Stunden)
- Stillstandszeit: 60 Minuten
- Ideale Zykluszeit: 2 Minuten pro Teil
- Produzierte Teile: 180 Stück
- Fehlerfreie Teile: 171 Stück
Die OEE-Berechnung erfolgt in drei Schritten:
Schritt 1: Verfügbarkeit berechnen
Verfügbarkeit = (480 - 60) / 480 = 420 / 480 = 0,875 = 87,5%
Schritt 2: Leistung berechnen
Idealer Output = 420 / 2 = 210 Teile
Leistung = 180 / 210 = 0,857 = 85,7%
Schritt 3: Qualität berechnen
Qualität = 171 / 180 = 0,95 = 95%
OEE-Gesamtberechnung
OEE = 0,875 × 0,857 × 0,95 = 0,712 = 71,2%
Dieser Wert von 71,2% zeigt, dass die Anlage nur knapp über 70% ihrer theoretischen Kapazität erreicht.
Verfügbarkeit berechnen: Technische Detailanleitung
Der Verfügbarkeitsfaktor ist mathematisch definiert als:
Verfügbarkeit = Tatsächliche Betriebszeit / Geplante Produktionszeit
Exakte Definition der Zeitkomponenten
Für eine präzise Berechnung müssen die Zeitkomponenten exakt definiert werden:
- Kalenderzeit: Gesamte verfügbare Zeit (24 Stunden × 7 Tage)
- Betriebszeit: Zeit, in der die Anlage besetzt ist (z.B. 3-Schicht-Betrieb)
- Geplante Produktionszeit: Betriebszeit abzüglich geplanter Stillstände
- Tatsächliche Betriebszeit: Geplante Produktionszeit abzüglich ungeplanter Stillstände
Stillstandskategorisierung für die Verfügbarkeitsberechnung
Eine präzise Kategorisierung der Stillstände ist entscheidend:
Stillstandstyp | Einfluss auf Verfügbarkeit | Beispiele | Erfassungsmethode |
---|---|---|---|
Geplante Stillstände | Nicht in Berechnung einbezogen | Wartung, Schichtwechsel, Pausen | Arbeitsplan, Schichtplan |
Ungeplante Stillstände >5 Min | Reduzieren Verfügbarkeit | Maschinenausfälle, Materialengpässe | Störmeldungen, Stillstandsprotokoll |
Mikrostillstände <5 Min | Je nach Definition | Materialstaus, Kleineinstellungen | Automatische IoT-Erfassung |
Rüstzeiten | Abhängig von Definition | Werkzeugwechsel, Umrüstung | Rüstprotokoll, MES-System |
Schichtlänge: 480 Minuten (8 Stunden)
Geplante Pausen: 30 Minuten
Geplante Wartung: 20 Minuten
Geplante Produktionszeit: 480 - 30 - 20 = 430 Minuten
Ungeplante Stillstände:
- Maschinenausfall: 35 Minuten
- Materialengpass: 18 Minuten
- Werkzeugbruch: 12 Minuten
Summe ungeplanter Stillstand: 65 Minuten
Tatsächliche Betriebszeit: 430 - 65 = 365 Minuten
Verfügbarkeit = 365 / 430 = 0,849 = 84,9%
Häufige Fehlerquellen bei der Verfügbarkeitsberechnung
-
Nichterfassung von Mikrostillständen: In einer Schicht können fünfzig 3-Minuten-Stops einen Gesamtverlust von 150 Minuten bedeuten, die bei manueller Erfassung oft unentdeckt bleiben.
-
Falsche Zuordnung geplanter Stillstände: Wartungszeiten werden manchmal fälschlicherweise als ungeplante Stillstände kategorisiert, was die Verfügbarkeit künstlich verschlechtert.
-
Inkonsistente Definitionen der Rüstzeiten: Je nach Unternehmen werden Rüstzeiten unterschiedlich behandelt. Wichtig ist eine konsistente Definition.
Technische Optimierung der Verfügbarkeitserfassung
OEE in Echtzeit erfassen und visualisieren
Vom Kennzahlen-Wirrwarr zum übersichtlichen Dashboard: So gelingt die professionelle OEE-Datenerfassung
Von der Theorie zur Praxis:
- Automatisierte Datenerfassung direkt an der Maschine
- Echtzeit-Berechnung aller OEE-Faktoren
- Anpassbare Dashboards für verschiedene Nutzergruppen
- Verlaufsanalysen für bessere Optimierungsentscheidungen
-
IoT-Sensorik für Echtzeiterfassung: Automatische Erfassung von Maschinensignalen ermöglicht die Identifikation von Mikrostillständen ab 3 Sekunden.
-
Stillstandskodierung: Implementieren Sie ein standardisiertes Kodierungssystem für Stillstandsursachen (z.B. technisch, organisatorisch, material- oder personalbezogen).
-
OEE-Dashboards: Visualisieren Sie Stillstandszeiten in Echtzeit, um sofortige Reaktionen zu ermöglichen.
Leistung berechnen: Exakte Bestimmung des Geschwindigkeitsfaktors
Der Leistungsfaktor misst, wie nahe die tatsächliche Produktionsgeschwindigkeit an der theoretisch möglichen liegt:
Leistung = (Ideale Zykluszeit × Produzierte Stückzahl) / Tatsächliche Betriebszeit
Alternativ kann die Formel auch umgestellt werden:
Leistung = Tatsächliche Produktionsrate / Ideale Produktionsrate
Bestimmung der idealen Zykluszeit
Die korrekte Bestimmung der idealen Zykluszeit ist entscheidend für eine realistische Leistungsberechnung:
Methode | Beschreibung | Vor- und Nachteile |
---|---|---|
Herstellerangaben | Technische Daten des Maschinenherstellers | Oft zu optimistisch, berücksichtigt keine Betriebsbedingungen |
Design-Kapazität | Ausgelegter Durchsatz der Anlage | Realitätsnäher, aber ohne Betriebseinflüsse |
Best-Demonstrated-Performance | Bestleistung unter realen Bedingungen | Realistisch, aber evtl. nicht dauerhaft erreichbar |
Statistische Analyse | Erfassung der schnellsten 10% der Zyklen | Wissenschaftlicher Ansatz, praxisnah |
Empfohlener Ansatz: Kombinieren Sie Best-Demonstrated-Performance mit statistischer Analyse und verifizieren Sie die Ergebnisse durch Zeitstudien.
Leistungsberechnung mit Zeiteinheiten
Die Leistungsberechnung kann mit verschiedenen Zeiteinheiten durchgeführt werden:
Tatsächliche Betriebszeit: 6,5 Stunden (390 Minuten)
Ideale Zykluszeit: 30 Sekunden pro Teil = 0,5 Minuten = 0,00833 Stunden
Produzierte Teile: 650 Stück
Leistung = (0,00833 × 650) / 6,5 = 5,41 / 6,5 = 0,832 = 83,2%
Tatsächliche Betriebszeit: 390 Minuten = 23.400 Sekunden
Ideale Zykluszeit: 30 Sekunden pro Teil
Produzierte Teile: 650 Stück
Leistung = (30 × 650) / 23.400 = 19.500 / 23.400 = 0,833 = 83,3%
Die minimale Abweichung (83,2% vs. 83,3%) zeigt die Bedeutung einer konsistenten Verwendung von Zeiteinheiten.
Besonderheiten bei der Leistungsberechnung
-
Produktmix-Einfluss: Bei verschiedenen Produkten mit unterschiedlichen Zykluszeiten muss eine gewichtete Berechnung erfolgen:
BeispielProdukt A: 400 Teile, ideale Zykluszeit 30 Sekunden
Produkt B: 250 Teile, ideale Zykluszeit 45 Sekunden
Gesamte ideale Produktionszeit = (400 × 30) + (250 × 45) = 12.000 + 11.250 = 23.250 Sekunden
Leistung = 23.250 / Tatsächliche Betriebszeit in Sekunden -
Leistungswerte über 100%: Ein Leistungswert über 100% ist ein klares Indiz für eine zu niedrig angesetzte ideale Zykluszeit. In diesem Fall sollte die Referenzzeit überprüft und angepasst werden.
-
Dynamische Geschwindigkeitsanpassung: Bei Anlagen mit variabler Geschwindigkeit (z.B. abhängig von Materialien oder Temperatur) kann die ideale Zykluszeit schwanken. Hier ist eine dynamische Berechnung basierend auf aktuellen Bedingungen notwendig.
Tatsächliche Betriebszeit: 405 Minuten = 24.300 Sekunden
Ideale Zykluszeit: 4 Sekunden pro Verpackung
Produzierte Verpackungen: 5.000 Stück
Idealer Output in 24.300 Sekunden = 24.300 / 4 = 6.075 Verpackungen
Leistung = 5.000 / 6.075 = 0,823 = 82,3%
Alternativ mit direkter Formel:
Leistung = (4 × 5.000) / 24.300 = 20.000 / 24.300 = 0,823 = 82,3%
Technische Optimierung der Leistungserfassung
-
Automatische Taktzeiterfassung: Implementieren Sie Sensoren, die Zykluszeiten in Echtzeit messen und Variationen erkennen.
-
Statistische Prozessgrenzen: Definieren Sie obere und untere Kontrollgrenzen für Zykluszeiten, um abnormale Geschwindigkeitsschwankungen zu identifizieren.
-
Leistungstrend-Analyse: Überwachen Sie die Entwicklung der Leistung über Zeit, um schleichende Verschlechterungen frühzeitig zu erkennen.
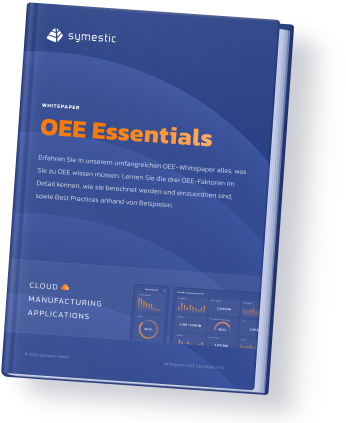
Qualität berechnen: Präzise Erfassung fehlerfreier Produktion
Der Qualitätsfaktor quantifiziert den Anteil der fehlerfreien Produktion an der Gesamtproduktion:
Qualität = Anzahl guter Teile / Gesamtanzahl produzierter Teile
Die Qualitätskomponente der OEE unterscheidet sich von klassischen Qualitätskennzahlen durch ihren Fokus auf Ausschuss und Nacharbeit direkt am Entstehungsort.
Präzise Definition von "guten Teilen"
Für eine exakte Qualitätsberechnung ist die Definition von "guten Teilen" entscheidend:
Kategorie | Für OEE-Berechnung | Begründung |
---|---|---|
Fehlerfreie Teile | Zählen als "gut" | Entsprechen Qualitätsanforderungen ohne Nacharbeit |
Teile mit Nacharbeit | Zählen NICHT als "gut" | Verursachen zusätzlichen Ressourceneinsatz |
Ausschuss | Zählen NICHT als "gut" | Vollständiger Verlust der Wertschöpfung |
Werkzeugteile/Muster | Je nach Definition | Klare Regelung erforderlich |
Berechnung mit unterschiedlichen Qualitätsverlusten
Eine differenzierte Qualitätsberechnung unterscheidet zwischen verschiedenen Arten von Qualitätsverlusten:
Gesamte Produktion: 1.000 Teile
Fehlerfreie Teile: 940 Teile
Nacharbeit: 35 Teile
Ausschuss: 25 Teile
Qualität = 940 / 1.000 = 0,94 = 94%
Alternativ kann die Berechnung auch über die Verluste erfolgen:
Qualität = (1.000 - 35 - 25) / 1.000 = 940 / 1.000 = 0,94 = 94%
Zeitpunkt der Qualitätskontrolle
Der Zeitpunkt der Qualitätskontrolle beeinflusst die OEE-Berechnung entscheidend:
Kontrollzeitpunkt | Auswirkung auf OEE-Berechnung | Zu beachten |
---|---|---|
Direkt nach Produktion | Zeitnahe Daten, direkte Rückkopplung | Nicht alle Fehler sofort erkennbar |
Nach Zwischenlagerung | Umfassendere Qualitätsbewertung | Zeitverzögerung bei der Berechnung |
Nach weiteren Prozessschritten | Spätere Fehlerentdeckung | Komplexe Ursachenzuordnung |
Best Practice: Implementieren Sie ein mehrstufiges Qualitätssystem, das sowohl direkte als auch nachgelagerte Kontrollen umfasst, und definieren Sie klar, welche Daten in die OEE-Berechnung einfließen.
Qualitätsberechnung bei kontinuierlichen Prozessen
Bei kontinuierlichen Prozessen (z.B. Chemie, Papierherstellung) wird die Qualität anders berechnet:
Qualität = Menge in Spezifikation / Gesamte produzierte Menge
Beispiel:
Gesamtproduktion: 10.000 Liter
Spezifikationsgerechte Produktion: 9.700 Liter
Qualität = 9.700 / 10.000 = 0,97 = 97%
Gesamtproduktion: 5.000 Leiterplatten
Fehlerfreie Leiterplatten: 4.800
Leiterplatten mit Lötfehlern (Ausschuss): 150
Leiterplatten mit reparierbaren Defekten (Nacharbeit): 50
Qualität = 4.800 / 5.000 = 0,96 = 96%
Häufige Fehlerquellen bei der Qualitätsberechnung
-
Einbeziehung von Nacharbeit als "gute Teile": Nacharbeit verursacht zusätzliche Kosten und sollte als Qualitätsverlust betrachtet werden.
-
Fehlende Rückverfolgbarkeit von Qualitätsproblemen: Ohne klare Ursachenzuordnung ist keine gezielte Verbesserung möglich.
-
Zeitliche Verzögerung bei der Qualitätserfassung: Qualitätsdaten müssen zeitnah in die OEE-Berechnung einfließen, um aussagekräftige Ergebnisse zu liefern.
OEE-Gesamtberechnung und Interpretation der Ergebnisse
Die Multiplikation der drei Faktoren ergibt den OEE-Wert:
OEE = Verfügbarkeit × Leistung × Qualität
OEE-Berechnung im Detail
Aus unseren vorherigen Beispielen:
- Verfügbarkeit: 84,9%
- Leistung: 82,3%
- Qualität: 96%
OEE = 0,849 × 0,823 × 0,96 = 0,671 = 67,1%
Interpretation von OEE-Werten
OEE-Wert | Bewertung | Typische Ursachen | Handlungsempfehlung |
---|---|---|---|
<60% | Unterdurchschnittlich | Erhebliche Verluste in mehreren Faktoren | Umfassende Analyse aller Faktoren, Priorität auf größten Verlustfaktor |
60-75% | Durchschnittlich | Typisch für viele Unternehmen ohne systematische OEE-Optimierung | Gezielte Verbesserung des schwächsten Faktors |
75-85% | Gut | Etablierte Verbesserungsprozesse | Feinoptimierung und standardisierte Prozesse |
>85% | Weltklasse | Hochentwickelte Prozesse mit kontinuierlicher Optimierung | Stabilisierung und Standardisierung der Prozesse |
Branchenspezifische Benchmarks
Die folgende Tabelle zeigt typische OEE-Benchmark-Werte für verschiedene Industriezweige:
Industriezweig | Unterdurchschnittlich | Durchschnittlich | Gut | Weltklasse |
---|---|---|---|---|
Automobilindustrie | < 70% | 70-85% | 85-90% | > 90% |
Prozessindustrie (kontinuierlich) | < 75% | 75-85% | 85-90% | > 90% |
Maschinenbau | < 60% | 60-75% | 75-85% | > 85% |
Kunststoff | < 65% | 65-80% | 80-85% | > 85% |
Lebensmittel | < 60% | 60-75% | 75-80% | > 80% |
Pharmaindustrie | < 60% | 60-70% | 70-80% | > 80% |
Metallverarbeitung | < 55% | 55-70% | 70-80% | > 80% |
Druckindustrie | < 50% | 50-65% | 65-75% | > 75% |
Priorisierung von Verbesserungsmaßnahmen
Ein wichtiger Aspekt der OEE-Berechnung ist die Priorisierung von Verbesserungsmaßnahmen basierend auf den Ergebnissen:
-
Pareto-Analyse der Verluste: Identifizieren Sie die Hauptverlustquellen nach dem 80/20-Prinzip.
-
Vergleich der Faktoren: In unserem Beispiel ist die Leistung mit 82,3% der schwächste Faktor, sollte also zuerst optimiert werden.
-
ROI-Analyse: Berechnen Sie die finanziellen Auswirkungen von Verbesserungen:
Bei einer Anlage mit 2.000 Betriebsstunden/Jahr und einem Maschinenstundensatz von 250€:
- Aktueller OEE: 67,1%
- Ziel-OEE nach Verbesserung: 75%
- Differenz: 7,9%
Zusätzliche produktive Zeit: 2.000 × 0,079 = 158 Stunden/Jahr
Finanzieller Vorteil: 158 × 250€ = 39.500€/Jahr
Häufige Berechnungsfehler und deren Vermeidung
Bei der OEE-Berechnung treten regelmäßig spezifische Fehler auf, die zu ungenauen oder irreführenden Ergebnissen führen können:
1. Unrealistische Annahme der idealen Zykluszeit
Problem: Die ideale Zykluszeit wird oft aus Herstellerangaben übernommen, die unter Laborbedingungen ermittelt wurden. Dies führt häufig zu Leistungswerten über 100%, was mathematisch unmöglich ist.
Laut Hersteller: 3 Sekunden pro Teil
Realistische Zykluszeit: 4 Sekunden pro Teil
Bei Verwendung der Herstellerangabe:
Leistung = (3 × 1.000) / 3.300 = 0,909 = 90,9%
Bei 3,5-Sekunden-Zyklen in der Realität:
Tatsächliche Leistung = (4 × 1.000) / 3.300 = 1,212 = 121,2% (unmöglich!)
Lösung:
- Bestimmen Sie die ideale Zykluszeit durch Tests unter realen Produktionsbedingungen
- Nutzen Sie statistische Methoden: Durchschnitt der besten 10% aller gemessenen Zykluszeiten
- Verwenden Sie Best-Demonstrated-Performance unter normalen Betriebsbedingungen
2. Unvollständige Erfassung von Stillständen
Problem: Mikrostillstände (unter 5 Minuten) werden bei manueller Erfassung oft übersehen, summieren sich aber zu erheblichen Verlusten.
50 Mikrostillstände à 3 Minuten = 150 Minuten Gesamtverlust (2,5 Stunden!)
Bei geplanter Produktionszeit von 8 Stunden sind das 31,25% Verfügbarkeitsverlust
Lösung:
- Implementieren Sie automatisierte Datenerfassung, die auch kurze Stillstände registriert
- Schulen Sie Mitarbeiter in der korrekten Erfassung auch kurzer Unterbrechungen
- Nutzen Sie IoT-Sensoren zur automatischen Erfassung von Stillständen ab 3 Sekunden
3. Falsche Behandlung von Rüstzeiten
Problem: Rüstzeiten werden in verschiedenen Unternehmen unterschiedlich in die OEE-Berechnung einbezogen.
Variante 1: Rüsten ist geplante Nicht-Produktionszeit → nicht in OEE einbezogen
Variante 2: Rüsten ist ungeplanter Stillstand → reduziert Verfügbarkeit
Variante 3: Nur Rüstzeiten über Standard-Rüstzeit reduzieren Verfügbarkeit
Lösung:
- Definieren Sie klar, wie Rüstzeiten in Ihrer OEE-Berechnung behandelt werden
- Verwenden Sie konsequent dieselbe Definition im gesamten Unternehmen
- Dokumentieren Sie den Ansatz, um Vergleichbarkeit zu gewährleisten
4. Fehlerhafte Einbeziehung von Nacharbeit in die Qualitätsberechnung
Problem: Nachgearbeitete Teile werden fälschlicherweise als "gute Teile" gezählt, was die Qualitätskomponente verfälscht.
1.000 produzierte Teile
900 sofort fehlerfreie Teile
80 Teile mit Nacharbeit
20 Teile Ausschuss
Falsche Berechnung: Qualität = (900 + 80) / 1.000 = 0,98 = 98%
Korrekte Berechnung: Qualität = 900 / 1.000 = 0,9 = 90%
Lösung:
- Zählen Sie nur Teile, die im ersten Durchlauf fehlerfrei sind, als "gut"
- Erfassen Sie Nacharbeit separat als Qualitätsverlust
- Implementieren Sie First Pass Yield (FPY) als ergänzende Kennzahl
5. Inkonsistente Zeitbasis bei der Berechnung
Problem: Die Verwendung unterschiedlicher Zeiteinheiten (Stunden, Minuten, Sekunden) kann zu Berechnungsfehlern führen.
Betriebszeit: 390 Minuten
Zykluszeit: 45 Sekunden
Falsche Berechnung mit gemischten Einheiten:
Leistung = (45 × 500) / 390 = 57,7 (Unsinn!)
Korrekte Berechnung mit einheitlichen Zeitmaßen:
Leistung = (45 × 500) / (390 × 60) = 0,962 = 96,2%
Lösung:
- Verwenden Sie konsistent dieselbe Zeiteinheit, idealerweise Sekunden
- Implementieren Sie automatisierte Berechnungstools zur Vermeidung von Umrechnungsfehlern
- Prüfen Sie ungewöhnliche Ergebnisse auf mögliche Zeiteinheitenfehler
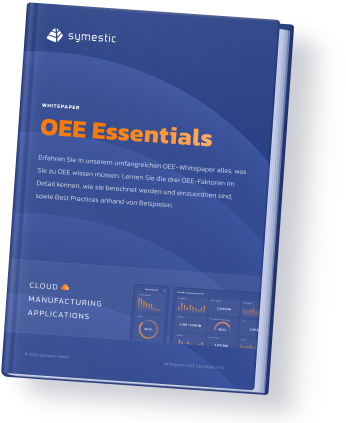
Branchenspezifische Berechnungsvarianten
Die OEE-Berechnung muss an die spezifischen Anforderungen verschiedener Branchen angepasst werden, um aussagekräftige Ergebnisse zu liefern.
Automobilindustrie
In der Automobilfertigung mit komplexen Linien und taktgebundenen Prozessen sind folgende Anpassungen üblich:
Leistung = Gesamtoutput / (Engpass-Stationskapazität × Betriebszeit)
Besonderheiten:
- Qualitätsberechnung berücksichtigt unterschiedliche Fehlerklassen mit Gewichtung
- Verfügbarkeit wird oft auf Engpassstation (Bottleneck) fokussiert
- JIT-Produktion erfordert Berücksichtigung von Materialverfügbarkeit
Prozessindustrie (Chemie, Papier, Stahl)
In kontinuierlichen Prozessen ohne diskrete Teile:
Leistung = Tatsächlicher Durchsatz / Nomineller maximaler Durchsatz
Besonderheiten:
- Qualität wird über Spezifikationsgrenzen definiert (in Spezifikation vs. außerhalb)
- Verfügbarkeit berücksichtigt auch Teillastbetrieb
- Grade-Wechsel (Produktwechsel) werden anders bewertet als komplette Stillstände
Lebensmittel- und Getränkeindustrie
In der Lebensmittelindustrie mit hohen Hygienestandards:
Verfügbarkeit = Betriebszeit / (Schichtzeit - Reinigungszeit)
Besonderheiten:
- Regelmäßige Reinigungszyklen (CIP, Clean-in-Place) werden als geplante Nicht-Produktion definiert
- Qualität umfasst neben Produktfehlern auch mikrobiologische Parameter
- Haltbarkeitsdaten beeinflussen die Definition von "guten Produkten"
Pharmaindustrie
In der stark regulierten Pharmaproduktion:
Qualität = (Produzierte Menge - Ausschuss - Abweichungen - Quarantäne) / Produzierte Menge
Besonderheiten:
- Validierungsläufe werden aus der OEE-Berechnung ausgeschlossen
- Dokumentationszeit wird als produktiver Teil des Prozesses betrachtet
- Qualitätsprüfungen mit Freigabeprozessen erfordern zeitverzögerte OEE-Berechnung
OEE-Berechnung für kontinuierliche Prozesse
Kontinuierliche Fertigungsprozesse (z.B. in der Chemie-, Papier- oder Stahlindustrie) erfordern eine angepasste OEE-Berechnung, da hier keine diskreten Einheiten produziert werden.
Angepasste Formeln für kontinuierliche Prozesse
Verfügbarkeit: Die Berechnung bleibt grundsätzlich gleich, berücksichtigt aber auch Teillastbetrieb:
Verfügbarkeit = Produktive Zeit / Geplante Produktionszeit
Leistung = Tatsächlicher Durchsatz / Maximaler Durchsatz
Qualität = Menge innerhalb Spezifikation / Gesamtproduzierte Menge
Praktisches Berechnungsbeispiel: Papierherstellung
Geplante Produktionszeit: 24 Stunden
Stillstände: 2,5 Stunden
Teillastbetrieb (75%): 4 Stunden
Maximaler Durchsatz: 25 Tonnen/Stunde
Durchschnittlicher Durchsatz während Vollbetrieb: 22 Tonnen/Stunde
Durchschnittlicher Durchsatz während Teillastbetrieb: 18 Tonnen/Stunde
Gesamtproduktion: 22 × 17,5 + 18 × 4 = 385 + 72 = 457 Tonnen
Theoretische Maximalproduktion: 25 × 21,5 = 537,5 Tonnen
Außerhalb Spezifikation: 23 Tonnen
Verfügbarkeit = 21,5 / 24 = 0,896 = 89,6%
Leistung = 457 / 537,5 = 0,85 = 85%
Qualität = (457 - 23) / 457 = 0,95 = 95%
OEE = 0,896 × 0,85 × 0,95 = 0,724 = 72,4%
Besonderheiten bei kontinuierlichen Prozessen
- Teillastbetrieb: Bei reduzierter Geschwindigkeit wird entweder:
- als Leistungsverlust berechnet (Verfügbarkeit = 100%, Leistung reduziert)
- oder als Verfügbarkeitsverlust (Verfügbarkeit reduziert, Leistung = 100%) - Produktwechsel (Grade-Change): Übergangsphasen zwischen Produktvarianten werden je nach Definition als:
- Geplanter Stillstand (nicht in OEE einbezogen)
- Leistungsverlust (reduzierte Geschwindigkeit während Umstellung)
- Qualitätsverlust (Übergangsprodukt außerhalb Spezifikation) - Messfrequenz: Kontinuierliche Prozesse erfordern kontinuierliche oder hochfrequente Messungen:
- Durchflussmesser für Volumen/Gewicht
- Inline-Qualitätssensoren für Echtzeitdaten
- Prozesssteuerungssysteme (DCS) als Datenquelle
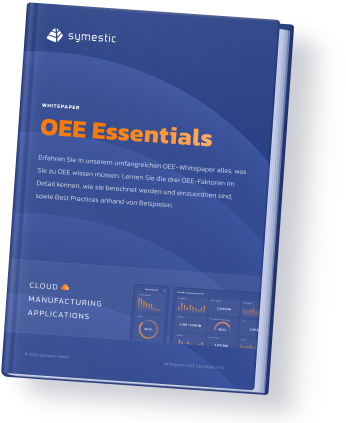
Die Big Six Losses: Verlustanalyse zur OEE-Optimierung
Die "Six Big Losses" sind die sechs Hauptverlustquellen, die die OEE negativ beeinflussen. Diese systematische Kategorisierung hilft, Verbesserungspotenziale gezielt zu identifizieren und zu quantifizieren.
Überblick: Die Six Big Losses und ihre Zuordnung
Verlustquelle | OEE-Faktor | Typische Ursachen | Typisches Optimierungspotenzial |
---|---|---|---|
1. Anlagenausfälle | Verfügbarkeit | Technische Defekte, Werkzeugbruch | 5-20% Verbesserung |
2. Rüst- und Einstellzeiten | Verfügbarkeit | Produktwechsel, Werkzeugwechsel | 10-30% Verbesserung |
3. Kurze Stillstände | Leistung | Materialstaus, kleine Störungen | 5-15% Verbesserung |
4. Reduzierte Geschwindigkeit | Leistung | Suboptimale Einstellungen, Verschleiß | 5-25% Verbesserung |
5. Anlaufverluste | Qualität | Instabile Prozesse nach Neustart | 1-5% Verbesserung |
6. Qualitätsverluste | Qualität | Prozessschwankungen, Materialfehler | 2-10% Verbesserung |
Detaillierte Berechnungsmethoden für die Big Six Losses
1. Anlagenausfälle
Anlagenausfallverlust (%) = (Ausfallzeit / Geplante Produktionszeit) × 100
Beispiel:
Ausfallzeit: 85 Minuten
Geplante Produktionszeit: 480 Minuten
Verlust = (85 / 480) × 100 = 17,7%
2. Rüst- und Einstellzeiten
Rüstzeitverlust (%) = (Rüstzeit / Geplante Produktionszeit) × 100
Beispiel:
Rüstzeit: 45 Minuten
Geplante Produktionszeit: 480 Minuten
Verlust = (45 / 480) × 100 = 9,4%
3. Kurze Stillstände
Kurzstillstandsverlust (%) = (Anzahl Teile bei idealer Geschwindigkeit ohne Kurzstillstände -
Tatsächlich produzierte Teile) / Anzahl Teile bei idealer Geschwindigkeit
Beispiel:
Ideale Produktion ohne Kurzstillstände: 5.000 Teile
Tatsächliche Produktion: 4.600 Teile
Verlust = (5.000 - 4.600) / 5.000 = 0,08 = 8%
4. Reduzierte Geschwindigkeit
Geschwindigkeitsverlust (%) = (Ideale Zykluszeit × Produzierte Teile) / Netto-Betriebszeit - 1
Beispiel:
Ideale Zykluszeit: 30 Sekunden
Produzierte Teile: 800
Netto-Betriebszeit: 450 Minuten = 27.000 Sekunden
Verlust = (30 × 800) / 27.000 - 1 = 24.000 / 27.000 - 1 = 0,889 - 1 = -0,111 = 11,1%
5. Anlaufverluste
Anlaufverlust (%) = Anzahl Ausschussteile während Anlauf / Gesamte produzierte Teile während Betriebszeit
Beispiel:
Ausschuss während Anlauf: 25 Teile
Gesamtproduktion: 1.200 Teile
Verlust = 25 / 1.200 = 0,021 = 2,1%
6. Qualitätsverluste während stabiler Produktion
Qualitätsverlust (%) = (Ausschuss + Nacharbeit während stabiler Produktion) /
Gesamte produzierte Teile
Beispiel:
Ausschuss während stabiler Produktion: 20 Teile
Nacharbeit: 35 Teile
Gesamtproduktion: 1.200 Teile
Verlust = (20 + 35) / 1.200 = 55 / 1.200 = 0,046 = 4,6%
Verlustdiagnose mit Pareto-Analyse
Die Pareto-Analyse hilft, die bedeutendsten Verlustquellen zu identifizieren und Optimierungsmaßnahmen zu priorisieren:
- Erfassen Sie alle Verluste über einen repräsentativen Zeitraum
- Sortieren Sie die Verluste nach ihrer Größe (absteigend)
- Berechnen Sie die kumulativen Prozentwerte
- Konzentrieren Sie sich auf die wenigen Verlustarten, die 80% der Gesamtverluste ausmachen
Beispiel:
Verlustanalyse einer Verpackungslinie:
- Kurze Stillstände: 12% (Materialstaus)
- Anlagenausfälle: 8% (Defekte Förderbänder)
- Rüstzeiten: 7% (Formatwechsel)
- Reduzierte Geschwindigkeit: 6% (Verschlissene Lager)
- Qualitätsverluste: 3% (Fehlklebungen)
- Anlaufverluste: 1% (Instabile Parameter)
Top-2-Verluste (Kurzstillstände und Anlagenausfälle) verursachen bereits 20% von 37% Gesamtverlust = 54% der Verluste
OEE-Berechnung im Kontext von Industrie 4.0
Die digitale Transformation und Industrie 4.0-Technologien revolutionieren die OEE-Berechnung durch Echtzeitdaten, automatisierte Analysen und prädiktive Funktionen.
IoT-basierte OEE-Datenerfassung
Moderne IoT-Sensoren liefern hochpräzise Echtzeit-Daten für eine exakte OEE-Berechnung:
Datentyp | Erfassungsmethode | Vorteile | Auswirkung auf OEE-Berechnung |
---|---|---|---|
Maschinenzustände | SPS-Anbindung, I/O-Signale | Automatisierte Erfassung ohne Benutzereingriffe | Präzise Verfügbarkeitsberechnung mit Mikrostillständen |
Taktzeiterfassung | Lichtschranken, Näherungssensoren | Hohe Genauigkeit, echtzeitnahe Datenerfassung | Exakte Leistungsberechnung in Echtzeit |
Stückzahlerfassung | Vision-Systeme, RFID-Tracking | Automatische Zählung und Identifikation | Genaue Input/Output-Messung für Qualitätsberechnung |
Prozessparameter | Temperatur-, Druck-, Vibrationssensoren | Kontinuierliche Überwachung kritischer Parameter | Frühwarnsystem für Qualitäts- und Leistungsprobleme |
Technisches Setup:
Maschinensignal → Edge-Device → OEE-Software → Dashboards
Wichtige Schnittstellen:
- OPC UA für standardisierte Maschinenkommunikation
- MQTT für leichtgewichtige IoT-Kommunikation
- REST-APIs für Integration mit übergeordneten Systemen
Machine Learning für präzisere OEE-Berechnungen
KI-Algorithmen verbessern die OEE-Berechnung durch intelligente Musterkennung:
-
Automatische Stillstandskategorisierung: ML-Algorithmen klassifizieren Stillstände automatisch basierend auf Mustern und Signalen, was manuelle Eingaben reduziert.
-
Dynamische Anpassung idealer Zykluszeiten: Selbstlernende Systeme passen ideale Zykluszeiten basierend auf Produktvarianten, Materialien und Umgebungsbedingungen an.
-
Präzisere Qualitätsvorhersage: Predictive Quality nutzt Prozessparameter, um Qualitätsprobleme vorherzusagen, bevor sie auftreten.
Beispiel:
Traditionelle Berechnung:
Feste ideale Zykluszeit für Produkt A: 45 Sekunden
ML-optimierte Berechnung:
Dynamische ideale Zykluszeit für Produkt A mit Material X bei Temperatur Y: 42,3 Sekunden
Cloud-basierte OEE-Berechnung für globale Produktionsnetzwerke
Cloud-Plattformen ermöglichen standortübergreifende OEE-Analysen:
Architektur:
Lokale Datenerfassung → Edge-Computing (Vorverarbeitung) → Cloud-Plattform → Globale Dashboards
Vorteile:
- Globale Standardisierung der OEE-Berechnung
- Standortübergreifendes Benchmarking
- Zentrale Datenhaltung bei dezentraler Nutzung
- Skalierbare Rechenkapazität für komplexe Analysen
Digital Twin für OEE-Simulation
Digitale Zwillinge ermöglichen die Simulation von Produktionsprozessen zur Prognose und Optimierung der OEE:
-
What-If-Analysen:
"Wie verändert sich die OEE, wenn wir Rüstzeiten um 20% reduzieren?"
"Welchen Effekt hat eine Erhöhung der Maschinengeschwindigkeit um 5% auf die Qualität?" -
Optimale Produktionsplanung:
Simulation verschiedener Produktionssequenzen zur Minimierung von Rüstzeiten
Berechnung der optimalen Losgröße für maximale OEE -
Kapazitätsplanung:
Prognose der benötigten Kapazität basierend auf historischen OEE-Werten
Simulation von Spitzenlasten und deren Auswirkung auf die OEE
Best Practices: Datenerfassung und -analyse für die OEE-Berechnung
Für eine aussagekräftige OEE-Berechnung ist eine strukturierte Datenerfassung und -analyse unerlässlich.
Strukturierter Datenerfassungsplan für OEE
Ein effektiver Datenerfassungsplan umfasst folgende Komponenten:
-
Stammdaten:
- Definitionen aller Zeitkategorien (geplante Produktion, Pausen, Wartung)
- Ideale Zykluszeiten pro Produkt
- Qualitätsstandards und Toleranzgrenzen
-
Bewegungsdaten:
- Stillstandszeiten mit Kategorisierung
- Produktionszahlen (Input/Output)
- Ausschuss und Nacharbeit mit Fehlerklassifizierung
-
Erfassungsintervalle:
- Stillstände: Sofort bei Auftreten
- Produktionszahlen: Stündlich oder pro Schicht
- Qualitätsdaten: Bei Qualitätschecks oder kontinuierlich
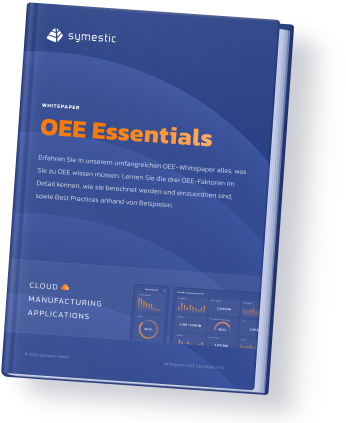
Datenaggregation und -analyse
Für aussagekräftige OEE-Analysen müssen Daten sinnvoll aggregiert werden:
-
Zeitliche Aggregation:
- Schichtbezogen für operatives Management
- Tagesbezogen für taktische Entscheidungen
- Wochenbezogen für Trendanalysen
- Monatsbezogen für strategisches Management
-
Produkt- und Anlagenbezogene Analyse:
OEE nach Produktfamilie:
- Produkt A: 82%
- Produkt B: 68%
- Produkt C: 75%
OEE nach Schichtteam:
- Team 1: 76%
- Team 2: 74%
- Team 3: 69% -
Drill-Down-Fähigkeit: Die Möglichkeit, von aggregierten Daten auf Detailebene zu navigieren, ist entscheidend für die Ursachenanalyse:
OEE Gesamtwert → Faktor mit größtem Verlust → Hauptverlustquelle → Spezifische Vorfälle → Detailanalyse
Visualisierung von OEE-Daten
Eine effektive Visualisierung ist entscheidend für die Interpretation und Kommunikation von OEE-Daten:
-
Operative Dashboards:
- Echtzeitanzeige der aktuellen OEE und ihrer Komponenten
- Zeitlicher Verlauf der letzten Stunden/Schichten
- Visualisierung aktueller Stillstände und Verluste
-
Taktische Analysetools:
- Pareto-Diagramme der Verlustquellen
- Trendanalysen über mehrere Tage/Wochen
- Vergleichsanalysen zwischen Produkten/Schichten
-
Strategische Reports:
OEE-Berechnungstools und Software-Lösungen
Für die praktische Implementierung stehen verschiedene Tools zur Verfügung, von einfachen Tabellenkalkulationen bis zu komplexen Manufacturing Execution Systems (MES).
Excel-basierte OEE-Berechnung
Für Einsteiger und kleine Betriebe bietet Excel einen guten Startpunkt:
Vorteile:
- Geringe Einstiegshürde
- Flexible Anpassung an spezifische Anforderungen
- Keine zusätzliche Software notwendig
Nachteile:
- Manuelle Dateneingabe
- Begrenzte Echtzeitfähigkeit
- Fehleranfällig bei komplexen Berechnungen
Beispiel-Template-Struktur:
- Eingabeblatt für Produktionsdaten
- Berechnungsblatt mit OEE-Formeln
- Dashboard mit Visualisierungen
- Historisches Archiv für Trendanalysen
Spezialisierte OEE-Software
Dedizierte OEE-Software bietet umfassende Funktionen für professionelle Anwendungen:
Kernfunktionen:
- Automatische Datenerfassung von Maschinen
- Echtzeitvisualisierung der OEE
- Umfassende Analysetools und Berichte
- Integration mit bestehenden Systemen
Auswahlkriterien:
- Skalierbarkeit (Anzahl der erfassbaren Anlagen)
- Integrationsoptionen (Schnittstellen zu Maschinen und ERP)
- Mobilfähigkeit (Zugriff von Tablets/Smartphones)
- Anpassbarkeit (Berechnungsmethoden, Dashboards)
MES-integrierte OEE-Berechnung
Manufacturing Execution Systems bieten OEE als Teil einer ganzheitlichen Produktionssteuerung:
Vorteile der Integration:
- Konsistente Datenbasis für alle Produktionskennzahlen
- Bidirektionale Kommunikation mit ERP- und Planungssystemen
- Ganzheitliche Prozessoptimierung statt isolierter Kennzahlenverbesserung
- Durchgängige Rückverfolgbarkeit von Produkten und Prozessen
Integration mit anderen Kennzahlen:
- OEE-Werte fließen in KPIs wie Gesamtanlagenproduktivität (OAE) ein
- Verknüpfung mit Energieeffizienz-Kennzahlen für nachhaltige Optimierung
- Korrelationsanalysen mit Kostenkennzahlen für wirtschaftliche Bewertung
Cloud-native OEE-Lösungen
Moderne OEE-Lösungen nutzen Cloud-Technologien für maximale Flexibilität und Skalierbarkeit:
Technische Vorteile:
- Schnelle Implementierung ohne komplexe IT-Infrastruktur
- Automatische Updates und Erweiterungen ohne Systemunterbrechungen
- Standortübergreifender Zugriff und Benchmarking
- Flexible Skalierung je nach Unternehmenswachstum
Funktionale Highlights:
- Multi-Device-Zugriff (PC, Tablet, Smartphone, Shopfloor-Displays)
- Modulare Erweiterbarkeit (OEE → Predictive Maintenance → APM)
- KI-basierte Analysen mit steigender Datenmenge
- Offene APIs für Integration mit bestehenden Systemen
Fazit: Die OEE-Berechnung als kontinuierlicher Verbesserungsprozess
Die Berechnung der Gesamtanlageneffektivität ist weit mehr als eine mathematische Übung – sie ist der Schlüssel zu nachhaltiger Produktivitätssteigerung in der Fertigung.
Der OEE-Optimierungszyklus
Für langfristigen Erfolg muss die OEE-Berechnung in einen kontinuierlichen Verbesserungsprozess eingebettet werden:
- Messen: Erfassen Sie OEE-Daten präzise und konsistent
- Analysieren: Identifizieren Sie die größten Verlustquellen durch Pareto-Analysen
- Verbessern: Setzen Sie gezielte Maßnahmen zur Reduzierung der Hauptverluste um
- Standardisieren: Etablieren Sie neue Best Practices als Standard
- Wiederholen: Starten Sie den Zyklus mit höheren Zielvorgaben neu
Kritische Erfolgsfaktoren für die OEE-Berechnung
Die praktische Erfahrung aus zahlreichen OEE-Implementierungen zeigt, dass folgende Faktoren entscheidend sind:
- Datenzuverlässigkeit: Die Präzision Ihrer OEE-Werte hängt direkt von der Qualität Ihrer Datenerfassung ab.
- Methodische Konsistenz: Standardisieren Sie Definitionen und Berechnungsmethoden unternehmensweit.
- Führungsunterstützung: OEE-Optimierung erfordert Engagement auf allen Ebenen, besonders im Management.
- Mitarbeitereinbindung: Schulen Sie Bediener und Instandhalter in der Bedeutung und Anwendung von OEE.
- Technologische Unterstützung: Nutzen Sie moderne Technologien für präzise Datenerfassung und -analyse.
Vom Messen zum Verbessern: OEE in die Praxis umsetzen
Quick Wins identifizieren
Lösen Sie zunächst einfache, hochfrequente Probleme mit geringem Aufwand.
Zielgerichtete Investitionen
Nutzen Sie OEE-Daten zur Priorisierung von Investitionen mit optimalem ROI.
Die systematische OEE-Berechnung und -Optimierung ist ein Schlüsselfaktor für die Wettbewerbsfähigkeit produzierender Unternehmen. Transformieren Sie Ihre Produktion von einer Kostenstelle zum strategischen Wettbewerbsvorteil!
OEE-Optimierung
Bewährte Strategien und Verfahren aus über 200 erfolgreichen OEE-Projekten.
Exklusives Whitepaper
Lernen Sie die modernsten Ansätze der Industrie 4.0, die Sie in Ihrer Produktion schon morgen umsetzen können, um innerhalb von 4 Wochen Ihre Kosten um gut 20% zu reduzieren.
mehr erfahren