Industrie 4.0: Definition, Vorteile & Implementierung [2025-Guide]
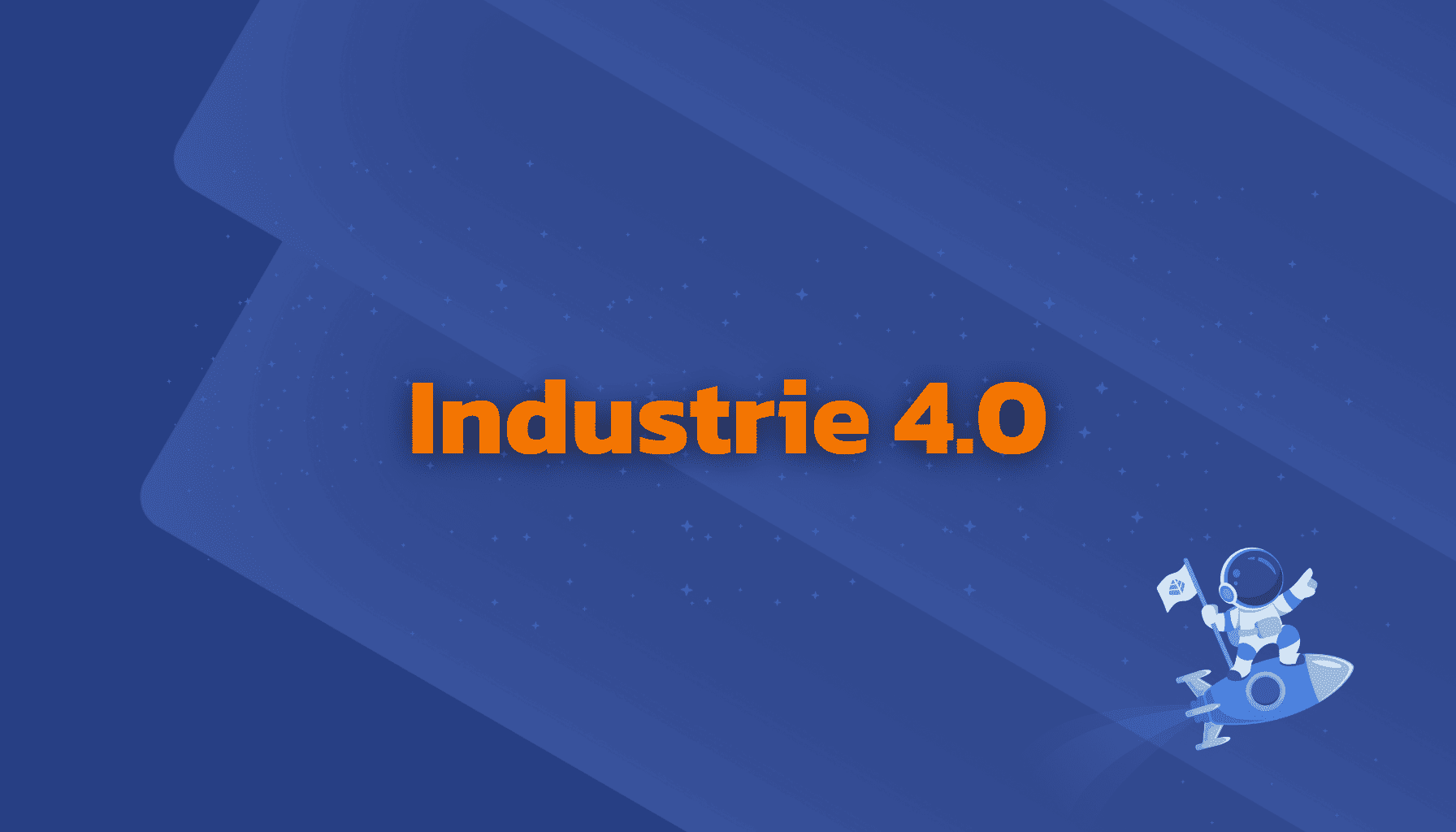
Inhaltsverzeichnis
- Was ist Industrie 4.0?
- Die 4 Säulen der Smart Factory
- Implementierung in der Praxis
- Standards & Zukunftstrends
Was ist Industrie 4.0?
Die vierte industrielle Revolution läutet ein neues Zeitalter der Produktion ein. Während frühere industrielle Revolutionen durch Dampfkraft, Elektrifizierung und erste Computertechnologien geprägt waren, steht Industrie 4.0 für die vollständige digitale Transformation der Fertigungsindustrie. Doch was verbirgt sich konkret hinter diesem Begriff, der die Produktionswelt revolutioniert?
Definition & Kernelemente
Industrie 4.0 beschreibt die intelligente Vernetzung moderner Produktionssysteme. Im Zentrum steht dabei die Vision einer Smart Factory, in der Maschinen, Produkte und Menschen nahtlos miteinander kommunizieren. Anders als bei herkömmlicher Automatisierung geht es nicht nur um einzelne Produktionsschritte, sondern um ein ganzheitliches, sich selbst optimierendes System.
Die Basis bilden dabei drei zentrale Kernelemente:
Cyber-Physische Systeme (CPS): Diese Systeme verbinden die physische mit der digitalen Welt. Sensoren erfassen kontinuierlich Produktionsdaten, während intelligente Software diese in Echtzeit analysiert und Produktionsabläufe automatisch anpasst. Ein Beispiel: Eine Fertigungsanlage erkennt selbstständig Materialengpässe und bestellt automatisch Nachschub.
Internet der Dinge (Industrial IoT): Das industrielle Internet der Dinge vernetzt alle Komponenten der Produktion miteinander. Maschinen, Werkstücke und Logistiksysteme tauschen permanent Daten aus und koordinieren sich selbstständig. So "weiß" ein Werkstück bereits beim Produktionsstart, welche Bearbeitungsschritte es durchlaufen muss und kommuniziert dies direkt mit den verfügbaren Maschinen.
Digitaler Zwilling: Als digitales Abbild der realen Produktion ermöglicht der Digital Twin die Simulation und Optimierung von Prozessen, bevor sie in der Realität umgesetzt werden. Änderungen können vorab getestet und Risiken minimiert werden.
Die wichtigsten Technologien im Überblick
Die Umsetzung von Industrie 4.0 basiert auf mehreren Schlüsseltechnologien, die das Fundament der intelligenten Fabrik bilden:
Big Data Analytics & KI: Moderne Analyseverfahren verarbeiten die enormen Datenmengen aus der Produktion und gewinnen daraus wertvolle Erkenntnisse. Künstliche Intelligenz erkennt Muster und optimiert Prozesse kontinuierlich. Ein Beispiel ist die vorausschauende Wartung (Predictive Maintenance), bei der KI-Systeme den optimalen Zeitpunkt für Wartungsarbeiten vorhersagen.
Cloud Computing: Die Cloud bildet das Rückgrat der vernetzten Produktion. Sie stellt flexible Rechenleistung und Speicherkapazität zur Verfügung und ermöglicht den standortübergreifenden Datenaustausch. Unternehmen können ihre IT-Ressourcen dadurch optimal an den tatsächlichen Bedarf anpassen.
5G & Industrielle Kommunikation: Hochleistungsfähige Kommunikationsnetze sind entscheidend für Industrie 4.0. 5G-Technologie ermöglicht die Echtzeitübertragung großer Datenmengen und die zuverlässige Vernetzung tausender Geräte. Dies ist besonders wichtig für zeitkritische Anwendungen wie die Robotersteuerung.
- Datenvernetzung: Alle Systeme digital verbinden
- Echtzeit-Monitoring: Prozesse kontinuierlich überwachen
- Cloud-Einstieg: Mit einzelner Produktionslinie starten
Quick-Guide: Vorteile auf einen Blick
Die Implementierung von Industrie 4.0 bringt Unternehmen zahlreiche messbare Vorteile:
Effizienzsteigerung
- Produktivitätssteigerung um 20-35% durch optimierte Prozesse
- Reduzierung von Stillstandzeiten um bis zu 50%
- Senkung der Energiekosten um durchschnittlich 15-20%
Qualitätsverbesserung
- Fehlerquote sinkt um bis zu 25% durch intelligente Qualitätskontrolle
- Kontinuierliche Prozessoptimierung durch Echtzeitdaten
- Rückverfolgbarkeit aller Produktionsschritte
Flexibilität & Innovation
- Schnellere Reaktion auf Marktveränderungen
- Individualisierte Produktion auch bei kleinen Stückzahlen
- Entwicklung neuer, datenbasierter Geschäftsmodelle
Die Transformation zur Industrie 4.0 ist dabei keine Option, sondern eine Notwendigkeit für Unternehmen, die im globalen Wettbewerb bestehen wollen. Die Investitionen in moderne Technologien zahlen sich durch gesteigerte Effizienz, bessere Qualität und neue Geschäftsmöglichkeiten aus.
Die 4 Säulen der Smart Factory
Die Transformation zur Industrie 4.0 basiert auf vier fundamentalen Säulen, die gemeinsam das Fundament der intelligenten Fabrik bilden. Diese Säulen sind entscheidend für Unternehmen, die den Schritt in die digitalisierte Produktion erfolgreich meistern wollen. In der modernen Industrie 4.0 greifen diese Elemente nahtlos ineinander und ermöglichen eine nie dagewesene Effizienz in der Fertigung.
Vernetzung & IoT: Das Nervensystem der Industrie 4.0
Die durchgängige Vernetzung bildet das Rückgrat jeder Industrie 4.0-Lösung. Durch das Industrial Internet of Things (IIoT) kommunizieren Maschinen, Produkte und Systeme in Echtzeit miteinander. Diese intelligente Vernetzung ermöglicht:
- Transparente Produktionsprozesse durch lückenlose Datenerfassung
- Automatische Anpassung der Produktion an veränderte Bedingungen
- Effiziente Ressourcennutzung durch optimierte Abstimmung aller Komponenten
In der Praxis bedeutet dies beispielsweise, dass eine Fertigungslinie automatisch ihre Geschwindigkeit anpasst, wenn vor- oder nachgelagerte Prozesse dies erfordern. Moderne 5G-Campusnetze und Industrial Ethernet sorgen dabei für die nötige Kommunikationsinfrastruktur, die für Industrie 4.0-Anwendungen unerlässlich ist.
Datenanalyse & KI: Das Gehirn der Smart Factory
Im Kontext von Industrie 4.0 spielt die intelligente Datenanalyse eine Schlüsselrolle. Künstliche Intelligenz und Machine Learning verwandeln die gesammelten Daten in wertvolle Erkenntnisse:
- Predictive Maintenance reduziert ungeplante Stillstandzeiten um bis zu 50%
- Qualitätsprognosen erhöhen die Produktqualität nachweislich um 20-30%
- Energiemanagement-Algorithmen senken den Energieverbrauch um bis zu 25%
Ein Beispiel aus der Industrie 4.0-Praxis: Ein KI-System analysiert kontinuierlich Maschinendaten und erkennt frühzeitig Verschleißmuster. Wartungsarbeiten können dadurch optimal geplant werden, bevor es zu kostspieligen Ausfällen kommt.
Automatisierung & Robotik: Die Muskulatur der Industrie 4.0
Die dritte Säule der Smart Factory verbindet klassische Automatisierung mit intelligenter Steuerung. In der Industrie 4.0 arbeiten Menschen und Maschinen eng zusammen:
- Kollaborative Roboter (Cobots) unterstützen Mitarbeiter flexibel bei verschiedenen Aufgaben
- Autonome mobile Roboter (AMR) optimieren die innerbetriebliche Logistik
- Adaptive Produktionssysteme passen sich automatisch an neue Produktvarianten an
Die Integration dieser Technologien in Industrie 4.0-Umgebungen steigert die Produktivität nachweislich um 15-35%, während gleichzeitig die Arbeitssicherheit erhöht wird.
Cloud Manufacturing: Das Betriebssystem der Industrie 4.0
Cloud-basierte Lösungen bilden die vierte Säule der modernen Smart Factory. Sie ermöglichen:
- Flexible Skalierung von IT-Ressourcen nach Bedarf
- Standortübergreifende Vernetzung aller Produktionsstandorte
- Echtzeit-Zugriff auf Produktionsdaten von überall
In der Industrie 4.0-Praxis nutzen Unternehmen zunehmend hybride Cloud-Modelle, die die Vorteile von Private und Public Cloud optimal kombinieren. Dies ermöglicht eine kosteneffiziente und gleichzeitig sichere Digitalisierung der Produktion.
Diese vier Säulen der Smart Factory bilden zusammen das Fundament für eine erfolgreiche Implementierung von Industrie 4.0. Unternehmen, die diese Elemente geschickt miteinander verbinden, schaffen die Voraussetzungen für eine zukunftsfähige und wettbewerbsfähige Produktion.
Die Integration dieser Technologien ist dabei kein einmaliges Projekt, sondern ein kontinuierlicher Prozess der digitalen Transformation.
Implementierung in der Praxis
Die erfolgreiche Implementierung von Industrie 4.0 erfordert einen strukturierten Ansatz und die richtigen Technologiepartner. Besonders cloud-basierte Manufacturing Execution Systems (MES) haben sich als idealer Einstiegspunkt in die digitale Transformation bewährt. Wie die praktische Umsetzung gelingt, zeigen wir anhand konkreter Implementierungsschritte.
5-Schritte Implementation Guide
1. Ist-Analyse & Digitalisierungsstrategie: Die Transformation zur Industrie 4.0 beginnt mit einer gründlichen Analyse der bestehenden Prozesse. Dabei gilt es, die digitale Reife des Unternehmens zu bewerten und konkrete Ziele zu definieren. Ein modernes Cloud-MES wie SYMESTIC unterstützt bereits in dieser Phase durch:
- Standardisierte Analysewerkzeuge für Produktionsprozesse
- Vordefinierte Best-Practice-Templates
- Schnelle Implementierbarkeit ohne große Vorinvestitionen
2. Aufbau der digitalen Infrastruktur: Die technische Basis für Industrie 4.0 muss nicht komplex sein. Mit modernen Cloud-Lösungen entfällt der Aufbau einer aufwendigen IT-Infrastruktur. Stattdessen:
- Flexible Cloud-Architekturen nach Bedarf
- Standardisierte Schnittstellen für einfache Integration
- Sofortige Nutzung ohne lange Implementierungszeiten
3. Pilotprojekt und erste Erfolge Der Einstieg in Industrie 4.0 gelingt am besten über klar definierte Pilotprojekte. Dabei hat sich besonders die schrittweise Einführung eines MES bewährt:
- Start mit einzelnen Produktionslinien
- Schnelle Erfolgserlebnisse durch vorkonfigurierte Lösungen
- Kontinuierliche Optimierung basierend auf Echtzeitdaten
4. Skalierung und Integration Nach erfolgreichen Pilotprojekten folgt die unternehmensweite Ausrollung. Cloud-basierte Systeme bieten hier entscheidende Vorteile:
- Flexible Skalierung nach Bedarf
- Einfache Anbindung weiterer Produktionsstandorte
- Nahtlose Integration mit bestehenden Systemen
5. Kontinuierliche Verbesserung Die Implementierung von Industrie 4.0 ist ein fortlaufender Prozess. Moderne MES-Lösungen unterstützen durch:
- Kontinuierliches Performance-Monitoring
- KI-gestützte Prozessoptimierung
- Regelmäßige Updates und neue Funktionen
Typische Herausforderungen & Lösungen
Die Praxis zeigt, dass Unternehmen bei der Implementierung von Industrie 4.0 häufig vor ähnlichen Herausforderungen stehen. Mit dem richtigen Ansatz lassen sich diese jedoch meistern:
Herausforderung: Hohe Investitionskosten
Lösung: Cloud-basierte Pay-per-Use Modelle, eliminieren hohe Anfangsinvestitionen. Unternehmen zahlen nur für die tatsächlich genutzten Ressourcen.
Herausforderung: Komplexe IT-Integration
Lösung: Moderne MES-Lösungen bieten standardisierte Schnittstellen und vorkonfigurierte Integrationen. Die Anbindung an bestehende Systeme erfolgt meist innerhalb weniger Tage.
Herausforderung: Mitarbeiterakzeptanz
Lösung: Intuitive Benutzeroberflächen und umfassende Schulungskonzepte sorgen für eine hohe Akzeptanz bei den Mitarbeitern.
Kosten & ROI-Berechnung
Die Investition in Industrie 4.0-Technologien zahlt sich nachweislich aus. Praxiserfahrungen zeigen:
Typische Einsparungen:
- Reduzierung der Produktionskosten um 15-25%
- Senkung der Qualitätskosten um bis zu 20%
- Verringerung der IT-Kosten durch Cloud-Nutzung um 30-40%
ROI-Faktoren bei Cloud-MES:
- Keine hohen Initialinvestitionen
- Schnelle Implementierung binnen weniger Wochen
- Messbare Ergebnisse bereits nach 3-6 Monaten
Die Praxis zeigt: Besonders Cloud-basierte Lösungen ermöglichen einen schnellen und risikoarmen Einstieg in Industrie 4.0. Durch die flexible Skalierbarkeit und das Pay-per-Use Modell können Unternehmen die Digitalisierung ihrer Produktion schrittweise und entsprechend ihrer individuellen Bedürfnisse vorantreiben.
Standards & Zukunftstrends in der Industrie 4.0
Die Entwicklung von Industrie 4.0 schreitet kontinuierlich voran. Für Unternehmen ist es entscheidend, sowohl die aktuellen Standards als auch die kommenden Trends im Blick zu behalten. Nur so können sie ihre Wettbewerbsfähigkeit langfristig sichern.
Wichtige Normen und Standards
Die Basis für eine erfolgreiche Industrie 4.0-Implementierung bilden internationale Standards und Normen. Diese gewährleisten Interoperabilität und Zukunftssicherheit:
RAMI 4.0 (Referenzarchitekturmodell Industrie 4.0): Das Referenzarchitekturmodell bietet einen strukturierten Rahmen für die Einführung von Industrie 4.0-Technologien. Es definiert:
- Hierarchische Ebenen der Produktion
- IT-Security-Anforderungen
- Kommunikationsstandards
- Datenaustauschformate
Internationale Kommunikationsstandards: Moderne Cloud-MES-Systeme wie SYMESTIC basieren auf bewährten Standards:
- OPC UA für die sichere Maschinenkommunikation
- MQTT für IoT-Anwendungen
- REST-APIs für Systemintegration
- Automation ML für den Datenaustausch
Technologietrends 2024
Die Industrie 4.0 entwickelt sich ständig weiter. Folgende Trends werden die Produktion in den kommenden Jahren prägen:
1. Edge Computing in der Produktion
- Dezentrale Datenverarbeitung direkt an der Maschine
- Reduzierte Latenzzeiten für kritische Prozesse
- Optimierte Bandbreitennutzung
2. KI-gestützte Autonomie
- Selbstoptimierende Produktionssysteme
- Vorausschauende Qualitätssicherung
- Autonome Logistiklösungen
3. Digital Twin Evolution
- Komplette Abbildung der Produktionsumgebung
- Echtzeitoptimierung durch Simulation
- Verbesserte Planungssicherheit
4. Nachhaltige Smart Factories
- Energieeffiziente Produktionsprozesse
- CO2-Fußabdruck-Monitoring
- Ressourcenoptimierung durch KI
Ausblick: Die Zukunft der industriellen Produktion
Die Transformation zur Industrie 4.0 ist kein endlicher Prozess, sondern eine kontinuierliche Entwicklung. Unternehmen, die heute die richtigen Weichen stellen, sichern sich entscheidende Wettbewerbsvorteile für die Zukunft.
Kurzfristige Entwicklungen (1-2 Jahre)
- Verstärkte Integration von Cloud-MES-Lösungen
- Ausbau von 5G-Campusnetzen
- Zunehmende Automatisierung durch Cobots
Mittelfristige Trends (3-5 Jahre)
- Vollständig vernetzte Wertschöpfungsketten
- KI-gesteuerte Produktionsoptimierung
- Flexible Fertigungssysteme für Losgröße 1
Fazit: Industrie 4.0 als Schlüssel zum Erfolg
Die digitale Transformation der Industrie ist nicht mehr aufzuhalten. Unternehmen stehen vor der Herausforderung, den Wandel aktiv zu gestalten. Die gute Nachricht: Der Einstieg in Industrie 4.0 muss weder komplex noch kostspielig sein.
Moderne Cloud-MES-Lösungen, wie sie SYMESTIC anbietet, ermöglichen einen schnellen und risikoarmen Start in die digitale Transformation:
- Keine hohen Initialinvestitionen durch Pay-per-Use Modelle
- Schnelle Implementierung binnen weniger Wochen
- Messbarer ROI bereits nach wenigen Monaten
- Zukunftssichere Technologie durch kontinuierliche Updates
Die Erfahrung zeigt: Unternehmen, die jetzt in Industrie 4.0-Technologien investieren, verschaffen sich entscheidende Wettbewerbsvorteile:
- Gesteigerte Produktionseffizienz
- Verbesserte Produktqualität
- Höhere Flexibilität
- Reduzierte Kosten
Der Weg zur Smart Factory beginnt mit dem ersten Schritt. Mit dem richtigen Partner und einer klaren Strategie kann jedes Unternehmen die Chancen der digitalen Transformation nutzen. Die Zeit zu handeln ist jetzt.
Exklusives Whitepaper
Lernen Sie die modernsten Ansätze der Industrie 4.0, die Sie in Ihrer Produktion schon morgen umsetzen können, um innerhalb von 4 Wochen Ihre Kosten um gut 20% zu reduzieren.
mehr erfahren