OEE-Erfassung + Dashboards: Software und Monitoring für die Produktion
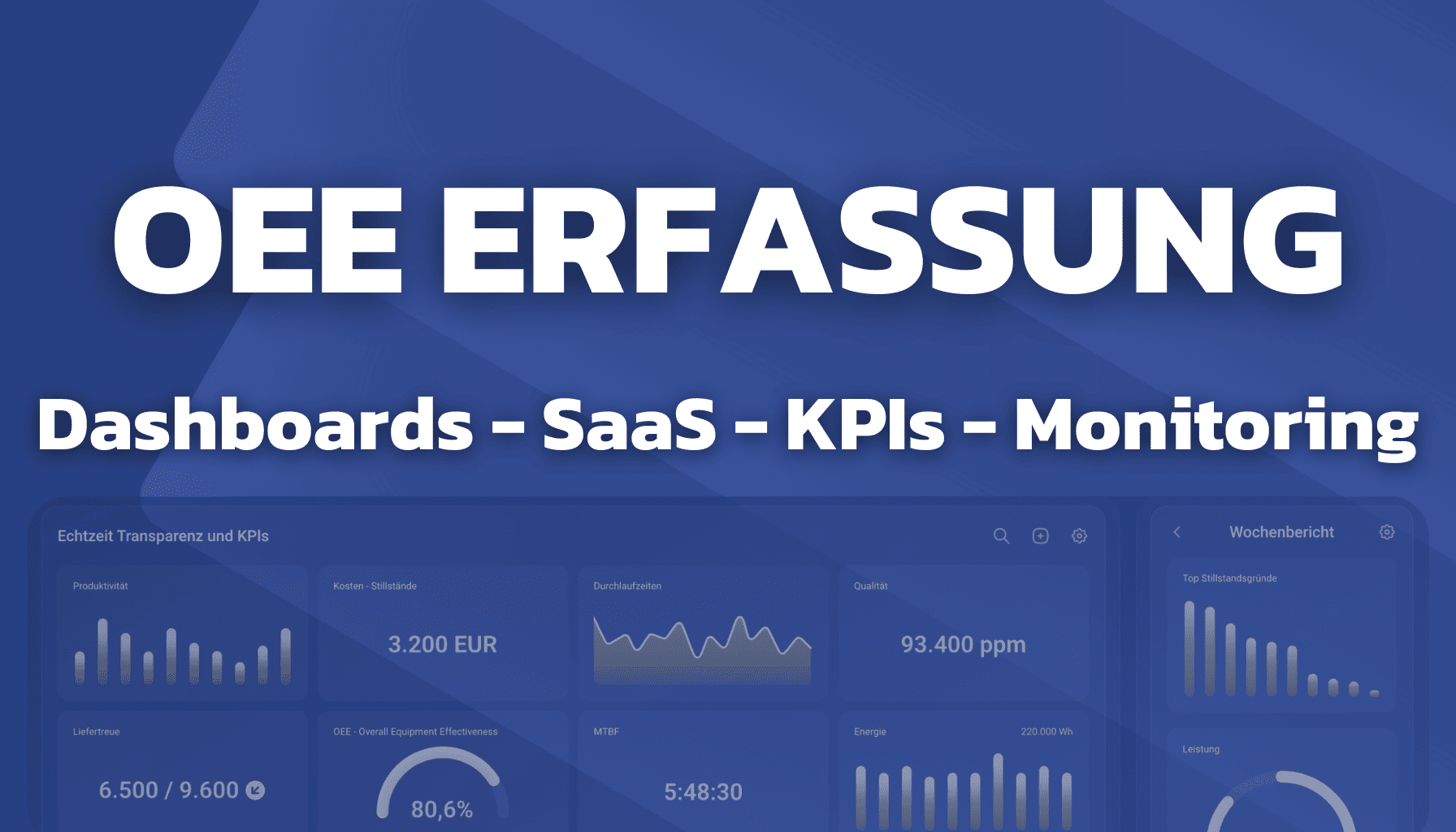
Inhaltsverzeichnis
Dieser Artikel behandelt einen spezifischen Aspekt der Overall Equipment Effectiveness (OEE). Für einen umfassenden Überblick und Grundlagen zur OEE empfehlen wir unseren Hauptartikel:
Zum OEE-HauptartikelGrundlagen der OEE-Erfassung
Die Ermittlung der Gesamtanlageneffektivität basiert auf präzisen mathematischen Modellen und standardisierten Berechnungsverfahren, die drei Kernkomponenten umfassen. Die technische Umsetzung der Datenerfassung für diese Komponenten ist entscheidend für die Genauigkeit und Zuverlässigkeit der OEE-Berechnung.
Navigieren Sie hier zum OEE-Berechnungsartikel.
1. Verfügbarkeit
Die Verfügbarkeit einer Anlage wird definiert als das Verhältnis zwischen geplanter Produktionszeit und tatsächlicher Laufzeit, ausgedrückt durch die Formel:
Verfügbarkeit = Laufzeit / Geplante Produktionszeit = (Geplante Produktionszeit - Stillstandszeit) / Geplante Produktionszeit
Erfassungsparameter
Zur präzisen Verfügbarkeitsberechnung müssen folgende technischen Parameter erfasst werden:
- Geplante Produktionszeit: Definiert durch Produktionsplanung, Schichtmodelle und Arbeitszeitregelungen
- Stillstandszeiten: Zeitabschnitte, in denen die Anlage trotz geplanter Produktion nicht läuft
- Rüstzeiten: Zeitintervalle für Produktwechsel, Werkzeugwechsel und Einrichtungsprozesse
- Stillstandsursachen: Kategorisierte Ursachencodes gemäß ISO 22400 oder unternehmensspezifischen Katalogen
- Mikrostillstände: Kurze Unterbrechungen unter einem definierten Schwellenwert (typischerweise 3-5 Minuten)
Vom Messen zum Verbessern: OEE in die Praxis umsetzen
Quick Wins identifizieren
Lösen Sie zunächst einfache, hochfrequente Probleme mit geringem Aufwand.
Zielgerichtete Investitionen
Nutzen Sie OEE-Daten zur Priorisierung von Investitionen mit optimalem ROI.
Die systematische OEE-Berechnung und -Optimierung ist ein Schlüsselfaktor für die Wettbewerbsfähigkeit produzierender Unternehmen. Transformieren Sie Ihre Produktion von einer Kostenstelle zum strategischen Wettbewerbsvorteil!
OEE-Optimierung
Bewährte Strategien und Verfahren aus über 200 erfolgreichen OEE-Projekten.
Technische Detektionsmethoden
Die Erfassung der Anlagenverfügbarkeit kann über verschiedene technische Methoden realisiert werden:
- Direkte Signaldetektion: Erfassung von SPS-Signalen wie "Anlage in Automatik", "Not-Aus", "Störung aktiv"
- Implementierungsbeispiel: Anbindung an potentialfreie Kontakte mit 24V Signalpegel und Optokopplern zur galvanischen Trennung
- Abtastrate ab: 10ms zur präzisen Erfassung auch kurzer Stillstände
- Laufzeitüberwachung: Messung von Antriebskomponenten durch Stromaufnahme oder Drehzahlsensoren
- Technische Parameter: 4-20 mA Strommessung mit Umformern, Frequenzeingänge für Drehzahlerfassung
- Schwellenwertdefinition: Konfigurierbare Grenzwerte zur Unterscheidung zwischen Leerlauf und Produktion
- Erweiterte Zustandsmodelle: Verwendung mehrstufiger Zustandsmodelle über einfache Lauf/Stopp-Detektion hinaus
- Modelltiefe: Typisierte Zustände wie "Produktion", "Einrichten", "Störung", "Wartung", "Energiesparend"
- Zustandsübergänge: Definierte Transitionsregeln mit hysteresebehafteten Umschaltpunkten
Erfassungsmethodik und Datenqualität
Die technische Umsetzung der Verfügbarkeitserfassung erfolgt über diese Methoden:
- Automatische Erfassung:
- Technologie: Direkte SPS-Anbindung über OPC UA oder Modbus
- Präzision: Millisekundengenaue Zeitstempel für Zustandsänderungen
- Ausfallsicherheit: Lokale Pufferung mit zeitsynchronisierten Datenbanken
- Halbautomatische Erfassung:
- Technische Umsetzung: Grundzustandserfassung automatisch, Ursachenzuordnung manuell
- Intelligente Mustererkennung: Hochkomplexer Algorithmus, der Ist-Zyklusmuster mit Soll-Zyklusmustern vergleicht und Abweichungen identifiziert
- Zeitverzögerung: Konfigurierbare Timeout-Parameter für Ursacheneingaben
- Validierung: Automatische Plausibilitätsprüfung der eingegebenen Daten
- BDE-Terminal-basierte Erfassung:
- Hardware: Industrietaugliche Touchscreen-Terminals mit IP65-Schutzklasse
- Bedienkonzept: Optimierte UX für Werkstattumgebungen mit Handschuhen
- Datenkonsistenz: Integrierte Validierungslogik zur Vermeidung von Fehleingaben
2. Leistung
Die Leistungskomponente quantifiziert die Produktionsgeschwindigkeit im Verhältnis zur theoretischen Maximalleistung:
Leistung = (Produzierte Menge × Ideale Zykluszeit) / Laufzeit = Tatsächliche Produktionsrate / Ideale Produktionsrate
Erfassungsparameter
Für die exakte Leistungsberechnung sind folgende technische Parameter zu erfassen:
- Soll-Zykluszeit: Referenzwert für die Vorgabe-Produktionsgeschwindigkeit, je nach Produkt und technologischem Prozess
- Tatsächliche Produktionsrate: Gemessene Produktionsgeschwindigkeit in Echtzeit
- Produktionsmengen: Stückzahlen, Meter, Kilogramm oder andere produktspezifische Mengeneinheiten
- Taktraten: Frequenz der Produktionszyklen in Takt pro Minute oder Takt in Sekunden
- Geschwindigkeitsprofile: Bei nicht-linearen Produktionsprozessen die komplette Geschwindigkeitskurve
Technische Erfassungsmethoden
Die präzise Erfassung der Leistungsparameter erfordert spezialisierte technische Ansätze:
- Direkter Stückzahlzähler:
- Sensortypologie: Lichtschranken, induktive Sensoren, Barcode-Scanner, RFID-Reader
- Signalverarbeitung: Debouncing-Algorithmen zur Eliminierung von Prelleffekten
- Präzision: Fehlerrate <0,01% durch redundante Sensorkonfiguration
- Taktzeiterfassung:
- Messprinzip: Hochpräzise Zeitmessung zwischen definierten Prozessschritten
- Synchronisation: PTP (Precision Time Protocol) nach IEEE 1588 für mikrosekungenaue Taktung
- Statistische Auswertung: Kontinuierliche Berechnung von Durchschnitt, Standardabweichung und Trendanalysen
- Direkte Geschwindigkeitsmessung:
- Messtechnologie: Drehzahlsensoren, Encoder, Frequenzumrichter-Rückmeldungen
- Auflösung: 12-16 Bit für hochpräzise Geschwindigkeitsregulierung
- Skalierung: Automatische Umrechnung von Antriebsdrehzahl in Produktionseinheiten
Parameteroptimierung und Kalibrierung
Für eine präzise Leistungserfassung sind folgende technische Maßnahmen notwendig:
- Referenzwertermittlung:
- Methodik: Statistische Analyse historischer Bestleistungen
- Machine Learning: Kontinuierliche Optimierung von Referenzwerten durch KI-gestützte Modelle
- Kontextadaption: Automatische Anpassung an Produktvarianten, Materialchargen und Umgebungsbedingungen
- Dynamische Sollwertanpassung:
- Algorithmus: Fuzzy-Logic-Regelwerk zur situationsabhängigen Sollwertbestimmung
- Parameter: Berücksichtigung von Materialparametern, Werkzeugverschleiß und Umgebungstemperatur
- Self-Learning: Selbstoptimierende Modelle zur kontinuierlichen Verbesserung der Referenzwerte
3. Qualität
Die Qualitätskomponente misst das Verhältnis von Gutteilen zur Gesamtproduktion:
Qualität = Gutteile / Gesamtproduktion = (Gesamtproduktion - (Ausschuss + Nacharbeit)) / Gesamtproduktion
Erfassungsparameter
Für eine detaillierte Qualitätsanalyse sind folgende Parameter zu erfassen:
- Gesamtproduktion: Bruttomenge aller produzierten Einheiten
- Ausschuss: Defekte Teile nach kategorisierten Fehlerarten gemäß definiertem Fehlerkatalog
- Nacharbeit: Teile mit Mängeln, die durch definierte Nachbearbeitungsprozesse korrigiert werden können
- Fehlerursachen: Kategorisierte Defektcodes nach standardisierten Qualitätstaxonomien
- Prozessfähigkeitskennzahlen: Cpk, Ppk und weitere statistische Qualitätsparameter
- Qualitätskosten: Monetäre Bewertung von Ausschuss und Nacharbeit für ROI-Analysen
Technische Erfassungsmethoden
Die Qualitätserfassung erfordert spezialisierte technische Systeme:
- Automatische Qualitätsprüfsysteme:
- Technologien: Maschinelles Sehen, Lasermesssysteme, 3D-Scanning, Röntgeninspektionssysteme
- Auflösung: Mikrometergenaue Vermessung kritischer Produktmerkmale
- Fehlerklassifikation: Deep-Learning-basierte Erkennung und Kategorisierung von Defekten
- Inline-Messtechnik:
- Integration: Direkt im Produktionsprozess integrierte Sensoren
- Messprinzipien: Optisch, taktil, induktiv, kapazitiv je nach Anwendung
- Echtzeitverarbeitung: Sub-Millisekunden-Analyse für Hochgeschwindigkeitsproduktion
- CAQ-System-Integration:
- Schnittstellen: Standardisierte Anbindung an Qualitätsmanagementsysteme
- Datenaustausch: Bidirektionaler Transfer von Prüfplänen, Messdaten und Fehlerstatistiken
- Rückverfolgbarkeit: Chargen- oder teileindividuelle Zuordnung von Qualitätsdaten
Korrelationsanalysen und Prädiktive Qualität
Fortschrittliche OEE-Monitoring-Systeme bieten erweiterte Analysefunktionen:
- Multi-Parameter-Korrelation:
- Technische Basis: Big-Data-Analyse von Prozess- und Qualitätsparametern
- Algorithmen: Multivariate Regressionsmodelle, neuronale Netze zur Defektvorhersage
- Implementierung: GPU-beschleunigte Berechnung für komplexe Korrelationsanalysen
- Prädiktive Qualitätsmodelle:
Technische Ansätze zur OEE-Datenerfassung
Je nach technologischem Stand der Produktionsanlagen und spezifischen Anforderungen kommen verschiedene technische Erfassungsmethoden zum Einsatz. Die Auswahl und Implementierung dieser Methoden hat direkten Einfluss auf Präzision, Aktualität und Zuverlässigkeit der OEE-Berechnung.
Manuelle Datenerfassung
Die manuelle Datenerfassung stellt nach wie vor in vielen Produktionsumgebungen eine praktikable Option dar, insbesondere bei älteren Bestandsanlagen ohne digitale Schnittstellenoptionen.
Papierbasierte Erfassung
- Dokumentationsstandards: Normierte Erfassungsbögen gemäß ISO 22400
- Prozessintegration: Definierte Erfassungsintervalle (typisch: 2-4 Stunden)
- Datentransformation: Nachgelagerte Digitalisierung durch semi-automatische Scanprozesse
Digitale manuelle Erfassung
- Hardware-Spezifikationen:
- Terminals: Industrietaugliche Touch-Panels (IP65/IP67)
- Mobile Devices: Industrietablets mit stoßfesten Gehäusen (MIL-STD-810G)
- Barcode-Scanner: 1D/2D-Scanner mit CMOS-Sensoren, Lesereichweite 10-100 cm
- Softwarearchitektur:
- Frontends: Progressive Web Apps (PWA) für geräteübergreifende Kompatibilität
- Responsezeiten: <300ms für kritische UI-Interaktionen
- Offlinefähigkeit: IndexedDB-basierte lokale Datenspeicherung mit Synchronisationsmechanismen
- Erfassungstechnologien:
- Barcode-Scanning: GS1-konforme Codes zur Produkt- und Auftragsverfolgung
- RFID-Integration: 13,56 MHz HF-Systeme (ISO/IEC 14443) für kontaktlose Identifikation
- NFC-Authentifizierung: Personalisierter Zugriff durch NFC-Token (ISO/IEC 18092)
Technische Limitationen und Fehlerminimierung
- Datenqualitätskontrollen:
- Plausibilitätsprüfungen: Automatische Validierung gegen definierte Grenzwerte
- Zeitstempelgenauigkeit: NTP-synchronisierte Uhren für millisekungenaue Zeiterfassung
- Dopplungserkennung: Implementierung von UUID-basierten Datensätzen zur Eliminierung von Duplikaten
- Latenzaspekte:
- Datenerfassungsverzögerung: Typischerweise 5-30 Minuten
- Aktualisierungszyklen: Konfigurierbare Push- oder Pull-Intervalle (1-60 Minuten)
- Synchronisationsstrategien: Prioritätsbasierte Datenübertragung bei Netzwerkwiederherstellung
Maschinendatenerfassung (MDE)
Die direkte Erfassung von Maschinensignalen repräsentiert den technologischen Goldstandard für OEE-Monitoring-Systeme.
Direkte Signalerfassung
Bei der direkten Signalerfassung werden elektronische Signale von Maschinensteuerungen oder Sensoren mit hoher Präzision erfasst:
- Signaltypen und technische Spezifikationen:
- Digitale Eingänge:
- Spannungspegel: 24V DC (industriestandard), 5V DC (TTL)
- Galvanische Trennung: Optokoppler mit 2,5-5 kV Isolationsspannung
- Eingangsimpedanz: Typisch 2,5-10 kΩ
- Samplingrate: 1-10 kHz für präzise Zustandserfassung
- Analoge Eingänge:
- Signalbereiche: 0-10V, 0-20mA, 4-20mA (industriestandard)
- Auflösung: 12-16 Bit für hochgenaue Messwerterfassung
- Genauigkeit: Typisch ±0,1% vom Messbereichsendwert
- Sample & Hold-Architektur für präzise Momentanwerterfassung
- Impuls-/Frequenzeingänge:
- Frequenzbereiche: 0,1 Hz bis 50 kHz
- Entprellalgorithmen: Digitale Filterung mit konfigurierbarer Zeitkonstante
- Zählerdatenformate: 32/64-Bit für Überlauffestigkeit bei Hochfrequenzzählern
- Digitale Eingänge:
- Hardware-Implementierungen:
- I/O-Module:
- Modulare Aufbauweise: DIN-Schienen-Montage nach EN 60715
- Kommunikationsschnittstellen: EtherCAT, PROFINET, Modbus TCP
- Schutzklassen: IP20 (Schaltschrankmontage), IP67 (Feldmontage)
- Temperaturbereiche: -25°C bis +70°C für industrielle Umgebungen
- IoT-Gateways:
- Prozessorarchitektur: ARM Cortex-M4/A53 oder Intel Atom für Edge-Computing
- Speicher: 1-4 GB RAM, 8-32 GB Flash für lokale Datenpufferung
- Connectivity: Ethernet (100/1000 Mbit), Wi-Fi (IEEE 802.11 a/b/g/n/ac), 4G/5G, LoRaWAN
- Stromversorgung: 24V DC mit Weitbereichseingang (18-36V) und Überspannungsschutz
- Sensornetzwerke:
- Topologien: Stern, Mesh oder Hybrid für redundante Kommunikation
- Protokolle: IO-Link (IEC 61131-9), ASi (EN 50295), Wireless HART (IEC 62591)
- Energieversorgung: Power over Ethernet (PoE) nach IEEE 802.3af/at oder Energy Harvesting
- I/O-Module:
Vom Messen zum Verbessern: OEE in die Praxis umsetzen
Quick Wins identifizieren
Lösen Sie zunächst einfache, hochfrequente Probleme mit geringem Aufwand.
Zielgerichtete Investitionen
Nutzen Sie OEE-Daten zur Priorisierung von Investitionen mit optimalem ROI.
Die systematische OEE-Berechnung und -Optimierung ist ein Schlüsselfaktor für die Wettbewerbsfähigkeit produzierender Unternehmen. Transformieren Sie Ihre Produktion von einer Kostenstelle zum strategischen Wettbewerbsvorteil!
OEE-Optimierung
Bewährte Strategien und Verfahren aus über 200 erfolgreichen OEE-Projekten.
OEE-Monitoring: Von Daten zu Erkenntnissen
Die reine Datenerfassung schafft noch keinen Mehrwert. Erst durch systematisches Monitoring und aussagekräftige Visualisierung werden die Daten zu wertvoller Entscheidungsgrundlage.
Echtzeit-Monitoring
Moderne OEE-Monitoring-Systeme bieten Echtzeit-Einblicke in den Produktionsstatus:
- Live-Statusüberwachung: Aktuelle Betriebszustände aller Anlagen
- Performance-Tracking: Kontinuierliche Überwachung der OEE-Komponenten
- Alarmsysteme: Automatische Benachrichtigungen bei Abweichungen oder Störungen
Diese Echtzeit-Funktionen ermöglichen schnelle Reaktionen auf Probleme und verhindern längere Produktivitätsverluste.
Historische Analysen
Neben der Echtzeitüberwachung ist die Analyse historischer Daten für kontinuierliche Verbesserungen entscheidend:
- Trendanalysen: Langfristige Entwicklung der OEE und ihrer Komponenten
- Verlustanalysen: Identifikation und Quantifizierung der größten Verlustfaktoren
- Vergleichsanalysen: Benchmarking zwischen Anlagen, Schichten oder Standorten
Durch diese Analysen können systematische Probleme identifiziert und gezielt Maßnahmen zur OEE-Verbesserung abgeleitet werden.
Visualisierung: OEE-Dashboards
Die visuelle Aufbereitung der OEE-Daten spielt eine zentrale Rolle für deren Nutzbarkeit:
Typische Dashboard-Elemente
- OEE-Gauges: Tachometer-ähnliche Anzeigen für Gesamtwert und Teilkomponenten
- Zeitverlaufsdiagramme: Visualisierung von OEE-Trends über Zeit
- Pareto-Diagramme: Priorisierte Darstellung von Verlustursachen
- Heatmaps: Farbcodierte Darstellung von Problembereichen
- Produktionskalender: Übersicht über OEE-Werte nach Tagen oder Schichten
Anwendungsspezifische Dashboards
Je nach Zielgruppe und Anwendungsfall werden unterschiedliche Dashboard-Varianten benötigt:
- Shopfloor-Dashboards: Große Anzeigetafeln mit Fokus auf aktuelle Performance
- Management-Dashboards: Zusammenfassende Übersichten mit Fokus auf KPIs
- Analyse-Dashboards: Detaillierte Auswertungen für Produktionsexperten
- Mobile Dashboards: Optimierte Darstellung für Smartphones und Tablets
Die richtige Gestaltung dieser Dashboards ist entscheidend für die effektive Nutzung der OEE-Daten in verschiedenen Unternehmensbereichen.
Datenverarbeitung und -integration
Ein leistungsfähiges OEE-Monitoring-System erfordert nicht nur die Datenerfassung, sondern auch deren effiziente Verarbeitung und Integration in die bestehende IT-Landschaft.
Datenverarbeitungskette
Die typische Verarbeitungskette für OEE-Daten umfasst:
- Datenerfassung: Sammlung von Rohdaten aus verschiedenen Quellen
- Datenvalidierung: Plausibilitätsprüfung und Fehlerkorrektur
- Datenaufbereitung: Normalisierung und Standardisierung der Daten
- Berechnung: Anwendung der OEE-Formeln und Algorithmen
- Aggregation: Zusammenfassung auf verschiedenen Zeitebenen
- Speicherung: Effiziente Datenhaltung für Echtzeitanzeige und Historie
- Visualisierung: Aufbereitung für verschiedene Darstellungsformen
Integration in die Unternehmens-IT
Für maximalen Nutzen sollte ein OEE-Monitoring-System mit anderen Unternehmenssystemen verbunden sein:
- ERP-Integration: Abgleich mit Auftrags- und Produktionsdaten
- MES-Integration: Einbindung in übergeordnete Fertigungssteuerung
- Qualitätsmanagement: Verknüpfung mit QM-Systemen
- Instandhaltung: Verbindung zu Wartungs- und Instandhaltungssystemen
Diese Integrationen ermöglichen ganzheitliche Analysen und vermeiden Datensilos.
Nachdem wir die Grundlagen der OEE-Erfassung und des Monitorings kennengelernt haben, befassen wir uns nun mit modernen Softwarelösungen, die diese Prozesse digitalisieren und optimieren. Cloud-native Lösungen wie die SYMESTIC Manufacturing Platform bieten hierbei besondere Vorteile für Unternehmen, die ihre Produktionseffizienz steigern möchten.
Moderne OEE-Software: Von On-Premises zu Cloud-nativ
Die Evolution von OEE-Software hat sich parallel zur allgemeinen Entwicklung der IT-Landschaft vollzogen:
Legacy-Systeme und On-Premises Lösungen
Traditionelle OEE-Systeme wurden häufig als On-Premises-Lösungen implementiert:
- Lokale Installation: Software wird auf unternehmenseigenen Servern betrieben
- Hohe Initialkosten: Signifikante Investitionen in Hardware, Lizenzen und Implementierung
- Komplexe Updates: Aufwändige Update-Prozesse mit möglichen Ausfallzeiten
- Begrenzte Skalierbarkeit: Kapazitätserweiterungen erfordern zusätzliche Hardware
- Isolierte Datensilos: Eingeschränkte Möglichkeiten zur standortübergreifenden Datenkonsolidierung
Diese Systeme bieten zwar hohe Kontrolle über die eigene IT-Infrastruktur, bringen jedoch erhebliche Nachteile bei Agilität, Skalierbarkeit und Kostenstruktur mit sich.
Cloud-native MES-Lösungen
Die neueste Generation von MES-Software nutzt cloudbasierte Technologien und folgt dem Software-as-a-Service (SaaS) Modell:
- Keine lokale Infrastruktur: Betrieb in hochverfügbaren Rechenzentren
- Abonnement-basiertes Preismodell: Planbare monatliche oder jährliche Kosten statt hoher Initialinvestitionen
- Automatische Updates: Kontinuierliche Funktionserweiterungen ohne Wartungsfenster
- Unbegrenzte Skalierbarkeit: Flexibles Wachstum je nach Bedarf
- Globale Datenverfügbarkeit: Standortübergreifende Datenzugriffe und -analysen
- Schnelle Implementierung: Produktiver Einsatz innerhalb von Tagen statt Monaten
Cloud-native OEE-Lösungen wie die SYMESTIC Manufacturing Platform bieten besonders für mittelständische und große Unternehmen mit mehreren Standorten erhebliche Vorteile.
SYMESTIC Cloud-MES: Eine Komplettlösung für OEE-Monitoring
Die SYMESTIC Manufacturing Platform ist eine cloud-native MES-Lösung, die umfassende Funktionen zur OEE-Erfassung, -Visualisierung und -Analyse bietet.
Plattform-Architektur
Die SYMESTIC-Lösung basiert auf einer mehrschichtigen Architektur:
- Konnektivitätsschicht: Verschiedene Optionen zur Maschinenanbindung
- DI Cloud Gateway: Direkte Signalerfassung über digitale Inputs
- OPC-UA Cloud Gateway: Standardisierte Anbindung an moderne Steuerungen
- Shopfloor Clients: Browserbasierte Terminals für manuelle Erfassung
- Cloud-Infrastruktur: Hochskalierbare Microsoft Azure-Plattform
- Microservice-Architektur für hohe Verfügbarkeit
- Umfassende Datensicherheit nach industriellen Standards
- Multi-Tenant-Fähigkeit mit strikter Mandantentrennung
- Manufacturing Apps: Modulare Anwendungen für verschiedene Anwendungsfälle
- MDE (Maschinendatenerfassung): Echtzeit-Überwachung für maximale Effizienz
- BDE (Betriebsdatenerfassung): Transparente und effiziente Datenerfassung
- Kennzahlen: Datenbasierte Entscheidungen in Echtzeit
OEE-spezifische Funktionalitäten
Die SYMESTIC-Plattform bietet spezialisierte Funktionen für das OEE-Monitoring:
Erfassung der Verfügbarkeitskomponente
- Automatische Zustandserkennung: Echtzeit-Erkennung von Produktions- und Stillstandszuständen
- Kategorisierte Stillstandserfassung: Strukturierte Erfassung von Stillstandsursachen
- Integriertes Störungsmanagement: Workflow-basierte Bearbeitung von Störungsmeldungen
- Schichtplanung: Flexible Definition von Produktionszeiten und Schichtmodellen
Erfassung der Leistungskomponente
- Automatische Stückzahlerfassung: Präzise Zählung produzierter Einheiten
- Dynamische Taktzeitanalyse: Erkennung von Abweichungen vom Idealwert
- Produkt- und auftragsspezifische Sollwerte: Flexible Referenzwerte je nach Produkt
Erfassung der Qualitätskomponente
- Integrierte Qualitätsprüfung: Direkte Erfassung von Ausschuss und Nacharbeit
- Fehlerursachenkatalog: Standardisierte Kategorisierung von Qualitätsproblemen
- Qualitätstrendanalysen: Erkennung von systematischen Qualitätsabweichungen
Visualisierung und Analyse
SYMESTIC bietet leistungsfähige Visualisierungs- und Analysefunktionen:
- Konfigurierbare Dashboards: Anpassbare Ansichten für verschiedene Nutzergruppen
- Echtzeit-Anzeigen: Live-Darstellung aktueller OEE-Werte und Produktionszustände
- Historische Analysen: Trenddarstellungen und Vergleichsanalysen über beliebige Zeiträume
- Kennzahlenhierarchien: Drill-Down von Werks- bis Maschinenebene
- Mobilzugriff: Native Apps für iOS und Android für standortunabhängigen Zugriff
Integrationsoptionen
Die SYMESTIC-Plattform bietet umfangreiche Integrationsmöglichkeiten:
- ERP-Integration: Bidirektionaler Datenaustausch mit SAP, Microsoft Dynamics und anderen Systemen
- REST-APIs: Standardisierte Schnittstellen für Drittanbieter-Integrationen
- 3rd Party Integration: Offene Schnittstellen für die Einbindung weiterer Systeme
Implementierungsansatz und ROI
Die Implementierung einer cloud-nativen OEE-Lösung wie SYMESTIC folgt einem strukturierten Prozess:
Phasenweiser Implementierungsansatz
- Evaluierung: Kennenlernen der Plattform und Funktionalitäten
- Pilot-Werk: Umsetzung in einem Pilotbereich zur Validierung
- Globaler Rollout: Schrittweise Ausweitung auf weitere Standorte
Dieser Ansatz ermöglicht eine risikoarme Einführung mit schnellen ersten Erfolgen.
Typische ROI-Faktoren
Anwender der SYMESTIC-Plattform berichten von messbaren Ergebnissen:
- Reduzierte Projektzeit: >90% Zeitersparnis bei der IT/OT-Integration
- Zeitersparnis bei Berichten: >90% Reduktion des Aufwands für KPI-Berichte
- CAPEX-Einsparungen: >95% durch SaaS-Modell ohne Initialinvestitionen
- Reduzierte Ausfallzeiten: Typischerweise 10% durch detaillierte Datenanalyse
- Effizienteres Reporting: 50% höhere Effizienz durch nahtlos integrierte Prozesse
Branchenübergreifende Anwendungen
Die SYMESTIC-Lösung wird in verschiedenen Branchen erfolgreich eingesetzt:
- Automobilindustrie: Spritzguss, Montage, Umformung (Yanfeng, Meleghy Automotive)
- Metallbearbeitung: Warmpresswerk, Bito, Schmiede
- Konsumgüter: Brita, Britax Römer, Neoperl
- Lebensmittelindustrie: Erlenbacher Backwaren, New Coffee, L.Stroetmann Saat
Besondere Vorzüge der SYMESTIC-Plattform
Gegenüber anderen OEE-Lösungen bietet die SYMESTIC-Plattform einige Alleinstellungsmerkmale:
Schnelle Implementierung
- Produktiver Einsatz innerhalb weniger Tage statt monatelanger Projekte
- Self-Service-Ansatz ermöglicht eigenständige Erweiterung durch den Kunden
Flexible Konnektivität
- Multiple Anbindungsoptionen für Bestandsanlagen und moderne Maschinen
- Unterstützung verschiedener Kommunikationswege (LAN, 4G/5G)
Transparentes Preismodell
- Planungssichere monatliche Abonnementkosten
- Keine versteckten Kosten für Updates oder Support
Mobile-First-Ansatz
- Native Apps für Mobilgeräte (iOS, Android)
- Standortunabhängiger Zugriff auf Produktionsdaten
Enterprise-Ready
- Globale Skalierbarkeit für multinationale Unternehmen
- Höchste Sicherheitsstandards durch Microsoft Azure-Infrastruktur
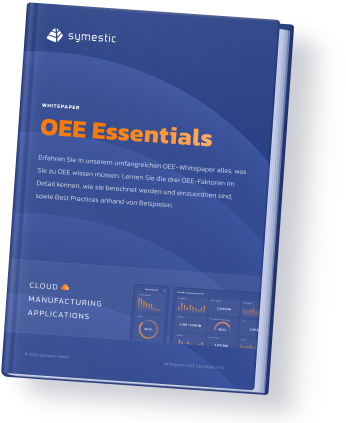
Fazit: Der Weg zur datengesteuerten Produktion
Die Implementierung einer modernen OEE-Software wie der SYMESTIC Manufacturing Platform markiert einen entscheidenden Schritt auf dem Weg zur datengesteuerten Produktion. Die Kombination aus präziser Datenerfassung, aussagekräftigen Visualisierungen und fortschrittlichen Analysefunktionen ermöglicht nicht nur die Messung, sondern auch die kontinuierliche Verbesserung der Gesamtanlageneffektivität.
Cloud-native Lösungen bieten dabei besondere Vorteile in Bezug auf Implementierungsgeschwindigkeit, Skalierbarkeit und Kosteneffizienz. Die SYMESTIC-Plattform verbindet diese Vorzüge mit branchenspezifischem Know-how und einer intuitiven Benutzeroberfläche, wodurch der Weg vom Datensammeln zum wertschöpfenden Handeln verkürzt wird.
Für Unternehmen, die ihre Wettbewerbsfähigkeit durch höhere Produktionseffizienz steigern möchten, bietet die digitalisierte OEE-Erfassung mit einer cloud-nativen Lösung einen überzeugenden Ansatz mit nachweisbarem ROI und schnellen Implementierungserfolgen.
Sie möchten mehr über die SYMESTIC Manufacturing Platform erfahren? Kontaktieren Sie uns für eine unverbindliche Demonstration oder einen 30-tägigen kostenlosen Testzugang.
Exklusives Whitepaper
Lernen Sie die modernsten Ansätze der Industrie 4.0, die Sie in Ihrer Produktion schon morgen umsetzen können, um innerhalb von 4 Wochen Ihre Kosten um gut 20% zu reduzieren.
mehr erfahren