Effizienzsteigerung in der Fertigung: Leitfaden für Ergebnisse
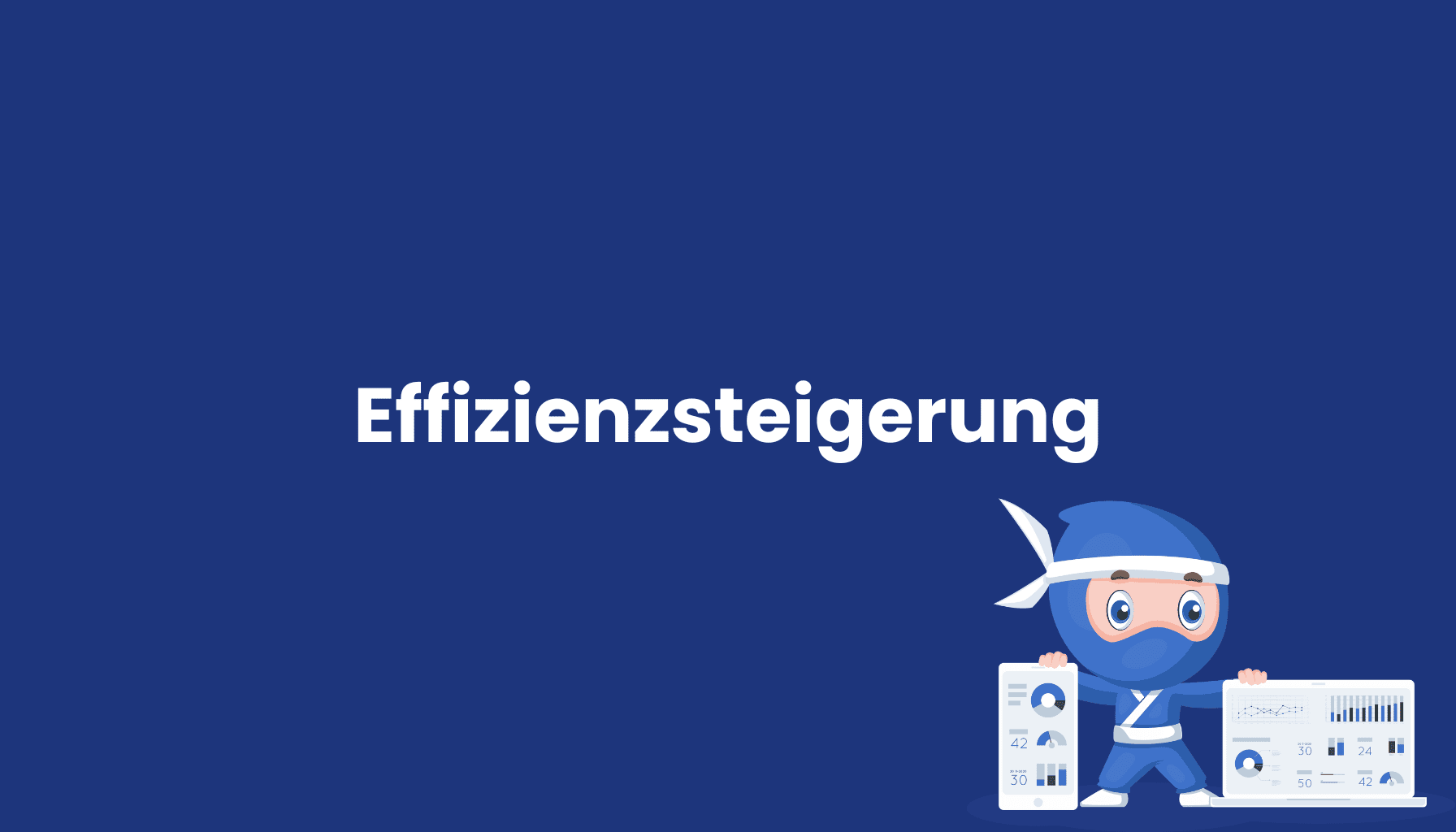
Was ist Effizienzsteigerung wirklich?
Effizienzsteigerung bezeichnet die systematische Optimierung des Verhältnisses zwischen eingesetzten Ressourcen (Input) und erzielten Ergebnissen (Output). In der Fertigung bedeutet dies konkret: Maximierung der Wertschöpfung bei gleichbleibenden oder reduzierten Kosten.
Definition: Effizienz = Ergebnis (Output) ÷ Aufwand (Input) × 100%
Wichtig dabei: Effizienz ist nicht gleichbedeutend mit Effektivität. Effektivität bedeutet "die richtigen Dinge tun" (Zielerreichung), während Effizienz bedeutet "die Dinge richtig tun" (Ressourcenoptimierung). Für nachhaltigen Unternehmenserfolg benötigen Sie beides.
Die 5 kritischen Dimensionen der Effizienzsteigerung
Die Steigerung der Effizienz in der Fertigung sollte ganzheitlich angegangen werden:
1. Prozesseffizienz
Die Optimierung der Abläufe bildet das Fundament jeder Effizienzsteigerung:
- Wertstromanalyse: Identifikation von Verschwendungen und Optimierungspotentialen
- SMED (Single Minute Exchange of Die): Reduzierung von Rüstzeiten
- TPM (Total Productive Maintenance): Minimierung von Anlagenausfällen
- Standardisierung: Etablierung von Best Practices und reproduzierbaren Abläufen
ROI-Tipp: Eine strukturierte Wertstromanalyse kann Durchlaufzeiten um 30-50% reduzieren und damit direkte Kosteneinsparungen generieren.
2. Ressourceneffizienz
Die optimale Nutzung von Material, Energie und Betriebsmitteln:
- Materialeffizienz: Reduzierung von Ausschuss und Verschnitt
- Energieeffizienz: Senkung des Energieverbrauchs pro Produktionseinheit
- Maschinenauslastung: Optimierung der Betriebszeiten und Kapazitäten
- Werkzeugmanagement: Systematische Verwaltung und Optimierung von Werkzeugen
Kennzahl-Fokus: Die OEE (Overall Equipment Effectiveness) ist der Goldstandard zur Messung der Anlageneffizienz: OEE = Verfügbarkeit × Leistung × Qualität
3. Informationseffizienz
Der optimale Fluss von Informationen ist entscheidend:
- Digitalisierung von Datenerfassung: Automatische Erfassung von Prozessdaten
- Transparenz in Echtzeit: Visualisierung relevanter KPIs auf Shopfloor-Ebene
- Datenbasierte Entscheidungen: Nutzung von Datenanalysen für schnellere und bessere Entscheidungen
- Papierlose Produktion: Digitalisierung von Dokumenten und Arbeitsanweisungen
Praxisbeispiel: Ein Automobilzulieferer konnte durch Einführung eines digitalen Dashboards für die Produktionssteuerung die Reaktionszeit auf Abweichungen von durchschnittlich 45 Minuten auf 8 Minuten reduzieren.
4. Personaleffizienz
Die Mitarbeiter sind der Schlüssel zu nachhaltiger Effizienz:
- Kompetenzentwicklung: Gezielte Weiterbildung und Skill-Matrix-Management
- Flexible Arbeitszeitmodelle: Anpassung der Personalkapazität an den Bedarf
- Arbeitsplatzgestaltung: Ergonomie und optimale Materialbereitstellung
- Mitarbeiterbeteiligung: Kontinuierlicher Verbesserungsprozess (KVP) durch Einbindung aller Mitarbeiterebenen
Expertentipp: Investieren Sie in strukturierte Problemlösungskompetenzen Ihrer Mitarbeiter. Unternehmen mit etablierten PDCA-Zyklen erreichen nachweislich 15-25% höhere Produktivitätssteigerungen.
5. Logistikeffizienz
Die optimale Versorgung der Produktion minimiert Wartezeiten:
- Just-in-Time (JIT): Bedarfsgerechte Materialbereitstellung
- Lageroptimierung: Minimierung von Beständen bei maximaler Versorgungssicherheit
- Intralogistik: Effiziente innerbetriebliche Materialflüsse
- Supply Chain Visibility: Transparenz über die gesamte Lieferkette
ROI-Rechner: Eine Reduzierung der Bestände um 20% führt bei einem typischen Fertigungsunternehmen zu Kosteneinsparungen von 3-5% des Jahresumsatzes.
Die 5 wirksamsten Technologien zur Effizienzsteigerung
Moderne Technologien sind entscheidende Enabler für signifikante Effizienzsprünge:
1. Manufacturing Execution System (MES)
Ein MES verbindet die Produktionsebene mit den übergeordneten Planungssystemen und ermöglicht:
- Echtzeit-Produktionsüberwachung
- Detaillierte Produktionsplanung und -steuerung
- Qualitätskontrolle und -sicherung
- Ressourcenmanagement und Kapazitätsplanung
Benchmark: Unternehmen mit vollintegriertem MES erreichen durchschnittlich 15-20% höhere Produktivität im Vergleich zu Betrieben mit isolierten IT-Lösungen.
2. Predictive Maintenance
Die vorausschauende Instandhaltung revolutioniert die Anlagenverfügbarkeit:
- Erkennung von Verschleiß vor dem Ausfall
- Optimierung der Wartungsintervalle
- Reduzierung ungeplanter Stillstände
- Verlängerung der Anlagenlebensdauer
Praxisbeispiel: Ein Lebensmittelhersteller konnte durch Implementierung von Predictive Maintenance die ungeplanten Stillstände um 72% reduzieren und gleichzeitig die Wartungskosten um 25% senken.
3. Automatisierung und Robotik
Intelligente Automation schafft Freiräume für wertschöpfende Tätigkeiten:
- Kollaborative Roboter (Cobots)
- Autonome Transportsysteme (AGVs/AMRs)
- Automatisierte Qualitätskontrolle
- Robotergestützte Montage und Fertigung
ROI-Tipp: Moderne Cobots amortisieren sich in der Regel innerhalb von 12-18 Monaten und bieten deutlich mehr Flexibilität als herkömmliche Industrieroboter.
4. Industrial Internet of Things (IIoT)
Vernetzte Produktionssysteme ermöglichen neue Dimensionen der Transparenz:
- Lückenlose Datenerfassung aus der Produktion
- Echtzeit-Analyse von Prozessparametern
- Vorausschauende Qualitätssicherung
- Edge Computing für schnelle Reaktionszeiten
Expertentipp: Beginnen Sie mit einem klar definierten Use Case, der schnellen ROI verspricht, statt mit einer unternehmensweiten IIoT-Implementierung.
5. Advanced Analytics und Künstliche Intelligenz
Datenbasierte Entscheidungen auf höchstem Niveau:
- Mustererkennungsalgorithmen für Prozessoptimierung
- Digitale Zwillinge zur Simulation von Produktionsszenarien
- Anomalieerkennung für frühzeitige Problemidentifikation
- Selbstoptimierende Produktionssysteme
Benchmark: Führende Unternehmen in der Fertigungsindustrie, die Advanced Analytics einsetzen, erzielen eine um 15-20% höhere Gesamtanlageneffektivität (OEE) als ihre Wettbewerber.
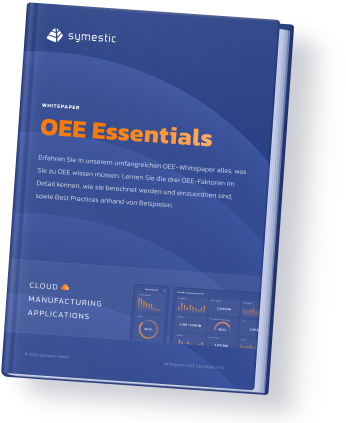
Erfolgsfaktoren für nachhaltige Effizienzsteigerungen
Die Implementierung der richtigen Technologien allein garantiert noch keine Effizienzsteigerung. Entscheidend sind folgende Erfolgsfaktoren:
1. Systemisches Denken
Betrachten Sie Effizienz ganzheitlich als System, nicht als isolierte Verbesserungsprojekte:
- Verständnis der Wechselwirkungen zwischen verschiedenen Prozessen
- Betrachtung der gesamten Wertschöpfungskette
- Vermeidung von Insellösungen und Suboptimierungen
- Fokus auf Engpässe gemäß der Theory of Constraints
2. Datenbasierte Entscheidungskultur
Etablieren Sie eine Kultur, in der Daten die Grundlage für Entscheidungen bilden:
- Definition und Visualisierung relevanter KPIs
- Transparenz über Ziele und Ergebnisse auf allen Ebenen
- Regelmäßige Leistungsreviews
- Faktenbasierte Problemlösung statt "Bauchgefühl"
3. Kontinuierliche Verbesserung
Schaffen Sie organisatorische Strukturen für stetige Weiterentwicklung:
- Etablierung eines kontinuierlichen Verbesserungsprozesses (KVP)
- Systematisches Problemlösungsmanagement
- Regelmäßige Kaizen-Events für größere Optimierungsprojekte
- Integration von Verbesserungsaktivitäten in den Arbeitsalltag
4. Change Management
Begleiten Sie Ihre Effizienzinitiative mit professionellem Change Management:
- Klare Vision und Kommunikation der Veränderungsziele
- Einbindung aller betroffenen Mitarbeiterebenen
- Qualifizierung für neue Technologien und Methoden
- Abbau von Widerständen durch aktive Beteiligung
5. Führungsverhalten
Die Führungskräfte müssen als Vorbilder und Ermöglicher agieren:
- Sichtbares Commitment zu Effizienzzielen
- Coaching und Unterstützung statt Kontrolle
- Bereitstellung notwendiger Ressourcen
- Konsequente Nachverfolgung von Maßnahmen
Wie Symestic Sie bei der Effizienzsteigerung unterstützt
Als Spezialist für moderne Fertigungstechnologien bietet Symestic ein umfassendes Portfolio zur Effizienzsteigerung:
- Cloud-basiertes MES: Echtzeitüberwachung und -steuerung Ihrer Produktion ohne komplexe IT-Infrastruktur
- OEE-Analyse: Detaillierte Kennzahlen zur Gesamtanlageneffektivität mit konkreten Optimierungsvorschlägen
- Predictive Maintenance: Vermeidung von Anlagenausfällen durch vorausschauende Instandhaltung
- Digitale Werkerführung: Papierlose Produktion mit digitalen Arbeitsanweisungen
- Smart Data Analytics: Datenbasierte Entscheidungsunterstützung für kontinuierliche Verbesserung
Unsere Lösungen sind modular aufgebaut und lassen sich schrittweise implementieren – für schnelle Ergebnisse bei minimalen Implementierungsrisiken.
Berechnung und Messung von Effizienzsteigerungen
Um Effizienzsteigerungen nachzuweisen und zu bewerten, sind aussagekräftige Kennzahlen unerlässlich:
OEE (Overall Equipment Effectiveness)
Die OEE ist die wichtigste Kennzahl zur Messung der Anlageneffizienz:
OEE = Verfügbarkeit × Leistung × Qualität
- Verfügbarkeit = Produktionszeit ÷ Geplante Produktionszeit
- Leistung = (Produzierte Menge × Idealzykluszeit) ÷ Produktionszeit
- Qualität = Gutteile ÷ Produzierte Menge
Benchmark: World-Class-Unternehmen erreichen OEE-Werte von >85%, während der Durchschnitt in der Fertigungsindustrie bei 60-65% liegt.
Durchlaufzeit und Work-in-Progress (WIP)
Die Optimierung des Materialflusses zeigt sich in:
- Durchlaufzeitverkürzung: Schnellere Auftragsabwicklung
- WIP-Reduzierung: Weniger gebundenes Kapital
- First-Time-Right-Rate: Weniger Nacharbeit und Ausschuss
- Bestandsreichweite: Niedrigere Lagerbestände
Expertentipp: Eine Halbierung der Durchlaufzeit führt typischerweise zu einer Reduktion der Bestände um 30-40% und einer Verbesserung der Termintreue um 20-30%.
Produktivitätskennzahlen
Die Effizienz des Personaleinsatzes wird gemessen durch:
- Output pro Mitarbeiterstunde: Direkte Messung der Arbeitsproduktivität
- Wertschöpfung pro Mitarbeiter: Berücksichtigt auch qualitative Aspekte
- Umsatz pro Mitarbeiter: Übergeordnete Kennzahl mit Benchmarking-Potenzial
- Automatisierungsgrad: Vergleich von automatisierten zu manuellen Prozessen
ROI-Rechner: Eine Steigerung der Arbeitsproduktivität um 10% führt bei einem typischen Fertigungsunternehmen zu einer Gewinnsteigerung von 3-5%.
Häufig gestellte Fragen zur Effizienzsteigerung
Was ist der Unterschied zwischen Effizienz und Produktivität?
Produktivität ist das Verhältnis zwischen erzeugter Leistung und eingesetzten Mitteln, meist bezogen auf einen einzelnen Faktor (z.B. Arbeitsproduktivität). Effizienz hingegen betrachtet die Wirksamkeit des gesamten Systems und berücksichtigt auch qualitative Aspekte wie Kundenzufriedenheit oder Flexibilität.
Welche Effizienzsteigerungsmaßnahmen haben den schnellsten ROI?
Erfahrungsgemäß zeigen diese Maßnahmen die schnellsten Ergebnisse:
- SMED (Single Minute Exchange of Die) zur Rüstzeitoptimierung
- OEE-Monitoring mit Verlustquellenanalyse
- 5S-Methodik zur Arbeitsplatzoptimierung
- Engpassoptimierung gemäß Theory of Constraints
- Standardisierung der wichtigsten Prozesse
Wie kann Effizienzsteigerung mit Flexibilität vereinbart werden?
Moderne Effizienzkonzepte setzen auf:
- Modulare Produktions- und Anlagenkonzepte
- Schnell umrüstbare Fertigungszellen
- Flexible Automatisierung (z.B. durch Cobots)
- Digitale Werkerführung für schnellen Produktwechsel
- Adaptives Produktionssteuerungssystem
Wie hoch sollten die Investitionen in Effizienzsteigerung sein?
Als Faustregel gilt: Investitionen in Effizienzsteigerung sollten 2-5% des Jahresumsatzes betragen und einen ROI von 200-300% innerhalb von 2-3 Jahren erzielen. Die konkrete Höhe hängt jedoch stark von der aktuellen Effizienz und dem Wettbewerbsumfeld ab.
Starten Sie Ihre Effizienzoffensive mit Symestic
Effizienzsteigerung ist kein einmaliges Projekt, sondern ein kontinuierlicher Prozess. Mit Symestic als Partner gewinnen Sie einen erfahrenen Begleiter auf diesem Weg.
Unsere maßgeschneiderten Lösungen passen sich Ihren spezifischen Anforderungen an und wachsen mit Ihren Bedürfnissen. Beginnend mit einem umfassenden Effizienz-Assessment definieren wir gemeinsam mit Ihnen die vielversprechendsten Optimierungspotenziale und entwickeln einen maßgeschneiderten Implementierungsplan.
Kontaktieren Sie uns noch heute für ein unverbindliches Beratungsgespräch und entdecken Sie, wie Sie mit Symestic Ihre Produktivität, Effizienz und Qualität nachhaltig steigern können.
Exklusives Whitepaper
Lernen Sie die modernsten Ansätze der Industrie 4.0, die Sie in Ihrer Produktion schon morgen umsetzen können, um innerhalb von 4 Wochen Ihre Kosten um gut 20% zu reduzieren.
mehr erfahren