Parts Per Million (PPM) - Definition, Vorteile und Anwendung
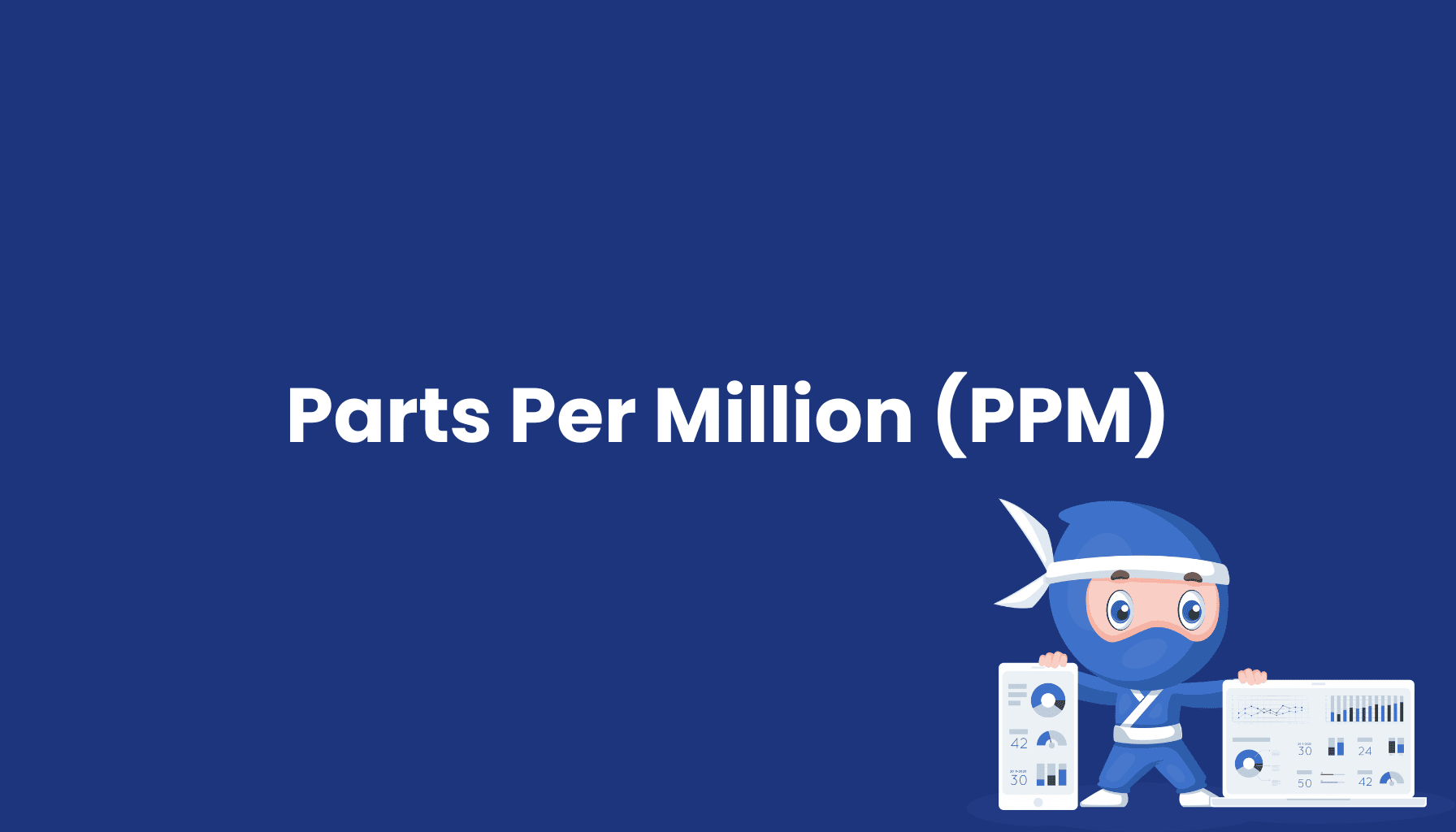
Was ist PPM (Parts Per Million)?
Parts Per Million (PPM) ist eine präzise Maßeinheit im Qualitätsmanagement, die angibt, wie viele Teile pro eine Million gefertigter Einheiten fehlerhaft sind. Als fundamentale Kennzahl in der Fertigungsindustrie dient PPM als kritischer Indikator für die Produktqualität, Prozesseffizienz und Zuverlässigkeit von Produktionssystemen.
Die PPM-Rate ist wesentlich feiner und präziser als Prozent- (10⁻²) oder Promilleangaben (10⁻³) und ermöglicht dadurch eine deutlich genauere Qualitätsbewertung, besonders in hochpräzisen Fertigungsbereichen wie der Automobilindustrie, Medizintechnik oder Elektronikproduktion.
Definition auf den Punkt gebracht: Ein PPM-Wert von 50 bedeutet, dass durchschnittlich 50 von 1.000.000 produzierten Teilen fehlerhaft sind – entsprechend einem Fehleranteil von 0,005%.
PPM im Qualitätsmanagement: Bedeutung und Stellenwert
Im modernen Qualitätsmanagement hat sich PPM als unverzichtbare Messgröße etabliert, die weit über einfache Fehlerquoten hinausgeht:
- Objektiver Qualitätsindikator: PPM liefert eine eindeutige, numerische Basis für die Beurteilung der Produktionsqualität
- Basis für Zulieferbewertung: In vielen Industrien werden verbindliche PPM-Grenzwerte vertraglich festgelegt
- Vergleichbarkeit: PPM ermöglicht den direkten Vergleich verschiedener Produktionslinien, Werke oder Zulieferer
- Integraler Bestandteil moderner QM-Systeme: PPM ist in IATF 16949, Six Sigma und anderen Qualitätsmanagementsystemen fest verankert
Typische PPM-Zielwerte nach Branchen
Branche | Typischer Zielwert | Spitzenwerte |
---|---|---|
Automobilindustrie | < 25 PPM | < 10 PPM |
Medizintechnik | < 10 PPM | < 3 PPM |
Elektronik | < 50 PPM | < 15 PPM |
Konsumgüter | < 100 PPM | < 50 PPM |
Pharmazeutik | < 5 PPM | < 1 PPM |
Exakte Berechnung von PPM-Werten
Die Berechnung des PPM-Werts erfolgt nach einer präzisen mathematischen Formel:
PPM = (Anzahl fehlerhafter Teile / Gesamtanzahl produzierter Teile) × 1.000.000
Beispielrechnung mit Schritt-für-Schritt-Erklärung:
- Ein Unternehmen produziert in einem Monat 250.000 Einheiten
- Während der Qualitätskontrolle werden 8 fehlerhafte Teile identifiziert
- PPM-Berechnung: (8 / 250.000) × 1.000.000 = 32 PPM
Dies bedeutet, dass bei einem vergleichbaren Produktionsvolumen von einer Million Teilen statistisch 32 fehlerhafte Einheiten zu erwarten wären.
Besonderheiten bei kleinen Produktionsmengen
Bei geringeren Produktionsmengen als einer Million Einheiten handelt es sich um eine hochgerechnete Kennzahl. Dies ist statthaft und üblich, kann aber bei sehr kleinen Stichprobengrößen zu statistischen Verzerrungen führen. Daher empfehlen wir:
- Bei Produktionsmengen unter 100.000 Einheiten: Erfassen Sie Daten über mehrere Produktionszeiträume
- Bei häufigen Produktwechseln: Berechnen Sie gruppenspezifische PPM-Werte nach Produktfamilien
- Bei neuen Produktlinien: Berücksichtigen Sie anfänglich höhere PPM-Raten in der Einlaufphase
Unterschied zwischen PPM und anderen Qualitätskennzahlen
Um PPM richtig einzuordnen, ist es wichtig, die Unterschiede zu anderen gängigen Qualitätskennzahlen zu verstehen:
Kennzahl | Definition | Typischer Anwendungsbereich | Vorteile gegenüber PPM |
---|---|---|---|
DPMO (Defects Per Million Opportunities) | Fehler pro Million Fehlermöglichkeiten | Six Sigma | Berücksichtigt mehrere Fehlermöglichkeiten pro Teil |
RTY (Rolled Throughput Yield) | Wahrscheinlichkeit, dass ein Produkt alle Prozessschritte ohne Fehler durchläuft | Prozessanalyse | Bewertet die Gesamtprozessleistung |
OEE (Overall Equipment Effectiveness) | Gesamtanlageneffektivität | Anlagenoptimierung | Berücksichtigt Verfügbarkeit, Leistung und Qualität |
FPY (First Pass Yield) | Anteil ohne Nacharbeit | Prozessverbesserung | Fokussiert auf "Beim ersten Mal richtig" |
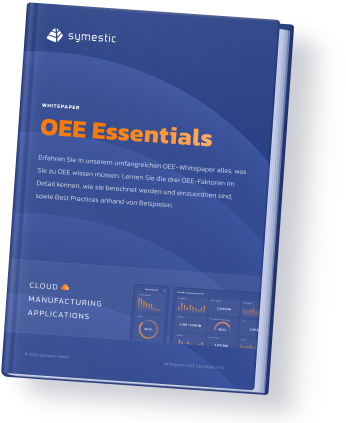
Warum ist PPM präziser als Prozentangaben?
Eine Fehlerrate von 0,1% klingt zunächst niedrig, entspricht aber 1.000 PPM – ein Wert, der in vielen Hightech-Industrien inakzeptabel wäre. Die PPM-Skala ermöglicht:
- Höhere Auflösung: Feinere Differenzierung zwischen Qualitätsniveaus
- Bessere Visualisierung von Fortschritten: Verbesserungen von z.B. 35 PPM auf 28 PPM sind klar erkennbar
- Angemessene Darstellung moderner Qualitätsstandards: Heutige Spitzenleistungen liegen oft unter 10 PPM
Implementierung einer erfolgreichen PPM-Reduzierungsstrategie
Eine systematische PPM-Reduktion erfordert einen ganzheitlichen Ansatz, der alle Unternehmensbereiche einbezieht:
1. PPM-Analyse und -Tracking
- Detaillierte Datenerfassung: Implementieren Sie ein MES (Manufacturing Execution System) zur automatischen Erfassung aller Fehlerarten
- Fehlerklassifizierung: Kategorisieren Sie Fehler nach Art, Schwere und Entstehungsort
- Statistische Auswertung: Identifizieren Sie Muster, Trends und Korrelationen in den Fehlerarten
- Echtzeit-Monitoring: Verfolgen Sie PPM-Werte in Echtzeit, um sofort auf Abweichungen reagieren zu können
2. Ursachenanalyse (Root Cause Analysis)
- Fehlerursachenkatalog: Erstellen Sie eine strukturierte Übersicht möglicher Fehlerursachen
- Ishikawa-Diagramm: Visualisieren Sie Ursache-Wirkungs-Beziehungen für häufige Fehlerarten
- 5-Why-Methode: Hinterfragen Sie jeden Fehler systematisch, um Grundursachen statt Symptome zu identifizieren
- FMEA (Fehlermöglichkeits- und Einflussanalyse): Bewerten Sie potenzielle Fehlermodi präventiv
3. Implementierung präventiver Maßnahmen
- Poka Yoke (Fehlervermeidung): Implementieren Sie technische Vorkehrungen, die Fehler unmöglich machen
- SPC (Statistische Prozesssteuerung): Überwachen Sie Prozessparameter, um Abweichungen vor der Fehlerentstehung zu erkennen
- Mitarbeiterschulung: Stärken Sie das Qualitätsbewusstsein und vermitteln Sie spezifische Problemlösungskompetenzen
- Design for Manufacturability: Optimieren Sie Produktdesigns für einfachere und fehlerresistentere Fertigung
4. Kontinuierliche Prozessverbesserung
- PDCA-Zyklus: Etablieren Sie einen strukturierten Verbesserungsprozess
- Kaizen-Events: Führen Sie regelmäßige Workshops zur PPM-Reduktion durch
- Benchmarking: Vergleichen Sie PPM-Werte mit Branchenführern und adaptieren Sie Best Practices
- Validierung: Überprüfen Sie die Wirksamkeit implementierter Maßnahmen anhand der PPM-Entwicklung
PPM-Messung mit modernen Manufacturing Execution Systems (MES)
Die präzise Erfassung und Auswertung von PPM-Daten wird heute zunehmend durch digitale Fertigungssysteme unterstützt:
Vorteile eines MES-basierten PPM-Trackings:
- Automatisierte Datenerfassung: Eliminierung manueller Fehler bei der Qualitätsdatenerfassung
- Echtzeit-Monitoring: Sofortige Erkennung von Qualitätsabweichungen
- Umfassende Analysemöglichkeiten: Detaillierte Aufschlüsselung nach Produkten, Linien, Schichten und Zeiträumen
- KI-gestützte Prognosen: Vorhersage von PPM-Entwicklungen basierend auf historischen Daten
- Integration in die Produktionssteuerung: Automatische Einleitung von Korrekturmaßnahmen bei Überschreitung kritischer PPM-Schwellen
Wichtige MES-Funktionen für effektives PPM-Management:
- Fehlererfassungsmodule: Digitale Erfassung und Kategorisierung von Fehlern direkt an der Linie
- Statistische Prozesssteuerung: Frühwarnsystem für Prozessabweichungen vor Fehlerereignissen
- Fehlertrend-Visualisierung: Grafische Darstellung der PPM-Entwicklung über Zeit, Produktgruppen oder Prozessparameter
- Automatisierte Berichterstattung: Regelmäßige PPM-Reports für verschiedene Führungsebenen
- Rückverfolgbarkeit: Verknüpfung von Fehlermustern mit spezifischen Chargen, Materialien oder Maschinenparametern
Fallstudie: PPM-Reduktion durch MES-Implementation
Ein mittelständischer Automobilzulieferer konnte durch die Einführung eines integrierten MES-Systems mit dediziertem PPM-Modul folgende Verbesserungen erzielen:
- Reduktion der PPM-Rate von 45 auf 12 innerhalb von 8 Monaten
- 67% schnellere Reaktionszeit bei Qualitätsabweichungen
- Produktivitätssteigerung um 14% durch Reduzierung von Nacharbeit und Ausschuss
- ROI der MES-Investition innerhalb von 11 Monaten
PPM-Ziele in verschiedenen Qualitätsmanagementsystemen
Die PPM-Rate ist in verschiedenen Qualitätsmanagementsystemen unterschiedlich positioniert:
IATF 16949 (Automobilindustrie)
- Explizite Anforderung zur PPM-Messung und kontinuierlichen Verbesserung
- OEM-spezifische PPM-Zielwerte als vertragliche Anforderung
- Eskalationsprozesse bei Nichterreichen der PPM-Ziele
- PPM als Schlüsselindikator für die Lieferantenbewertung
Six Sigma
- PPM als direkte Ableitung aus dem Sigma-Level:
- 6σ = 3,4 PPM
- 5σ = 233 PPM
- 4σ = 6.210 PPM
- 3σ = 66.807 PPM
- Strukturierte DMAIC-Methodik zur systematischen PPM-Reduktion
- Statistische Werkzeuge zur Prozessoptimierung
ISO 9001:2015
- Keine spezifischen PPM-Anforderungen, aber PPM als typische Kennzahl zur Erfüllung der allgemeinen Qualitätsanforderungen
- PPM-Tracking oft als Teil des Anforderungen zur Messung, Analyse und Verbesserung implementiert
Herausforderungen beim PPM-Management und deren Lösungen
Bei der praktischen Umsetzung eines effektiven PPM-Managements treten typische Herausforderungen auf:
Herausforderung | Lösungsansatz |
---|---|
Stichprobenproblematik | Statistisch fundierte Prüfpläne mit angemessenen Stichprobengrößen; Ergänzung durch alternative Qualitätskennzahlen bei kleinen Losgrößen |
Fehlerklassifizierung | Klare Definitionen für Fehlerkategorien; Schulung der Qualitätsprüfer; Regelmäßige Kalibrierungssessions |
Datenintegrität | Digitale Erfassungssysteme mit Plausibilitätsprüfungen; Automatisierte Datenerfassung wo möglich |
PPM-Manipulation | Vier-Augen-Prinzip; Stichprobenartige Verifikation; Trennung von Produktion und Qualitätskontrolle |
"Null-PPM"-Forderungen | Offene Diskussion mit Kunden; Definition alternativer Qualitätsziele; Risikomanagement-Ansatz |
Spezialfall: Die "Null-PPM"-Diskussion
In der Praxis werden oft "Null-PPM"-Forderungen gestellt, insbesondere bei sicherheitskritischen Komponenten. Diese sind jedoch aus statistischer Sicht problematisch:
- Mathematische Unmöglichkeit: Ein tatsächlicher Null-PPM-Wert würde eine fehlerfreie Produktion ohne jegliche Varianz bedeuten
- Negative Nebeneffekte: Überzogene PPM-Forderungen können zu Fehlermaskierung, Datenmanipulation oder unverhältnismäßigen Kosten führen
- Sinnvolle Alternative: Risikoorientierter Ansatz mit FMEA, besonderen Merkmalen und spezifischen Kontrollplänen
Praxisgerechter Umgang mit Null-PPM-Forderungen:
- Differenzierte Qualitätsziele: Besonders strenge PPM-Ziele nur für sicherheits- und funktionskritische Merkmale
- Ergänzende Qualitätsmaßnahmen: Fehlerverhinderung durch Poka Yoke, 100%-Prüfung kritischer Merkmale
- Prozessfähigkeitsindizes: Fokus auf Cpk > 1,67 als Nachweis stabiler, beherrschter Prozesse
- Übergreifende Qualitätsvereinbarungen: Dialog mit Kunden über realistische Qualitätsziele und geeignete Messmethoden
PPM-Erfolgsfaktoren: Best Practices aus der Industrie
Unternehmen, die nachhaltig exzellente PPM-Werte erreichen, setzen typischerweise auf folgende Praktiken:
1. Ganzheitlicher Qualitätsansatz
- Total Quality Management: Qualität als Verantwortung aller Mitarbeiter und Abteilungen
- Design for Quality: Berücksichtigung von Fertigungsaspekten bereits in der Produktentwicklung
- Qualitätsorientierte Unternehmenskultur: Offener Umgang mit Fehlern und aktive Suche nach Verbesserungspotentialen
2. Datenbasierte Entscheidungsfindung
- Advanced Analytics: Nutzung komplexer Datenanalysemethoden zur Identifikation verborgener Zusammenhänge
- Korrelationsanalysen: Verbindung von PPM-Daten mit Prozessparametern, Materialchargen und anderen Faktoren
- Prediktive Qualitätsmodelle: Entwicklung von Algorithmen zur Vorhersage potenzieller Qualitätsprobleme
3. Technologische Enabler
- Inline-Messtechnik: Kontinuierliche Prozessüberwachung statt stichprobenartiger Endkontrolle
- Machine Learning: Erkennung subtiler Muster in Qualitätsdaten durch KI-Systeme
- Digitaler Zwilling: Simulation von Produktionsprozessen zur präventiven Erkennung von Fehlerrisiken
4. Lieferantenmanagement
- PPM-basierte Lieferantenbewertung: Systematische Erfassung und Bewertung der Zuliefererqualität
- Entwicklungspartnerschaften: Enge Zusammenarbeit mit Schlüssellieferanten zur gemeinsamen PPM-Reduktion
- Qualitätsvorausplanung: Frühzeitige Einbindung von Lieferanten in Entwicklungsprojekte
Die Zukunft des PPM-Managements: Trends und Entwicklungen
Das Management von PPM-Kennzahlen entwickelt sich mit den technologischen Möglichkeiten und Marktanforderungen stetig weiter:
Industrie 4.0 und PPM
- Echtzeit-PPM: Kontinuierliche, sekündliche Berechnung und Visualisierung von PPM-Werten
- Selbstoptimierung: Fertigungssysteme, die eigenständig auf PPM-Abweichungen reagieren
- Durchgängige Rückverfolgbarkeit: Lückenlose Dokumentation aller qualitätsrelevanten Parameter
KI-gestützte Qualitätsprognose
- Vorhersagemodelle: Identifikation potenzieller Qualitätsprobleme bevor sie auftreten
- Automatisierte CAPA-Prozesse: KI-gestützte Ableitung wirksamer Korrektur- und Vorbeugemaßnahmen
- Bildverarbeitungssysteme: Visuelle Fehleridentifikation mit höherer Präzision als menschliche Prüfer
Erweiterte PPM-Konzepte
- Lifecycle-PPM: Berücksichtigung der Produktqualität über den gesamten Lebenszyklus
- Risk-adjusted PPM: Gewichtung von Fehlern nach Risikopotential und Auswirkung
- Customer-perceived PPM: Fokus auf aus Kundensicht relevante Qualitätsmerkmale
PPM in verschiedenen Anwendungsbereichen
Über die klassische Fehlerquote in der Fertigung hinaus wird PPM in verschiedenen Kontexten eingesetzt:
PPM als Maßeinheit in Technik und Wissenschaft
- Analytik: Konzentration von Substanzen (z.B. 5 ppm Chlor in Trinkwasser)
- Messtechnik: Präzision von Messinstrumenten (z.B. ±10 ppm Genauigkeit)
- Elektronik: Frequenzstabilität von Oszillatoren (z.B. 25 ppm Toleranz)
PPM im Umwelt- und Gesundheitsbereich
- Luftqualität: Schadstoffkonzentrationen (z.B. CO₂-Gehalt in ppm)
- Wasseranalytik: Grenzwerte für Verunreinigungen
- Lebensmittelsicherheit: Zulässige Rückstandsmengen
PPM als Teil der digitalen Transformation in der Fertigung
Die systematische PPM-Optimierung ist ein wichtiger Baustein der digitalen Transformation in der Produktion:
- Integrierte Datenlandschaft: Verknüpfung von PPM-Daten mit anderen Betriebskennzahlen
- End-to-End-Qualitätsmanagement: Durchgängige Qualitätsüberwachung von Lieferanten bis zum Endkunden
- Datengestützte Geschäftsmodelle: Nutzung von Qualitätsdaten für erweiterte Serviceangebote und Garantieleistungen
Fazit: PPM als strategischer Wettbewerbsfaktor
Die PPM-Rate ist weit mehr als eine technische Kennzahl – sie ist ein strategischer Leistungsindikator mit direkten Auswirkungen auf:
- Kundenzufriedenheit und -bindung
- Marktposition und Markenstärke
- Kostenstruktur und Profitabilität
- Innovationsfähigkeit und Agilität
Unternehmen, die ihre PPM-Werte konsequent optimieren, schaffen nicht nur qualitativ hochwertigere Produkte, sondern etablieren auch die Grundlage für langfristigen Geschäftserfolg in einem zunehmend qualitätsorientierten globalen Markt.
Häufig gestellte Fragen zu PPM
Ist ein PPM-Wert von Null realistisch erreichbar?
Ein theoretischer PPM-Wert von absolut Null ist in der Fertigung praktisch nicht erreichbar, da selbst bei höchster Prozessstabilität stets eine gewisse statistische Varianz verbleibt. Nachhaltige Werte unter 10 PPM gelten jedoch als exzellent und sind mit modernen Fertigungsmethoden für viele Produkte erreichbar.
Wie kann ein kleines Unternehmen PPM-Tracking implementieren?
Auch ohne umfangreiche MES-Systeme können kleine Unternehmen effektives PPM-Tracking einführen:
- Nutzung von Excel-basierten Tracking-Tools mit statistischen Funktionen
- Fokussierung auf wesentliche Qualitätsmerkmale statt umfassender Datenerfassung
- Schrittweise Digitalisierung mit kostengünstigen Cloud-basierten QM-Lösungen
- Schulung von Mitarbeitern in grundlegenden statistischen Methoden
Wie kann ich PPM-Werte zwischen verschiedenen Produkten vergleichen?
Beim produktübergreifenden PPM-Vergleich sollten Sie beachten:
- Komplexitätsunterschiede (ein komplexeres Produkt hat mehr Fehlermöglichkeiten)
- Vergleichbare Prüftiefe und -methodik
- Ähnliche Produktionsreife und -volumen
- Normierung auf vergleichbare Fehlermöglichkeiten (DPMO-Ansatz)
Welche Rolle spielt PPM bei der Lieferantenauswahl?
Bei der Bewertung potenzieller Lieferanten ist die PPM-Rate ein wichtiges, aber nicht das einzige Kriterium:
- Historische PPM-Entwicklung (Trend über Zeit)
- PPM-Management-System des Lieferanten
- Reaktionsfähigkeit bei Qualitätsabweichungen
- Transparenz in der Qualitätsberichterstattung
Wie hängen PPM und Wirtschaftlichkeit zusammen?
Die PPM-Rate beeinflusst die Wirtschaftlichkeit auf verschiedenen Ebenen:
- Direkte Fehlerkosten (Ausschuss, Nacharbeit, Garantieleistungen)
- Indirekte Kosten (Lieferverzögerungen, Kundenbeschwerden, Reputationsschäden)
- Präventionskosten (Qualitätssicherungssysteme, Schulungen, verbesserte Prozesse)
- Opportunitätskosten (verlorene Aufträge durch Qualitätsprobleme)
Eine ausgewogene PPM-Strategie berücksichtigt sowohl Qualitätsziele als auch wirtschaftliche Aspekte.
Exklusives Whitepaper
Lernen Sie die modernsten Ansätze der Industrie 4.0, die Sie in Ihrer Produktion schon morgen umsetzen können, um innerhalb von 4 Wochen Ihre Kosten um gut 20% zu reduzieren.
mehr erfahren