Total Effective Equipment Performance (TEEP) - Definition & Vorteile
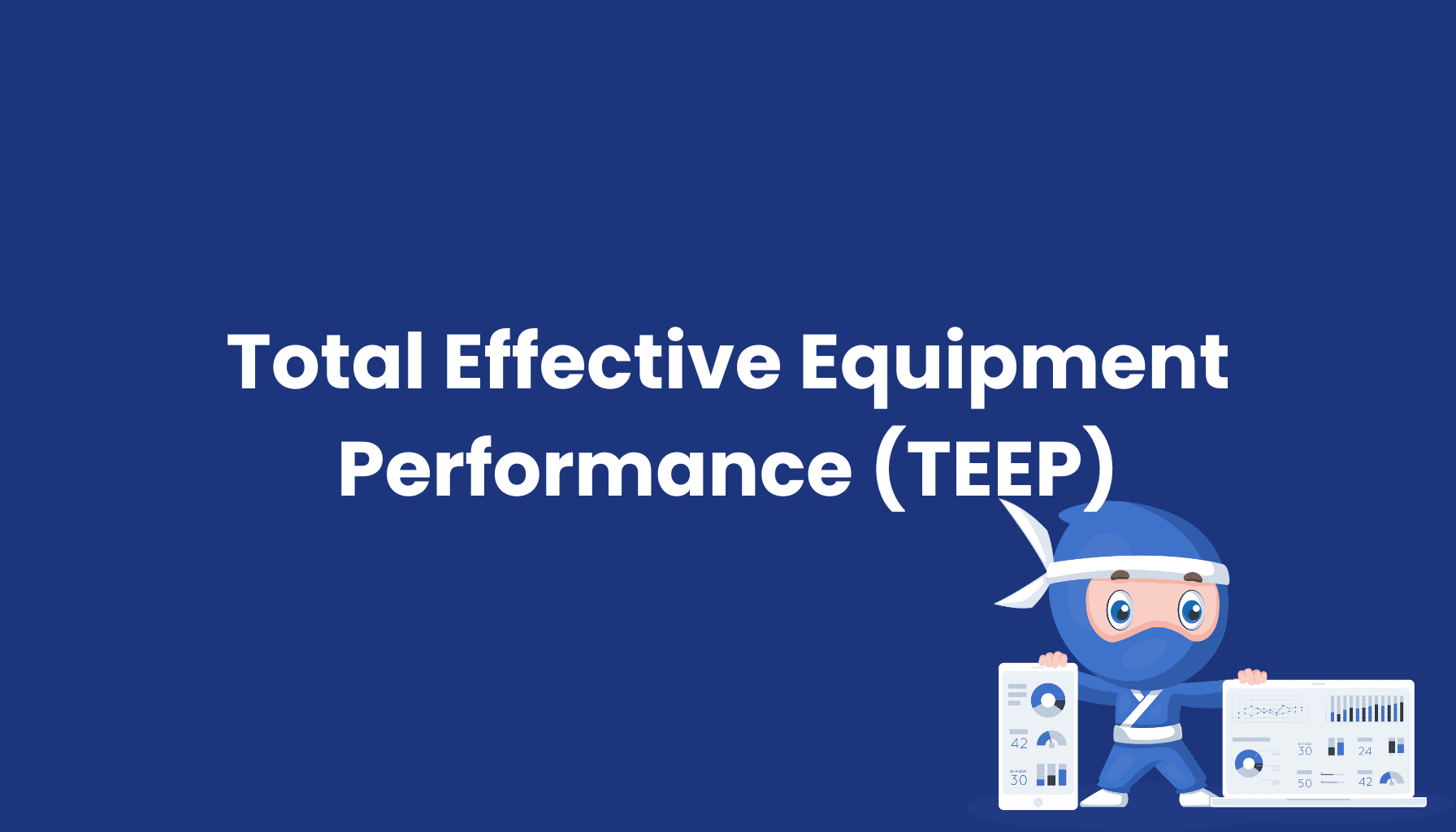
Was ist TEEP?
TEEP (Total Effective Equipment Performance) ist die umfassendste Kennzahl zur Bewertung der Produktionskapazitätsnutzung. Anders als die bekannte OEE-Kennzahl (Overall Equipment Effectiveness), die die Effizienz innerhalb der geplanten Produktionszeit misst, bezieht TEEP die gesamte Kalenderzeit (24/7/365) in die Betrachtung ein.
Dieser Artikel behandelt einen spezifischen Aspekt der Overall Equipment Effectiveness (OEE). Für einen umfassenden Überblick und Grundlagen zur OEE empfehlen wir unseren Hauptartikel:
Zum OEE-HauptartikelDefinition: TEEP zeigt, wie effektiv Sie die theoretisch maximal verfügbare Zeit Ihrer Anlagen tatsächlich nutzen.
TEEP vs. OEE: Der entscheidende Unterschied
Die Beziehung zwischen TEEP und OEE lässt sich präzise definieren:
TEEP = OEE × Anlagennutzungsgrad
Wobei:
Anlagennutzungsgrad = Geplante Produktionszeit ÷ Kalenderzeit
OEE fokussiert auf die Effizienz während der geplanten Betriebszeit und blendet geplante Stillstände wie Schichtwechsel oder Wochenenden aus.
TEEP hingegen betrachtet das absolute Produktivitätspotenzial und zeigt auf, ob zusätzliche Kapazitäten durch Erweiterung der Produktionszeiten genutzt werden könnten.
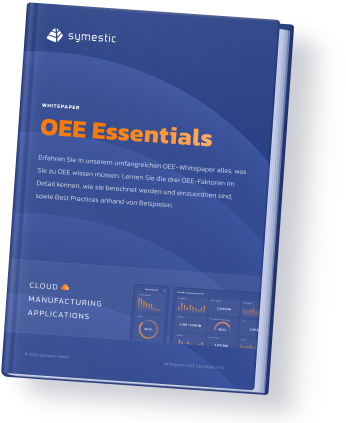
Praktisches Berechnungsbeispiel
Betrachten Sie folgendes Szenario:
- Kalenderzeit: 168 Stunden (7 Tage × 24 Stunden)
- Geplante Produktion: 80 Stunden (5 Tage × 16 Stunden)
- OEE: 75%
Anlagennutzungsgrad = 80 ÷ 168 = 47,6%
TEEP = 75% × 47,6% = 35,7%
Dies bedeutet: Nur 35,7% der theoretisch verfügbaren Anlagenkapazität werden produktiv genutzt.
Warum TEEP für Entscheidungsträger unverzichtbar ist
TEEP liefert drei kritische Erkenntnisse, die über die OEE hinausgehen:
- Kapazitätsreserven identifizieren: TEEP zeigt ungenutzte Zeiträume, die für zusätzliche Produktion genutzt werden könnten, ohne in neue Anlagen investieren zu müssen.
- Make-or-Buy-Entscheidungen fundieren: Ein niedriger TEEP-Wert kann bedeuten, dass Kapazitäten für Zusatzaufträge vorhanden sind, statt diese extern zu vergeben.
- Investitionsplanung optimieren: TEEP hilft zu erkennen, ob Kapazitätsengpässe durch erweiterte Betriebszeiten oder erst durch Neuinvestitionen gelöst werden können.
Wann TEEP wichtiger ist als OEE
In diesen Situationen sollten Sie besonders auf TEEP achten:
- Hohe Anlagenkosten: Je teurer die Maschinen, desto wichtiger ist die Maximierung der Nutzungsdauer.
- Kapazitätsengpässe: Bevor Sie in neue Anlagen investieren, prüfen Sie die Erweiterung der Betriebszeiten.
- Saisonale Schwankungen: TEEP hilft bei der Identifikation von Zeiträumen, die für vorgezogene Produktion genutzt werden können.
- Kontinuierliche Fertigung: Branchen mit hohen Anfahrkosten (Stahl, Papier, Chemie) profitieren besonders von TEEP-Analysen.
3 Strategien zur TEEP-Optimierung
1. Anlagennutzungsgrad erhöhen
- Einführung zusätzlicher Schichten
- Durchgehende Produktion an Wochenenden
- Reduzierung geplanter Stillstandszeiten
- Verlagerung von Wartung in produktionsfreie Zeiten
Praxistipp: Eine Ausweitung der Betriebszeit von 5 auf 7 Tage kann den TEEP-Wert um bis zu 40% steigern – ohne jegliche Investition in neue Anlagen.
2. OEE-Komponenten verbessern
- Verfügbarkeit: Reduzierung ungeplanter Stillstände
- Leistung: Erhöhung der Zyklusgeschwindigkeit
- Qualität: Minimierung von Ausschuss und Nacharbeit
Faktencheck: Während typische OEE-Werte in der Fertigungsindustrie bei 60-70% liegen, erreichen Weltklasse-Unternehmen Werte über 85%.
3. Synchronisation der Wertschöpfungskette
- Engpassanlagen mit höchster Priorität optimieren
- Mehrmaschinenbesetzung an Nicht-Engpassanlagen
- Kapazitätsplanung mit Fokus auf Engpässe
- Integration von Lieferanten und Kunden in die Kapazitätsplanung
Experten-Insight: Nach der Theory of Constraints (TOC) bestimmt der Engpass den maximalen Durchsatz des Gesamtsystems – hier sollte der TEEP-Wert maximiert werden.
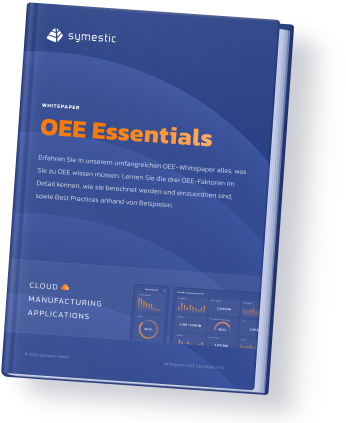
TEEP-Benchmarks nach Branchen
Typische TEEP-Werte variieren je nach Branche erheblich:
Branche | Durchschnittlicher TEEP | Spitzenwerte |
---|---|---|
Automobilindustrie | 35-45% | >60% |
Prozessindustrie | 50-65% | >75% |
Konsumgüter | 30-40% | >55% |
Maschinenbau | 25-35% | >50% |
Fazit: TEEP als strategische Kennzahl
TEEP ist mehr als eine Erweiterung der OEE – es ist ein strategisches Werkzeug zur Bewertung der Gesamtanlageneffektivität über die gesamte verfügbare Zeit. In Zeiten steigender Anlagenkosten und wachsenden Wettbewerbsdrucks kann ein systematisches TEEP-Management entscheidende Wettbewerbsvorteile schaffen.
Mit Symestic's Manufacturing Excellence Plattform überwachen Sie nicht nur OEE in Echtzeit, sondern auch TEEP – und identifizieren so verborgene Produktivitätspotenziale, die über die üblichen Optimierungsansätze hinausgehen.
Kontaktieren Sie uns für eine detaillierte TEEP-Analyse Ihrer Produktionsanlagen und entdecken Sie ungenutzte Kapazitätsreserven in Ihrem Unternehmen.
Exklusives Whitepaper
Lernen Sie die modernsten Ansätze der Industrie 4.0, die Sie in Ihrer Produktion schon morgen umsetzen können, um innerhalb von 4 Wochen Ihre Kosten um gut 20% zu reduzieren.
mehr erfahren