CIP (Continuous Improvement Process): Complete Guide 2025
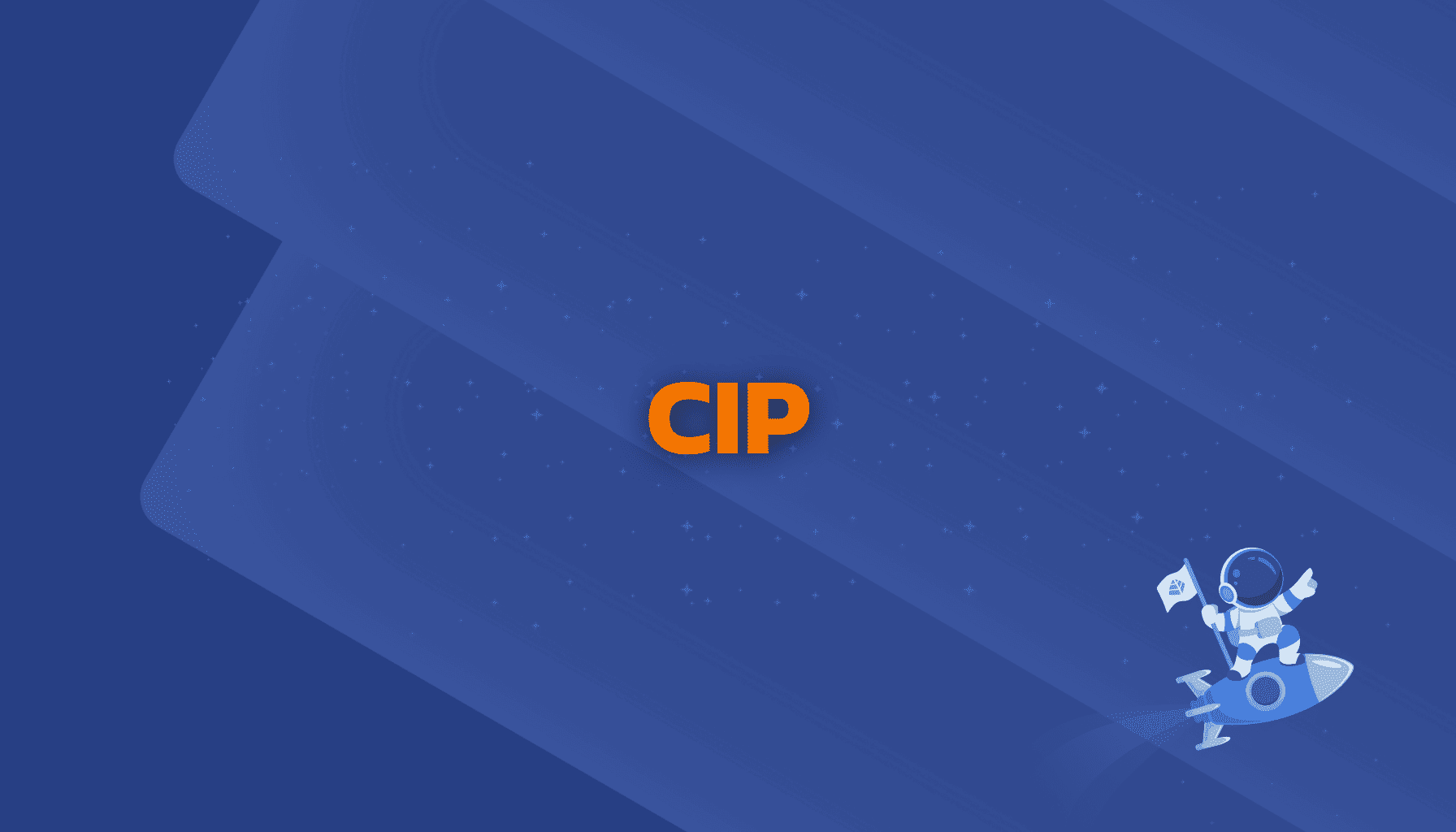
The 3 Key Success Factors for CIP:
- • Implement PDCA cycle (Plan, Do, Check, Act) as your core framework
- • Actively involve employees and implement suggestions promptly
- • Prioritize multiple small improvements over few large projects
- What is CIP in Practice?
- The 6 Essential CIP Tools (Six Sigma, Kaizen, Value Stream Mapping)
- Step-by-Step CIP Implementation Guide
- Proven Strategies for Sustainable Process Improvement
- Tips for Developing a CIP Culture
What is CIP in Practice?
CIP has established itself as a key methodology in modern manufacturing. While large corporations like Toyota have achieved productivity increases of up to 30%, medium-sized companies are now also successfully implementing Continuous Improvement processes. The crucial advantage: Instead of major restructuring, CIP focuses on quickly implementable, small improvements in daily operations.The practical impacts are measurable:
- Increased OEE metrics in production
- Reduced cycle times across all processes
- Minimized waste in value creation
- Higher employee satisfaction through active involvement
The 6 Essential CIP Tools for Practice
Successful organizations use a combination of proven methods. These 6 tools have proven particularly effective:
1. Six Sigma
The data-driven Six Sigma methodology systematically reduces process variations. Using the DMAIC cycle (Define, Measure, Analyze, Improve, Control), problems are analyzed and solved in a structured way.
2. Kaizen
This Japanese method focuses on daily micro-improvements implemented by all employees. The emphasis is on quickly actionable optimizations directly at the workplace. Toyota has used Kaizen for decades as the foundation of its success.
3. Value Stream Mapping
This visual tool creates transparency in material flows and information pathways. Waste becomes immediately visible and can be specifically eliminated. Practice shows: cycle times can often be reduced by 30-50%.
4. 5S Method
Sort, Set in order, Shine, Standardize, and Sustain - these 5 steps create the foundation for efficient processes. An indispensable tool, particularly in production environments.
5. PDCA Cycle
The Plan-Do-Check-Act cycle structures the improvement process. It ensures that changes are not only implemented but also verified for effectiveness.
6. Poka Yoke
This "fool-proof" design of processes and tools prevents errors before they occur. A classic example: USB connectors that can only be inserted in one direction.
⚠️Important note: These tools work best in combination. While Six Sigma provides the analytical foundation, Kaizen ensures daily improvement, and Value Stream Mapping shows where optimizations will have the greatest impact.
Step-by-Step CIP Implementation Guide
Successful CIP implementation follows a proven path. Our practical experience shows: These 5 steps ensure successful implementation in your organization:
Analyze Current State
- Conduct inventory of current processes
- Identify bottlenecks and weak points
- Define KPIs for later success measurement
- Identify quick wins for early success
Prepare Management and Team
- Train leaders as role models
- Assemble CIP team from various departments
- Clearly assign responsibilities
- Establish communication structures
Launch Pilot Project
- Choose manageable area for first CIP run
- Actively involve on-site employees
- Implement first improvement suggestions promptly
- Document and communicate successes
Systematic Expansion
- Transfer successful methods to other areas
- Conduct regular CIP workshops
- Continuously train employees
- Systematically capture improvement suggestions
Ensure Sustainability
- Establish standards for successful improvements
- Introduce regular reviews
- Continuously monitor KPIs
- Maintain motivation through recognition and rewards
💡Practice Tip: The most common mistake in CIP implementation is trying to do too much at once. Focus on one area first and celebrate early successes. This creates acceptance and motivation for further rollout.
Proven CIP Strategies: How to Achieve Sustainable Process Improvement
Leading manufacturing companies like Toyota, Bosch and Daimler achieve productivity increases of up to 30% with CIP.
Their successful strategies can be summarized in four proven CIP methods:
Establish and Monitor CIP Metrics
- Make OEE improvements measurable
- Conduct weekly CIP audits
- Identify improvement potential through data analysis
- Calculate ROI for each CIP measure
💻Learn here how to successfully calculate OEE.
Continuous Employee Development in CIP
- Daily CIP meetings (max. 15 minutes)
- 24-hour feedback on improvement suggestions
- Build CIP champions (Six Sigma) in each team
- Conduct monthly CIP training
Implement CIP Standards
- Use Value Stream Mapping as foundation
- Integrate Six Sigma methods
- Conduct regular Kaizen events
- Consistently apply PDCA cycle
Implement Digital CIP Tools
- Process optimization through real-time monitoring
- CIP software for systematic idea management
- Digital CIP boards in production
- Automated CIP success measurement
💡 Practice Tip for CIP Implementation: Start with a 30-day CIP challenge. A realistic goal is 30 implemented improvements in 30 days. This creates quick wins and motivates the team for long-term CIP initiatives.
Successfully Developing a CIP Culture: Best Practices
Developing a vibrant CIP culture determines the long-term success of the Continuous Improvement Process.
Leading manufacturing companies focus on the following CIP success factors:
1. Establish CIP Leadership
- Train leaders as active CIP role models
- Daily shopfloor walks by management
- Provide direct feedback on CIP suggestions
- Publicly acknowledge and celebrate successes
2. Strengthen CIP Communication
- Weekly CIP updates in teams
- Share success stories company-wide
- Visualize transparent CIP metrics
- Establish regular CIP newsletters
3. Foster CIP Motivation
- Guarantee quick implementation of improvement ideas
- Award monthly CIP recognition
- Celebrate team successes together
- Create career paths for CIP experts
💡 Practice Tip: The best CIP cultures emerge through the "15-minute principle" - reserve fifteen minutes daily for improvements. This makes CIP a habit.
Conclusion: CIP as Key to Business Success
The Continuous Improvement Process is more than just a method – it's the path to sustainable process optimization and competitiveness. Practice shows: Companies successfully living CIP achieve:
- 20-30% higher productivity
- 50% fewer process errors
- Significantly increased employee satisfaction
- Sustainable cost savings
The first step to CIP success? Start today with a small improvement.