Industry 4.0: Definition, benefits & implementation [2025-Guide]
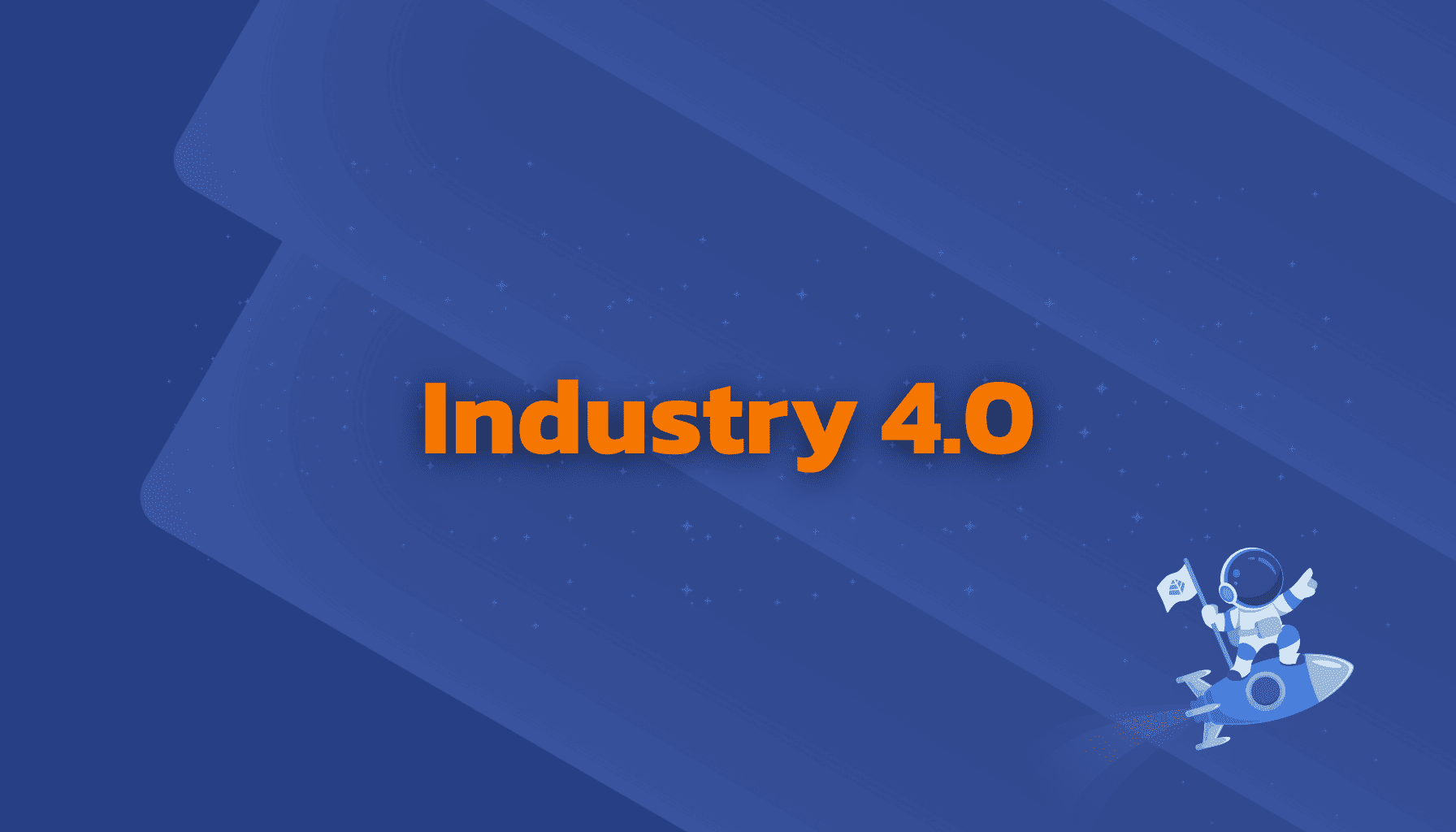
In this comprehensive guide, you'll learn everything important about Industry 4.0 and how digital transformation is revolutionizing the manufacturing landscape. We'll show you:
- How to successfully implement the core elements of Industry 4.0 in your company
- Which technologies form the basis for the Smart Factory of the future
- How to increase your productivity by up to 35% through digital transformation
- Field-tested implementation strategies with concrete examples
- Current trends and developments for 2024 and beyond
After reading this guide, you'll not only understand the theoretical foundations of Industry 4.0 but also know exactly how to implement digital transformation in your company.
What is Industry 4.0?
The fourth industrial revolution heralds a new age of production. While previous industrial revolutions were characterized by steam power, electrification, and early computer technologies, Industry 4.0 represents the complete digital transformation of the manufacturing industry. But what exactly lies behind this concept that's revolutionizing the production world?
Definition & Core Elements
Industry 4.0 describes the intelligent networking of modern production systems. At its center is the vision of a Smart Factory where machines, products, and people communicate seamlessly. Unlike conventional automation, it's not just about individual production steps but about a holistic, self-optimizing system.
The foundation consists of three central core elements:
Cyber-Physical Systems (CPS): These systems connect the physical with the digital world. Sensors continuously collect production data, while intelligent software analyzes this in real-time and automatically adjusts production processes. Example: A manufacturing system independently recognizes material shortages and automatically orders supplies.
Internet of Things (Industrial IoT): The industrial Internet of Things networks all production components together. Machines, workpieces, and logistics systems permanently exchange data and coordinate independently. Thus, a workpiece "knows" from the start of production which processing steps it must go through and communicates this directly with the available machines.
Digital Twin: As a digital replica of real production, the Digital Twin enables simulation and optimization of processes before they are implemented in reality. Changes can be tested in advance and risks minimized.
Key Technologies Overview
The implementation of Industry 4.0 is based on several key technologies that form the foundation of the intelligent factory:
Big Data Analytics & AI: Modern analysis methods process the enormous amounts of data from production and gain valuable insights. Artificial intelligence recognizes patterns and continuously optimizes processes. An example is predictive maintenance, where AI systems predict the optimal time for maintenance work.
Cloud Computing: The cloud forms the backbone of networked production. It provides flexible computing power and storage capacity and enables cross-location data exchange. Companies can thereby optimally adapt their IT resources to actual needs.
5G & Industrial Communication: High-performance communication networks are crucial for Industry 4.0. 5G technology enables real-time transmission of large amounts of data and reliable networking of thousands of devices. This is especially important for time-critical applications like robot control.
Quick Guide: Benefits at a Glance
The implementation of Industry 4.0 brings companies numerous measurable benefits:
Efficiency Increase
- 20-35% productivity increase through optimized processes
- Reduction of downtime by up to 50%
- Energy cost reduction by an average of 15-20%
Quality Improvement
- Error rate decreases by up to 25% through intelligent quality control
- Continuous process optimization through real-time data
- Traceability of all production steps
Flexibility & Innovation
- Faster reaction to market changes
- Individualized production even for small quantities
- Development of new, data-based business models
The transformation to Industry 4.0 is not an option but a necessity for companies wanting to compete globally. Investments in modern technologies pay off through increased efficiency, better quality, and new business opportunities.
The 4 Pillars of the Smart Factory
The transformation to Industry 4.0 is based on four fundamental pillars that together form the foundation of the intelligent factory.
1. Networking & IoT: The Nervous System of Industry 4.0
Comprehensive networking forms the backbone of every Industry 4.0 solution. Through the Industrial Internet of Things (IIoT), machines, products, and systems communicate in real-time. This intelligent networking enables:
- Transparent production processes through complete data collection
- Automatic adaptation of production to changed conditions
- Efficient resource utilization through optimized coordination of all components
2. Data Analysis & AI: The Brain of the Smart Factory
Intelligent data analysis plays a key role in Industry 4.0. Artificial intelligence and machine learning transform collected data into valuable insights:
- Predictive maintenance reduces unplanned downtime by up to 50%
- Quality forecasts demonstrably increase product quality by 20-30%
- Energy management algorithms reduce energy consumption by up to 25%
3. Automation & Robotics: The Muscles of Industry 4.0
The third pillar of the Smart Factory combines classical automation with intelligent control:
- Collaborative robots (Cobots) flexibly support employees in various tasks
- Autonomous mobile robots (AMR) optimize internal logistics
- Adaptive production systems automatically adjust to new product variants
4. Cloud Manufacturing: The Operating System of Industry 4.0
Cloud-based solutions form the fourth pillar of the modern Smart Factory. They enable:
- Flexible scaling of IT resources as needed
- Cross-location networking of all production sites
- Real-time access to production data from anywhere
Implementation in Practice
5-Step Implementation Guide
1. Status Analysis & Digitalization Strategy
- Evaluation of digital maturity
- Definition of concrete goals
- Use of standardized analysis tools
2. Building Digital Infrastructure
- Flexible cloud architectures
- Standardized interfaces
- Immediate utilization without long implementation times
3. Pilot Project and First Successes
- Start with individual production lines
- Quick wins through pre-configured solutions
- Continuous optimization based on real-time data
4. Scaling and Integration
- Flexible scaling as needed
- Simple connection of additional production sites
- Seamless integration with existing systems
5. Continuous Improvement
- Continuous performance monitoring
- AI-supported process optimization
- Regular updates and new functions
Typical Challenges & Solutions
Challenge: High Investment Costs
-
Solution: Cloud-based pay-per-use models eliminate high initial investments
Challenge: Complex IT Integration
-
Solution: Modern MES solutions offer standardized interfaces and pre-configured integrations
Challenge: Employee Acceptance
-
Solution: Intuitive user interfaces and comprehensive training concepts
Costs & ROI Calculation
Typical savings:
- 15-25% reduction in production costs
- Up to 20% reduction in quality costs
- 30-40% reduction in IT costs through cloud usage
Standards & Future Trends in Industry 4.0
Important Standards
RAMI 4.0 (Reference Architecture Model Industry 4.0)
- Hierarchical levels of production
- IT security requirements
- Communication standards
- Data exchange formats
Technology Trends 2024
-
Edge Computing in Production
- Decentralized data processing directly at the machine
- Reduced latency for critical processes
- Optimized bandwidth utilization
-
AI-Supported Autonomy
-
Self-optimizing production systems
-
Predictive quality assurance
-
Autonomous logistics solutions
-
-
Digital Twin Evolution
-
Complete mapping of the production environment
-
Real-time optimization through simulation
-
Improved planning security
-
-
Sustainable Smart Factories
-
Energy-efficient production processes
-
CO2 footprint monitoring
-
Resource optimization through AI
-
Conclusion: Industry 4.0 as Key to Success
The digital transformation of industry is unstoppable. Companies face the challenge of actively shaping this change. The good news: Getting started with Industry 4.0 doesn't have to be complex or costly.
Modern cloud-based MES solutions enable:
- No high initial investments through pay-per-use models
- Quick implementation within weeks
- Measurable ROI within a few months
- Future-proof technology through continuous updates
Companies investing in Industry 4.0 technologies now gain decisive competitive advantages:
- Increased production efficiency
- Improved product quality
- Greater flexibility
- Reduced costs
The path to the Smart Factory begins with the first step. With the right partner and a clear strategy, any company can take advantage of digital transformation opportunities. The time to act is now.