Advanced Process Control (APC)
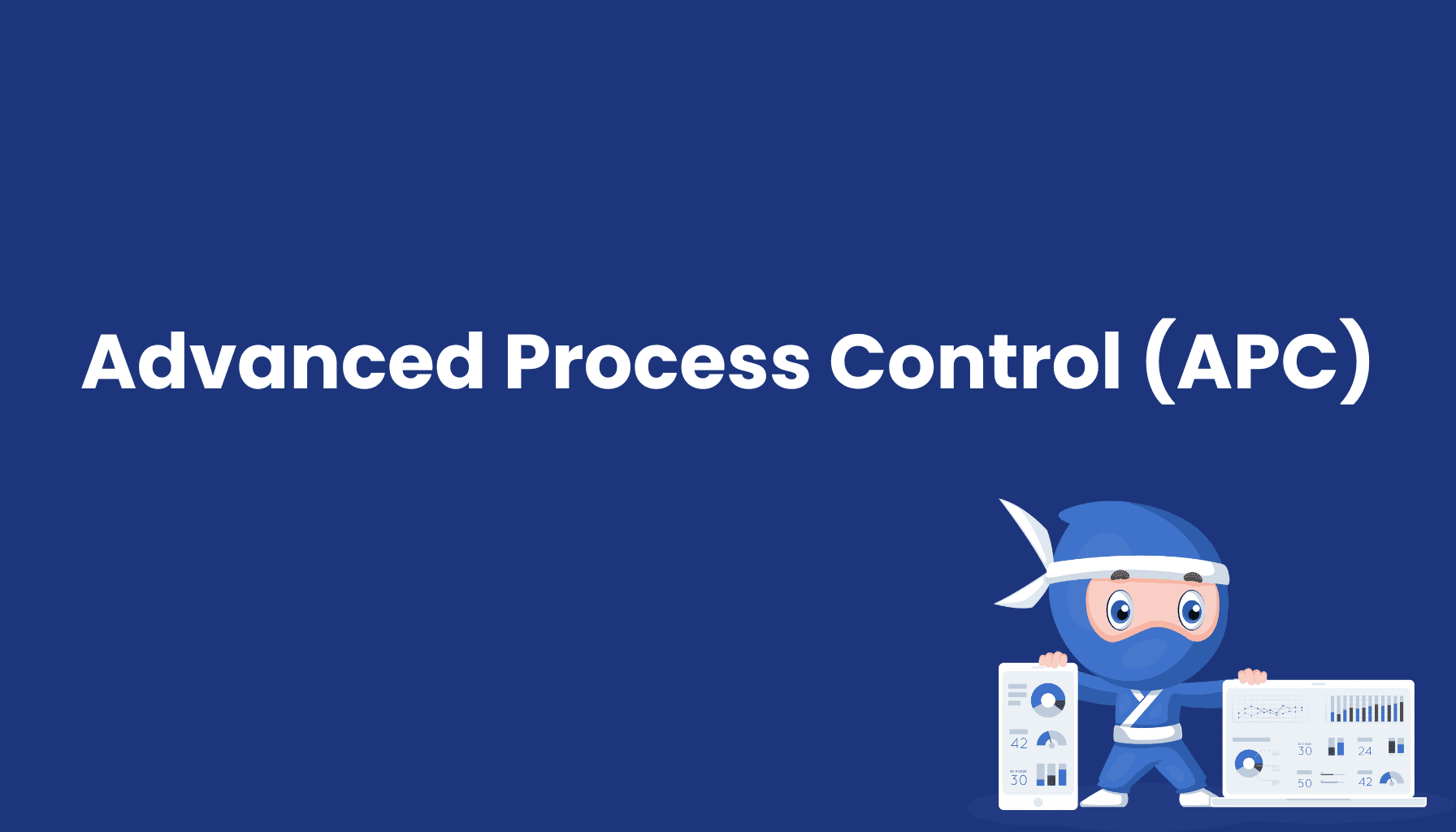
What is APC (Advanced Process Control)?
APC, or Advanced Process Control, refers to sophisticated control systems used in manufacturing to optimize production processes and increase efficiency. These systems leverage algorithms, mathematical models, and real-time data analysis tools to continuously monitor and adjust process parameters, improving both product quality and yield.
How Does APC Work?
APC systems measure and analyze various process variables such as temperature, pressure, and flow rates. Based on this data, the system automatically adjusts controls to maintain optimal conditions. Advanced models and predictive algorithms are used to stabilize production and ensure consistent quality throughout the manufacturing process.
Benefits of APC in Manufacturing
- Increased Efficiency: APC systems stabilize production processes, identify bottlenecks, and improve Overall Equipment Effectiveness (OEE).
- Improved Quality: By precisely controlling processes, APC minimizes fluctuations and maximizes product quality.
- Cost Savings: Reduced material waste and optimized resource usage result in significant cost reductions.
APC and OEE
Implementing APC directly impacts Overall Equipment Effectiveness (OEE) by enhancing availability, performance, and quality. APC helps optimize processes, maximize utilization, and reduce quality losses, all of which contribute to a higher OEE.
The Role of APC in Modern Manufacturing
APC systems are vital in today’s manufacturing environments, particularly in complex production settings where precise control and ongoing optimization are crucial. They help companies meet production goals, reduce costs, and improve product quality, all while enhancing operational efficiency.