Bottleneck
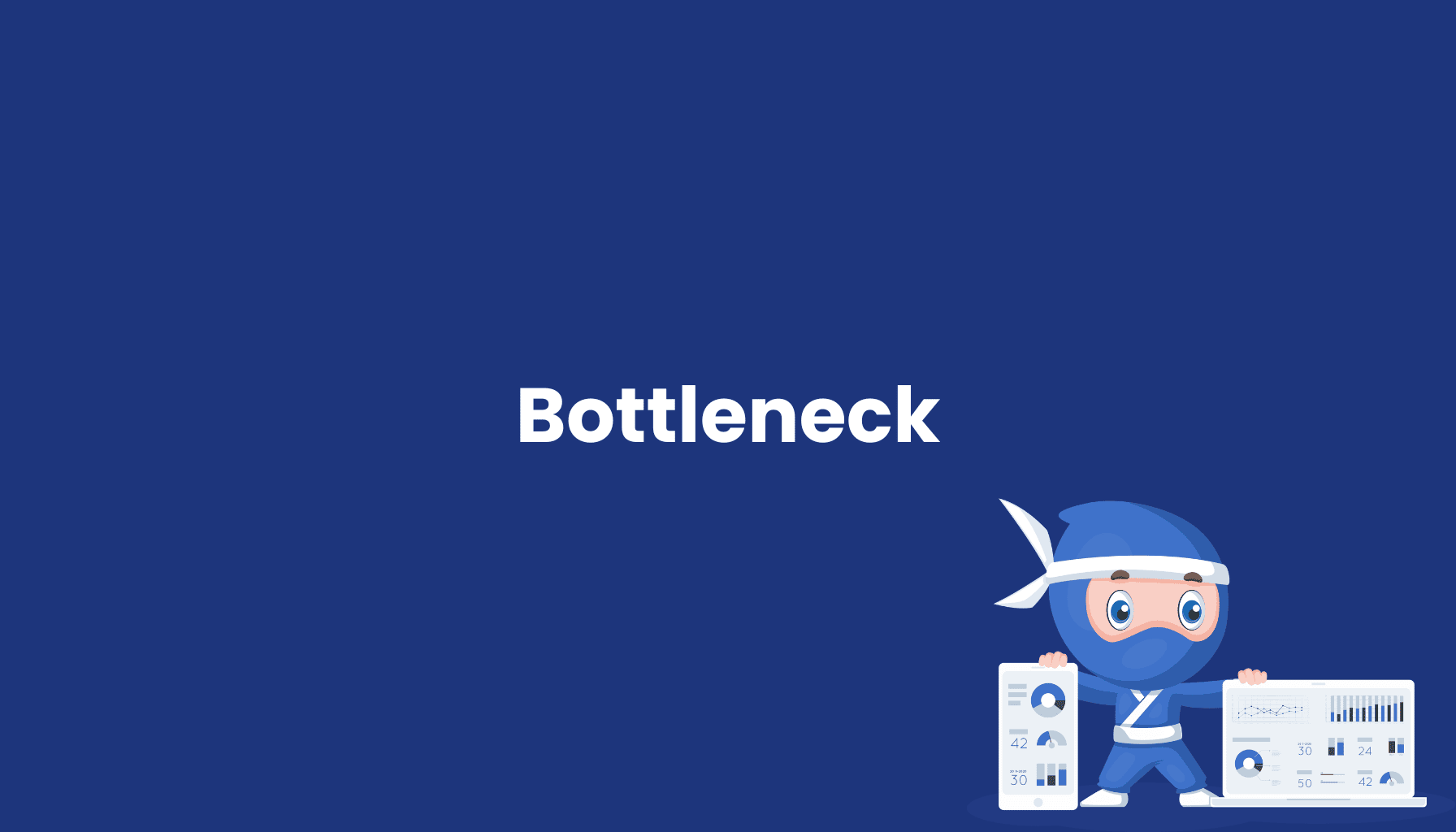
What is a Bottleneck?
In the context of business and production, a bottleneck refers to a resource, process, or situation where a lack of capacity or resources slows down or obstructs the overall process flow. Bottlenecks often occur in areas where demand exceeds supply or when a specific resource or workstation becomes overloaded. The term "bottleneck" is frequently used interchangeably with "constraint" to describe this critical limitation.
Significance and Causes of Bottlenecks
Bottlenecks are pivotal points in production and service processes that can significantly impede workflows, reducing a company's efficiency and productivity. Understanding the causes of bottlenecks is essential, as they can manifest in various aspects of a system. Common causes include:
- Capacity Shortages: When demand surpasses capacity, bottlenecks often emerge, particularly in crucial processes.
- Resource Scarcity: Insufficient availability of machines, manpower, or materials can slow down production, creating bottlenecks.
- Inefficient Processes: Outdated systems or poorly optimized workflows often lead to delays that hinder the overall process.
- Planning Errors: Inaccurate planning or poor coordination can result in unexpected bottlenecks, such as insufficient inventory or missed deadlines.
Types of Bottlenecks
Bottlenecks can be categorized based on where they occur and their specific impacts on processes. Key types include:
- Resource Bottlenecks: Arising from a lack of resources like labor, raw materials, or equipment.
- Capacity Bottlenecks: Occurring when production or machinery capacity is insufficient to meet demand.
- Process Bottlenecks: Resulting from inefficient workflows or poorly sequenced tasks.
Impact of Bottlenecks
Bottlenecks can have wide-ranging consequences for businesses, including:
- Production Delays: A bottleneck slows down the production process, jeopardizing delivery schedules.
- Increased Costs: Addressing bottlenecks often involves overtime labor, expedited shipping, or outsourcing, all of which increase operational costs.
- Customer Dissatisfaction: Delays caused by bottlenecks can lead to missed deadlines, disappointing customers, and potentially losing business.
- Underutilized Resources: When bottlenecks occur, other resources may sit idle or become underused, reducing overall productivity.
Strategies to Manage Bottlenecks
To identify and mitigate bottlenecks, companies use various approaches and tools. Proven strategies for reducing bottlenecks include:
- Analysis and Prioritization: Conducting detailed analyses of workflows to identify and prioritize critical bottlenecks.
- Resource Planning and Optimization: Better allocation of resources, including investment in additional capacity, can help address bottlenecks efficiently.
- Implementation of Lean Methods: Lean methodologies, such as the Theory of Constraints (TOC), focus on identifying and optimizing bottlenecks to ensure smoother operations.
- Continuous Process Improvement: Regularly reviewing and improving processes ensures long-term efficiency and flexibility, preventing bottlenecks from recurring.
Example of a Bottleneck in Production
In automotive manufacturing, a painting station often becomes a bottleneck. When this station is overloaded, it delays the entire production line, as subsequent processes must wait for painted car bodies to proceed. By analyzing station capacity and optimizing the painting process, manufacturers can alleviate the bottleneck, improving overall production flow.
Why Addressing Bottlenecks is Critical
Resolving bottlenecks is crucial for businesses aiming to enhance efficiency, reduce costs, and meet customer demands. By leveraging tools like real-time data, advanced planning systems, and continuous monitoring, companies can tackle bottlenecks proactively, maintaining a competitive edge in their industries.
This SEO-optimized article on bottlenecks is designed to rank highly on Google by addressing search intent, providing in-depth information, and offering actionable solutions to readers.