Continuous Improvement Process (CIP)
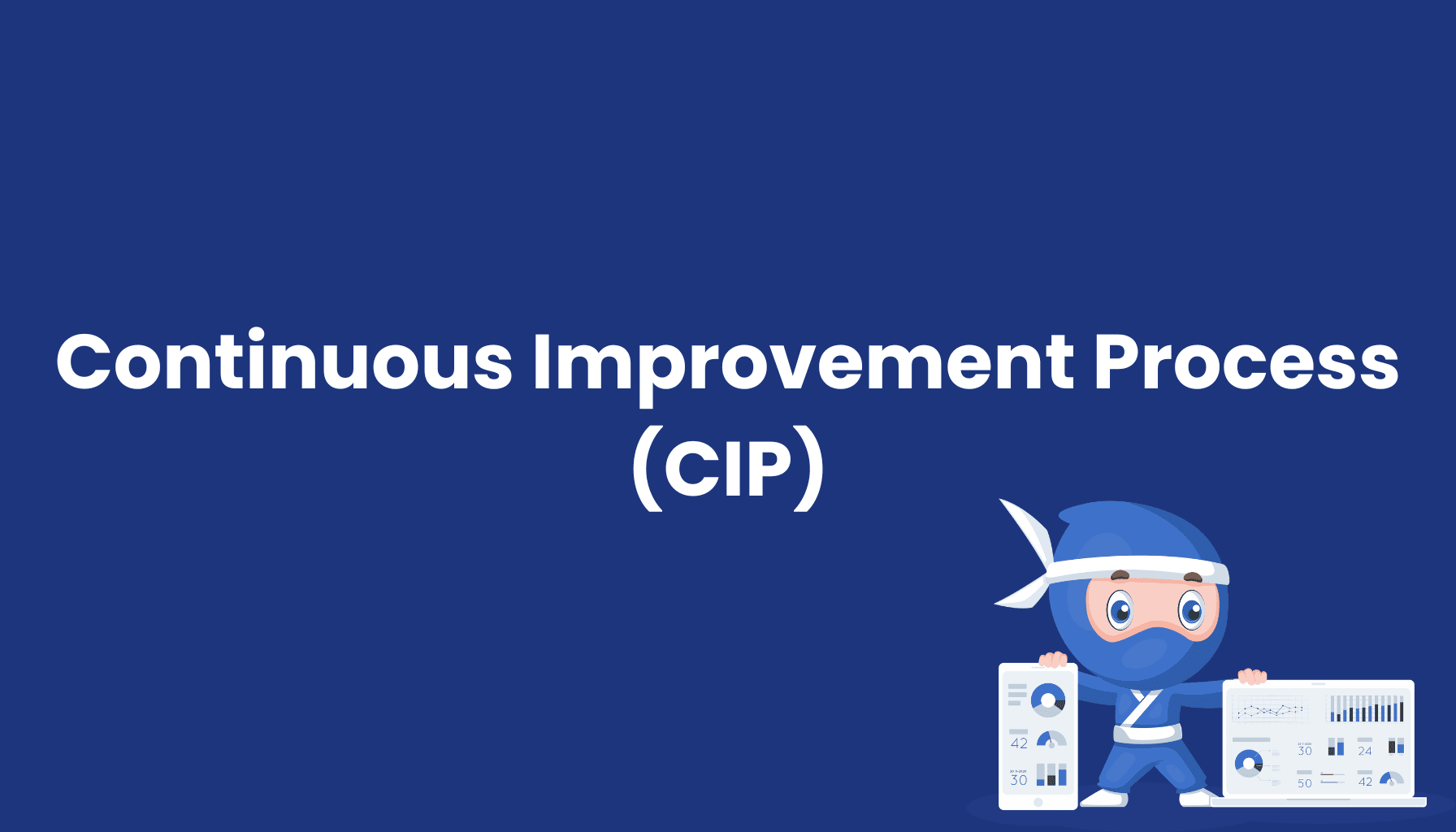
What is Continuous Improvement Process (CIP)?
The Continuous Improvement Process (CIP) is an approach focused on the ongoing optimization of products, services, and processes. By making regular, incremental changes, CIP aims to boost efficiency, quality, and flexibility within organizations. Central to Lean Management, this approach is widely adopted across industries to foster a culture of continuous enhancement.
Core Principles of the Continuous Improvement Process (CIP)
-
Employee Involvement: Every employee is engaged in the improvement process, actively identifying and implementing optimizations. This participation fosters a sense of ownership and commitment to achieving improvements.
-
Customer Focus: The primary goal is to enhance customer satisfaction. CIP is centered on meeting or exceeding customer expectations by creating added value through continuous adjustments.
-
Process Orientation: CIP emphasizes analyzing and refining all processes to optimize workflows, increase efficiency, and reduce error rates.
-
Long-term Perspective: CIP is an ongoing process that represents a lasting commitment to improvement rather than a one-off project.
Goals of CIP
-
Increase Productivity and Quality: CIP optimizes processes to boost quality and streamline operations, enhancing overall productivity.
-
Cost Reduction and Waste Minimization: By identifying and eliminating unnecessary expenses and waste, resources are used more effectively.
-
Employee Motivation and Satisfaction: Involving employees in improvement efforts increases their motivation and leads to a stronger connection to the organization.
-
Maintaining Competitiveness: Continuous improvement helps organizations quickly adapt to market changes and maintain a competitive edge.
Applications of CIP
-
Manufacturing: CIP optimizes production processes, reduces waste, and increases production capacity.
-
Service Sector: It enhances service quality and increases efficiency in service delivery.
-
Healthcare: CIP streamlines operations to improve patient care and reduce waiting times.
-
Logistics: The process optimizes supply chains, reducing lead times and inventory levels.
Challenges and Solutions
-
Resistance to Change: Employees may be hesitant to embrace changes. This can be overcome through transparent communication and active participation at all levels.
-
Long-term Commitment: CIP requires consistent execution and strong leadership. Ongoing training and clear leadership can sustain CIP for lasting impact.
CIP in Germany
In Germany, CIP is critical across sectors, especially in manufacturing and service industries. Companies increasingly rely on CIP to continuously refine their operations and remain competitive, especially in light of digital transformation. CIP provides a solution for steady process enhancement and improved efficiency.