Distributed Control System (DCS)
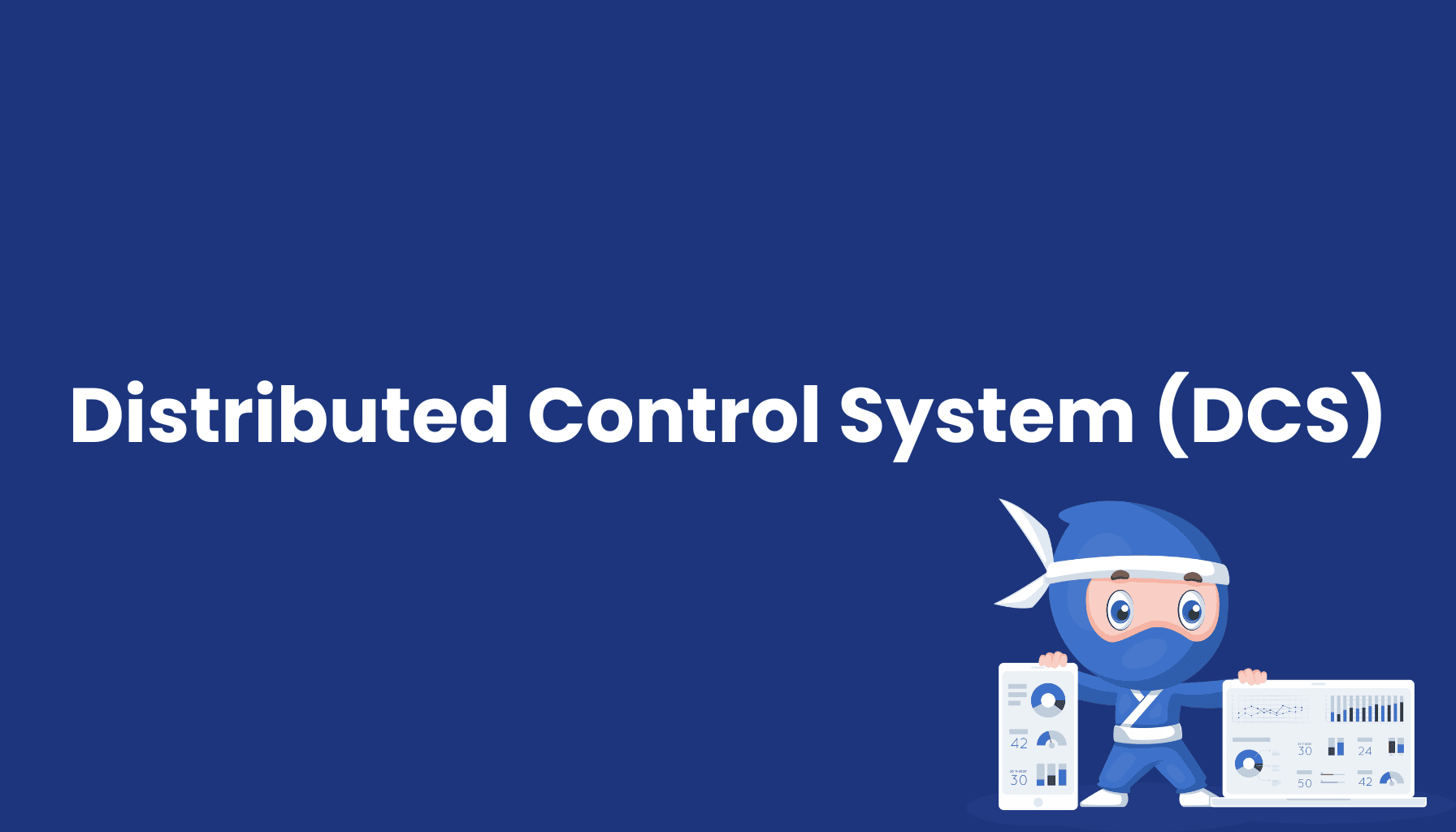
What Is a Distributed Control System (DCS)?
A Distributed Control System (DCS) is an automated system used to decentralize the control and monitoring of production processes in the manufacturing industry. A DCS consists of multiple interconnected controllers distributed across various sections of a plant, working together to manage the entire production process. These systems are particularly common in large, complex production environments such as chemical plants, power stations, and refineries, where they help improve efficiency, reliability, and safety.
Key Functions of a Distributed Control System
-
Decentralized Control: Unlike centralized control systems, a DCS distributes control tasks across multiple controllers installed near the processes they manage. This reduces the need for long cable runs and minimizes downtime by allowing localized control and monitoring.
-
Real-Time Monitoring and Control: A DCS provides real-time data on the status of production equipment, enabling operators to quickly respond to deviations or issues. This is crucial in manufacturing, where rapid decision-making is needed to prevent production disruptions.
-
Scalability and Flexibility: A DCS is modular, meaning new controllers and sensors can be easily added to meet changing requirements. This flexibility makes DCS an ideal solution for growing and evolving production environments.
-
Integrated Safety Features: Modern DCS systems incorporate advanced safety features such as emergency shutdowns that can be automatically triggered to prevent equipment damage and ensure personnel safety.
Benefits of a DCS in Manufacturing
-
Increased Reliability: By distributing control tasks across multiple controllers, a DCS can compensate for the failure of individual components without significantly impacting the overall process.
-
Improved Process Control: With a DCS, companies can precisely control their production processes, leading to consistent product quality and higher yields.
-
Efficient Resource Utilization: A DCS helps optimize energy consumption and material usage, leading to cost savings and sustainable production.
-
Rapid Issue Resolution: Since a DCS provides real-time data, problems can be quickly identified and resolved before they escalate into serious disruptions.
Applications of a DCS in Manufacturing
-
Chemical Industry: DCS systems are commonly used in chemical production to safely and efficiently manage complex and often hazardous processes.
-
Power Plants: In energy generation, DCS systems enable precise control and monitoring of power plant operations, increasing efficiency and reducing the risk of failures.
-
Automotive Industry: DCS is used in automotive manufacturing to coordinate the various production lines and ensure smooth operation of all processes.
-
Pharmaceutical Production: In the pharmaceutical industry, a DCS helps maintain strict production standards and ensure the quality of final products.
Conclusion: DCS as a Key to Process Optimization in Manufacturing
A Distributed Control System (DCS) is indispensable in the manufacturing industry, decentralizing the control and monitoring of production processes and thereby enhancing reliability and efficiency. By integrating a DCS, companies can optimize their production operations, reduce costs, and ensure the safety and quality of their products.