Digital Manufacturing
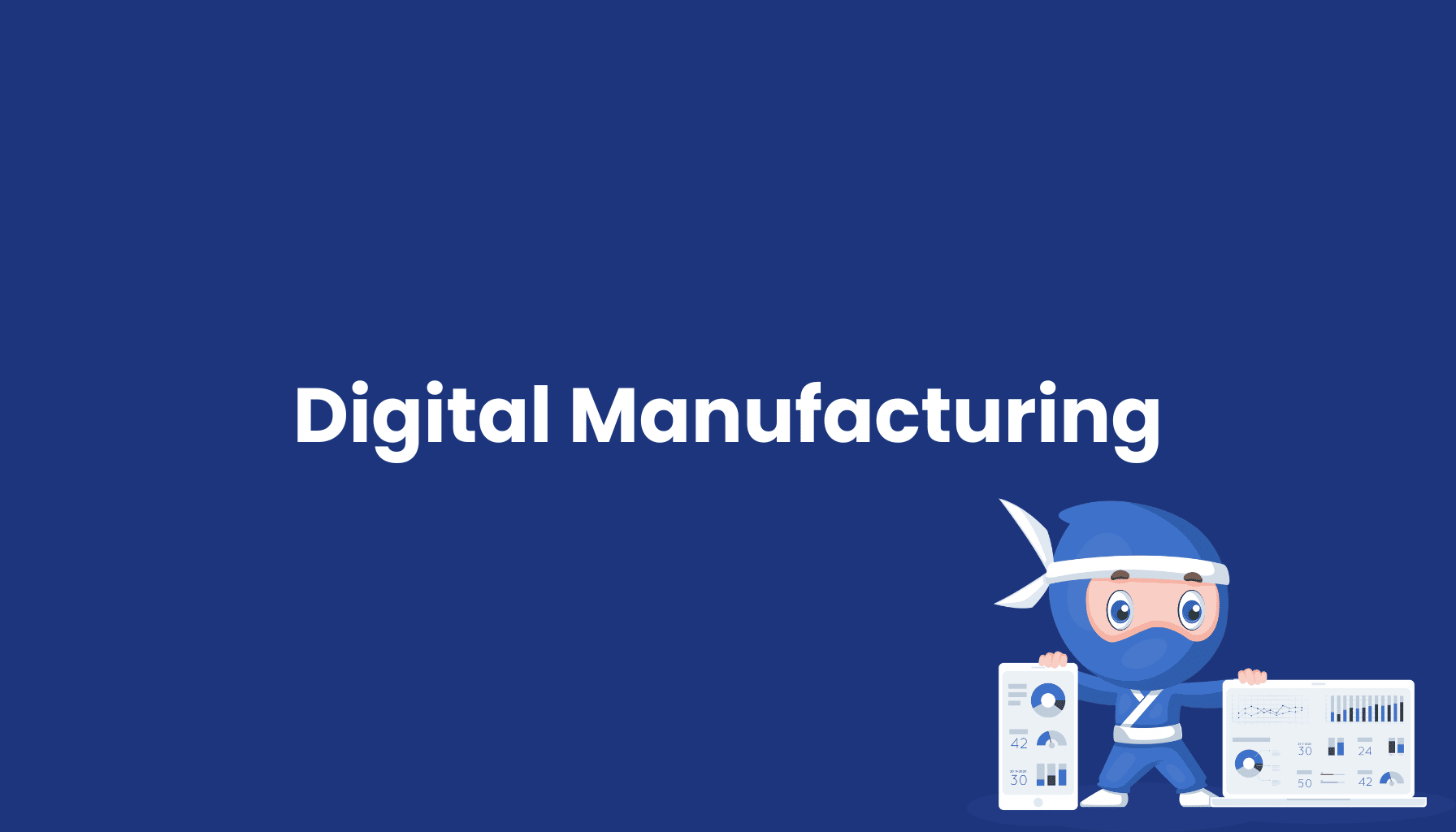
Digital manufacturing represents the forward-looking evolution of industrial production processes. A methodical implementation of digital technologies enables sustainable optimization of manufacturing efficiency through intelligent networking and data-driven process control.
System Architecture
The fundamental structure of digital manufacturing based on:
- Industrial Internet of Things (IIoT) integration enabling comprehensive connectivity
- Cloud-based production control facilitating scalable processing
- Edge computing delivering real-time data processing capabilities
- Digital Twin technology creating virtual process representations
- Cyber-Physical Systems (CPS) bridging physical and digital domains
Process Integration
Systematic networking of manufacturing components through:
- Manufacturing Execution Systems (MES) coordinating production activities
- Enterprise Resource Planning (ERP) managing business resources
- Product Lifecycle Management (PLM) overseeing product development
- Advanced Planning and Scheduling (APS) optimizing production schedules
- Quality Management Systems (QMS) ensuring product consistency
Data Management
Implementation of structured data processing:
- Big Data Analytics platforms processing large-scale information
- Real-time process monitoring enabling immediate response
- Predictive Analytics systems forecasting operational trends
- Machine Learning algorithms optimizing process parameters
- AI-supported decision making enhancing operational control
Automation Technology
Integration of modern automation solutions:
- Collaborative robot systems enhancing human-machine interaction
- Autonomous Guided Vehicles (AGV) optimizing material flow
- Smart sensor networks providing comprehensive monitoring
- Adaptive control systems ensuring process stability
- Flexible manufacturing cells enabling production agility
Performance Monitoring
Continuous performance surveillance through:
- Real-time KPI tracking measuring operational efficiency
- Predictive maintenance preventing equipment failures
- Quality analytics ensuring product consistency
- Capacity utilization monitoring optimizing resource usage
- Energy efficiency analysis reducing operational costs