Digital Shopfloor Management
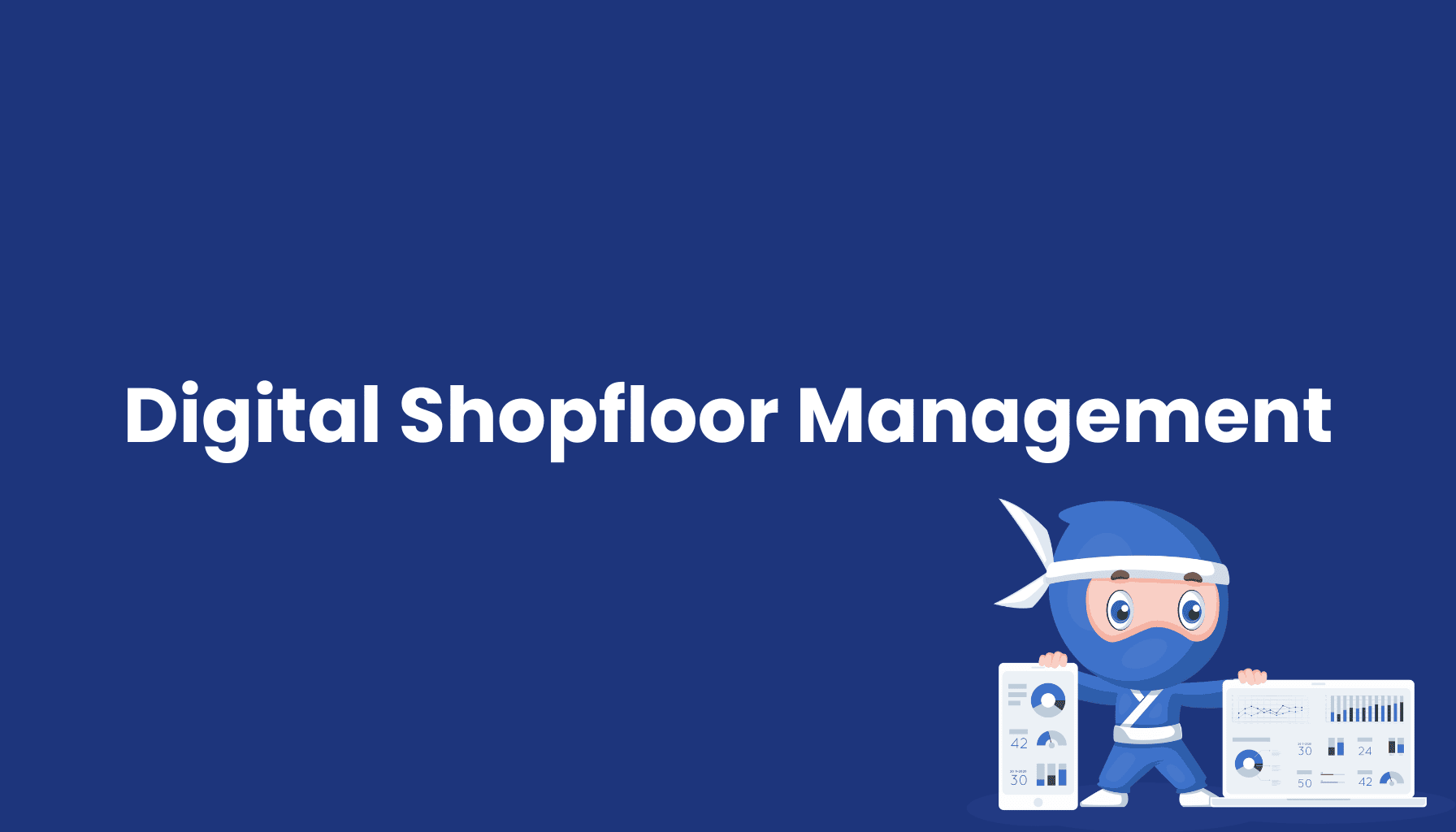
Digital transformation of shopfloor management revolutionizes the operational control of manufacturing processes. The integration of modern technologies creates a transparent and efficient production environment that significantly enhances both process quality and workforce productivity through systematic data utilization and real-time control capabilities.
Core Digital Components
Essential elements enabling operational excellence:
- Digital board management providing transparent communication platforms
- Mobile device integration enabling flexible data access
- Real-time performance monitoring systems tracking operations
- Digital shift handover ensuring information continuity
- Interactive visualization systems displaying operational status
- Automated data collection ensuring accurate documentation
- Digital workflow management coordinating activities
Process Integration
Systematic networking through comprehensive platforms:
- Seamless Manufacturing Execution System (MES) integration
- Shop floor data collection capturing operational metrics
- Digital work instructions providing clear guidance
- Quality data acquisition ensuring standards compliance
- Disruption management systems minimizing impacts
- Performance tracking enabling immediate response
- Resource allocation optimization maximizing efficiency
Performance Optimization
Continuous improvement through digital capabilities:
- KPI-based performance tracking measuring success
- Digital problem-solving processes enabling quick resolution
- Automated report generation providing insights
- Trend and pattern analysis identifying opportunities
- Preventive measure planning reducing issues
- Efficiency monitoring driving improvements
- Quality assurance maintaining standards
Implementation Framework
Strategic deployment methodology:
- Infrastructure assessment evaluating digital readiness
- System architecture design ensuring scalability
- Integration planning coordinating implementations
- Training program development ensuring adoption
- Performance baseline establishment
- Continuous improvement processes
Operational Benefits
Digital shopfloor advantages:
- Enhanced operational transparency through real-time data
- Improved decision-making through immediate information access
- Reduced response times to production issues
- Increased workforce productivity through better coordination
- Enhanced quality control through systematic monitoring
- Optimized resource utilization through data-driven allocation
- Streamlined communication across all levels
Performance Monitoring
Continuous surveillance through:
- Real-time KPI tracking
- Process visualization
- Quality monitoring
- Efficiency analysis
- Resource utilization assessment
- Productivity measurement
- Communication effectiveness
This comprehensive framework enables manufacturers to implement effective digital shopfloor management systems that drive operational excellence through enhanced visibility, improved coordination, and data-driven decision making.