Machine Downtime
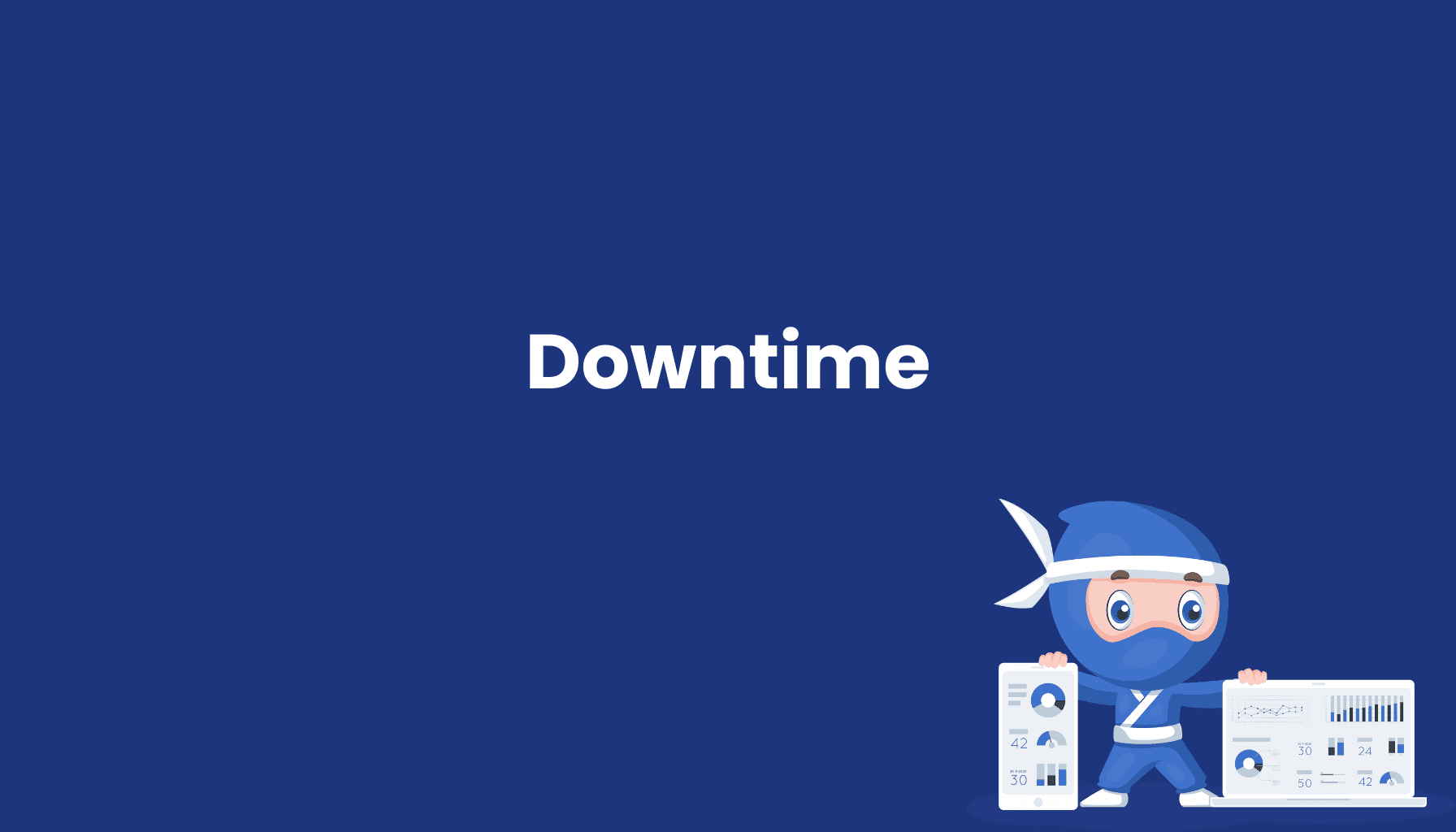
What is Machine Downtime?
Machine downtime refers to periods when manufacturing equipment is not operational due to failures, maintenance, or other unforeseen events. These interruptions can significantly impact a company's productivity and efficiency. Therefore, managing machine downtime is a critical aspect of the manufacturing industry.
Causes of Machine Downtime
- Technical Failures: Defective machine components, control system failures, or software issues.
- Planned Maintenance: Regular inspections and preventive maintenance to avoid major breakdowns.
- Material Shortages: Delays in the supply chain can lead to downtime when necessary materials are not available on time.
- Employee Absences: Sick leave or strikes can also cause machine downtime.
- External Factors: Power outages, natural disasters, or other external influences that disrupt operations.
Impact of Machine Downtime
- Productivity Loss: Downtime directly results in a decrease in production output, negatively affecting overall operational efficiency.
- Increased Costs: Additional costs arise from repairs, replacement parts, and potential loss of production orders.
- Quality Issues: Irregular production processes can lead to quality defects and increased rework.
- Customer Satisfaction: Delays in product delivery can negatively impact customer trust and satisfaction.
Relationship Between Machine Downtime and OEE
Overall Equipment Effectiveness (OEE) is a metric that evaluates the overall efficiency of a production facility. It consists of three main factors: availability, performance, and quality. Machine downtime directly affects availability, as any interruption reduces the actual available production time. By minimizing machine downtime, OEE can be significantly improved, leading to higher production output and product quality.
Strategies to Minimize Machine Downtime
- Preventive Maintenance: Regular and proactive maintenance activities to prevent unexpected failures.
- Condition Monitoring: Using monitoring technologies to detect anomalies and early warning signs.
- Employee Training: Regular training and development for staff to ensure quick and effective problem resolution.
- Supply Chain Optimization: Ensuring a stable and reliable supply of materials and spare parts.
- Utilizing Modern Technologies: Integrating IoT and AI for real-time monitoring and analysis of machine conditions.
Example of Successful Downtime Reduction
A leading automotive company implemented a comprehensive condition monitoring system that collected and analyzed real-time data from machines. By detecting wear and potential failures early, the company reduced unplanned downtime by 30% and improved OEE by 15%.
Conclusion
Machine downtime presents a significant challenge for the manufacturing industry, as it can drastically reduce productivity and efficiency. Through targeted measures and the use of modern technologies, companies can minimize the frequency and duration of downtimes, increase the availability of their equipment, and thereby improve overall equipment effectiveness (OEE).
Read our article on Optimizing Overall Equipment Effectiveness (OEE) to learn more about reducing machine downtime and enhancing the efficiency of your production processes.