Failure Mode and Effects Analysis (FMEA)
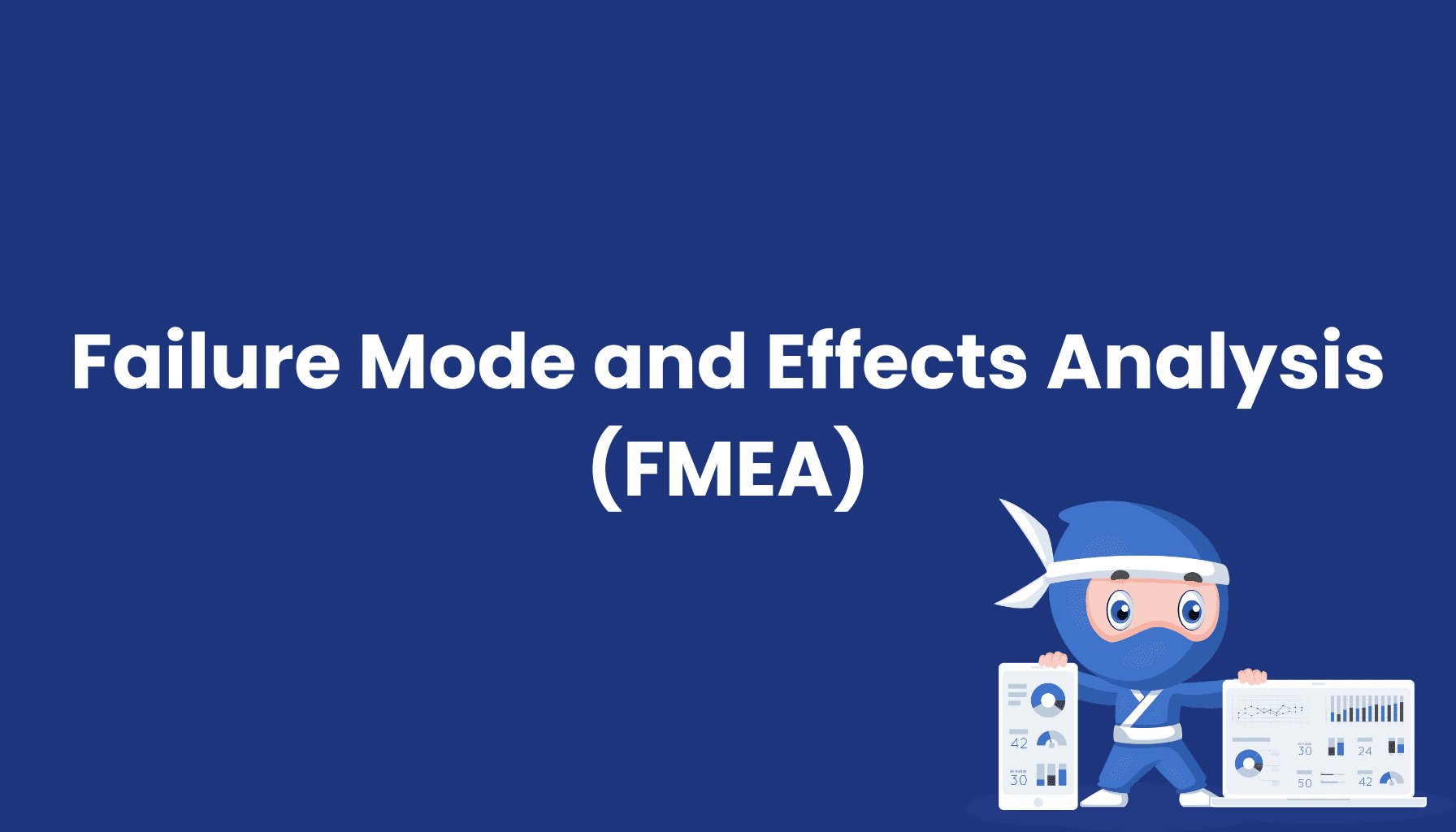
What is FMEA?
Failure Modes and Effects Analysis (FMEA) is a systematic methodology used to identify and assess potential failures in products or processes and determine the impacts of those failures. The primary goal of FMEA is to detect potential problems early and implement corrective measures before the issues actually occur.
Benefits of FMEA
- Early Detection of Failures: FMEA proactively analyzes processes and products, allowing failures to be identified before they escalate into costly problems.
- Risk Reduction: The method helps companies minimize the impacts of failures on quality, safety, and reliability.
- Cost Savings: By preventing failures and their consequences, businesses can reduce costs associated with rework, recalls, and warranty claims.
Key Steps in FMEA
- Identify Potential Failures: Analyze the possible failure modes in a product or process.
- Evaluate the Impact of Failures: Determine the severity, occurrence, and detectability of each failure.
- Risk Prioritization: Calculate the Risk Priority Number (RPN) to identify the most critical issues.
- Implement Corrective Actions: Develop and execute measures to prevent or mitigate the identified failures.
FMEA in Practice
FMEA is widely used across industries such as automotive, aerospace, medical devices, and manufacturing. The methodology enables companies to enhance the quality and reliability of their products and processes by systematically identifying and addressing potential failure points.
FMEA's Role in Quality Assurance
FMEA is a key component of quality assurance, helping organizations optimize their production processes and increase customer satisfaction. By applying FMEA, companies can ensure their products meet the highest quality standards while minimizing risks.