Improvement Potential in Manufacturing
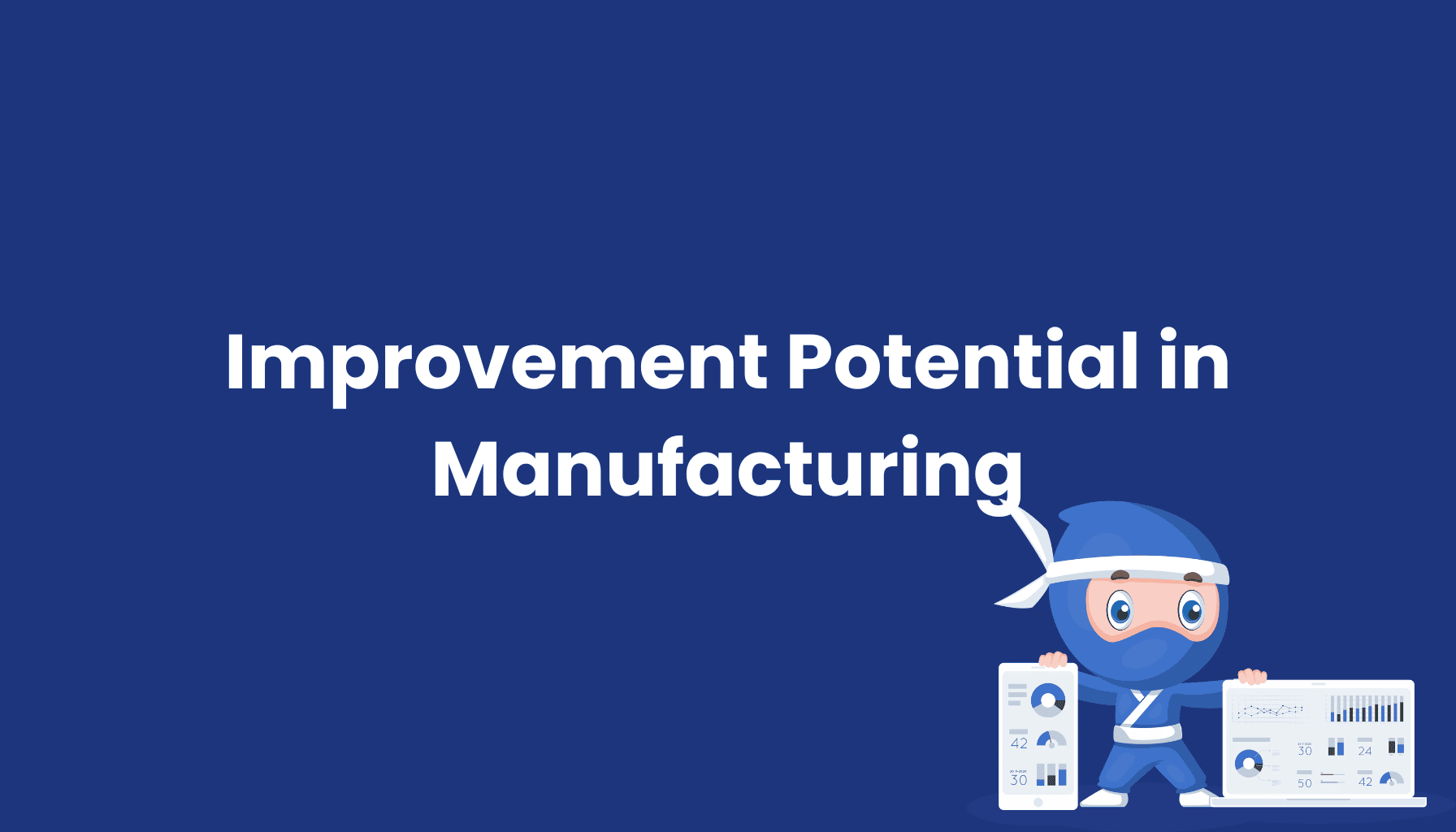
What Is Improvement Potential in Manufacturing?
The structured analysis of improvement potential forms the foundation for continuous process optimization in manufacturing environments. A systematic evaluation approach enables precise identification and effective implementation of optimization measures.
Performance Assessment Framework
A methodological performance assessment integrates multiple analytical dimensions:
- Quantitative performance metrics: Capturing the current state of operations.
- Benchmark analysis: Defining target parameters by comparing with industry standards.
- Gap analysis: Identifying areas for improvement by evaluating performance gaps.
- Impact assessment: Prioritizing focus areas based on their potential impact.
Process Optimization
Systematic process analysis focuses on critical parameters:
- Cycle time analysis: Quantifying process speed to identify bottlenecks.
- Quality performance evaluation: Measuring process stability and defect rates.
- Resource utilization assessment: Analyzing capacity and workforce usage.
- Waste identification: Systematically pinpointing sources of inefficiency.
Technological Optimization
Evaluation of technological improvement potential includes:
- Technology assessment matrix: Analyzing modernization options and feasibility.
- Automation potential analysis: Identifying opportunities for automation to enhance productivity.
- Digital transformation roadmap: Structuring digitization initiatives to leverage smart technologies.
- System integration framework: Optimizing the interoperability of technologies and processes.
Quality Improvement
Systematic quality optimization incorporates:
- Root cause analysis: Identifying and addressing underlying quality deficiencies.
- Prevention-based quality systems: Implementing measures to prevent defects.
- Process capability studies: Evaluating the potential for quality enhancements.
- Quality cost analysis: Quantifying the financial benefits of quality improvements.
Resource Efficiency
Optimizing resource utilization focuses on:
- Energy efficiency assessment: Analyzing and reducing energy consumption.
- Material utilization studies: Enhancing material efficiency and reducing waste.
- Labor productivity analysis: Optimizing workforce productivity through strategic measures.
- Equipment effectiveness monitoring: Maximizing equipment utilization and uptime.
Implementation Framework
A structured implementation methodology includes:
- Project prioritization matrix: Ranking initiatives by impact and feasibility.
- Resource allocation framework: Ensuring optimal distribution of resources.
- Timeline development methodology: Creating actionable and realistic implementation plans.
- Performance monitoring system: Tracking progress and outcomes with key performance indicators.
Continuous Improvement Culture
A systematic improvement culture emphasizes:
- Employee engagement programs: Involving staff in process improvement initiatives.
- Suggestion system implementation: Encouraging ideas and innovations from employees.
- Knowledge management framework: Centralizing and sharing critical operational insights.
- Best practice sharing platforms: Promoting proven methods across teams and departments.