Inventory Management
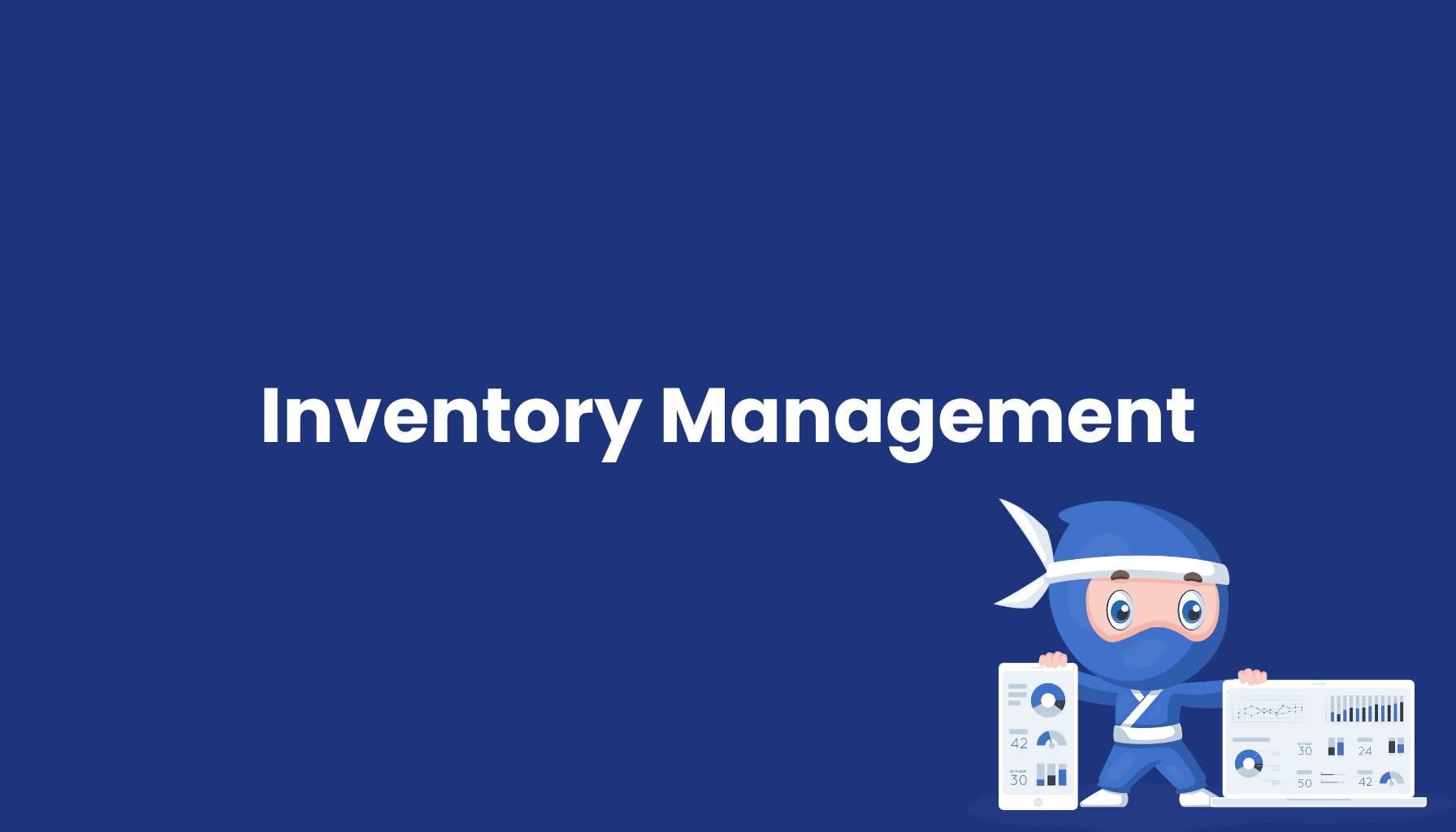
What Is Inventory Management?
Inventory Management refers to the systematic planning, control, and monitoring of stock levels in businesses. It serves as the foundation for optimized material flows and efficient supply chains in production.
Core Functions of Modern Inventory Management
Real-Time Warehouse Management
- Continuous stock monitoring
- Transparent inventory visibility
- Automated reordering processes
- Optimized storage management
- Efficient distribution of goods
Inventory Control and Information
- Up-to-date stock levels at a glance
- Centralized inventory information dashboard
- Automated alerts for supply shortages
- Real-time order tracking
- Analysis of demand fluctuations
Supply Chain Integration
- Connection to supply chains
- Integration with production processes
- Coordination with service levels
- Shipment scheduling
- Logistics optimization
Importance for Production
Operational Benefits
- Reduced storage costs
- Avoidance of supply shortages
- Improved inventory planning
- Increased customer satisfaction
- Enhanced operational efficiency
Strategic Advantages
- Better demand forecasting
- Reduced capital tied up in inventory
- Optimized inventory strategies
- Greater production flexibility
- Competitive advantages
Tools and Solutions
Digital Tools
- Inventory management software
- Real-time monitoring systems
- Forecasting tools
- Analytical modules
- Automated ordering systems
Control and Management Mechanisms
- ABC/XYZ analyses
- Just-in-Time (JIT) concepts
- Kanban systems
- FIFO/LIFO inventory methods
- Safety stock management
Challenges and Solutions
Typical Problems
- Fluctuating inventory levels
- Seasonal demand variations
- Complex material flows
- Delayed orders
- Unexpected supply shortages
Modern Solutions
- Dynamic inventory adjustments
- Predictive analytics for demand forecasting
- Automated restocking systems
- Intelligent warehousing strategies
- Demand-oriented inventory control
Implementation and Optimization
Successful Implementation
- Conduct inventory analysis
- Define objectives
- Select appropriate systems
- Adapt processes
- Train employees
Continuous Improvement
- Regular audits and reviews
- KPI monitoring
- Process optimization
- System adjustments
- Performance tracking
Industry-Specific Requirements
Production-Related Sectors
- Just-in-sequence deliveries
- Production supply management
- Material disposition
- Tool management
- Handling semi-finished products
Service-Level Management
- Availability guarantees
- Delivery time optimization
- Emergency reserves
- Spare parts supply
Integration with MES and ERP
- Data exchange for inventory, production, and planning
- Quality and logistics data integration
- Process alignment in:
- Production planning
- Material management
- Quality assurance
- Cost accounting
- Order management
Conclusion: Inventory Management as a Success Factor
Modern inventory management is a key pillar of efficient production processes. By integrating intelligent tools and connecting with MES and ERP systems, companies can optimize stock levels, reduce costs, and improve customer satisfaction. Real-time monitoring and automated control of material flows provide the foundation for a future-proof production environment.