Ishikawa-Diagramm
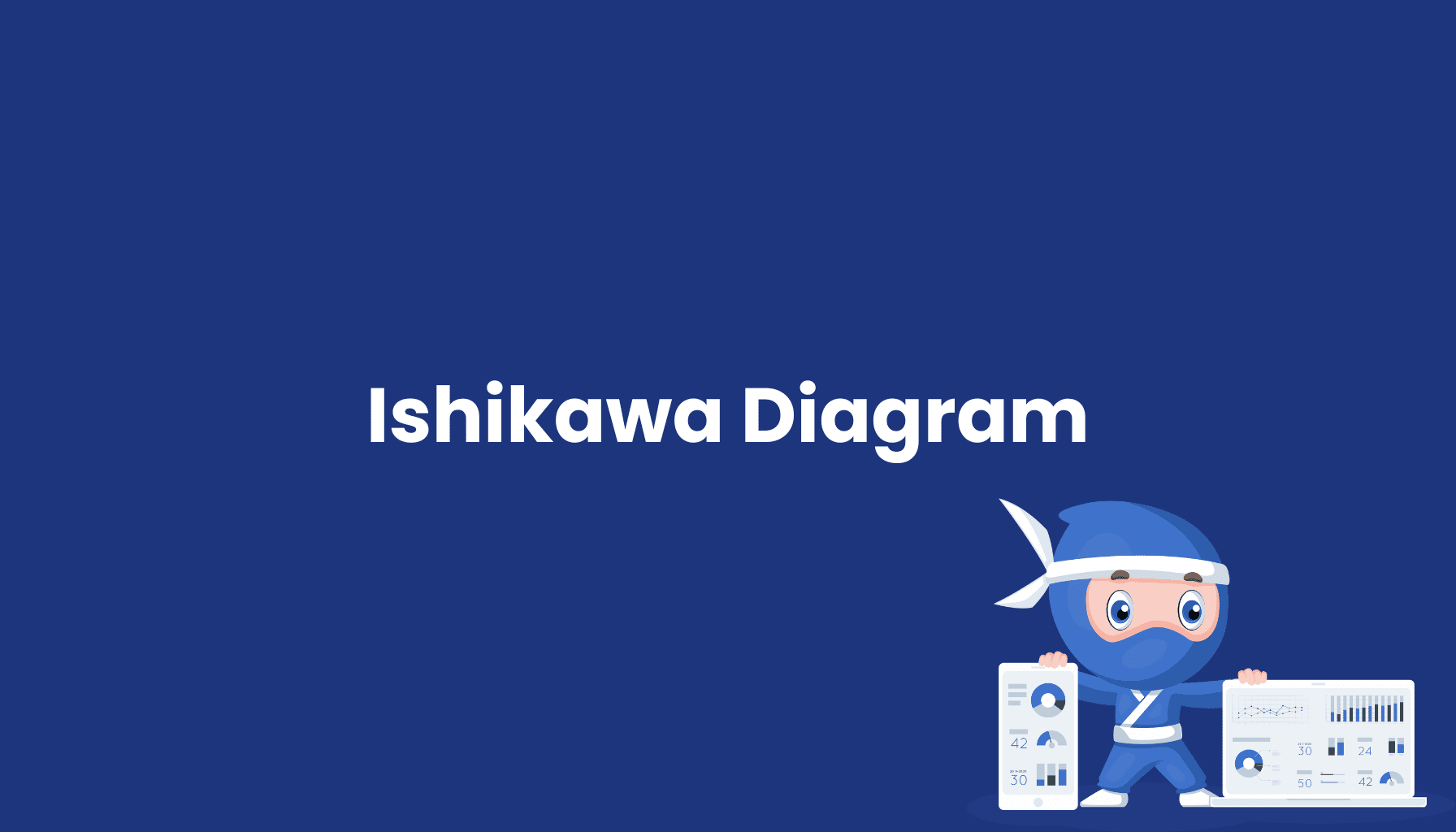
What is the Ishikawa Diagram?
The Ishikawa Diagram, also known as the Fishbone Diagram or Cause-and-Effect Diagram, is a quality management tool used to identify and analyze the root causes of a specific problem. It helps businesses to systematically examine all potential factors contributing to an issue by visually representing them in a structured format that resembles the bones of a fish.
Functionality and Goals of the Ishikawa Diagram
The main goal of the Ishikawa Diagram is to reveal the various causes contributing to a particular problem, making it easier to diagnose and solve. The diagram helps to break down the issue into categories to determine all possible factors contributing to the problem.
Creating the Ishikawa Diagram
The creation of an Ishikawa Diagram involves several steps:
- Defining the problem: Clearly state the issue, which is usually placed at the "head" of the fish.
- Identifying the major categories: Typical categories include factors like People, Methods, Machines, and Materials.
- Listing causes: For each category, specific causes are identified and listed as "bones" branching off the main body of the diagram.
- Analyzing relationships: Understanding how the identified causes contribute to the problem and establishing relationships between them.
Benefits of the Ishikawa Diagram
The Ishikawa Diagram offers several advantages for businesses:
- Clarity: It provides a clear and structured way to visualize complex problems and the multiple causes leading to them.
- Cause Identification: The tool facilitates an in-depth causal analysis, identifying both obvious and less apparent root causes.
- Efficient Problem Solving: By pinpointing the root causes, businesses can take targeted action to eliminate problems and prevent their recurrence.
Applications in Business
In business, the Ishikawa Diagram is commonly used for process improvement and troubleshooting. It plays a key role in Lean Manufacturing and Six Sigma methodologies, where identifying and addressing root causes is crucial to improving efficiency and reducing waste.
Example and Templates for the Ishikawa Diagram
Many businesses utilize predefined templates to create Fishbone Diagrams or build them using specialized software. These templates often include standard categories and offer flexibility to adjust based on industry needs. Industries like manufacturing and healthcare frequently use this diagram to improve product quality and operational processes.
Common Mistakes with the Ishikawa Diagram
Although effective, some common pitfalls should be avoided when using the Ishikawa Diagram:
- Vague Problem Definition: A clear and precise problem statement is crucial; otherwise, it becomes difficult to identify the right causes.
- Overcomplicating the Diagram: Adding too many categories or causes can dilute focus and hinder problem-solving.
- No Prioritization: Failing to prioritize causes can slow down the solution process.
Difference Between Ishikawa and Cause-and-Effect Diagram
The Ishikawa Diagram and Cause-and-Effect Diagram refer to the same tool. The difference is that the former is named after its creator, Kaoru Ishikawa, while the latter describes its function—showing cause-and-effect relationships.
Conclusion and Key Insights
- The Ishikawa Diagram is a valuable tool in quality management and process improvement, providing a systematic approach to identifying and resolving problems.
- Its visual nature makes it easier for teams to collaborate and uncover the root causes of issues, leading to more effective solutions.
- The diagram supports continuous improvement, a core principle of Lean Manufacturing and other process-focused methodologies, leading to better outcomes across industries.