Knowledge Management in Manufacturing
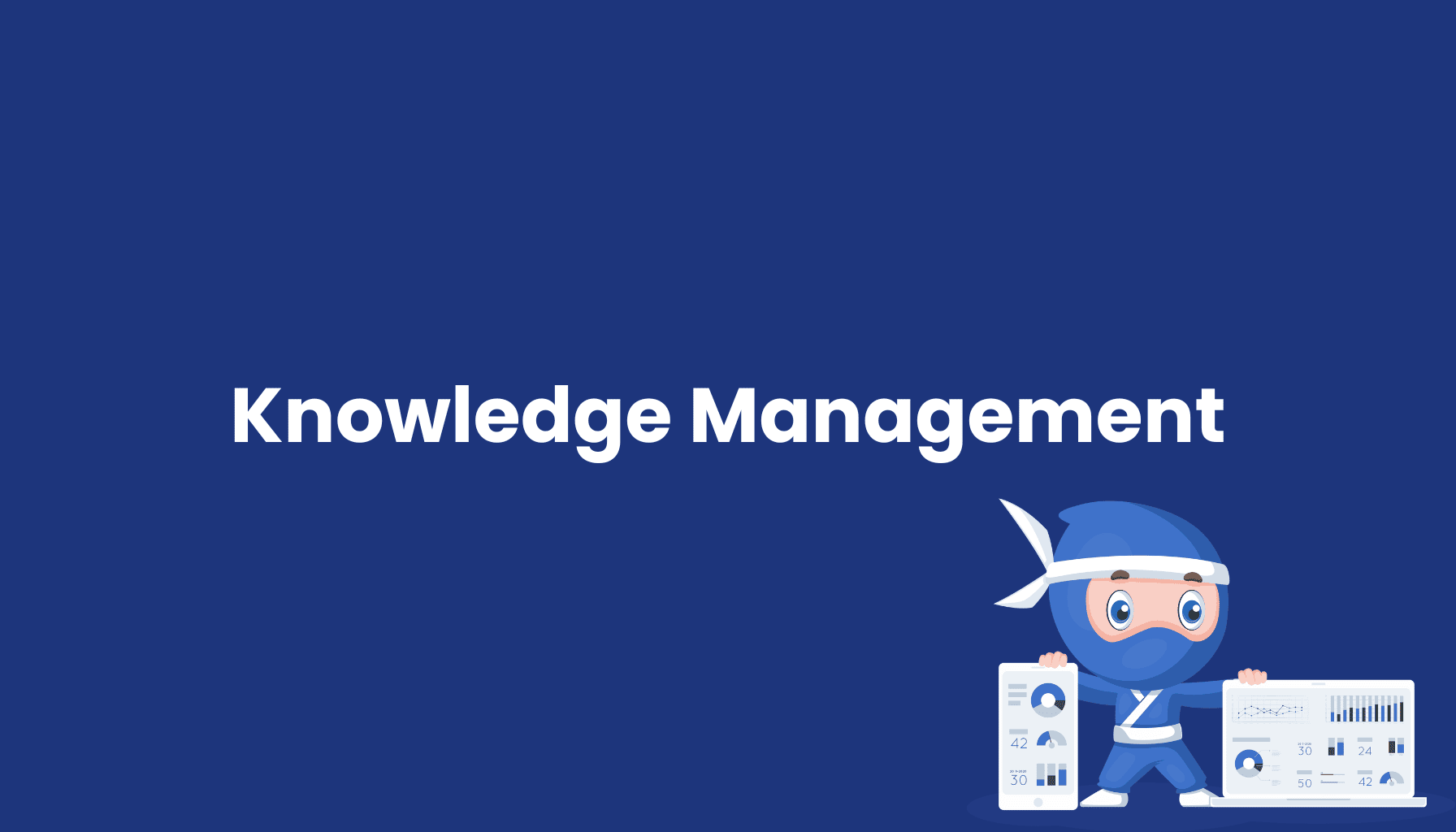
Definition
Knowledge Management in manufacturing encompasses all systematic processes and strategies for capturing, structuring, storing, sharing, and effectively utilizing an organization's production and corporate knowledge. It ensures that the collective knowledge of an organization is optimally leveraged to improve manufacturing processes, foster innovation, and secure sustainable competitive advantages.
Types of Knowledge in Manufacturing
Explicit Knowledge
- Documented Process Knowledge: Manufacturing instructions, work procedures, SOPs
- Technical Documentation: Machine specifications, CAD models, bills of materials
- Quality Standards: Inspection plans, norms, certification requirements
- Project Documentation: Lessons learned, best practices, case studies
Tacit Knowledge
- Experiential Knowledge: Practical skills and troubleshooting expertise
- Expert Know-how: Specialized knowledge of experienced employees
- Process Intuition: Undocumented optimizations and techniques
- Contextual Knowledge: Understanding of complex interrelationships
Core Components
Knowledge Acquisition
- Identification of relevant knowledge sources
- Systematic capture of production and process knowledge
- Documentation of problem solutions and optimizations
- Digitization of analog knowledge
Knowledge Organization
- Structuring by manufacturing areas, processes, or products
- Taxonomies and ontologies for manufacturing knowledge
- Metadata management for improved findability
- Versioning and change tracking
Knowledge Provision
- Knowledge platforms and document management systems
- Intranet portals with production wikis
- Digital work instructions and interactive guides
- Context-sensitive knowledge delivery directly at the workplace
Knowledge Transfer
- Mentoring and training programs
- Communities of practice for manufacturing areas
- Expert directories and skill maps
- Digital learning formats (e-learning, augmented reality)
Knowledge Application
- Integration into operational manufacturing processes
- Knowledge-based decision support
- Best practice sharing between production lines
- Continuous process improvement
Technological Enablers
Digital Knowledge Infrastructure
- Document Management Systems (DMS): Central management of all manufacturing-relevant documents
- Enterprise Content Management (ECM): Comprehensive management of digital content
- Collaboration Platforms: Cross-team knowledge exchange and development
- Semantic Technologies: Intelligent linking of knowledge content
Integration with Manufacturing Systems
- MES Integration: Connecting knowledge management with Manufacturing Execution Systems
- Digital Twin: Virtual representations of physical objects including associated knowledge
- Augmented Reality (AR): Context-sensitive display of relevant information and instructions
- Industrial IoT: Utilization of sensor data for knowledge generation and enrichment
AI-Supported Knowledge Processes
- Intelligent Search Technologies: AI-supported discovery of relevant information
- Automated Knowledge Extraction: From process data and documents
- Recommendation Systems: Suggestion of relevant content based on context
- Predictive Maintenance: Linking experiential knowledge with machine data
Strategic Aspects
Knowledge Management Strategy
- Alignment with corporate and production goals
- Prioritization of critical knowledge areas
- Resource planning and investment decisions
- Definition of KPIs for knowledge management
Knowledge Culture and Change Management
- Promoting an open knowledge culture in production
- Incentivizing knowledge sharing and documentation
- Involving all hierarchy levels in knowledge exchange
- Overcoming silo thinking between departments
Handling Critical Knowledge
- Identification and protection of core knowledge and IP
- Knowledge retention during employee turnover
- Securing expert knowledge before retirement
- Balancing knowledge protection and sharing
Implementation and Best Practices
Implementation Roadmap
- Knowledge Audit: Analysis of existing knowledge assets and gaps
- Strategy Development: Definition of goals and measures
- Pilot Project: Implementation in selected manufacturing areas
- Technology Introduction: Provision of supporting systems
- Roll-out: Company-wide in all relevant areas
- Continuous Improvement: Regular evaluation and adjustment
Success Factors
- Management commitment and leading by example
- User-friendliness of knowledge management systems
- Integration into daily work routines
- Measurable successes and visible added value
- Continuous maintenance and updating of the knowledge base
Common Pitfalls
- Focus on technology instead of people and processes
- Lack of incentives for knowledge sharing
- Insufficient maintenance and updating
- Overloading with irrelevant knowledge
- Complex processes for knowledge contribution
Measurement and ROI
Key Performance Indicators
- Scope and quality of the knowledge base
- Usage rates and access frequencies
- Reduction of training times and error rates
- Improvement of process quality and efficiency
- Time to problem resolution (Mean Time To Repair)
Economic Benefits
- Reduction of downtime through faster access to solutions
- Avoidance of redundant developments and "reinventing the wheel"
- Accelerated onboarding of new employees
- Securing expert knowledge during personnel changes
- Improved product quality through standardized best practices
Integration with Other Management Systems
- Quality Management: Documentation of standards and testing procedures
- Process Management: Provision of process knowledge and documentation
- Innovation Management: Promotion of knowledge exchange and new ideas
- Competence Management: Identification of knowledge holders and training needs
- Change Management: Support for the introduction of new technologies
Future Trends
Industrial AI and Machine Learning
- Automatic recognition and categorization of relevant knowledge
- Intelligent assistance systems with access to corporate knowledge
- Self-learning systems that learn from experiences and solutions
Collaborative Knowledge Ecosystems
- Enhanced knowledge exchange across company boundaries
- Secure platforms for collaboration with suppliers and customers
- Open innovation under controlled conditions
Context-Sensitive Knowledge Systems
- Workplace-integrated knowledge provision (moment of need)
- AR/VR-based knowledge visualization directly at the machine
- Voice-controlled knowledge queries in production
Conclusion
Knowledge Management in manufacturing is a strategic enabler for operational excellence and competitiveness. It connects people, processes, and technologies to optimally utilize and continuously develop an organization's collective knowledge. In times of demographic change, increasing complexity, and accelerating innovation speeds, effective knowledge management becomes a decisive success factor for manufacturing companies.
The integration of knowledge management with modern MES systems, cloud technologies, and intelligent manufacturing solutions creates a foundation for data-driven decisions, accelerated learning curves, and continuous improvement processes – essential elements on the path to the Smart Factory.