Lean Management
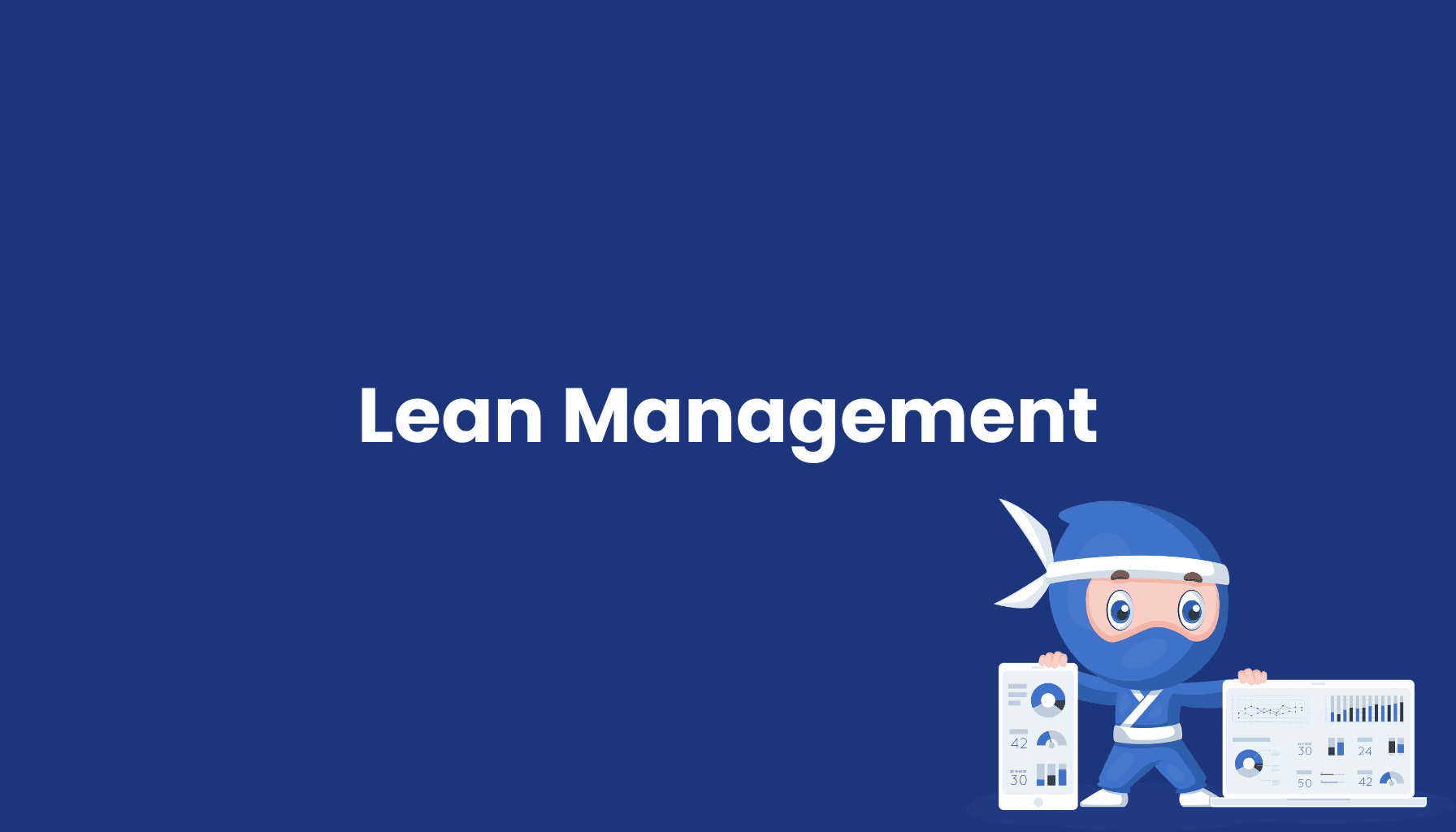
What is Lean Management? – Definition and Objectives
Lean Management is a management philosophy aimed at optimizing processes, increasing efficiency, and reducing waste within an organization. Initially developed by Toyota in the automotive industry, it has become a globally recognized approach across various industries, including manufacturing. The goal of Lean Management is to maximize customer value while minimizing resource use and streamlining processes.
Lean Management Definition
Lean Management can be defined as a systematic approach that aims to achieve maximum efficiency by continuously improving processes and operations. It seeks to eliminate waste at every stage of the value chain while enhancing customer satisfaction. Central to Lean Management are various Lean Methods, which focus on continuous improvement and efficiency enhancement.
Principles of Lean Management
- Define value from the customer's perspective: Only what directly benefits the customer is considered valuable.
- Identify the value stream: All steps in the process that contribute to value creation are clearly identified and analyzed.
- Ensure production flow: Processes should run smoothly without interruptions to avoid waste.
- Implement pull systems: Production and delivery are based on actual demand, preventing overproduction.
- Continuous Improvement (Kaizen): Constant improvement of processes to increase quality, efficiency, and productivity.
Lean Methods and Tools
- 5S Method: A fundamental Lean tool for workplace organization and maintaining order.
- Kaizen: Encourages small, incremental changes for process optimization.
- Kanban: A visual control system for flexible production planning.
- Just-in-Time (JIT): Producing only when there is a demand, reducing inventory costs.
- Value Stream Mapping: Visualizes the entire production process and identifies areas for improvement.
Benefits of Lean Management
- Increased Efficiency: By eliminating waste and optimizing processes, Lean Management significantly boosts efficiency in production and across the organization.
- Cost Reduction: Lean processes lead to reduced material and inventory costs, as well as more efficient use of resources.
- Improved Quality: By focusing on continuous improvement, companies can enhance their product quality.
- Customer Satisfaction: Lean Management’s focus on customer value increases both quality and flexibility, resulting in higher customer satisfaction.
Lean Management in Practice
In practice, Lean Management is often used in manufacturing industries to optimize production systems and streamline production processes. A key element of the Lean philosophy is continuous improvement, helping companies adapt to changing market conditions while improving productivity and efficiency.
Modern manufacturing companies often combine Lean Management with Cloud-native MES solutions like those from Symestic, utilizing real-time data to further optimize production processes and resource management.