Lean Management Methods
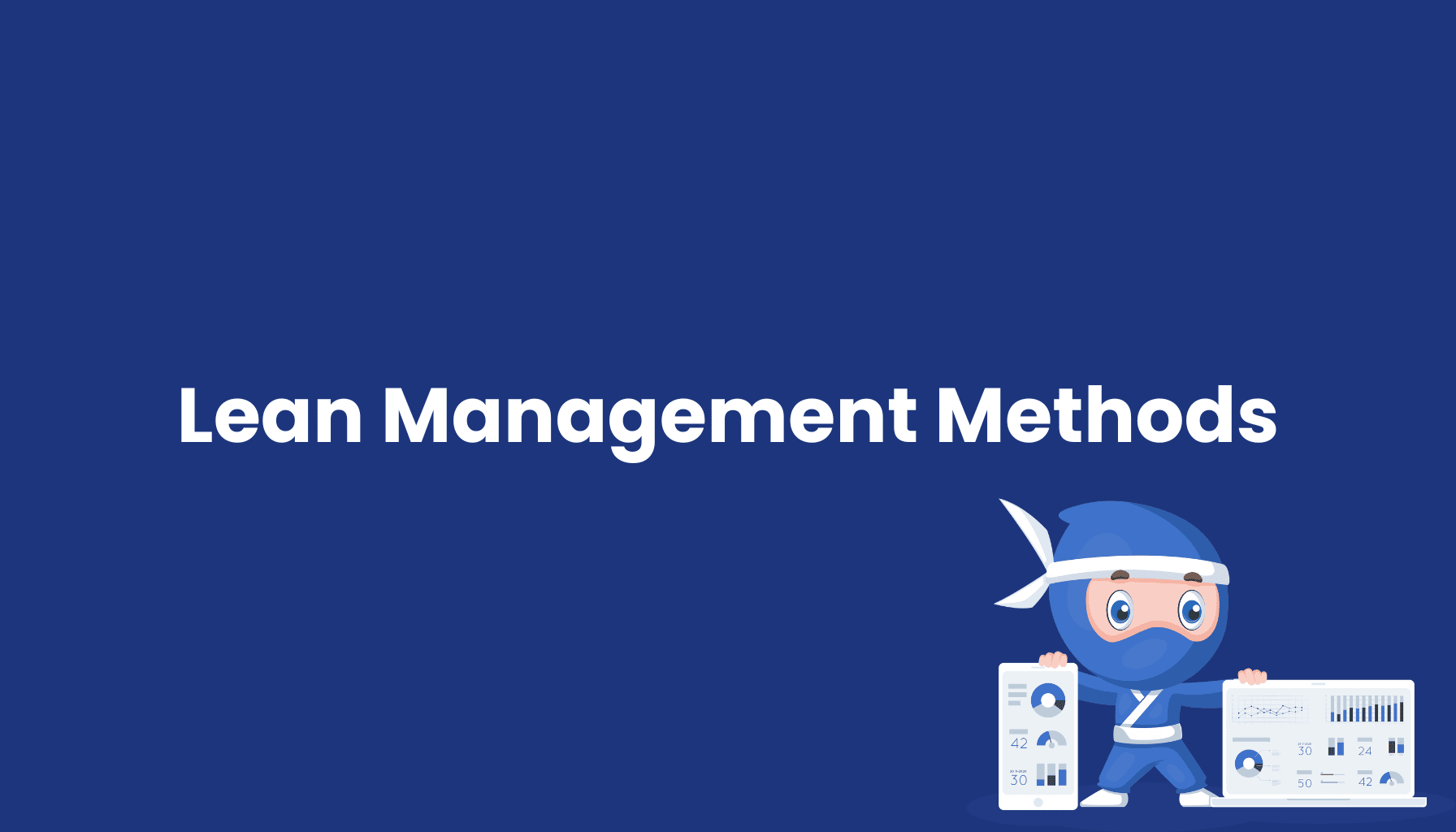
What are Lean Management Methods?
Lean Management methods are a collection of strategies and tools aimed at increasing process efficiency, minimizing waste, and maximizing value creation within companies. These methods are rooted in Lean Management principles, a management philosophy originating from the automotive industry, specifically Toyota. The goal of Lean Management is to improve customer orientation, boost efficiency, and enhance competitiveness by eliminating unnecessary steps in production processes and fostering continuous improvement.
Key Lean Management Methods
Lean Management methods provide a range of approaches to help companies streamline their processes. The most notable include:
-
Kaizen (Continuous Improvement)
Kaizen is a well-known Lean method meaning “change for the better.” It focuses on ongoing, incremental improvements across all company processes, with active involvement from employees in optimization efforts. -
5S Method
This method organizes and standardizes the workplace to increase efficiency and safety. The five steps—Sort, Set in order, Shine, Standardize, and Sustain—create organized workspaces that minimize unnecessary search and wait times. -
Just-in-Time (JIT) Production
JIT is a Lean method focused on delivering products at the right time and in the right quantity to minimize inventory and streamline material flow. This reduces costs and enhances production flexibility. -
Value Stream Mapping
This tool visualizes the value creation process, identifying non-value-added steps. It enables companies to detect waste and optimize workflows for increased efficiency. -
PDCA Cycle (Plan-Do-Check-Act)
The PDCA cycle is a continuous improvement process involving planning, implementing, evaluating, and refining actions. It’s used to plan improvements, assess success, and apply insights to future processes. -
Six Sigma
Six Sigma is a data-driven method for process optimization focused on reducing errors and deviations in production. Often combined with Lean methods, it enhances both efficiency and quality.
Principles of Lean Management
Lean Management principles form the foundation for all methods and tools used in this philosophy. The main principles include:
- Define Value from the Customer’s Perspective: Focus on delivering maximum value to customers, considering anything without value as waste.
- Identify the Value Stream: Analyze the value-creation process to eliminate unnecessary steps.
- Create Flow: Ensure that all steps contributing to value proceed without interruptions or delays.
- Implement a Pull System: Align production with actual customer demand to produce only what is needed.
- Strive for Perfection: Continuously improve processes to maximize efficiency and minimize errors.
Lean Management in Practice
Lean Management has proven especially effective in production but is increasingly applied in other areas, including management, service delivery, and logistics. Companies that successfully implement Lean Management benefit from a streamlined organization, improved processes, and reduced costs. Employee involvement in improvement efforts is essential for long-term success.
A notable example of Lean Management application is Just-in-Time in the automotive industry, which allows companies like Toyota to streamline production, minimize inventory, and enhance customer satisfaction.
Benefits of Lean Management Methods
Applying Lean Management methods offers numerous advantages:
- Increased Efficiency: By eliminating unnecessary steps and optimizing processes, productivity is significantly boosted.
- Cost Reduction: Reducing waste and efficiently utilizing resources help lower operating costs.
- Enhanced Customer Orientation: Lean Management prioritizes customer needs, ensuring that they remain central to process design.
- Improved Competitiveness: Optimized processes and increased efficiency allow companies to respond more flexibly and competitively in the market.
- Continuous Improvement: Lean Management fosters a culture of ongoing improvement, with employees actively contributing to workflow optimization.
Challenges in Implementing Lean Management Methods
Despite the benefits, implementing Lean Management methods presents some challenges:
- Cultural Shift: Implementing Lean Management often requires a profound cultural shift within the organization, with employees at all levels needing to be engaged and supported.
- Resistance to Change: Employees may be skeptical of new processes and working methods, potentially hindering the success of Lean initiatives.
- Training and Development: Successful application of Lean methods requires extensive training to ensure employees understand Lean Management principles and tools and can apply them effectively.
Lean Management methods provide companies with the tools to systematically enhance efficiency, eliminate waste, and achieve sustainable growth through a commitment to continuous improvement.