Lean Manufacturing
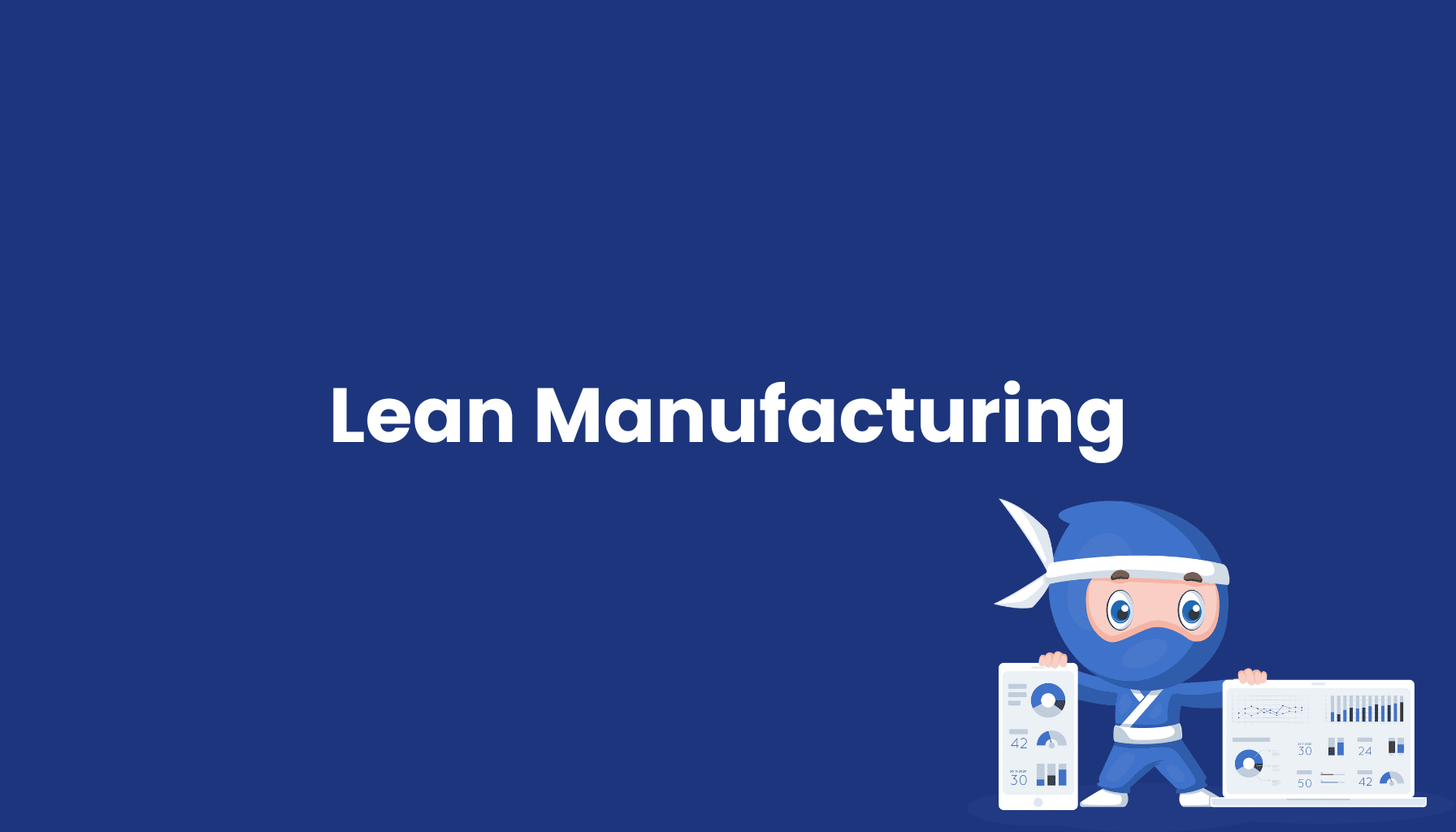
What is Lean Manufacturing?
Lean Manufacturing is a systematic approach aimed at minimizing waste and maximizing productivity within manufacturing systems. Also known as Lean Production, this concept originated in the Japanese automotive industry, particularly at Toyota, to increase efficiency in production processes, reduce costs, and improve both quality and flexibility.
Distinction Between Lean Manufacturing, Lean Production, and Lean Management
-
Lean Manufacturing: This term specifically focuses on production processes and optimizing manufacturing workflows. Key techniques include Just-In-Time (JIT) production, continuous improvement (Kaizen), and Total Quality Management (TQM). The primary goal is to maximize efficiency within product manufacturing.
-
Lean Production: Often used interchangeably with Lean Manufacturing, Lean Production actually refers to the entire production chain, covering resources, material flow, and supply chains. While Lean Manufacturing is centered on production, Lean Production has a broader scope that includes pre- and post-production activities.
-
Lean Management: This is a broader concept that goes beyond production, applying Lean principles across the entire organization. Lean Management incorporates elements of Lean Manufacturing and Lean Production but extends them to finance, HR, and customer service, fostering a culture of continuous improvement and boosting overall organizational performance.
Core Elements of Lean Manufacturing
-
Identifying Waste (Muda): Lean Manufacturing targets the elimination of seven key types of waste—overproduction, waiting, transport, over-processing, inventory, motion, and defects—making production workflows more efficient.
-
Continuous Improvement (Kaizen): This process empowers all employees to actively seek out and implement improvements, creating a dynamic culture of ongoing optimization.
-
Just-In-Time (JIT) Production: JIT minimizes inventory by producing goods only as needed, boosting flexibility and reducing storage costs.
-
Quality Assurance: By implementing error-proofing and ongoing quality checks, Lean Manufacturing consistently enhances product quality.
Advantages of Lean Manufacturing
- Cost Reduction: Eliminating waste lowers operating costs and creates a more cost-efficient production process.
- Increased Flexibility: Lean Manufacturing allows companies to adapt to fluctuations in demand with ease.
- Improved Product Quality: Constant quality monitoring and improvement raise customer satisfaction.
- Efficiency Gains: Optimized resource use enhances productivity across the board.
Lean Manufacturing in the Modern Industry
In the era of Industry 4.0, Lean Manufacturing integrates technologies like the Internet of Things (IoT) and Big Data, which enable more precise monitoring and optimization of production processes. These advances further improve efficiency and allow companies to adjust rapidly to market shifts.
Conclusion: Lean Manufacturing remains a crucial approach for optimizing production processes, improving efficiency, and maintaining flexibility in the manufacturing industry. By minimizing waste, fostering continuous process improvement, and utilizing advanced technology, Lean Manufacturing continues to play a pivotal role in enhancing competitiveness and quality in modern industry.