Machine Availability
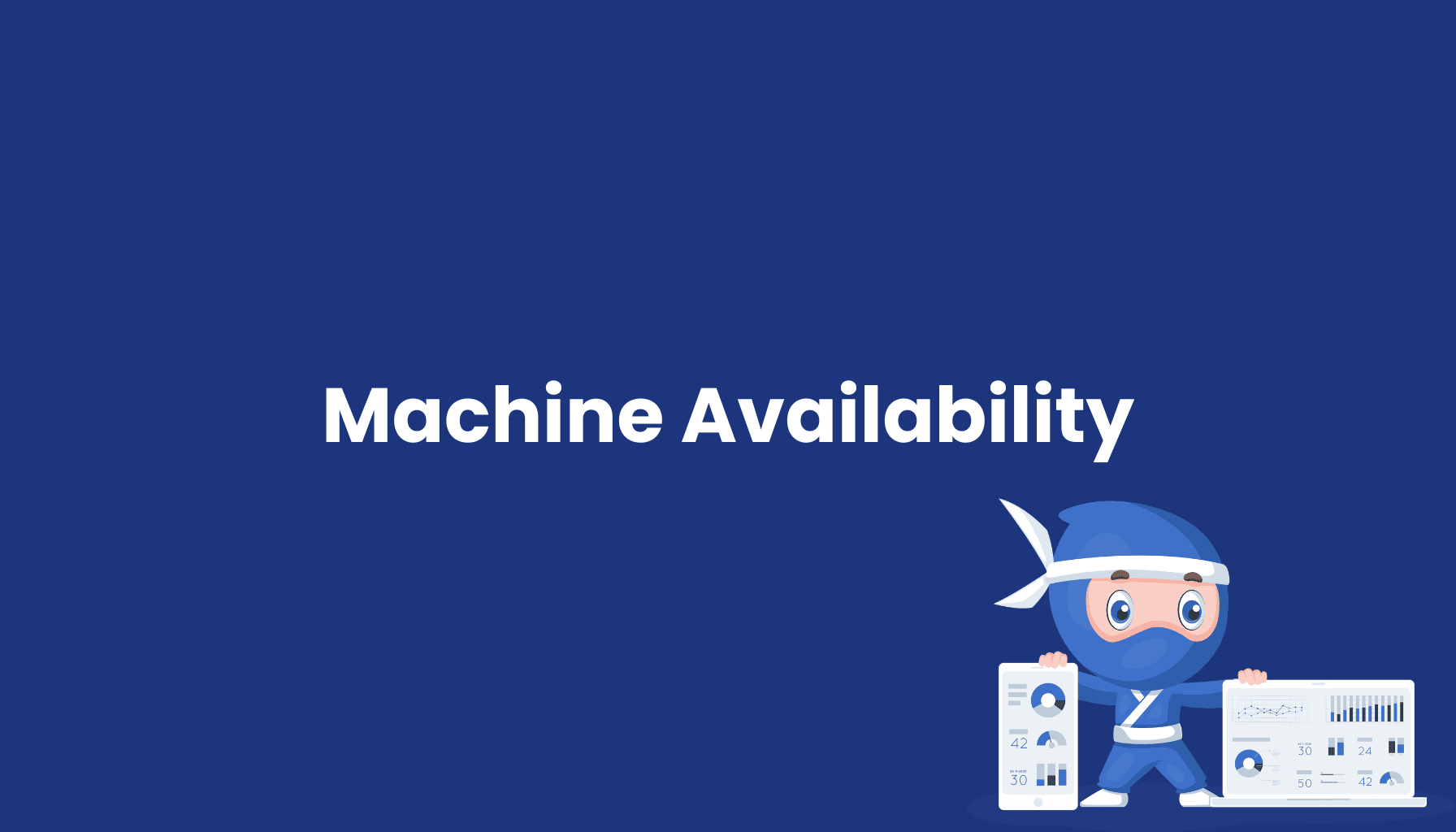
What is Machine Availability?
Machine availability is a critical metric in manufacturing that measures the proportion of time a machine or system is actually operational and ready for production. It is calculated as the ratio of actual operating time to planned production time. High machine availability is crucial for a company's efficiency and productivity as downtime due to maintenance, failures, or technical issues can lead directly to production losses.
Machine availability also plays a significant role in overall equipment availability, encompassing the readiness of all machines and systems within a facility. In modern production settings, metrics such as machine availability and Overall Equipment Effectiveness (OEE) are used to comprehensively assess the performance of equipment.
Difference Between Machine Availability and OEE
While machine availability focuses on the operational readiness time of a machine, OEE is a more comprehensive metric that considers three essential factors: availability, performance, and quality. Availability assesses operational readiness relative to planned production time, performance measures actual production speed versus ideal rates, and quality evaluates the proportion of defect-free products produced.
By integrating these factors, OEE provides a complete view of equipment efficiency in manufacturing, with machine availability being a crucial component but augmented by performance and quality considerations.
Calculating Machine Availability
Machine Availability (%)=(Planned Production TimeOperating Time)×100
This indicates that 30% of the planned production time was lost, leading to decreased production capacity.
To determine the machine availability rate, use the following formula:
Machine Availability (%)=(Operating TimePlanned Production Time)×100\text{Machine Availability (\%)} = \left(\frac{\text{Operating Time}}{\text{Planned Production Time}}\right) \times 100Machine Availability (%)=(Planned Production TimeOperating Time)×100
Where:
- Operating Time is the actual time the machine is in operation and producing products.
- Planned Production Time includes the total time the machine is scheduled to be operational, minus any planned downtime for maintenance or breaks.
This calculation provides a percentage that reflects the proportion of time the machine is available and functioning as intended compared to its scheduled operating time.