Maintenance Work
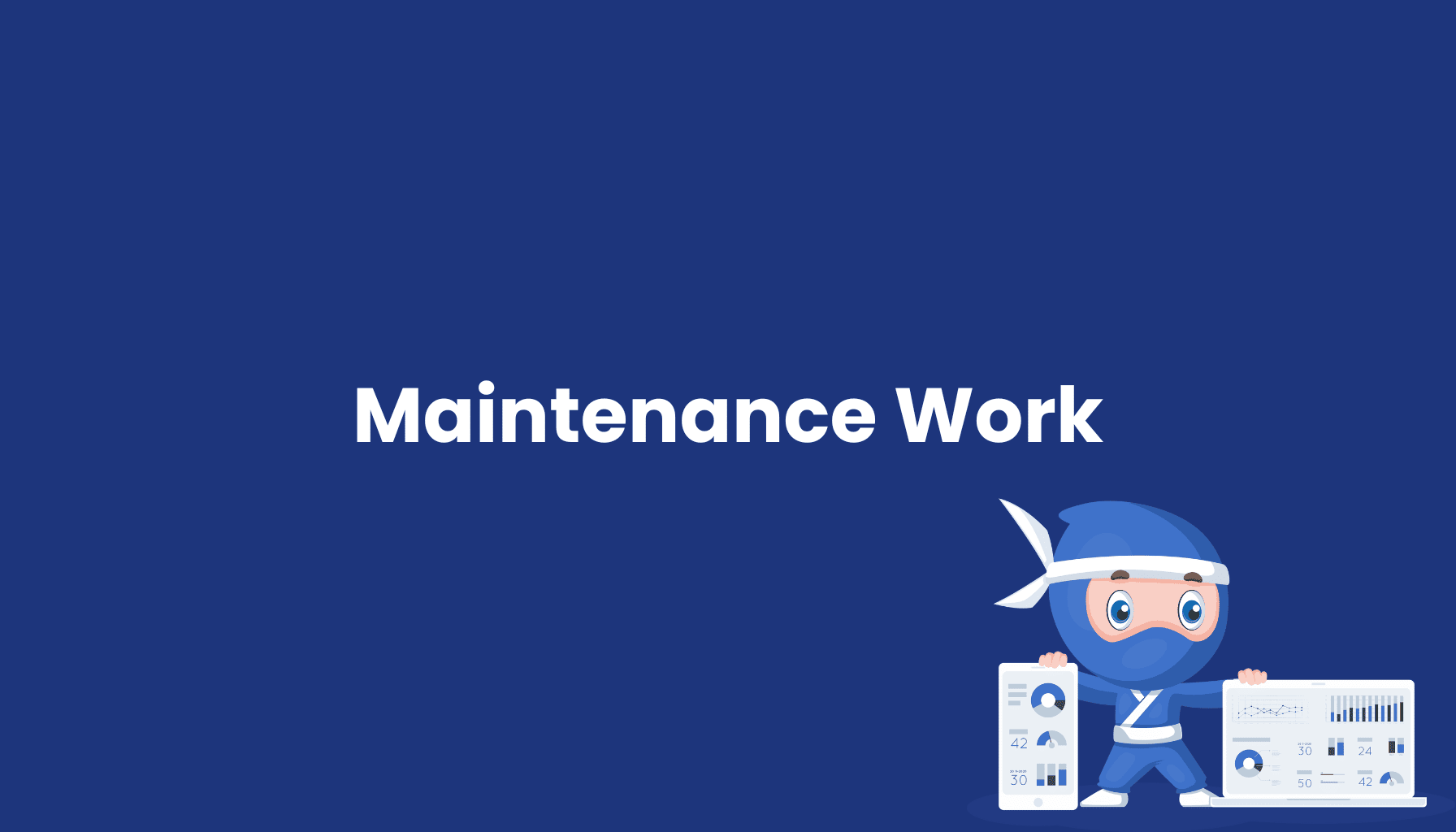
What is Maintenance Work?
Maintenance work consists of regular activities to ensure the functionality and safety of machines, equipment, and systems within an operation. These activities include inspections, repairs, and component replacements to keep production running smoothly and prevent unexpected disruptions or breakdowns. Maintenance work is a core element of operations management, contributing to maximizing machine lifespan and optimizing performance. Many modern companies utilize a central system to manage all maintenance activities, making machine status information easily accessible at all times.
Importance of Maintenance Work in Operations
For any company operating machinery and equipment, maintenance work is essential to maintain continuous production performance and safety. Effective maintenance ensures smooth operational processes and helps to avoid costly downtime and extensive repairs. A well-structured maintenance schedule ensures that all maintenance tasks are performed on time, keeping machinery in optimal condition. A central system facilitates maintenance planning and monitoring by providing instant access to maintenance data and reports.
Types of Maintenance Work
Various methods are used to perform maintenance tasks, depending on the equipment and industry. The main types include:
-
Preventive Maintenance: Regular measures aimed at checking the condition of machines and equipment to detect potential issues early. This includes inspections, cleaning, and replacing wear parts to prevent malfunctions.
-
Corrective Maintenance: This type of maintenance is performed when a failure or issue has already occurred, with the goal of quickly repairing the machine or equipment to resume operations.
-
Predictive Maintenance: This method uses sensors and data analytics to monitor the machine's condition in real-time, allowing maintenance tasks to be performed only when needed, thereby reducing costs and downtime. A central system gathers this data and provides instant information on machine performance and required maintenance.
Conducting Maintenance Work
A structured approach is essential for conducting maintenance work effectively and safely. Key steps include:
-
Inspection: Regular checks for wear or damage on machines and equipment.
-
Planning: Developing a maintenance schedule that covers all machines and outlines maintenance intervals. Many companies integrate this schedule into a central system for comprehensive monitoring.
-
Repair and Replacement: Replacing or repairing defective parts as needed to ensure safe operations.
-
Documentation: Recording all maintenance activities in a central system, creating transparency and easing the planning of future maintenance work.
Benefits of Regular Maintenance Work
Regular maintenance offers numerous benefits:
-
Increased Safety: Potential hazards are detected and addressed early, improving safety for both staff and equipment.
-
Extended Lifespan: Regular maintenance extends the lifespan of machines by timely replacement of wear parts and damage prevention.
-
Cost Reduction: Preventive maintenance helps to avoid major, costly repairs and minimizes production downtimes.
-
Maximized Productivity: Properly maintained machines operate more efficiently and reliably, increasing overall productivity.
Challenges in Maintenance Work
Despite its advantages, maintenance work presents certain challenges:
-
Planning and Execution: Maintenance must be scheduled to minimally disrupt ongoing operations, which requires effective coordination.
-
Costs: Preventive maintenance may involve significant upfront costs, as parts are regularly inspected or replaced.
-
Technological Requirements: Modern equipment often requires specialized solutions and expertise. Companies need to ensure their staff are adequately trained or can access external services as needed.
Maintenance Work and Digitalization
With increasing digitalization, companies are increasingly adopting smart maintenance solutions like predictive maintenance. Sensors and digital systems enable real-time monitoring for targeted and efficient maintenance planning. Central systems play a key role by processing collected data and providing immediate access to maintenance information. This setup also allows users to search for specific terms in a central system to quickly find maintenance documentation or repair instructions.
Conclusion
Maintenance work is essential for companies operating machinery and equipment, ensuring safety, efficiency, and reliability in production. By adopting modern maintenance systems, such as central systems that provide easy access to information and documentation, companies can ensure smooth operations and minimize production downtime.