Material Flow
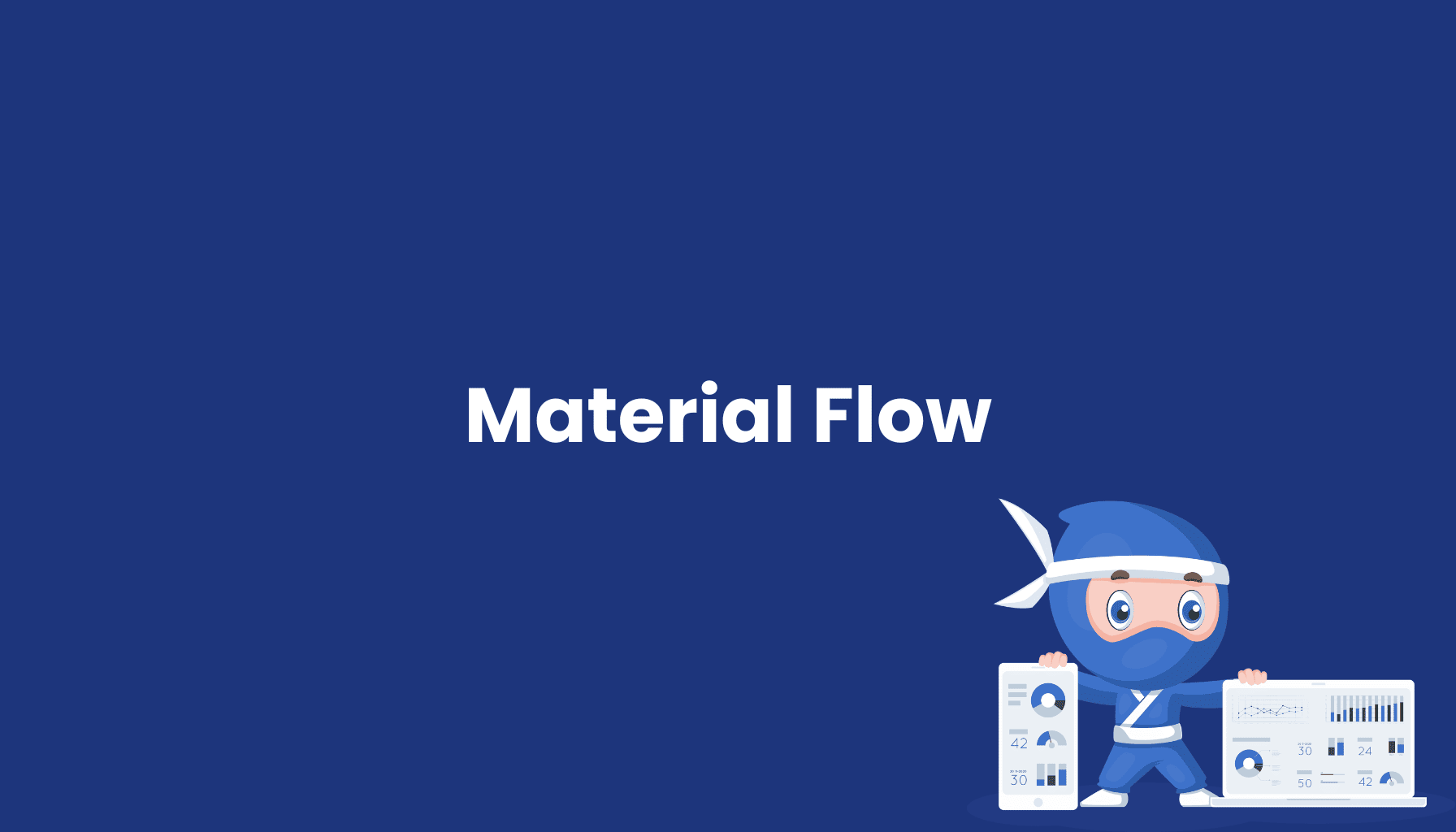
What is Material Flow?
Material flow refers to the movement and transportation of materials, components, raw materials, and products within a company or throughout an entire logistics chain. It encompasses all operations involved in moving materials and goods, from their entry into the company, through storage and in-house processing, to dispatch to the customer, and includes coordination with suppliers.
A smooth material flow is crucial for efficient production, high product quality, and an effective cost structure.
Core Components of Material Flow
-
Transportation: This involves moving materials within the company, such as between storage, production, and distribution points. Choosing the right transport methods is essential to streamline the flow of goods and support production processes.
-
Storage: Materials are often temporarily stored between production stages. Proper storage ensures that necessary materials are readily available without excessively inflating in-house inventory.
-
Material Processing: During production, raw materials are transformed into finished products. Material flow includes all in-production processing steps required to manufacture and prepare goods for the market in the desired form.
-
Packaging and Shipping: After production, products are packaged and shipped to the customer. Efficient packaging not only ensures safe transportation but also minimizes storage costs and transport distances.
Importance of Material Flow for Companies
A well-designed material flow is essential for improving productivity and optimizing the cost structure. By reducing unnecessary material movements, optimizing storage capacities, and improving logistical processes with suppliers, companies can increase profit margins.
Key advantages include:
-
Cost Reduction: Efficient material flow planning shortens transport routes, reduces storage times, and avoids unnecessary expenses.
-
Enhanced Productivity: An optimized material flow shortens production times and ensures smooth transitions between production stages.
-
Competitive Advantage through Flexibility: A flexible, fast material flow enables companies to respond more quickly to changing demand and customer requirements.
-
Sustainability and Resource Conservation: Reduced storage and efficient material flow help save resources and energy, lowering costs and offering sustainable benefits.
Challenges and Solutions in Material Flow
With increasing globalization and the high demand for rapid, precise logistics, companies face significant challenges. Integrating a well-planned, optimized material flow is essential.
Common optimization methods include:
-
Material Flow Analysis: This method identifies inefficiencies within the logistics chain for targeted improvement. Companies often use specialized software and ERP systems to analyze and optimize material flows and transport routes.
-
Automation and Digitalization: With technologies like IoT and software solutions, material flow can be transparently monitored and controlled, accelerating processes and minimizing errors.
-
Lean Methods: Lean management focuses on eliminating waste and continuously improving material flow. Examples include just-in-time production, where materials are only supplied as needed.
The Future of Material Flow: Industry 4.0 and Digitalization
Increasing digitalization and technologies like IoT, AI, and Big Data are transforming material flow processes. Data-driven technologies provide real-time transparency, precise tracking of material inventory, and precise planning that makes in-house material flow even more efficient.