Manufacturing Resource Planning (MRP)
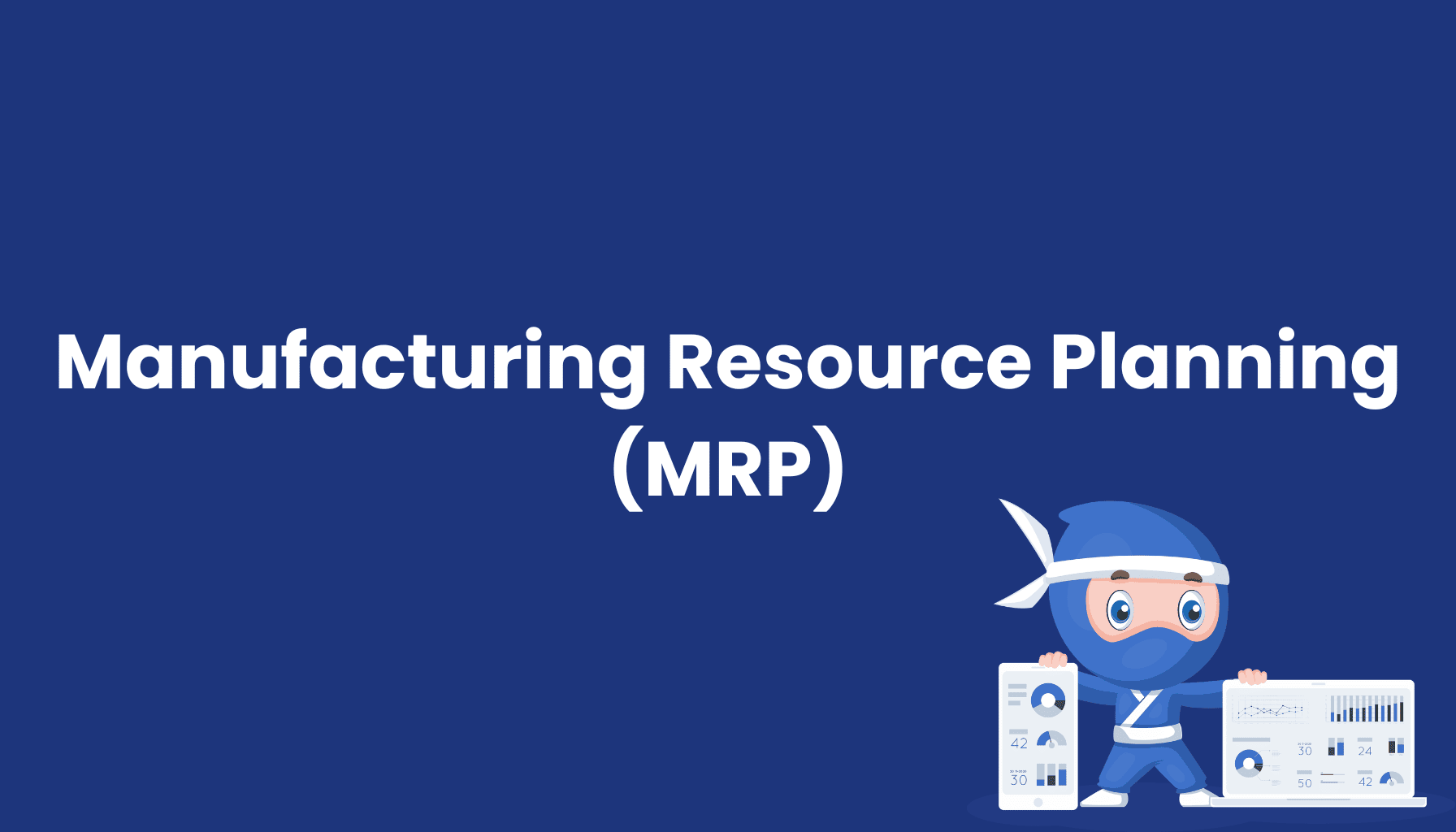
What is Manufacturing Resource Planning (MRP)?
Manufacturing Resource Planning (MRP) is an integrated system that assists companies in planning and managing production resources. MRP relies on accurate analysis of material requirements and production capacities to ensure efficient manufacturing. The primary goal is to optimize material flow and ensure that the right materials are available at the right time and in the correct quantities.
Key Features of MRP Systems
- Resource Planning: MRP aids in planning material and capacity needs by utilizing data from inventory levels, production orders, and sales forecasts.
- Inventory Management: The system optimizes inventory levels, ensuring that stock is neither excessively high nor too low, thus supporting continuous production.
- Production Control: MRP generates detailed production schedules that ensure efficient production flows and help prevent bottlenecks.
Benefits of MRP
- Efficiency Improvement: MRP helps in better planning and coordination of production processes, enhancing efficiency and reducing production costs.
- Cost Reduction: By optimizing inventory levels and reducing material waste, MRP contributes to lower storage and inventory costs.
- Flexibility: MRP allows companies to quickly adapt to changing market conditions and production demands by providing flexible production schedules.
Application of MRP in the Manufacturing Industry
In the manufacturing industry, MRP is critical for optimizing production processes. It ensures that materials are procured on time and that production capacities are utilized efficiently. This is particularly vital during periods of fluctuating demand or when launching new products, as MRP enables companies to allocate resources effectively and adjust production plans flexibly.