Needs Analysis in Manufacturing
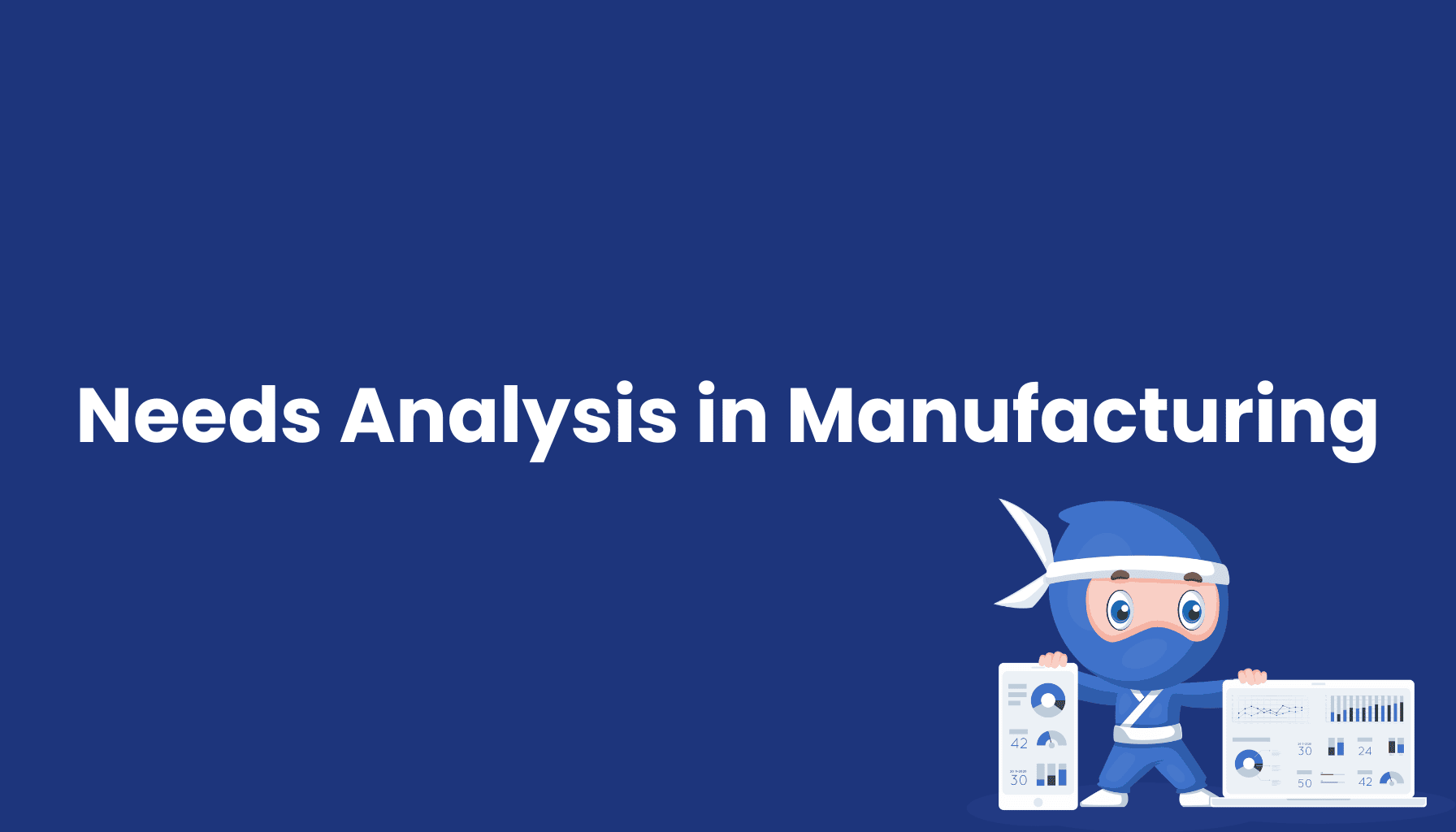
What Is Needs Analysis in Manufacturing?
Conducting a systematic needs analysis forms the foundation for efficient production planning and resource allocation. A structured analysis process enables precise identification of requirements and optimization opportunities in the manufacturing environment.
Methodological Foundations
Needs analysis is based on a multi-stage evaluation system incorporating quantitative and qualitative components.
- Requirements Engineering Frameworks systematically structure requirement gathering.
- Data Collection Protocols standardize information acquisition.
- Analytical Hierarchy Process prioritizes identified needs methodically.
Capacity Needs Assessment
Accurate quantification of production capacity requirements involves systematic analytical methods:
- Production Volume Analysis evaluates historical production data.
- Demand Forecasting projects future capacity requirements.
- Resource Utilization Assessment quantifies usage rates.
- Capacity Planning Tools optimize resource allocation.
Technology Needs Analysis
Evaluation of technological requirements integrates multiple assessment dimensions:
- Technology Assessment Matrix evaluates automation potential.
- Digital Maturity Analysis identifies digitalization needs.
- Equipment Modernization Planning structures investment requirements.
- Process Optimization Requirements define areas for improvement.
Workforce Planning
Systematic analysis of personnel requirements includes:
- Skill Gap Analysis identifies competency deficiencies.
- Workforce Planning quantifies personnel capacities.
- Training Needs Assessment evaluates upskilling requirements.
- Succession Planning ensures long-term workforce availability.
Material and Logistics Needs
Evaluation of logistical requirements focuses on:
- Material Requirements Planning optimizes inventory management.
- Supply Chain Analysis assesses supply chain needs.
- Inventory Optimization defines stockholding strategies.
- Transportation Needs Assessment structures logistical frameworks.
Quality Requirements
Systematic identification of quality requirements integrates:
- Quality Standards Compliance evaluates regulatory adherence.
- Process Capability Analysis assesses quality potential.
- Testing Requirements Definition structures inspection frameworks.
- Documentation Needs Assessment plans quality assurance systems.
Implementation and Monitoring
Continuous monitoring of needs development requires:
- Performance Monitoring Systems track key metrics.
- Variance Analysis systematically identifies deviations.
- Adjustment Mechanisms enable dynamic changes.
- Review Cycles regularly validate demand forecasts.