Operating Costs
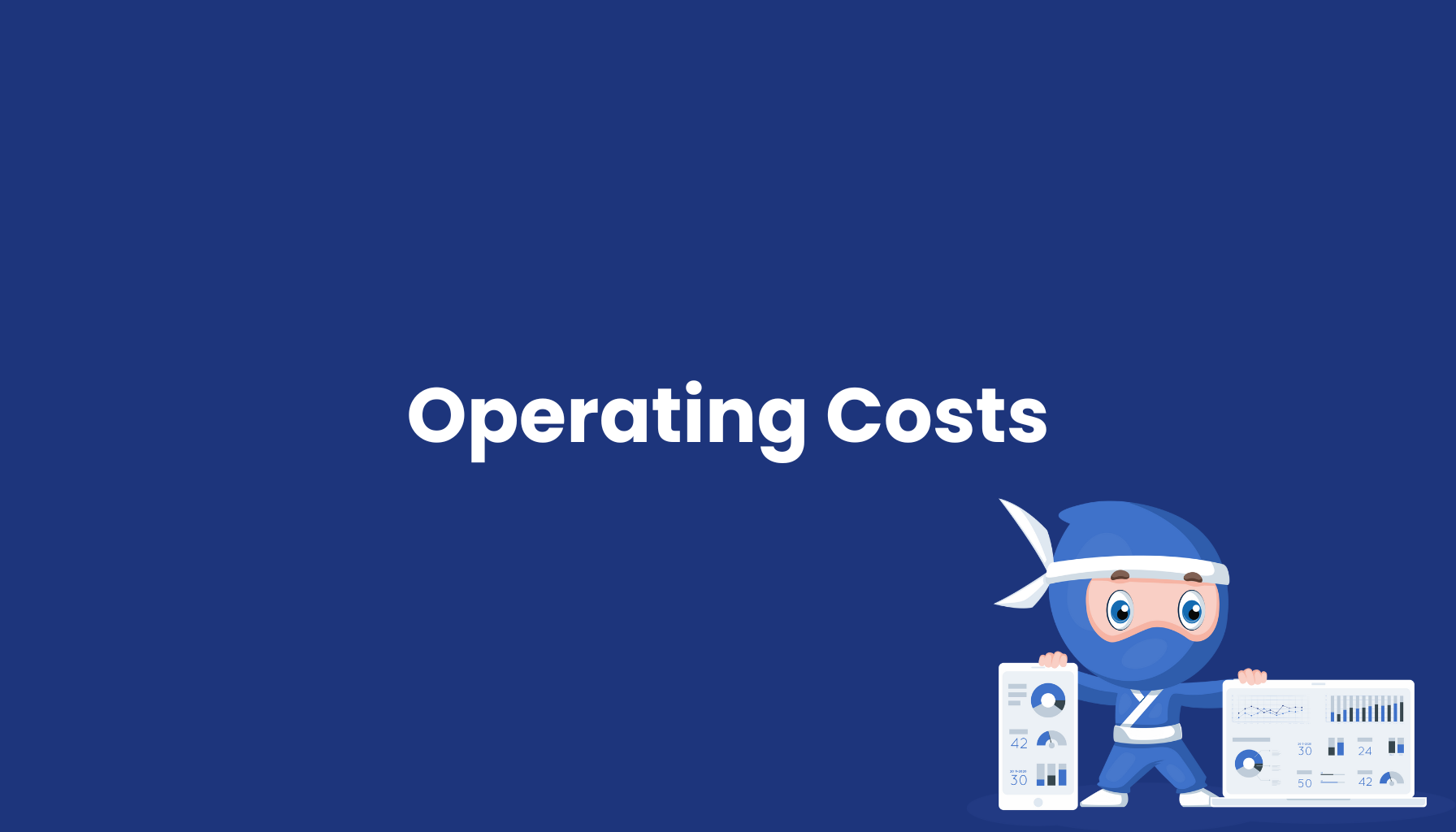
What are Operating Costs in an Industrial Context?
Operating costs refer to all ongoing expenses related to running a business or production facility. In an industrial setting, these costs encompass various items, such as energy consumption, maintenance, labor expenses, and the upkeep of machinery and equipment essential for daily production operations. Effective control and optimization of these costs are crucial for enhancing efficiency and profitability.
Key Components of Operating Costs in Industry
Operating costs in industrial settings comprise multiple items necessary for maintaining production:
-
Energy Costs: Expenses for electricity, gas, and other energy sources needed to power machinery and equipment.
-
Maintenance and Repair Costs: Routine upkeep and repairs on machines to ensure operational safety and readiness.
-
Labor Costs: Wages and benefits for personnel involved in production, maintenance, administration, and logistics.
-
Facility Costs: Expenses for using and maintaining buildings and auxiliary facilities where production occurs.
-
Administrative Costs: Overheads related to company operations, such as data management, accounting, and HR activities.
Importance of Operating Cost Management
Close monitoring of operating costs is essential for production businesses to remain competitive. By employing strategies such as energy-efficient equipment and automated processes, companies can reduce production expenses and increase efficiency. A structured operating cost accounting system that systematically records all costs helps identify potential savings and minimize overall expenditure.
Types of Operating Costs in Manufacturing
In manufacturing, operating costs can be categorized as follows:
-
Direct Costs: Expenses directly linked to the production of a specific product, including materials, energy, and labor time.
-
Indirect Costs: Costs that cannot be assigned to a specific product, such as machine maintenance, administration, and building expenses.
-
Variable Costs: Costs that vary with production volume, such as raw material consumption and energy use.
-
Fixed Costs: Unchanging costs, independent of production volume, such as rent or administrative expenses.
Analyzing and optimizing these types of costs can lead to improvements in production process efficiency.
Influence of Operating Costs on Production Planning
Operating costs directly impact production planning. Detailed cost analysis supports decisions related to production volumes, technology investments, and maintenance schedules. Particularly in large-scale production facilities, like those in the automotive industry, operating costs are crucial to long-term profitability. The implementation of efficient energy management systems and optimized resource use helps reduce operating expenses and enhance productivity.
Operating Cost Optimization in an Industrial Setting
Successful operating cost optimization in an industrial context requires thorough cost analysis and targeted measures. Common strategies include:
-
Energy Efficiency: Using energy-efficient equipment to significantly lower energy expenses.
-
Automation: Reducing labor costs and increasing production efficiency with automation solutions.
-
Maintenance Strategies: Thoughtful maintenance planning and predictive maintenance help minimize repair costs and downtime.
-
Logistics Optimization: Improved logistics processes reduce transportation and warehousing costs.
Challenges in Managing Operating Costs
Managing operating costs can be challenging, especially when it comes to accurately recording and allocating costs to specific products. Additionally, companies need to adapt to rising energy and raw material prices to maintain profitability.