Operating Time
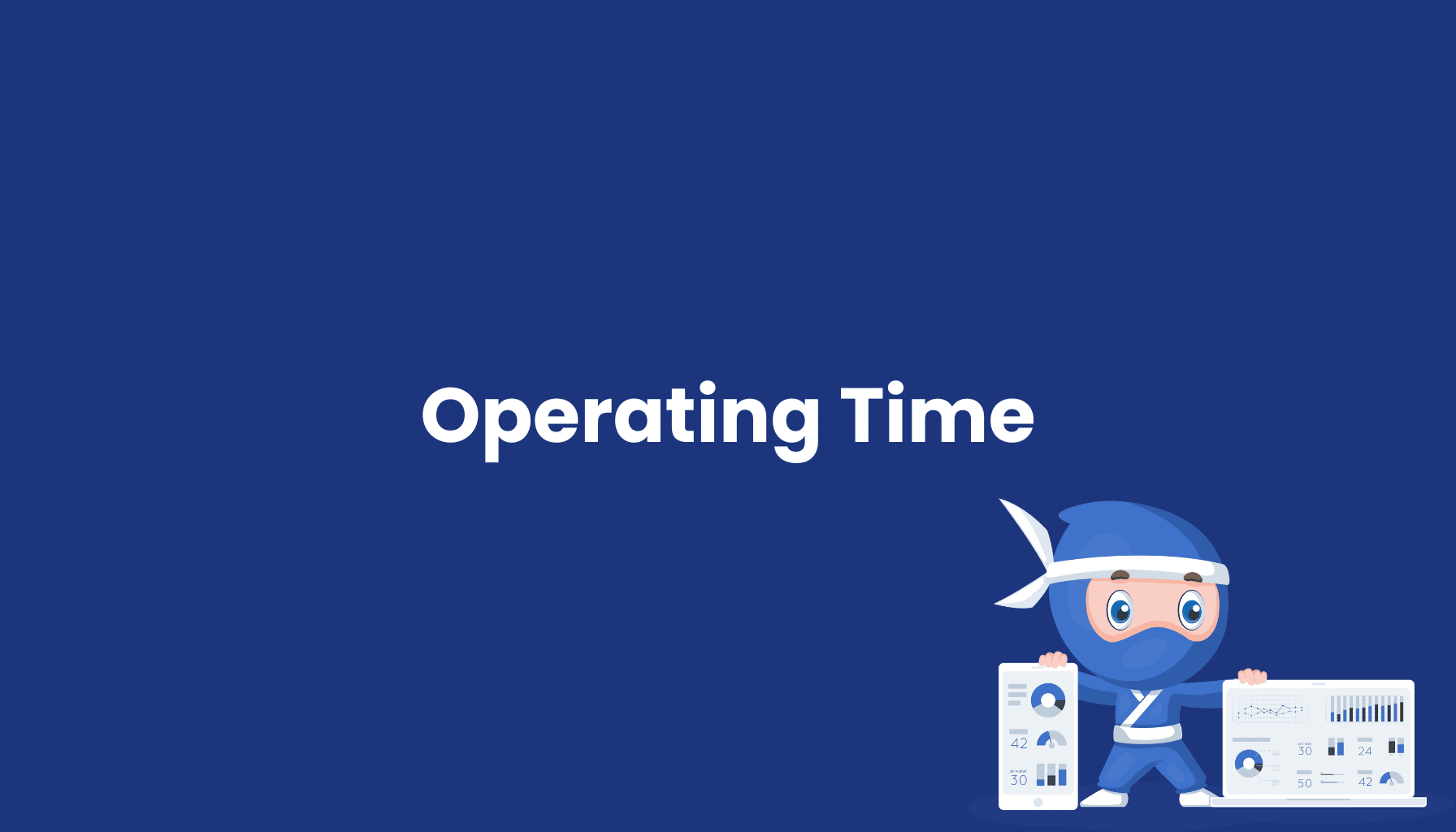
What is Operating Time?
Operating time refers to the duration in which a machine, system, or facility is operational and functional. In industrial and corporate environments, it serves as a critical key performance indicator (KPI) for measuring efficiency and productivity. The higher the operating time, the better the utilization of assets, which is essential for a company’s productivity and profitability.
Definition and Importance of Operating Time
Operating time is the period during which a machine or facility is actively in use and available to the company. Often referred to as "uptime" or operational duration, it represents the time a machine operates without interruptions. This metric is vital as it directly correlates with equipment reliability, operational efficiency, and availability.
Key Factors Affecting Operating Time
Several factors can either improve or reduce operating time, including:
- Maintenance and Servicing: Regular maintenance minimizes breakdowns and extends operating time by ensuring smooth operation.
- Equipment Quality: High-quality machines and systems are typically more robust and offer extended operating durations.
- Operational Strategies: Optimized schedules, such as multi-shift operations, help maximize operating time by utilizing machinery efficiently.
- Software and Systems: Reliable software solutions, like ERP and monitoring systems, ensure real-time tracking and control, contributing to extended operating time.
Advantages of High Operating Time
Maximizing operating time delivers several benefits, significantly enhancing overall operational efficiency. Key advantages include:
- Increased Productivity: Longer operating times mean more output can be generated within the same timeframe, boosting company efficiency.
- Cost Reduction: Higher operating time reduces downtime, resulting in lower costs for repairs and lost production.
- Better ROI on Investments: Maximized operating time extends the effective use of machinery and equipment, improving profitability and return on investment.
How to Calculate Operating Time
The operating time can be calculated using a simple formula that measures the proportion of utilization against total time:
\text{Operating Time (%) =} \frac{\text{Utilized Time of Equipment}}{\text{Total Available Time}} \times 100
This percentage indicates the proportion of time a machine or system is in operation, serving as a benchmark for equipment efficiency.
Strategies to Increase Operating Time
Companies implement various strategies and technologies to extend operating time, including:
- Preventive Maintenance: Scheduled maintenance helps minimize breakdowns and maximize operational hours.
- Digitalization and Monitoring: Real-time monitoring systems and data analytics allow for immediate action in case of faults, reducing downtime.
- Upgraded Equipment: Investing in modern machines and software solutions often leads to increased reliability and longer operating periods.
The Role of Operating Time in Industrial Applications
Operating time is a pivotal factor in industries like manufacturing and energy, as it directly impacts equipment availability, production planning, and reliability. For energy-intensive sectors, high operating time ensures steady energy production and optimal capacity utilization. In production environments, it guarantees smoother processes, enabling businesses to meet customer demands efficiently.
By optimizing operating time, companies can align their production processes with business goals, improving both performance and profitability.