Operational Technology (OT)/(IT)
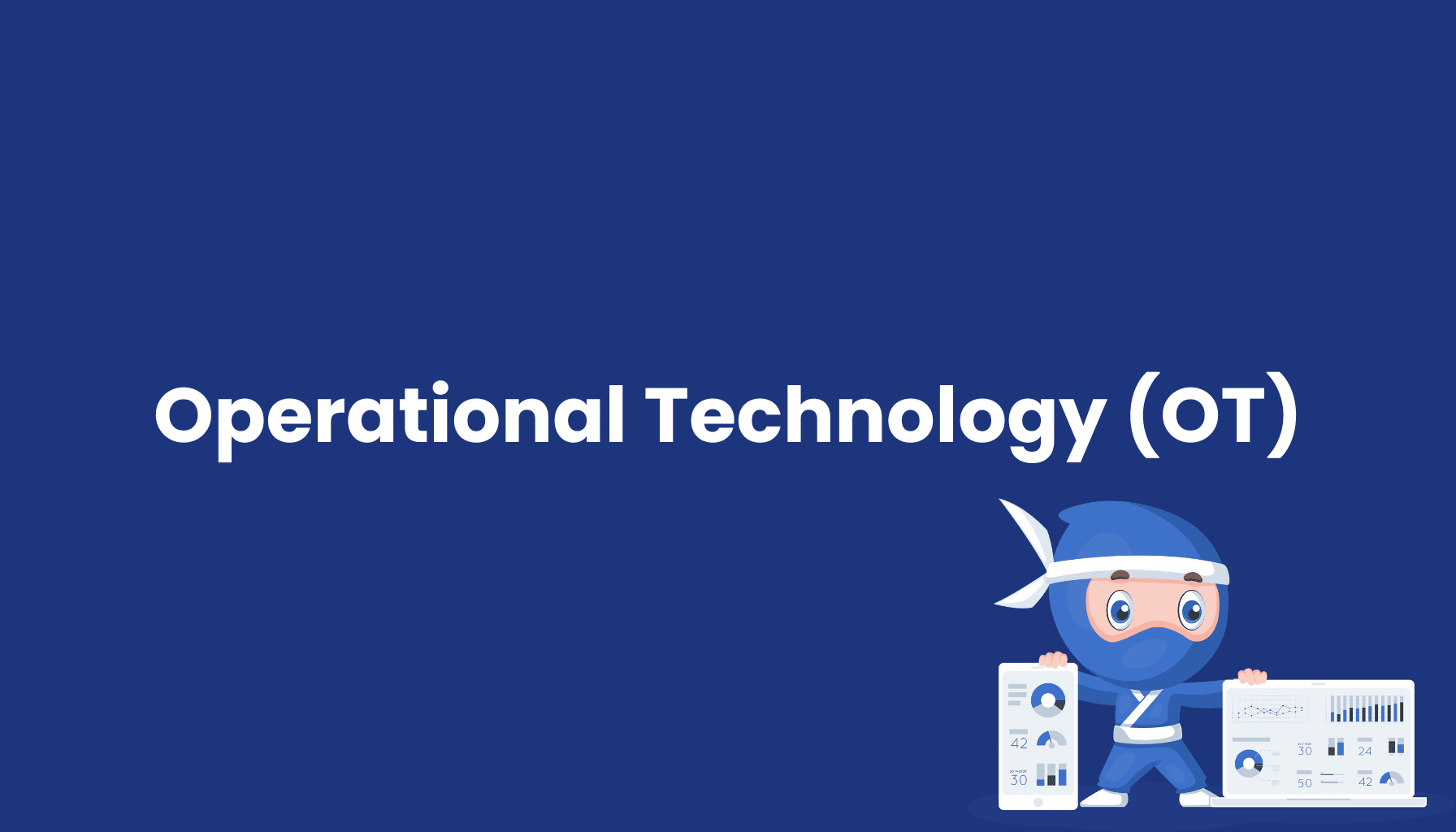
In today's modern manufacturing industry, one term is becoming increasingly important: Operational Technology (OT). But what exactly lies behind this concept, and why is the convergence of OT with traditional Information Technology (IT) so crucial for production companies' success? This article explores the fundamentals of OT, OT/IT convergence, and demonstrates how manufacturing companies can benefit from this development.
What is Operational Technology (OT)?
Operational Technology (OT) refers to hardware and software systems used to directly monitor, control, and manage physical devices, processes, and events in industrial environments. Unlike traditional IT, which primarily deals with data processing, storage, and transmission, OT focuses on interaction with the physical world.
OT systems include:
- Control systems (SCADA) for industrial process monitoring
- Programmable Logic Controllers (PLCs) for machine process automation
- Industrial Control Systems (ICS) for managing complex production facilities
- Human-Machine Interfaces (HMI) for operating equipment
- Edge computing devices for decentralized data processing
- IIoT sensors and actuators for process detection and control
Historically, OT systems in the manufacturing industry were mostly standalone, isolated solutions with proprietary protocols operating in segregated networks. The priority was high availability, stability, and operational safety – not IT security or flexible data integration.
The Differences Between IT and OT
To understand the significance of OT/IT convergence, it's worth examining the traditional differences between both worlds:
Aspect | Information Technology (IT) | Operational Technology (OT) |
---|---|---|
Primary focus | Data processing and management | Control of physical processes |
Critical requirement | Data security and integrity | Availability and operational safety |
Update cycles | Regular (days/weeks) | Rare (months/years) |
Downtime tolerance | Short outages acceptable | No outages tolerable |
Main risk | Data loss or compromise | Operational interruption, safety risks |
Lifecycle | 3-5 years | 10-20 years |
Standardization | High standardization | Historically proprietary systems |
These different priorities are also reflected in many companies' organizational structures: IT and OT departments often work independently, with their own budgets, different technical languages, and sometimes conflicting goals.
OT/IT Convergence: Why It's Inevitable
Digital transformation and Industry 4.0 make the convergence of OT and IT a strategic necessity. This merger is driven by several factors:
- Industry 4.0 and Smart Factory: The vision of the connected, intelligent factory requires seamless communication between machines, systems, and business processes.
- Industrial Internet of Things (IIoT): The increasing prevalence of networked sensors and devices in production generates valuable data that must be analyzed and utilized.
- Data-driven decision making: Companies need real-time data from production to make informed decisions and secure competitive advantages.
- Efficiency improvements: The integration of IT and OT systems enables process optimizations that would otherwise be impossible.
- Cost pressure: Standardized IT solutions often offer cost advantages over specialized OT systems.
Benefits of OT/IT Convergence for Manufacturing Companies
The successful integration of OT and IT systems offers numerous advantages:
1. Improved Operational Efficiency
By linking production and business systems, companies can optimize their processes and use resources more efficiently. MES (Manufacturing Execution Systems) play a central role here, functioning as a link between ERP systems and the production level.
2. Predictive Maintenance
Combining machine data from OT systems with advanced analytics tools from the IT world enables predictive maintenance. By early detection of potential failures, unplanned downtime can be minimized, directly increasing productivity and reducing costs.
3. Real-time Insights and Decision Making
When production data is available in real-time and combined with business data, decision-makers can respond faster and more precisely. This enables agile adaptation to market changes and customer needs.
4. Improved Quality Control
By integrating quality data from production into higher-level IT systems, quality issues can be detected and resolved earlier. This reduces waste, improves product quality, and increases customer satisfaction.
5. Greater Flexibility and Scalability
Modern OT solutions based on IT standards are easier to adapt and scale than traditional, proprietary systems. This is particularly important in times of rapid technological change and fluctuating market requirements.
Challenges in OT/IT Convergence
Despite the obvious benefits, the merger of OT and IT also brings significant challenges:
1. Cybersecurity Risks
Opening previously isolated OT systems to IT networks creates new attack vectors. Many older OT systems were not developed with cybersecurity in mind and lack basic security features such as authentication or encryption.
2. Different Requirements and Priorities
While IT systems are accustomed to regular updates and short maintenance windows, OT systems require absolute reliability and uninterrupted operation. Reconciling these conflicting requirements is a major challenge.
3. Technical Compatibility Issues
Proprietary OT protocols and interfaces make seamless integration with standardized IT systems difficult. Creating unified communication paths often requires complex middleware solutions or gateway technologies.
4. Organizational Silos
The different cultures, technical languages, and priorities of IT and OT teams can lead to communication problems and resistance. Successful convergence therefore also requires organizational changes and competency development.
5. High Investment Costs
Migrating legacy OT systems to modern, integrated solutions can require significant investments – both in technology and employee qualification.
Strategies for Successful OT/IT Convergence
To master the challenges and harness the benefits of OT/IT convergence, the following strategies are recommended:
1. Develop a Holistic Security Strategy
Develop a comprehensive security concept that considers both IT and OT-specific requirements. Implement network segmentation, access controls, and continuous monitoring to ensure the security of connected systems.
2. Promote Standardization
Rely on open standards and protocols that enable seamless integration between OT and IT systems. Industry 4.0 standards such as OPC UA offer promising approaches here.
3. Plan Gradual Migration
Pursue an evolutionary approach rather than a radical change. Start with pilot projects in less critical areas and gradually expand them based on the experience gained.
4. Use MES as a Connecting Link
Manufacturing Execution Systems (MES) can serve as a bridge between the production level and business systems. A modern, cloud-capable MES facilitates integration and provides valuable functions for production optimization.
5. Invest in Employee Qualification
Promote knowledge exchange between IT and OT teams and invest in further education to build the necessary competencies for the converged environment.
6. Utilize Edge Computing
Edge computing solutions can serve as mediators between the OT and IT worlds. They enable pre-processing of large amounts of data close to the source, reducing latency and bandwidth requirements.
The Future of OT/IT Convergence: Cloud and Artificial Intelligence
The next evolutionary stage of OT/IT convergence will be shaped by two technology trends:
Cloud-native MES Systems
Modern MES solutions are increasingly designed as cloud-native applications that offer scalability, flexibility, and location-independent access. These systems can be seamlessly integrated with other cloud services, enabling comprehensive digitalization of manufacturing.
Artificial Intelligence in Production
Combining OT data with AI technologies opens up new possibilities for process optimization, predictive maintenance, and automated quality control. Machine learning algorithms can identify patterns in production data that are invisible to humans, contributing to continuous improvements.
Conclusion: OT/IT Convergence as the Foundation for the Smart Factory
The convergence of Operational Technology and Information Technology is not a passing trend but a fundamental development that will shape the future of the manufacturing industry. Companies that successfully master this integration will benefit from greater flexibility, better efficiency, and improved competitiveness.
The key to success is a balanced approach that considers both the specific requirements of production and the possibilities of modern IT systems. Manufacturing Execution Systems play a key role in this development as mediators between both worlds.
Through OT/IT convergence, manufacturing companies lay the foundation for the smart factory of the future – a connected, intelligent, and agile production environment that enables continuous optimization and innovation.
Further Resources
- White paper: "Best Practices for OT/IT Integration in Manufacturing Environments"
- Webinar: "Cloud-native MES Systems as Enablers for the Smart Factory"
- Podcast: "Cybersecurity in Converged OT/IT Environments"
Would you like to learn more about OT/IT convergence and modern MES solutions? Contact our experts for individual consultation.