Operator Self-Inspection
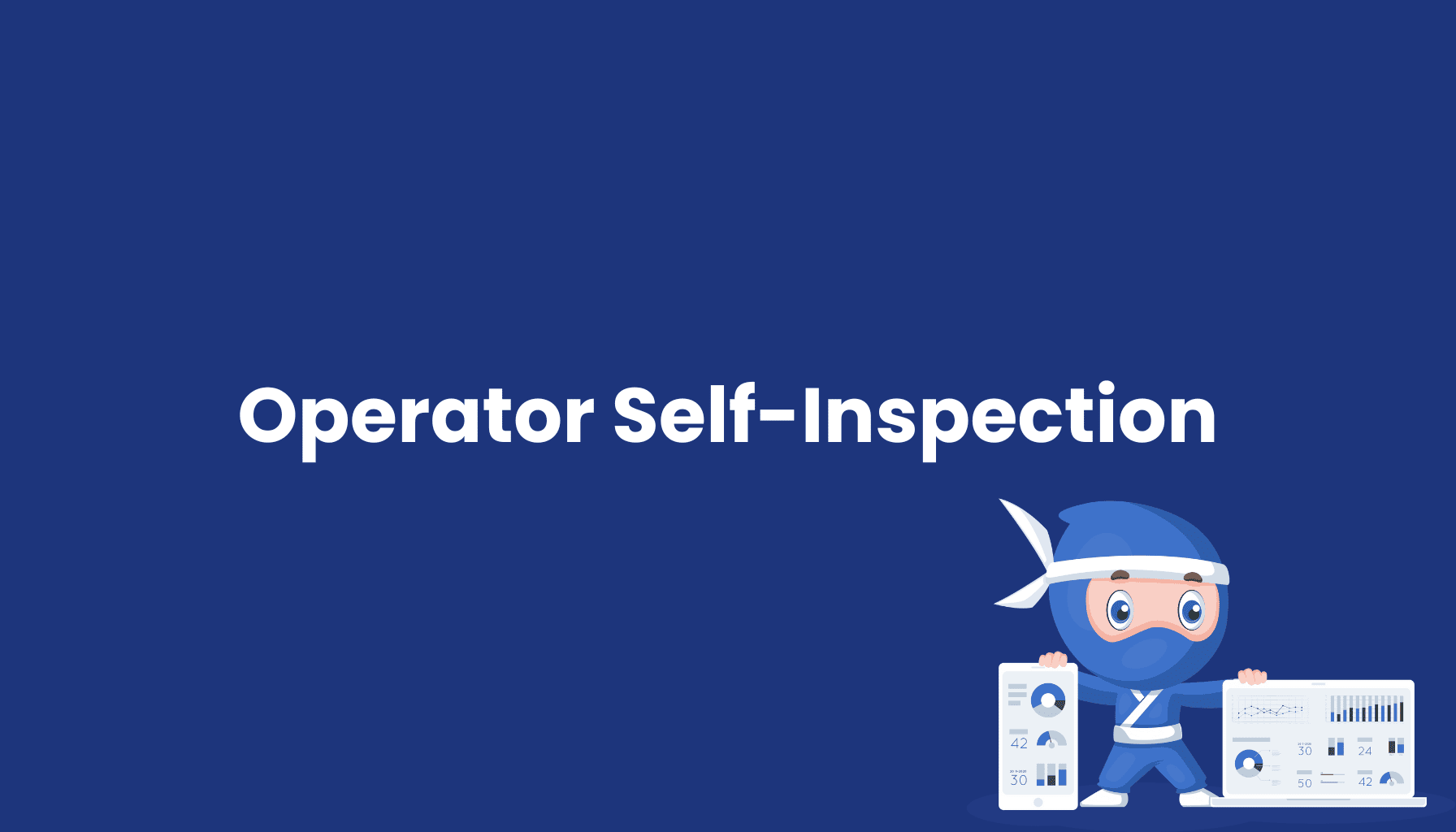
Operator self-inspection represents an efficient and cost-optimized approach to quality assurance where production employees verify the quality of their own work. This concept combines productivity with quality awareness and plays a central role in modern manufacturing environments—particularly in the context of lean manufacturing and continuous improvement processes.
What is Operator Self-Inspection?
Operator self-inspection is defined by shifting quality control directly to the point of product creation. Unlike traditional methods that employ separate quality inspectors, operator self-inspection places responsibility for quality control with the employees who manufacture the product.
Core elements of operator self-inspection:
- Self-responsible quality inspection by production employees
- Testing according to defined standards and specifications
- Immediate defect identification during the production process
- Documentation of inspection results, typically digitally in MES systems
- Immediate implementation of corrective measures when deviations occur
Operator self-inspection typically includes checking intermediate and final products against predetermined quality characteristics, performing measurements or tests, and examining machine parameters and the working environment.
Distinction from Traditional Quality Assurance Methods
Operator self-inspection differs fundamentally from traditional quality assurance approaches:
Characteristic | Traditional QA | Operator Self-Inspection |
---|---|---|
Inspection personnel | Specialized QA staff | Production employees themselves |
Timing | Downstream (end of line) | Integrated with process |
Response time | Delayed | Immediate |
Responsibility | Separate from production | Integrated into production |
Quality awareness | External control | Intrinsic motivation |
Costs | Separate QA department | Integration into production costs |
These differences make operator self-inspection particularly valuable for companies operating according to lean principles and seeking to continuously optimize their processes.
The 5 Critical Advantages
Implementing a structured operator self-inspection system offers companies numerous measurable benefits:
1. Defect Reduction and Quality Improvement
- Early defect detection directly at the source
- Reduction of defect costs by typically 30-50%
- Improvement in First Pass Yield by 10-25%
2. Productivity Increase
- Reduction of process times through integrated quality control
- Minimization of scrap and rework (typical reduction of 40-60%)
- Better equipment utilization through fewer interruptions for quality inspections
3. Employee Empowerment and Engagement
- Strengthening quality awareness throughout the workforce
- Higher job satisfaction through expanded areas of responsibility
- Improved problem-solving competence of employees
4. Cost Optimization
- Reduction of dedicated QA personnel without loss of quality
- Lowering quality costs by an average of 15-30%
- Minimization of complaint costs through higher product quality
5. Process Optimization
- Continuous improvement through direct feedback
- Faster implementation of process improvements
- Increased process stability through constant feedback
These advantages make operator self-inspection a valuable component of modern quality management strategies, particularly in the context of lean manufacturing and Industry 4.0.
Digital Support through MES Systems
Modern Manufacturing Execution Systems (MES) provide comprehensive support for operator self-inspection and elevate its efficiency to a new level:
Core Functions for Operator Self-Inspection
- Digital inspection plans with automatic inspection prompts
- Intuitive user interfaces for entering inspection results
- Automatic plausibility checks during data entry
- Real-time alerting for quality deviations
- Complete traceability of all inspection results
MES Integration
- Linkage with order and process data
- Automatic documentation of all quality-relevant activities
- Statistical Process Control (SPC) for early trend detection
- Integration with CAQ systems for comprehensive quality management
- Provision of inspection documents and visual aids
Paperless Quality Assurance
Digitizing operator self-inspection through MES systems leads to completely paperless quality assurance, which not only reduces administrative effort but also makes an important contribution to sustainability.
Key Performance Indicators and Performance Measurement
Relevant key performance indicators (KPIs) are essential for measuring the success of operator self-inspection and continuously improving it:
Quality KPIs
- First Pass Yield (FPY): Percentage of products passing all quality inspections without rework
- Defect Rate: Number of identified defects per unit
- Quality Incident Rate: Frequency of quality-related incidents
- Cost of Poor Quality (COPQ): Costs due to scrap, rework, and complaints
Process KPIs
- Inspection Coverage: Proportion of inspected characteristics relative to those required
- Inspection Efficiency: Time spent on quality inspections relative to total production time
- Response Time: Time span between defect detection and corrective action
Employee KPIs
- Training Level: Proportion of employees qualified for quality inspections
- Quality Awareness: Measurement via surveys or behavioral observations
- Improvement Suggestions: Number of quality-related optimization suggestions
Regular analysis of these KPIs enables data-based optimization of operator self-inspection and continuous improvement of quality processes.
Conclusion and Future Perspectives
Operator self-inspection has established itself as an effective approach to quality assurance in modern manufacturing environments. By integrating quality control into the production process and transferring responsibility to employees, costs are reduced and quality improved, while also increasing workforce engagement and satisfaction.
With the progressive digitalization of manufacturing within Industry 4.0, further optimization potential emerges for operator self-inspection:
- Assistance systems such as augmented reality to support complex inspections
- Automated inspection technologies like computer vision to complement manual inspections
- AI-based anomaly detection for early identification of quality issues
- Predictive Quality for anticipatory quality assurance
Companies that strategically implement operator self-inspection and continuously develop it create a sustainable competitive advantage through higher quality, lower costs, and more flexible processes.