Optimization Potentials in Manufacturing
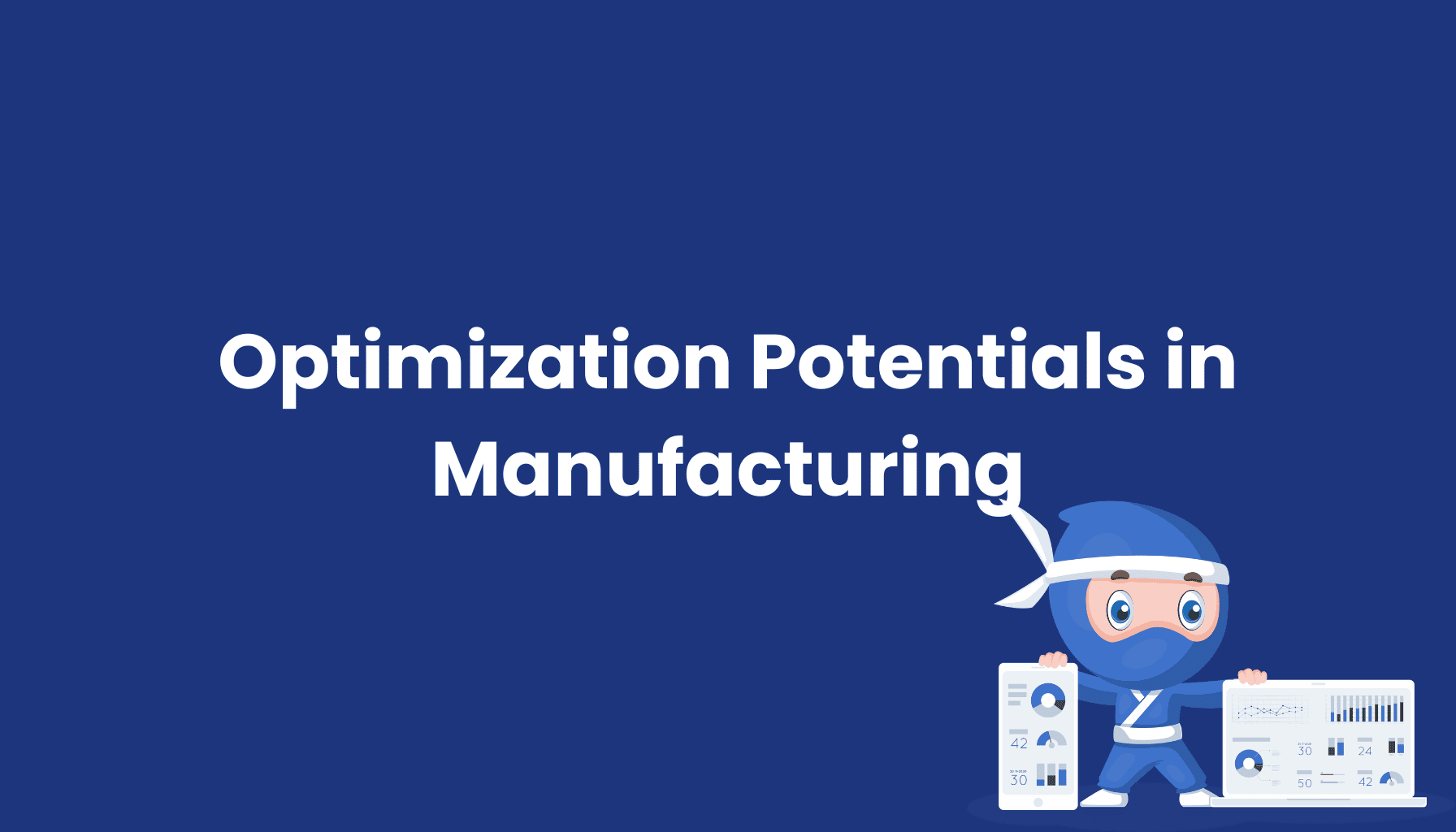
What Are Optimization Potentials in Manufacturing?
The systematic analysis and exploitation of optimization potentials represent a central success factor for manufacturing companies. A structured evaluation methodology enables the precise identification and effective implementation of improvement measures in the production environment.
Methodical Potential Analysis
Quantitative identification of optimization opportunities requires a multidimensional analysis system:
- Performance Measurement using standardized KPI systems
- Benchmark Analysis against best-in-class standards
- Integration of Data Analytics for pattern recognition
- Continuous Monitoring of critical process parameters
Process Efficiency Evaluation
Structured assessment of process efficiency focuses on specific performance dimensions:
- Cycle Time Analysis quantifies process speeds
- Capacity Utilization evaluates resource efficiency
- Throughput Time Analysis identifies process delays
- Quality Performance assesses process stability
Technological Optimization
The systematic evaluation of technological improvement potentials includes:
- Automation Level Assessment to identify modernization needs
- Digitalization Potential Analysis for evaluating transformation options
- System Integration Assessment to enhance connectivity
- Equipment Effectiveness Monitoring to quantify asset performance
Resource Efficiency
Methodical optimization of resource utilization integrates:
- Energy Efficiency Analysis using standardized measurement methods
- Material Utilization Studies to evaluate material flow efficiency
- Labor Productivity Analysis to optimize workforce resources
- Space Utilization Analysis to identify layout improvements
Implementation Framework
The structured realization of identified potentials relies on:
- Systematic Prioritization based on ROI criteria
- Standardized Project Management Methodology
- Defined Change Management Processes
- Continuous Performance Monitoring
Digital Transformation
The integration of digital optimization technologies involves:
- Predictive Analytics for process optimization
- Machine Learning for pattern recognition
- Digital Twin Technology for simulation analyses
- Industrial IoT for process monitoring
Continuous Improvement System
Sustainable optimization requires systematic improvement processes:
- Standardized PDCA Cycles
- Structured Idea Management
- Knowledge Management System
- Best Practice Sharing Platforms