Performance Analysis
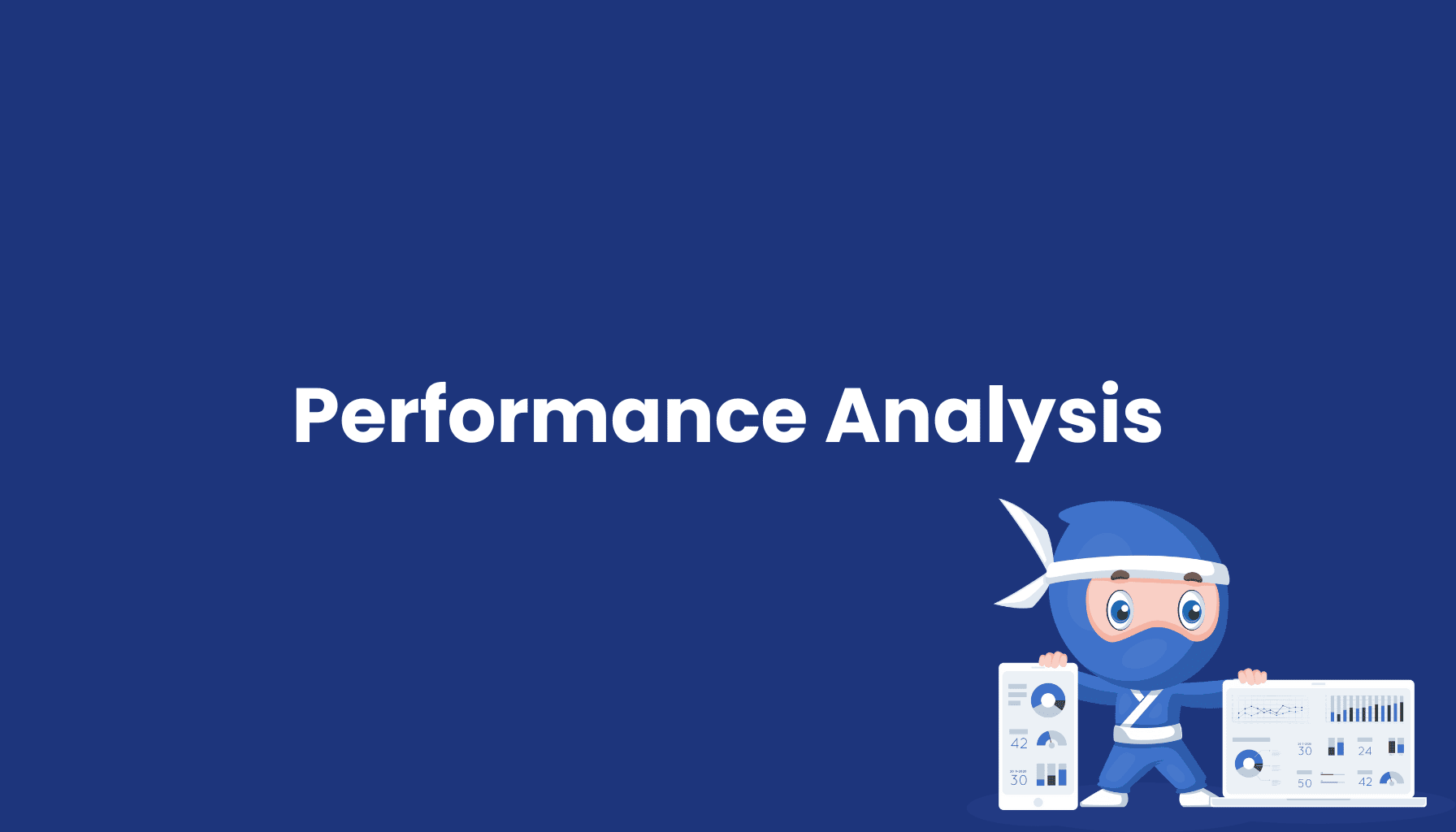
The structured analysis of manufacturing performance requires a comprehensive framework for quantitative evaluation of all production parameters. A methodical evaluation approach enables precise identification of optimization potentials and targeted implementation of improvement measures.
Fundamental Performance Metrics
The systematic capture of essential performance indicators based on defined measurements:
- Production system throughput rate with real-time monitoring capabilities
- Equipment availability and utilization rates tracking operational efficiency
- Process stability and quality quotients measuring manufacturing consistency
- Resource efficiency and capacity utilization optimizing asset performance
- Productivity indicators per manufacturing unit enabling detailed analysis
Quantitative Analysis Methodology
Implementation of standardized analysis procedures:
- OEE calculation following industry standards and best practices
- Statistical Process Control (SPC) enabling variance reduction
- Capacity utilization analysis optimizing resource allocation
- Cycle time analysis identifying process bottlenecks
- Cost factor analysis determining efficiency impacts
Performance Monitoring System
Integration of systematic surveillance mechanisms:
- Real-time data acquisition providing immediate insights
- Automated KPI calculation ensuring consistent measurement
- Trend analysis and forecasting functions enabling proactive management
- Deviation analysis with alert functions detecting anomalies
- Visualization through management dashboards enabling informed decision-making
Quality Performance Analysis
Methodical evaluation of quality performance through:
- First Pass Yield monitoring tracking initial production success
- Process Capability Studies assessing manufacturing consistency
- Defect Rate Analysis identifying quality improvement opportunities
- Root Cause Investigation enabling systematic problem solving
- Corrective Action Tracking ensuring continuous improvement
Optimization Potential Analysis
Structured identification of improvement opportunities:
- Systematic weakness analysis revealing enhancement areas
- Benchmarking against industry standards establishing targets
- Value Stream Analysis identifying process optimization potential
- Resource efficiency analysis maximizing asset utilization
- Process optimization potential assessment driving continuous improvement