Production Control
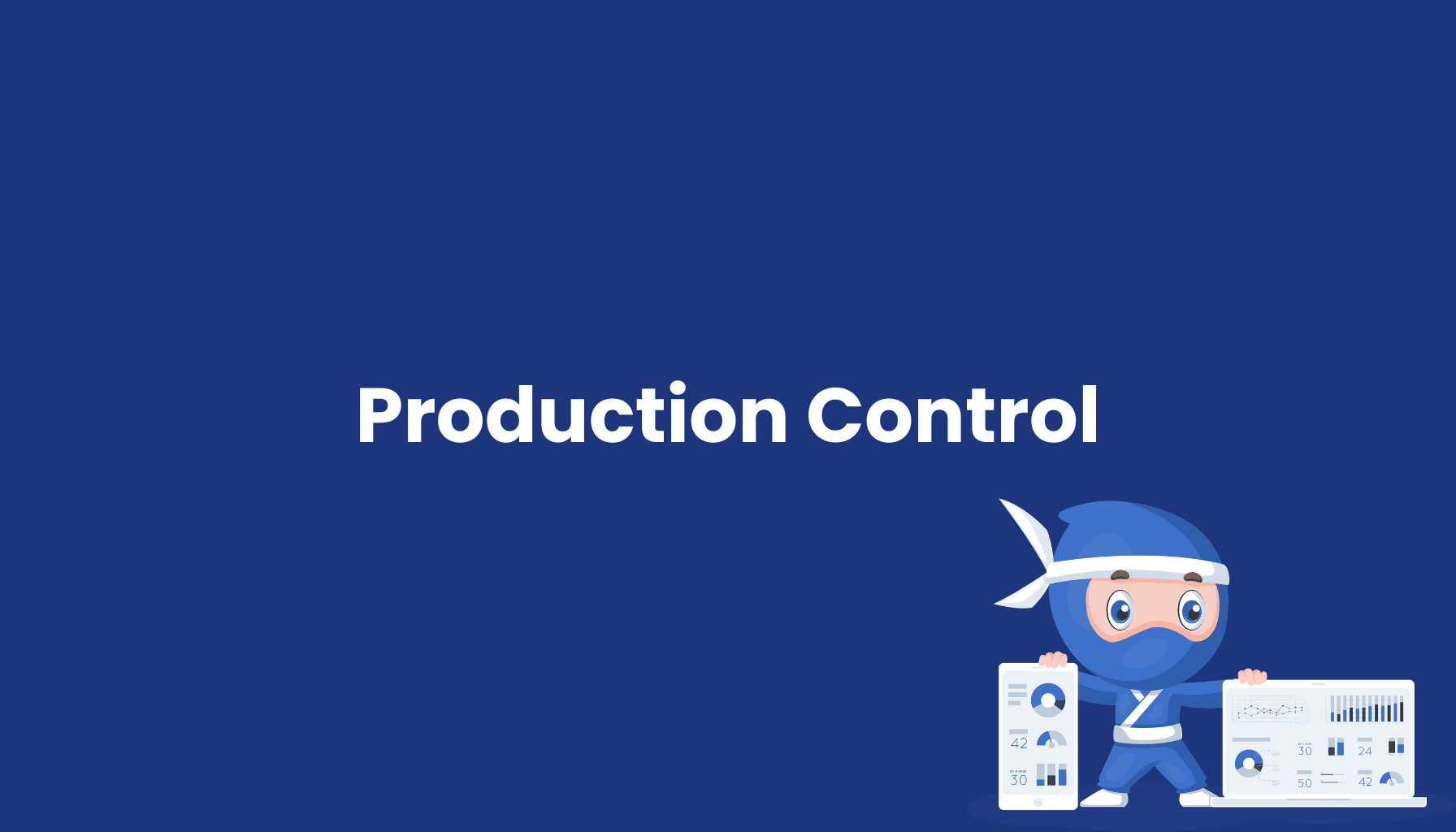
What is Production Control?
Production control encompasses all processes and measures aimed at efficiently organizing and monitoring a company's manufacturing operations. It ensures that production processes run smoothly and that all manufacturing orders are optimally executed to meet customer demands and quality standards. Closely linked to production planning, production control works to align manufacturing activities with market demand.
Functions and Objectives of Production Control
The primary responsibilities of production control involve planning, optimizing, monitoring, and managing production workflows. These responsibilities are designed to achieve several key objectives:
1. Increasing Efficiency:
Production processes are structured to maximize the utilization of resources such as machinery, materials, and labor. This minimizes production costs while boosting productivity.
2. Enhancing Flexibility:
Effective production control enables rapid responses to changes in demand or unexpected events, such as machine breakdowns or supply chain disruptions.
3. Ensuring Quality Standards:
Maintaining high-quality standards is a core objective of production control. Through continuous monitoring and control, errors are minimized, and product quality is guaranteed.
4. Meeting Delivery Deadlines:
Timely completion of orders is crucial to meeting customer expectations. Production control ensures adherence to delivery schedules by optimizing production timelines.
Key Components of Production Control
1. Production Planning and Control (PPC):
PPC systems assist in coordinating and optimizing production workflows. These systems enable the efficient management of manufacturing orders, machine capacities, and material flow.
2. ERP Systems:
Enterprise Resource Planning (ERP) systems integrate various departments within an organization, providing centralized data. Production control leverages these systems for real-time decision-making and process alignment.
3. Push and Pull Methods:
- Push Systems: Production is initiated based on forecasts and preplanned quantities.
- Pull Systems: Production is driven by actual demand, starting only when a specific need arises.
Each approach has unique advantages and is applied based on company requirements.
4. Scheduling and Sequencing:
This involves the temporal arrangement of production steps to optimize workflow. Proper scheduling reduces downtime and improves overall efficiency.
The Role of Production Control in Industry 4.0
With the advent of Industry 4.0, production control has undergone significant transformation. Digital tools such as the Internet of Things (IoT), Artificial Intelligence (AI), and Big Data provide unprecedented capabilities for real-time monitoring and optimization of production processes.
Example of Industry 4.0 in Production Control:
IoT sensors embedded in machines allow continuous monitoring of equipment utilization and condition. The collected data enables predictive maintenance, helping avoid unplanned downtime and ensuring seamless production flow.
Digital Twin Technology:
Digital twins—virtual representations of physical production systems—enable real-time simulation and optimization. This allows companies to anticipate potential issues and improve process efficiency.
Methods of Production Control
1. Just-in-Time (JIT):
JIT ensures materials and products are delivered only when needed, minimizing inventory levels and reducing costs. This method enhances efficiency and aligns production with demand.
2. Kanban:
A visual control system that regulates material flow within production. By identifying bottlenecks early, Kanban facilitates a flexible and efficient production environment.
3. Total Productive Maintenance (TPM):
Focused on proactive and preventive maintenance, TPM minimizes machine downtime, ensuring consistent production quality and efficiency.
Challenges in Production Control
Production control faces several challenges, especially in complex manufacturing environments:
1. Resource Constraints:
Material shortages or a lack of skilled personnel can significantly hinder production planning and execution.
2. Unforeseen Disruptions:
Machine breakdowns or supply delays require agile adjustments to minimize the impact on production schedules.
3. Ensuring Quality:
Maintaining consistent product quality requires rigorous and continuous monitoring of production processes.
Benefits of Effective Production Control
-
Cost Reduction:
Optimal resource utilization lowers operational costs by reducing waste and inefficiencies. -
Improved Productivity:
Streamlined workflows enable faster production, boosting output and overall productivity. -
Customer Satisfaction:
Reliable delivery timelines and high-quality products enhance customer trust and loyalty. -
Adaptability:
Companies can quickly respond to changing market demands or disruptions, maintaining their competitive edge.
Conclusion
Production control is a cornerstone of manufacturing success, ensuring efficient, flexible, and high-quality operations. As a vital link between planning and execution, production control enables seamless workflows and customer satisfaction through on-time delivery and adherence to quality standards.
With Industry 4.0 driving digital transformation, production control has become smarter and more agile. Technologies such as IoT, AI, and Big Data empower companies to monitor and optimize processes in real-time, enhancing productivity and adaptability. Methods like Just-in-Time, Kanban, and TPM further contribute to continuous improvement, allowing organizations to thrive in competitive and dynamic markets.
Investing in robust production control strategies ensures long-term success by aligning operations with business goals and market demands.