Production Control System
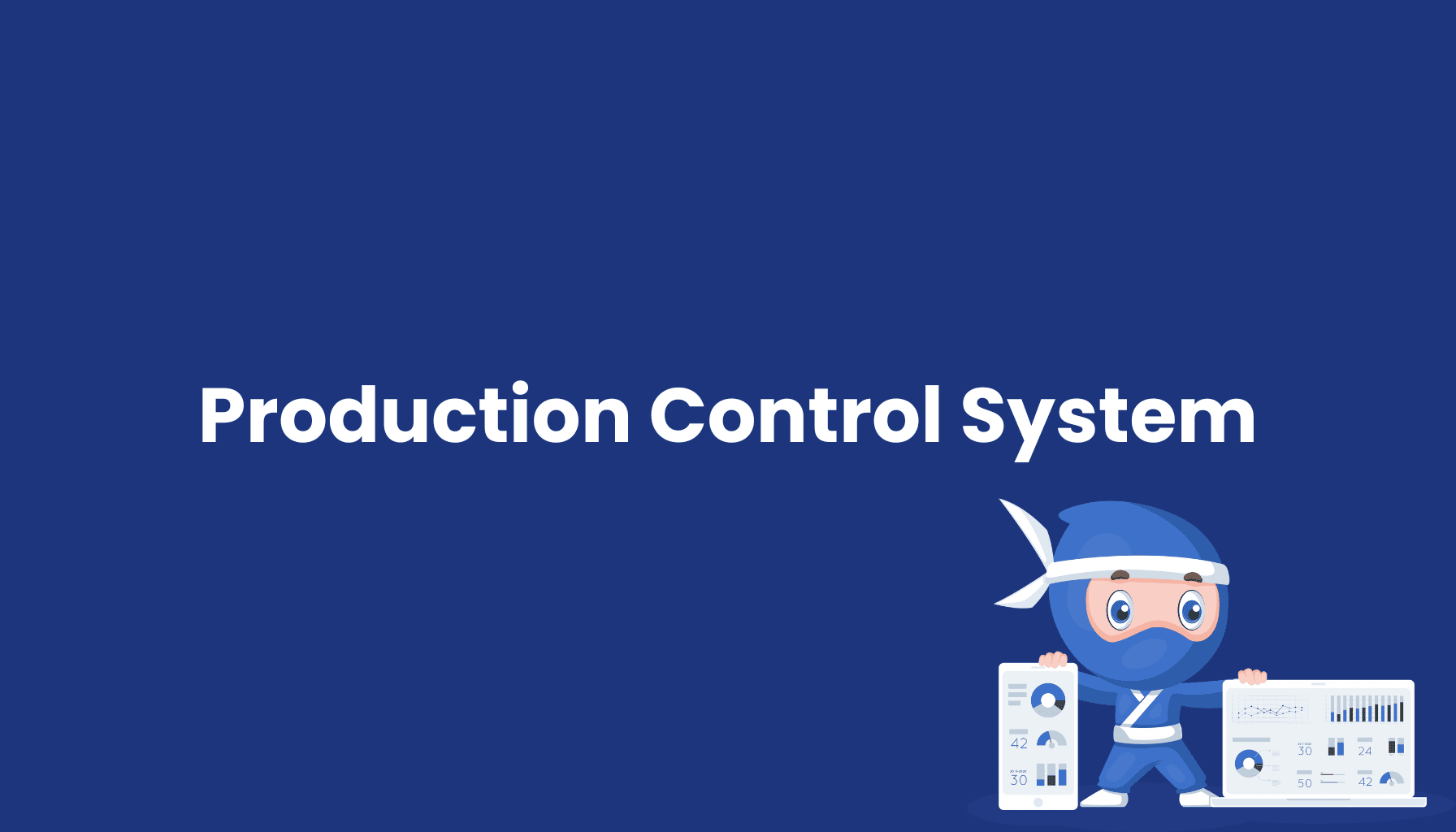
What Is a Production Control System (PCS)?
A Production Control System (PCS) is a centralized platform that enables real-time monitoring, management, and optimization of manufacturing processes. Acting as a bridge between the shop floor and higher-level business systems, PCS focuses on improving efficiency, reducing costs, and ensuring seamless coordination of production activities.
Core Functions of a Production Control System
Real-Time Monitoring
PCS continuously tracks and provides visibility into key production metrics, such as:
- Machine status
- Output quantities
- Quality parameters
- Material consumption
- Energy usage
Advanced Scheduling and Planning
It supports dynamic scheduling and resource allocation by managing:
- Production orders
- Material flow
- Workforce scheduling
- Equipment maintenance planning
Integrated Quality Management
The system ensures consistent quality with features like:
- Real-time quality monitoring
- Inspection plan management
- Error tracking and analysis
- Automated corrective actions
- Documentation and compliance tracking
Benefits of a Production Control System
Efficiency Gains
- Improved productivity
- Reduced cycle times
- Optimized resource utilization
- Faster response to production issues
Cost Reduction
- Minimized scrap and rework
- Lower downtime
- Efficient inventory and workforce management
Transparency and Decision-Making
- Real-time data for informed decisions
- End-to-end traceability of production processes
- Comprehensive performance insights
Technology and Integration
Modern Technologies in PCS
- IoT Integration: Sensors and devices collect real-time data from machines and processes.
- Cloud Connectivity: Enables scalability, global accessibility, and reduced IT costs.
- Artificial Intelligence: Supports predictive maintenance, quality forecasts, and anomaly detection.
- Mobile Access: Offers remote monitoring and management via smartphones or tablets.
System Integration
PCS seamlessly connects with:
- Enterprise Resource Planning (ERP) systems for demand planning and resource allocation.
- Warehouse Management Systems (WMS) for inventory control.
- Quality Management Systems (QMS) for compliance and reporting.
- Maintenance Systems for predictive and preventive maintenance schedules.
Implementation of a Production Control System
Steps for Successful Implementation
- Conduct a needs assessment to identify production challenges.
- Define key performance indicators (KPIs) and project goals.
- Launch a pilot project to validate the system’s functionality.
- Train employees on system usage and data interpretation.
- Gradually scale the system across production lines.
Best Practices
- Set clear priorities for integration.
- Ensure seamless communication between teams and systems.
- Monitor and optimize system performance continuously.
Future Trends in Production Control Systems
- AI-Driven Optimization: Automating decision-making with real-time insights.
- Digital Twins: Virtual replicas of production environments to simulate and test changes.
- Predictive Analytics: Proactively addressing issues before they impact operations.
- Edge Computing: Processing data closer to the source for faster response times.
Conclusion: The Role of PCS in Modern Manufacturing
A Production Control System (PCS) is more than just a tool for managing manufacturing operations—it’s a key enabler of smart, efficient, and adaptive production environments. By integrating real-time monitoring, advanced planning, and quality management, PCS empowers businesses to achieve higher productivity, reduce costs, and respond flexibly to market demands. As a cornerstone of Industry 4.0, PCS ensures that manufacturers remain competitive and prepared for the challenges of tomorrow.