Production Defect
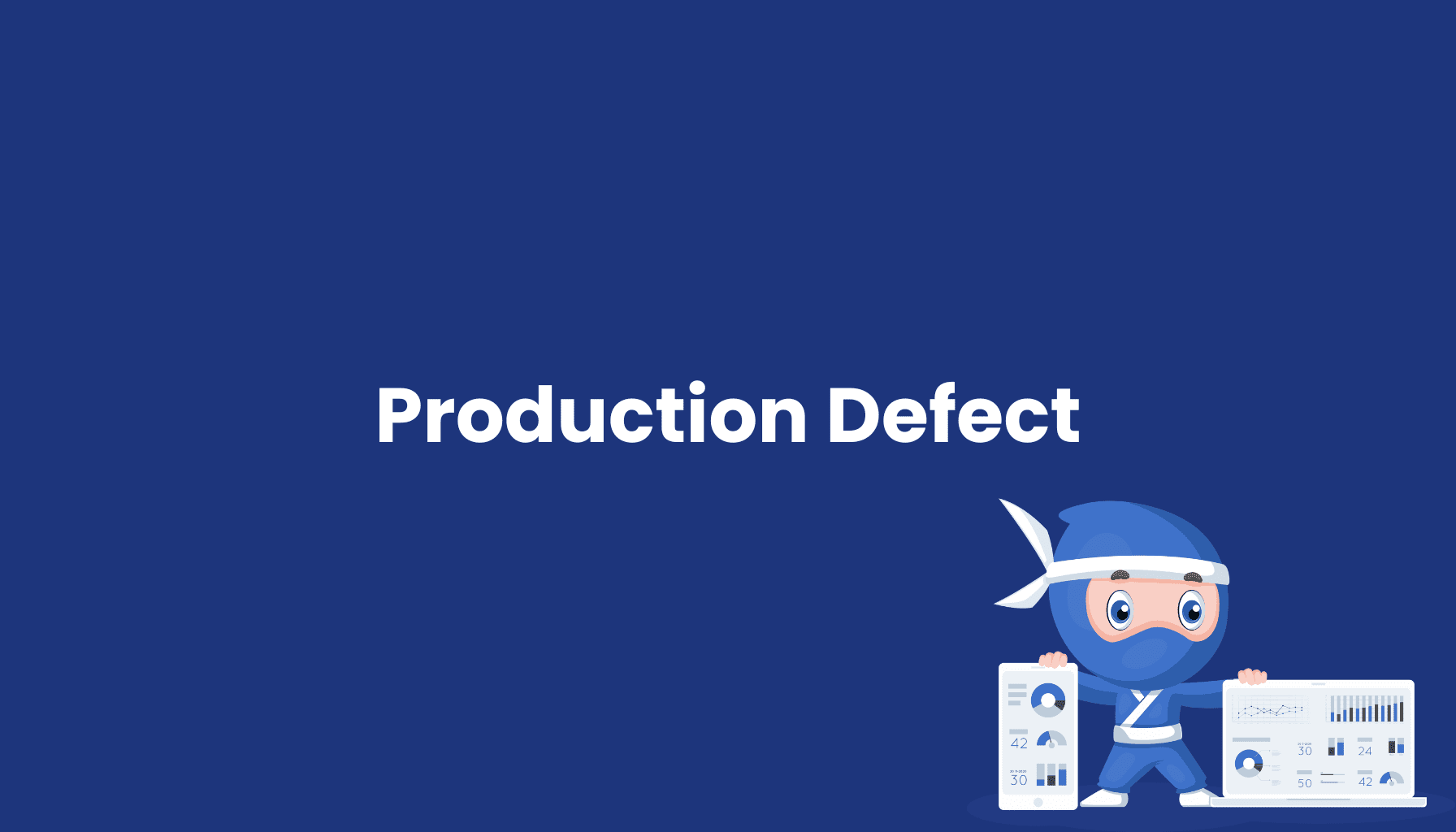
What is a Production Defect?
A production defect refers to any deviation or irregularity in the manufacturing process that causes a product to fail to meet the specified quality standards. These defects can manifest in various forms, ranging from visible flaws in the final product to functional issues that may not be detected until after the product has been delivered to the customer. Production defects can have significant impacts on product quality, customer satisfaction, and ultimately, a company's competitiveness.
Types of Production Defects
-
Material Defects:
- These occur when the raw materials or components used in production do not meet the required specifications. Material defects can arise from poor-quality supplies, improper storage, or faulty deliveries.
-
Processing Defects:
- These defects emerge during the manufacturing process itself, often due to incorrect machine settings, inadequate process monitoring, or human error. Processing defects can result in incorrect dimensions, incomplete assembly, or other inconsistencies.
-
Design Defects:
- Design flaws occur when a product is not properly engineered to function as intended or to withstand normal usage. These defects often stem from insufficient testing or incomplete design specifications.
-
Assembly Defects:
- Errors during the final assembly of components can lead to issues such as improper fitting of parts or the use of incorrect components, which can compromise the product's functionality.
Causes of Production Defects
Production defects can be caused by various factors, including:
- Inadequate Quality Control: Ineffective monitoring and inspection systems may allow defects to go unnoticed.
- Insufficient Employee Training: Workers who are not properly trained in the techniques and procedures used in production are more likely to make errors.
- Machine and Maintenance Issues: Machines that are poorly maintained or incorrectly calibrated can produce defective products.
Impacts of Production Defects
Production defects can have significant negative consequences, including:
- Customer Satisfaction: Defective products can lead to customer dissatisfaction, damaging trust in the brand and the company.
- Costs: Fixing production defects can be costly, especially if product recalls are necessary.
- Legal Consequences: Severe production defects can lead to liability claims, which can be both financially damaging and harmful to the company's reputation.
Prevention and Control of Production Defects
To minimize production defects, companies employ various strategies, including:
- Statistical Process Control (SPC): By using data analysis and monitoring tools, companies can detect and correct deviations in the production process early.
- Automated Inspections: The use of Artificial Intelligence (AI) and Machine Learning enables more precise detection of defects in real-time.
- Regular Maintenance and Calibration: Consistent maintenance and calibration of machines reduce the likelihood of machine-related defects.
Conclusion: Avoiding Production Defects
Avoiding production defects is crucial for ensuring product quality and the success of a company. With the right prevention strategies, effective quality control, and the use of modern technologies, companies can significantly reduce the risks of production defects while enhancing their efficiency and competitiveness.