Production Process Optimization
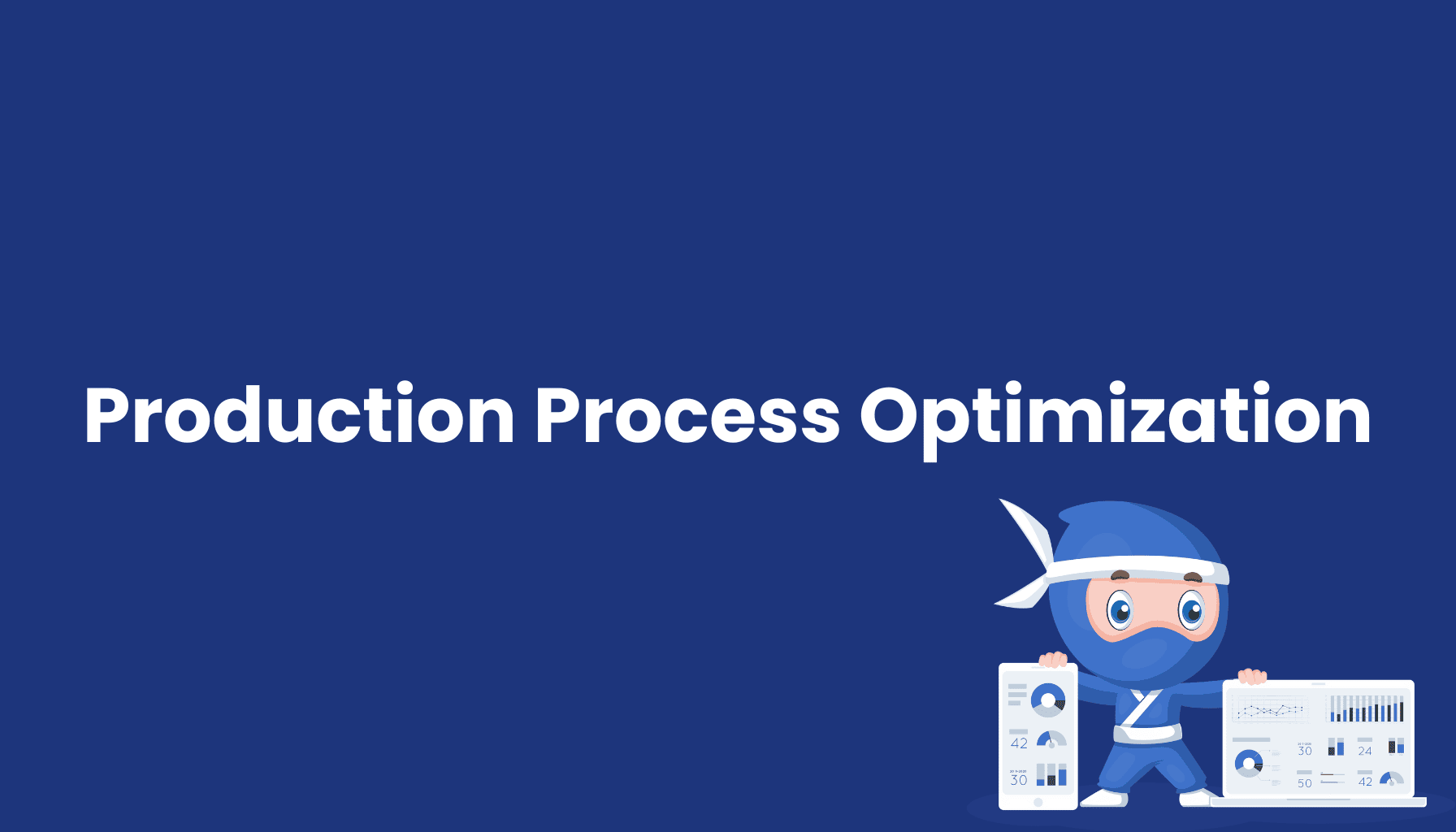
The methodical optimization of production processes represents a fundamental lever for enhancing manufacturing efficiency. A structured analysis and continuous improvement of all process parameters enables sustainable productivity enhancement through systematic implementation of proven methodologies.
Analysis Methodology
Systematic process evaluation through comprehensive tools:
- Value Stream Mapping identifying waste and optimization potential
- Process chain analysis evaluating operational sequences
- Cycle time measurement quantifying production flows
- Bottleneck identification locating constraints
- Loss source analysis determining inefficiencies
Optimization Strategies
Methodical improvement approaches leveraging proven frameworks:
- Lean Manufacturing principles eliminating non-value activities
- Six Sigma methodology reducing process variation
- Single-Minute Exchange of Die (SMED) minimizing changeover times
- Total Productive Maintenance (TPM) ensuring equipment reliability
- Quality optimization enhancing product consistency
Performance Monitoring
Continuous performance surveillance through metrics:
- Overall Equipment Effectiveness (OEE) tracking system efficiency
- Process capability analysis ensuring statistical control
- Key Performance Indicator (KPI) monitoring measuring success
- Quality metrics ensuring product standards
- Efficiency measurements optimizing resource utilization
Process Stabilization
Systematic stabilization through structured implementation:
- Standardized work procedures ensuring consistency
- Preventive maintenance reducing equipment failures
- Quality assurance maintaining product standards
- Process control maintaining operational stability
- Error prevention minimizing defects
Implementation Framework
Strategic deployment methodology:
- Current state analysis establishing baseline
- Target state definition setting objectives
- Implementation planning coordinating activities
- Performance measurement tracking progress
- Continuous improvement driving enhancement
Operational Benefits
Process optimization advantages:
- Enhanced production efficiency through waste reduction
- Improved product quality through process control
- Reduced operational costs through optimization
- Increased manufacturing flexibility through standardization
- Greater workforce productivity through engagement
This comprehensive framework enables manufacturers to systematically improve their production processes through data-driven analysis and structured implementation of proven optimization methodologies.