Quality control
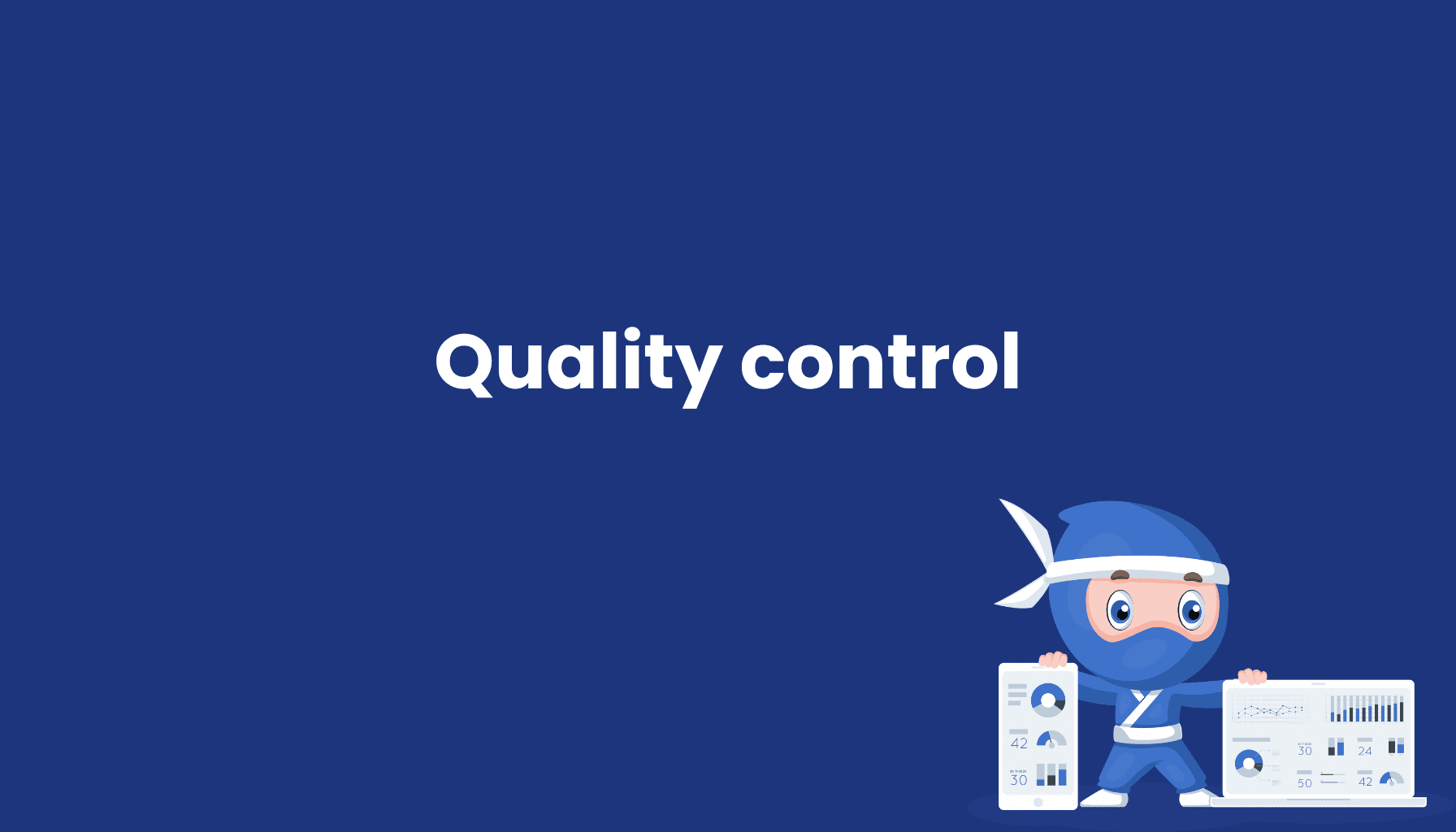
What is Quality Control?
Quality control (QC) is a critical aspect of quality management that involves a set of procedures and processes designed to ensure that products and services meet established quality standards and requirements. By definition, quality control involves the monitoring and inspection of every stage of production to guarantee that the product meets the required quality criteria. The process of quality control is essential in maintaining the consistency and reliability of the production process.
Key Aspects of Quality Control
-
Inspections and Testing
Regular inspections and testing are fundamental to quality control. These procedures involve examining products and services to ensure they meet the set quality requirements. Such inspections are particularly vital in manufacturing, where maintaining consistent quality across products is crucial. Quality control helps identify defects and ensures that only products that meet the necessary standards reach the customer. -
Statistical Process Control (SPC)
Statistical Process Control (SPC) is a method used to optimize the quality control process through the application of measurements and data analysis. By continuously monitoring the manufacturing processes, SPC ensures that all products adhere to the defined quality standards. This method significantly reduces defects and deviations, enhancing overall product quality. -
Documentation and Traceability
Proper documentation is crucial for making the results of quality control transparent and traceable. Traceability allows every step in the quality control process to be documented, making it easier to identify and correct any deviations. This aspect is a core component of quality management systems, which are designed to maintain high quality and efficiency in manufacturing. -
Employee Involvement
Employees play a vital role in quality control. Well-trained employees can detect quality issues early and take appropriate actions. The experience and dedication of the team are therefore critical for successful quality control.
Benefits of Quality Control
Customer Satisfaction: Consistently meeting quality requirements leads to higher customer satisfaction. Satisfied customers are more likely to remain loyal and contribute to a positive brand reputation.
Cost Reduction: Effective quality control minimizes the need for rework, thus lowering production costs. This leads to more efficient production and higher profitability.
Improved Product Quality: Continuous monitoring and inspection enhance the quality of the products. This results in fewer defects and increased customer satisfaction.
Connection Between Quality Control and Overall Equipment Effectiveness (OEE)
Effective quality control has a direct impact on Overall Equipment Effectiveness (OEE). By ensuring that products meet the required quality standards and minimizing defects, quality control contributes to higher OEE. This is because fewer defects mean less rework and downtime, leading to more efficient use of production time and resources.
Conclusion
Quality control is vital for ensuring that products and services meet the necessary quality standards and for achieving high customer satisfaction. By implementing effective quality control procedures, companies can not only reduce defects but also optimize their processes and lower costs. The strong link between quality control and OEE highlights the importance of robust quality assurance in driving efficiency and success in any business.