Resource Allocation
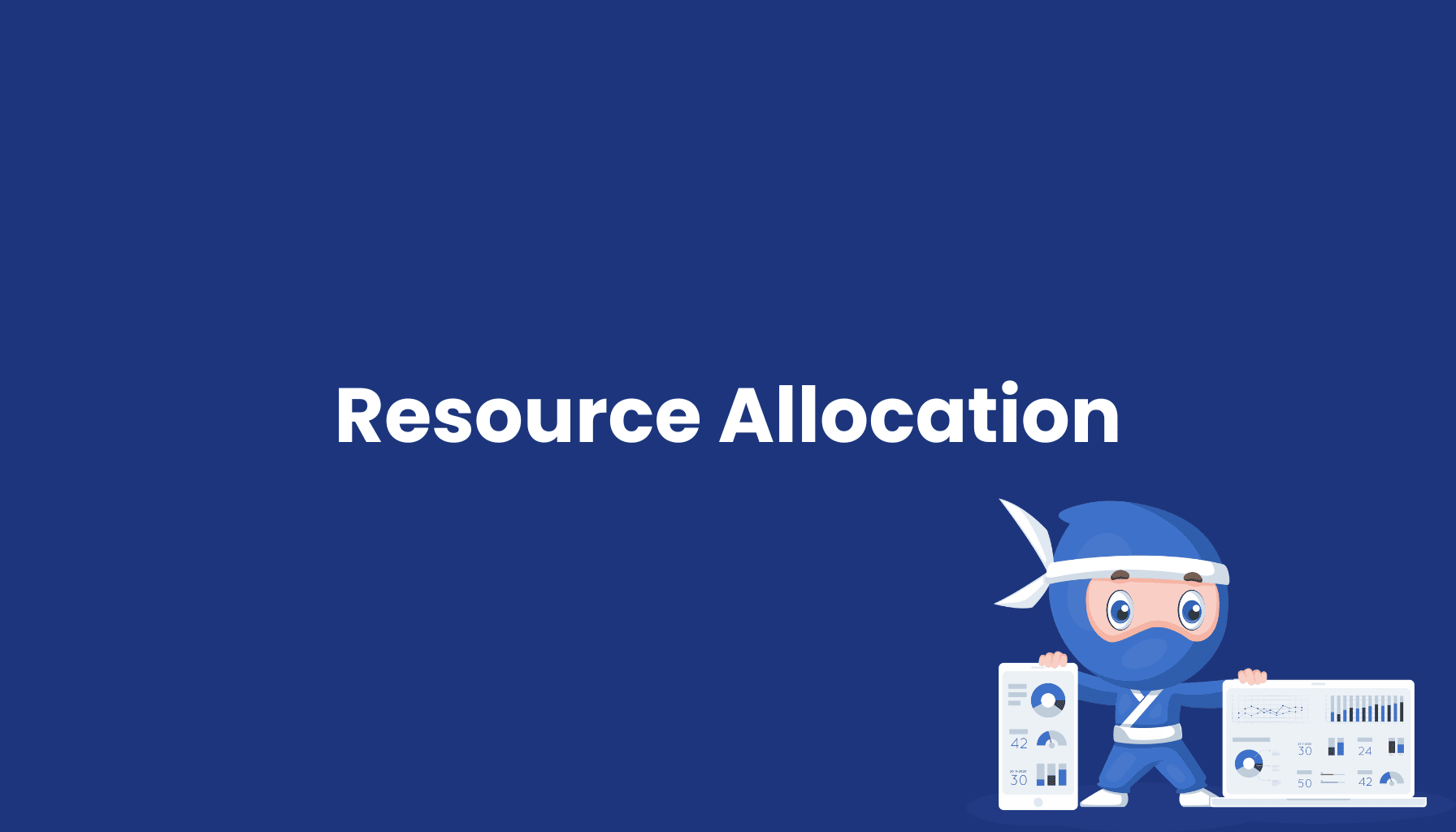
What Is Resource Allocation?
Resource allocation refers to the strategic distribution and planning of personnel, machinery, materials, and time in manufacturing. As a core aspect of modern production management, it ensures the optimal use of all available resources and significantly contributes to improving efficiency. Advanced technologies, such as Manufacturing Execution Systems (MES), enhance this process through intelligent algorithms and real-time data.
Importance in Modern Manufacturing
Efficient resource allocation is critical for:
- Optimal machine utilization
- Effective workforce deployment
- Minimized lead times
- Reduced production costs
Core Elements of Resource Allocation
Workforce Planning
- Skill-based task assignment
- Shift scheduling
- Balancing capacity utilization
- Leave and absence management
Machine Utilization
- Optimized order sequencing
- Reduction of setup times
- Integration of maintenance schedules
- Capacity planning
Material Flow Management
- Just-in-Time provisioning
- Inventory optimization
- Minimization of transport paths
- Buffer management
Benefits of Optimized Resource Allocation
Cost Savings
- 15–25% reduction in personnel costs
- 20–30% reduction in machine costs
- 30–40% reduction in material costs
- 25–35% reduction in inventory costs
Productivity Gains
- Increased machine utilization
- Shorter lead times
- Reduced setup times
- Optimized stock levels
Quality Improvements
- Fewer errors
- Lower scrap rates
- Improved schedule adherence
- Higher customer satisfaction
Technological Support for Resource Allocation
Manufacturing Execution Systems (MES)
MES systems offer advanced functionalities for resource allocation, including:
- Real-time monitoring
- Automated planning
- Capacity balancing
- Performance analysis
AI and Machine Learning
- Predictive planning
- Automatic adjustments
- Pattern recognition
- Simulation-based optimizations
Mobile Solutions
- Flexible control via smartphones and tablets
- Digital boards for quick adjustments
- Push notifications for real-time updates
Best Practices for Implementation
Analysis and Planning
- Assess the current state (as-is analysis)
- Identify bottlenecks and weaknesses
- Define objectives and KPIs
Implementation
- Integrate systems
- Digitize processes
- Train teams
- Continuously optimize operations
Challenges and Solutions
Complexity Management
- Dynamic adjustments to changing demands
- Building flexibility reserves
- Clear prioritization strategies
Data Quality
- Real-time data collection
- Plausibility checks
- Regular validation of standards
Future Trends in Resource Allocation
- AI-driven optimization
- Digital twins for resource simulation
- Predictive resource planning
- Autonomous systems for adaptive manufacturing
Conclusion
Efficient resource allocation is key to competitive production. Modern MES systems and digital technologies provide unparalleled precision and flexibility, enabling businesses to maximize efficiency and adapt to dynamic market conditions. Companies that invest in advanced resource allocation tools secure a significant edge in the global market.