Shopfloor Management
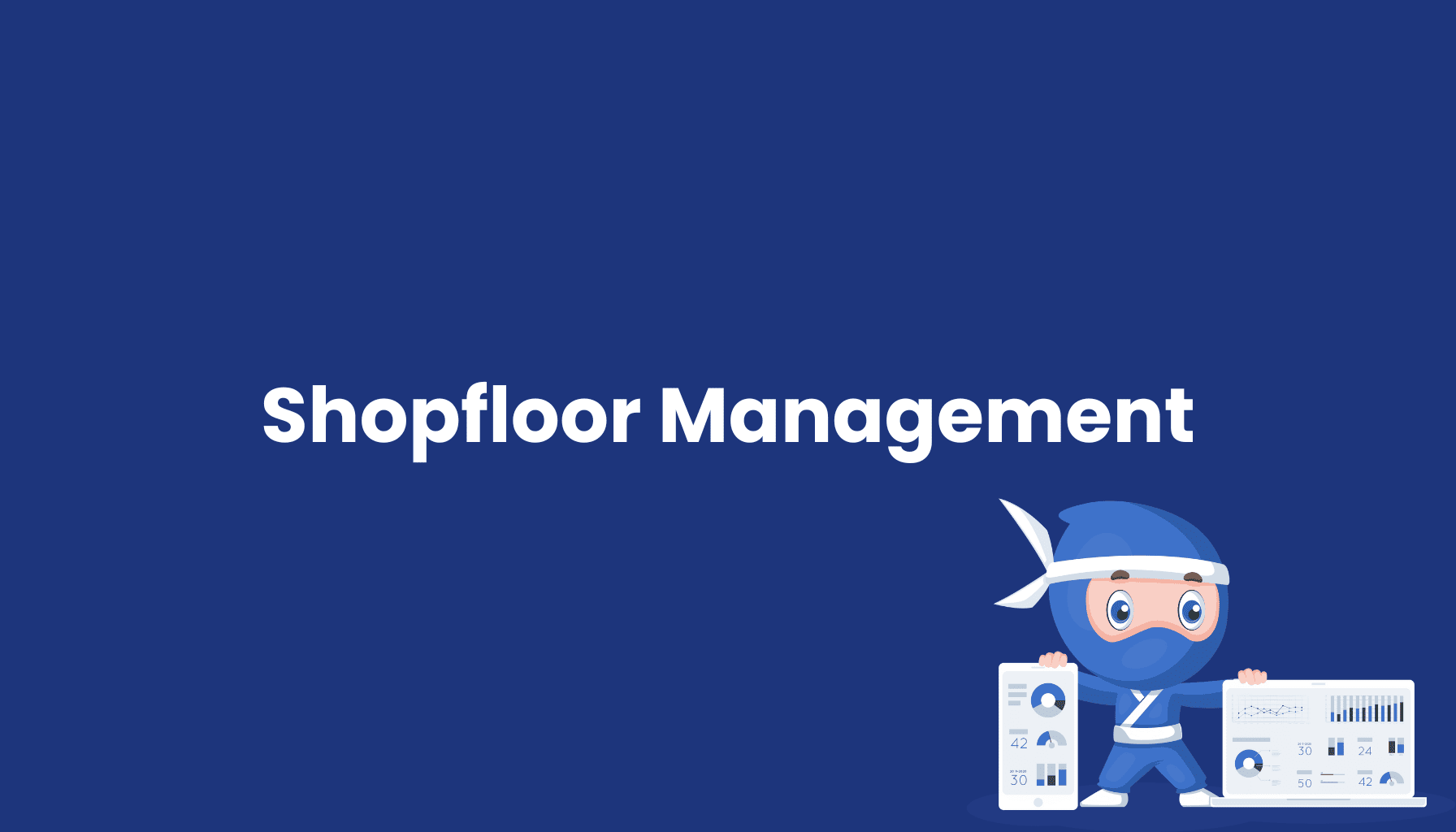
What is Shopfloor Management?
Shopfloor Management is an operational management method focused on the direct monitoring, supervision, and optimization of production processes on the factory floor. This approach uses tools and methods to oversee workflows in real time, solve problems quickly, and improve communication among team members. At its core, Shopfloor Management aims to maximize transparency, productivity, efficiency, and quality in manufacturing.
Benefits of Shopfloor Management
- Increased Transparency in Production: By continually monitoring and analyzing production data, weaknesses and deviations can be identified and addressed immediately, ensuring consistent quality.
- Faster Response Times to Issues: Immediate intervention on emerging issues reduces downtime, minimizes production losses, and ensures stable processes.
- Enhanced Employee Engagement: By involving employees directly in improvement processes, motivation and accountability are strengthened, fostering a culture of continuous improvement.
- Efficiency Gains: Clear objectives and constant optimization contribute to streamlined production and productivity gains.
Key Elements of Shopfloor Management
- Real-Time Transparency: Data from machinery and equipment is continuously monitored and analyzed to provide a full view of current production status.
- Daily Shopfloor Meetings: Regular, brief on-site meetings facilitate fast information exchange and problem resolution.
- Visual Management: Clear KPI dashboards, production plans, and quality standards provide a quick overview and enhance transparency.
- Standards and Key Performance Indicators (KPIs): Defined KPIs measure production performance, guiding targeted improvements.
- Problem-Solving and Continuous Improvement (CIP): Employees actively identify and eliminate bottlenecks in production, improving overall efficiency.
Applications of Shopfloor Management
Shopfloor Management is widely used in manufacturing across all sizes and is particularly valuable in industries where high precision and flexibility are essential, including:
- Automotive Industry: Optimizing assembly processes and ensuring quality control
- Electronics Manufacturing: Managing and adjusting production processes with precision
- Food Industry: Maintaining quality standards and optimizing material flow
Challenges of Shopfloor Management
- Presence and Commitment: Effective Shopfloor Management requires continuous presence from leadership on the production floor for timely response.
- Cultural Shift: Success depends on a company culture that encourages open communication and proactive, continuous improvement.
- Adapting to Digital Tools: Integrating digital tools such as IoT and Big Data requires training and process adaptations.
Shopfloor Management in Lean Production and Industry 4.0
In Lean Production and Industry 4.0, Shopfloor Management is vital for waste reduction and process optimization. By combining real-time data with digitally connected systems, this approach allows flexible adjustments to market changes, increases efficiency, and enhances production quality.
Future of Shopfloor Management
Digital technology is transforming Shopfloor Management. The integration of IoT, Big Data, and cloud platforms allows closer coordination between management and production processes. These technologies create precise real-time transparency and enhance responsiveness, resulting in higher efficiency and flexibility.
Conclusion
Shopfloor Management is an essential component of modern production strategies. Through real-time monitoring, employee involvement, and continuous process optimization, it supports more efficient, flexible, and high-quality production. The digital transformation of Industry 4.0 further reinforces the importance of Shopfloor Management in achieving manufacturing excellence.