Standardization in Manufacturing
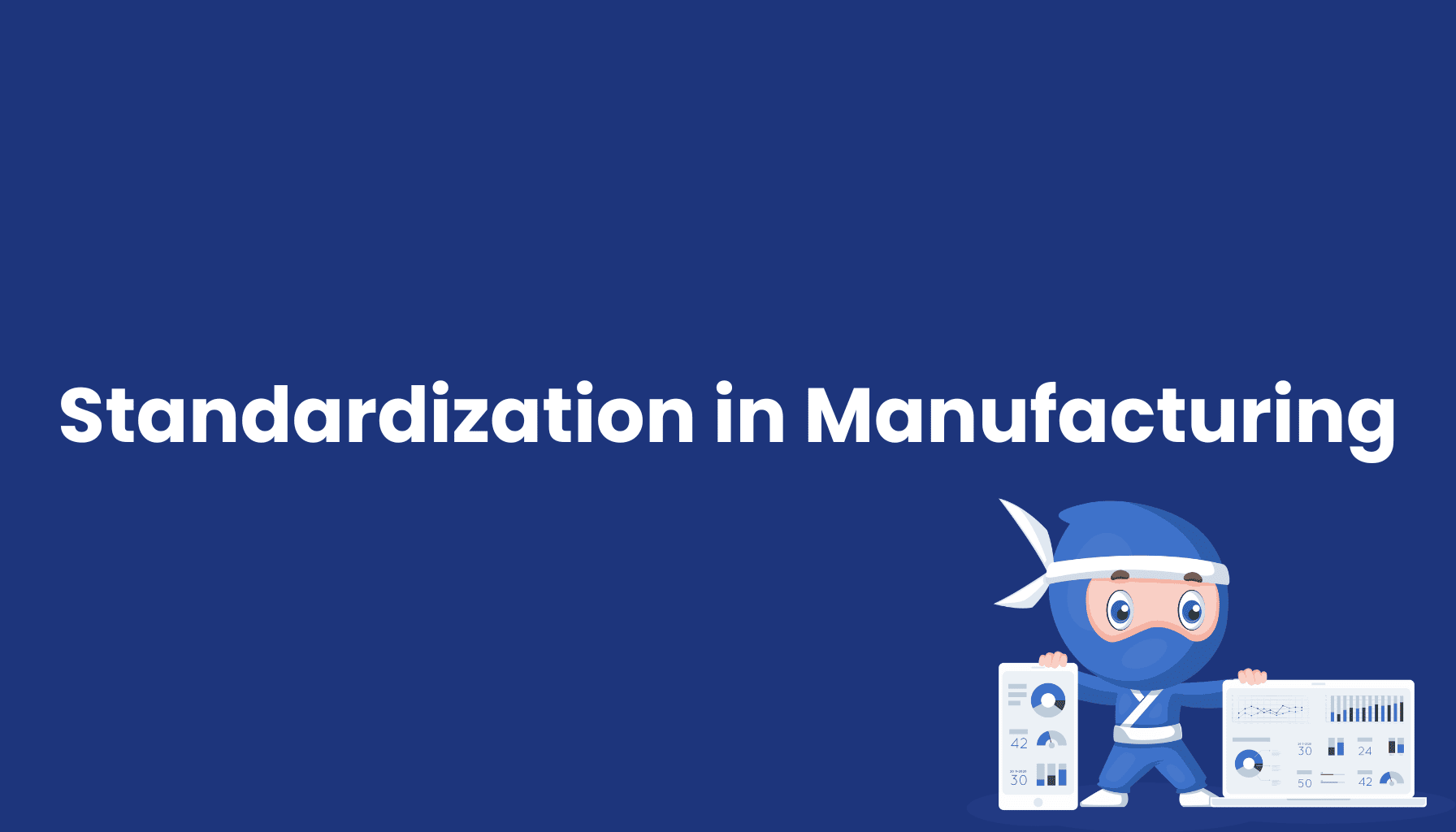
What Is Standardization in Manufacturing?
Standardization refers to the systematic unification of processes, workflows, and methods in production. As a fundamental principle of modern Manufacturing Execution Systems (MES), it ensures consistent quality, reduces errors, and enhances efficiency through well-defined standards.
Importance for Modern Manufacturing
In a digitized production environment, standardization enables:
- Reproducible quality
- Streamlined processes
- Reduced error rates
- Simplified employee training
Key Elements of Standardization
Process Standards
- Work instructions
- Inspection procedures
- Documentation practices
- Quality guidelines
Technical Standards
- Machine settings
- Tool management
- Maintenance workflows
- Calibration protocols
Organizational Standards
- Communication channels
- Defined responsibilities
- Training programs
- Best practices
Implementation Through MES
Manufacturing Execution Systems facilitate standardization via:
- Digital work instructions
- Automated process monitoring
- Standardized documentation
- Integrated quality management
Measurable Benefits
Effective standardization results in:
- 35% fewer process errors
- 40% reduced training time
- 25% higher productivity
- 30% improved quality
Conclusion
Standardization is key to achieving consistent quality and operational efficiency. Modern MES solutions provide the technological foundation for digital implementation and continuous improvement of production standards.