Systematic Performance Management in Manufacturing
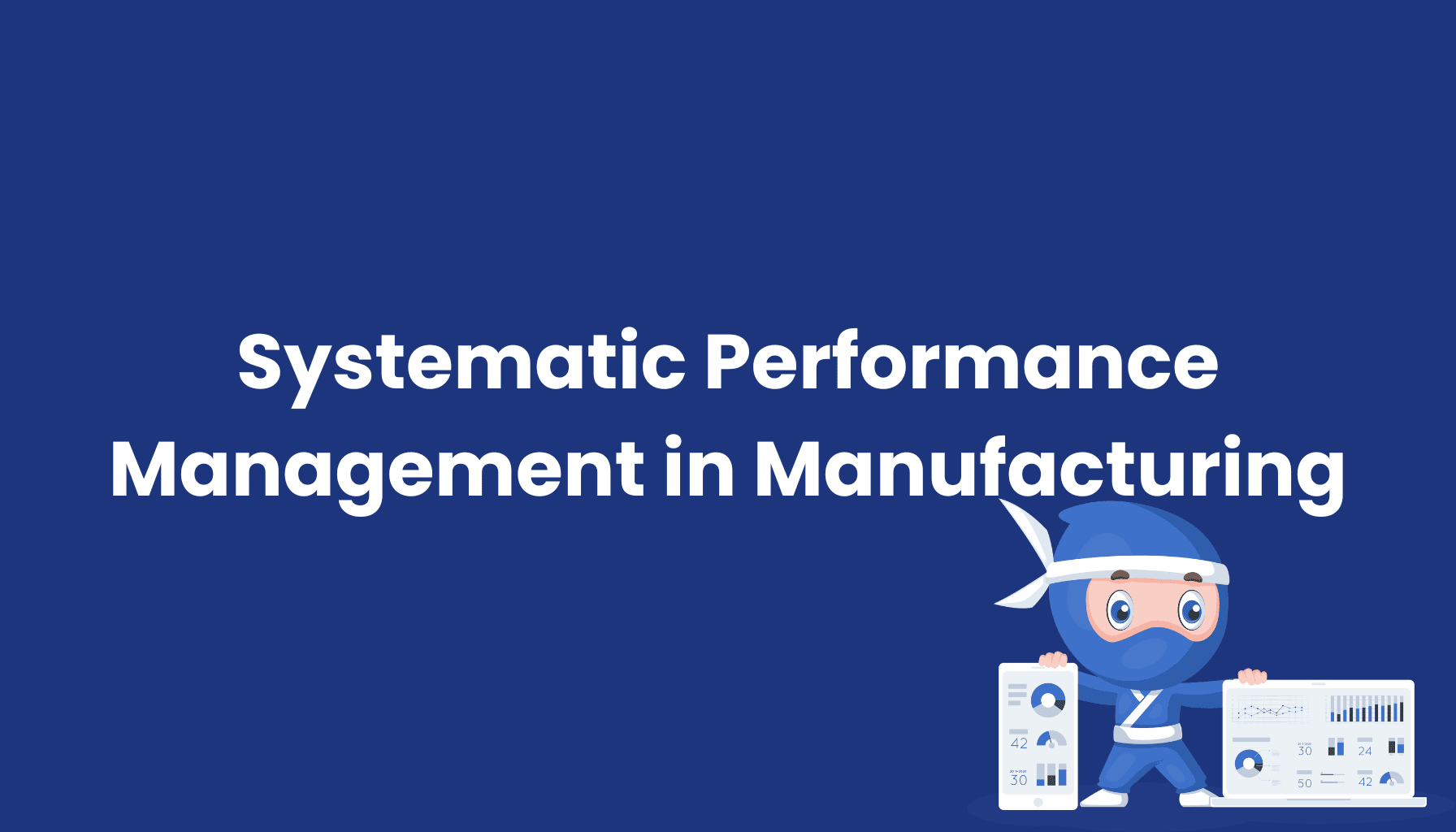
The systematic analysis and management of business performance form the foundation for sustainable competitiveness in the manufacturing sector. A structured approach to performance measurement enables precise identification of optimization potential and targeted implementation of improvement initiatives.
Key Metrics and Indicators
Performance measurement relies on a multidimensional system of metrics:
- Overall Equipment Effectiveness (OEE): Measures equipment efficiency by integrating availability, performance, and quality.
- Manufacturing Cycle Time: Analyzes lead times and process efficiency.
- First Pass Yield (FPY): Evaluates process quality during initial production runs.
Performance Monitoring Systems
Integrated monitoring systems facilitate real-time tracking of critical metrics:
- MES (Manufacturing Execution Systems): Automate the collection of production data.
- Real-Time Analytics Platforms: Transform raw data into actionable insights.
- Standardized Dashboards: Systematically visualize performance indicators.
Productivity Analysis
Systematic productivity analysis identifies areas for improvement:
- Labor Productivity Metrics: Measure workforce efficiency.
- Equipment Utilization Rate: Tracks equipment usage.
- Capacity Utilization Analysis: Assesses resource deployment.
Quality Performance
Evaluating quality performance incorporates multiple dimensions:
- Defect Rate Analysis: Quantifies quality deviations.
- Customer Complaint Rate: Assesses customer satisfaction.
- Process Capability Indices: Systematically measure process stability.
Efficiency Analysis
Efficiency evaluation focuses on resource utilization:
- Energy Efficiency Metrics: Measure energy consumption per unit produced.
- Material Utilization Rate: Analyzes material efficiency.
- Cost per Unit: Evaluates production cost-effectiveness.
Performance Optimization
Continuous performance optimization involves structured improvement processes:
- Root Cause Analysis: Identifies performance deficiencies systematically.
- Performance Improvement Teams: Implement targeted solutions.
- Continuous Monitoring: Validates the effectiveness of applied improvements.
Benchmarking and Best Practices
Benchmarking enables performance comparison with industry standards:
- Industry Performance Metrics: Define performance targets.
- Best Practice Sharing: Promotes the exchange of successful strategies.
- Competitive Analysis: Evaluates relative market positioning.
Digital Performance Management
Digital technologies enhance performance management capabilities:
- Artificial Intelligence: Identifies complex performance patterns.
- Machine Learning Algorithms: Develop predictive models for performance.
- Digital Twin Technology: Simulates optimization scenarios.