Target Costing in Manufacturing
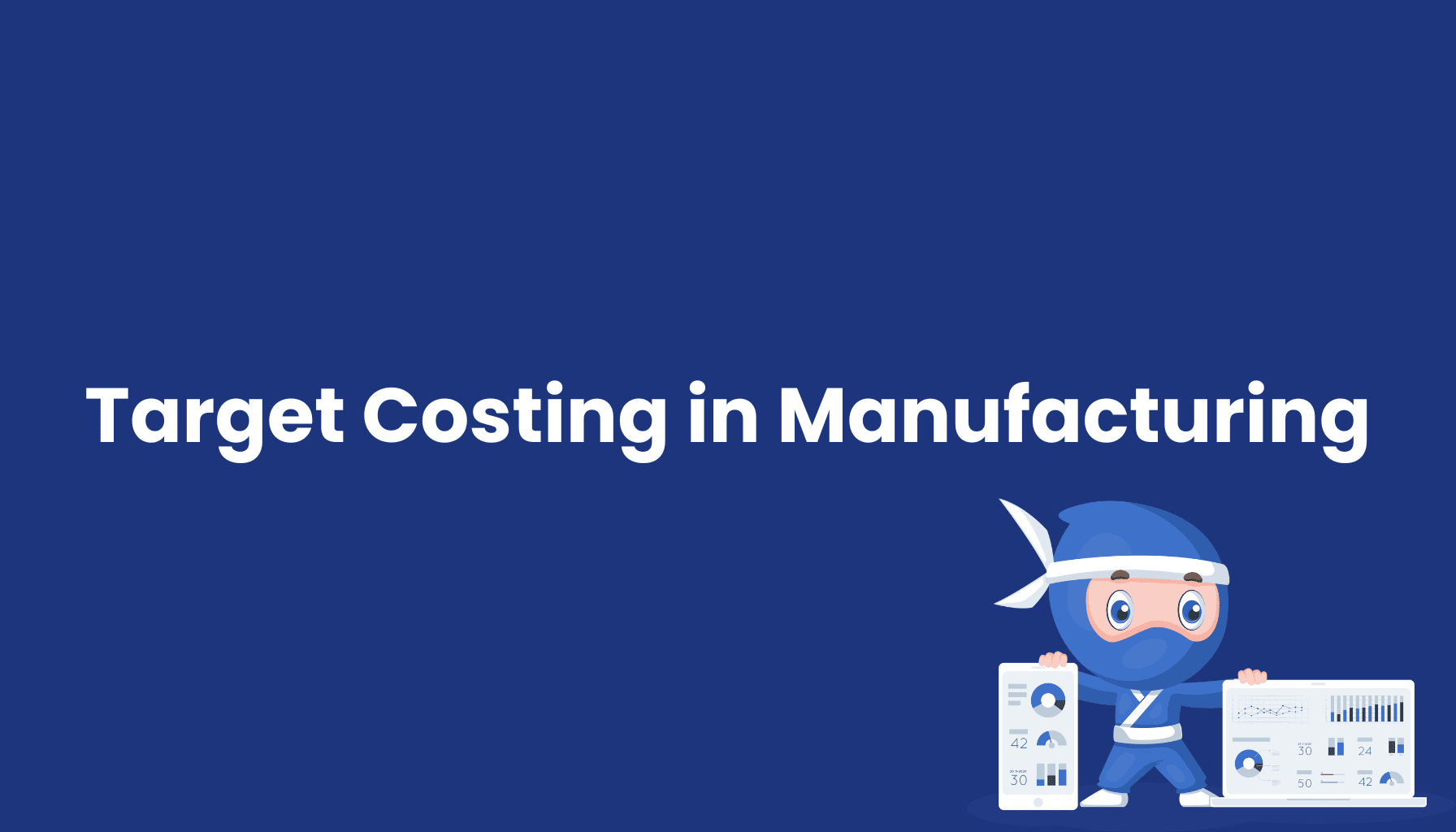
What Is Target Costing in Manufacturing?
Target costing represents a market-driven approach to systematic cost management in the manufacturing industry. This methodology enables precise definition and achievement of cost targets by integrating market demands with technical product specifications.
Systematic Implementation
The structured implementation of the target costing framework involves defined process steps:
- Market Price Determination through systematic market analysis.
- Target Profit Definition aligned with corporate strategies.
- Calculation of Allowable Product Costs based on financial goals.
- Development of Technical Specifications within cost constraints.
Cost Structure Analysis
Methodical analysis of cost structures includes:
- Value Engineering to identify cost drivers.
- Functional Cost Analysis for component evaluation.
- Cost Breakdown Structure for systematic cost allocation.
- Variance Analysis to detect deviations.
Design-to-Cost Integration
The integration of design-to-cost principles focuses on:
- Product Architecture Optimization aligned with cost objectives.
- Material Substitution without compromising functionality.
- Manufacturing Process Optimization for cost efficiency.
- Standardization to reduce complexity.
Cost Tracking and Monitoring
Continuous cost monitoring requires:
- Real-time Cost Tracking Systems for accuracy.
- Systematic Variance Analysis to identify discrepancies.
- Cost Driver Monitoring to manage influencing factors.
- Performance Metrics Evaluation to track progress.
Supplier Integration
Systematic supplier collaboration includes:
- Supplier Cost Analysis Framework for transparency.
- Collaborative Cost Reduction Programs to align goals.
- Value Chain Optimization for holistic improvements.
- Joint Development Initiatives for innovative solutions.
Performance Measurement
Quantitative success measurement integrates:
- Target Achievement Rate Analysis to evaluate goal alignment.
- Cost Reduction Performance Metrics to track savings.
- Process Efficiency Indicators to measure operational gains.
- Quality-Cost-Balance Evaluation for maintaining standards.
Continuous Improvement
Systematic improvement processes focus on:
- Kaizen Costing Implementation for ongoing refinement.
- Value Stream Optimization to enhance workflows.
- Process Innovation Integration for advanced methodologies.
- Cost Engineering Development to sustain competitive advantage.