Toyota Production System (TPS)
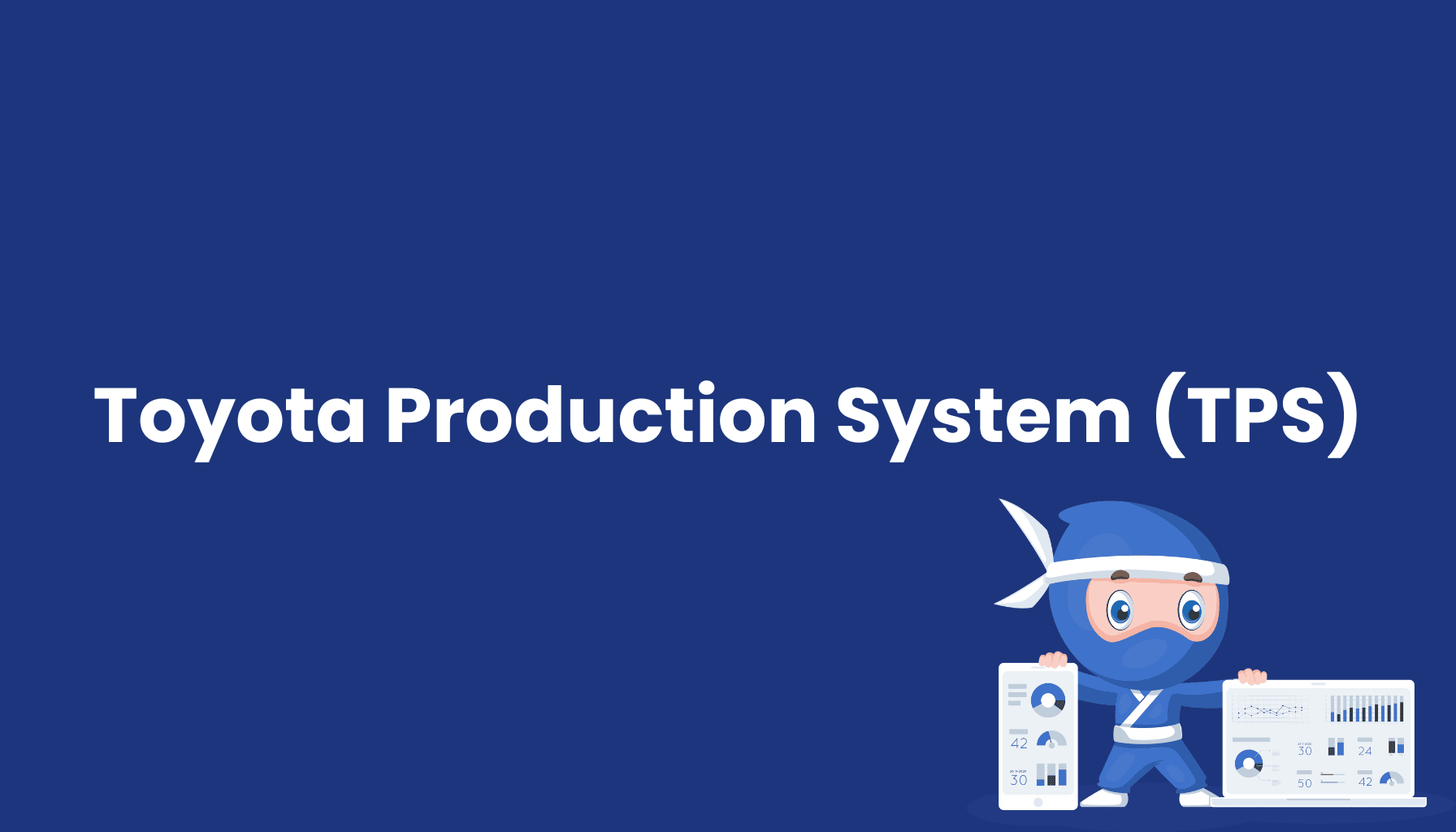
What is the Toyota Production System (TPS)?
The Toyota Production System (TPS) is an influential production methodology centered on efficiency, quality, and continuous improvement. Developed by Toyota, TPS aims to eliminate waste across all production areas, achieving maximum value creation. Core methods such as Just-in-Time (JIT) and Jidoka (automation with a human touch) support these objectives, enabling flexible, resource-efficient, and high-quality production processes.
Core Principles of TPS
-
Just-in-Time (JIT): Production occurs strictly as needed, minimizing overproduction and excess inventory. Materials and products are delivered and manufactured only when necessary. JIT reduces storage costs and optimizes resource use across the supply chain.
-
Jidoka (Automation with a Human Touch): This principle ensures that machines stop automatically when issues arise, and employees have the authority to halt production to address quality concerns immediately. Quality is thus maintained directly within the production process, and problems are resolved at the source.
Advantages of the Toyota Production System
-
Waste Minimization: TPS identifies seven types of waste (overproduction, waiting, transport, excess inventory, unnecessary movement, defects, and underutilized talent) and works systematically to eliminate them. This significantly reduces production costs.
-
Increased Productivity: Efficient use of resources and streamlined workflows accelerate processes and prevent bottlenecks, leading to a sustainable increase in productivity.
-
Continuous Improvement (Kaizen): TPS embodies a culture of constant improvement. Employees from all levels actively engage in identifying and implementing improvements. Kaizen fosters continuous optimization and contributes to a positive workplace atmosphere.
-
High Product Quality: Combining JIT and Jidoka ensures that only high-quality products leave the production line. By addressing issues immediately, TPS reduces defects and significantly improves product reliability.
-
Flexibility: TPS enables companies to adapt quickly to market changes and customer demands. The Just-in-Time approach minimizes inventory and supports agile responses to shifting conditions.
Applications and Global Relevance of TPS
Originally developed for the automotive industry, the Toyota Production System has been successfully adapted in various other sectors, including electronics, food production, and consumer goods manufacturing. The model holds international importance and serves as a global standard for efficient, customer-focused production methods.
Conclusion
The Toyota Production System (TPS) is a powerful approach to production optimization, focusing on efficiency, quality, and continuous improvement. With methods such as Just-in-Time and Jidoka, companies can minimize waste, maximize productivity, and deliver high-quality products. TPS is more than just a production system – it is a philosophy that deeply influences organizational culture and enhances competitiveness.