Operational Excellence (OPEX): Definition, Methoden und Implementierung
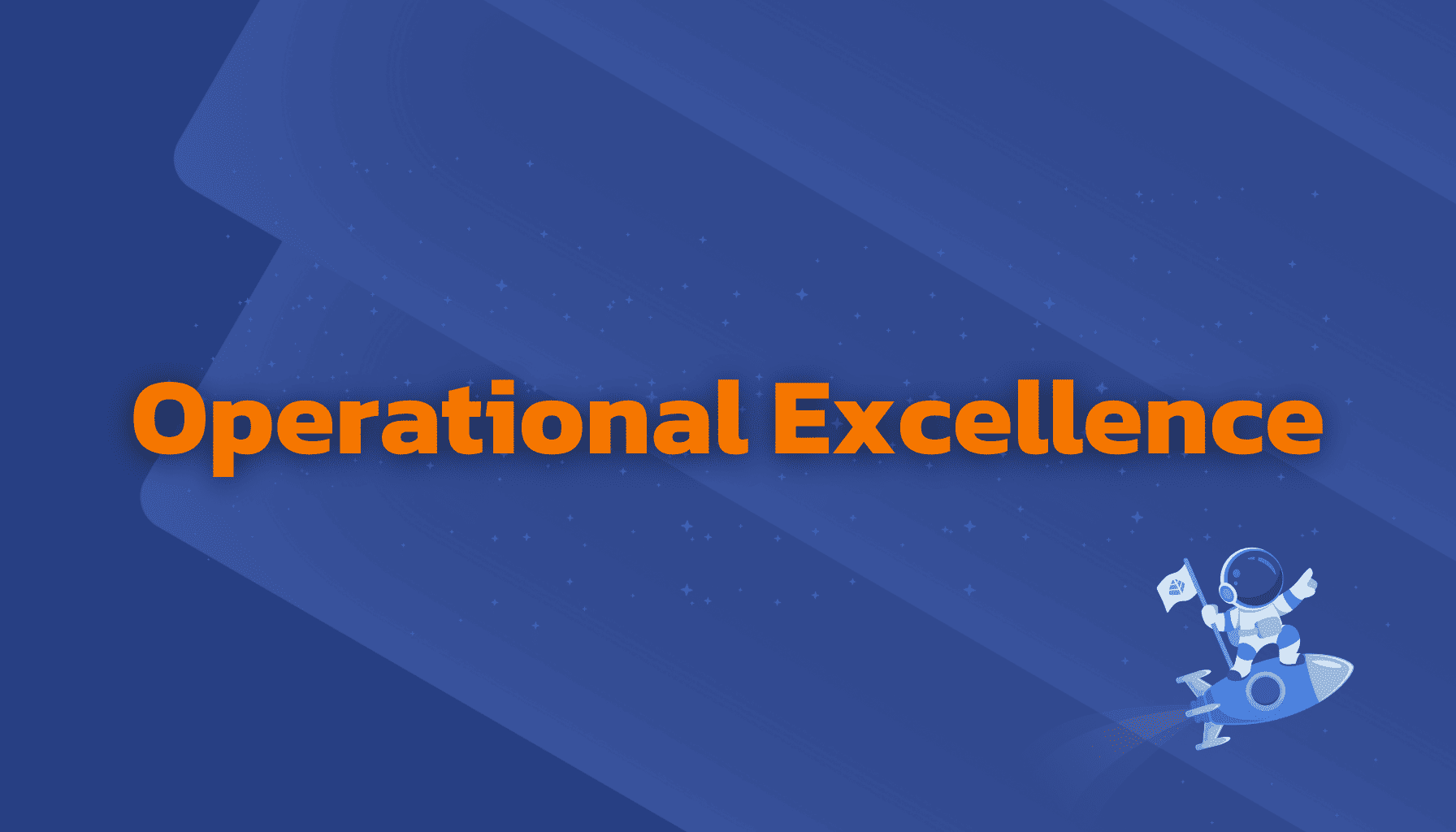
Was ist Operational Excellence (OPEX)?
Operational Excellence (OPEX) ist ein ganzheitlicher Managementansatz, der auf die kontinuierliche Optimierung der gesamten Wertschöpfungskette eines Unternehmens abzielt. Im Kern geht es darum, Prozesse hinsichtlich Effizienz und Effektivität systematisch zu verbessern, Verschwendung zu eliminieren und einen nachhaltigen Wettbewerbsvorteil zu schaffen.
Operational Excellence (OPEX) bezeichnet die Fähigkeit eines Unternehmens, alle Prozesse entlang der Wertschöpfungskette kontinuierlich zu optimieren und zu standardisieren. Das Konzept vereint Elemente aus Lean Management, Six Sigma und Total Quality Management mit dem Ziel, maximale Effizienz, höchste Qualität und konsequente Kundenorientierung zu erreichen.
Im Gegensatz zu punktuellen Verbesserungsinitiativen repräsentiert OPEX eine umfassende Unternehmensphilosophie, die tief in der Organisationskultur verankert sein muss. Sie erfordert ein grundlegendes Umdenken auf allen Ebenen – von der Führungsebene bis hin zu jedem einzelnen Mitarbeiter.
Die vier Säulen der Operational Excellence
Operational Excellence basiert auf vier fundamentalen Säulen, die gemeinsam das Fundament für nachhaltige Spitzenleistungen bilden:
1. Prozessoptimierung und -standardisierung
Die erste Säule konzentriert sich auf die systematische Verbesserung und Standardisierung aller Geschäftsprozesse:
- Wertstromanalyse: Identifikation von wertschöpfenden und nicht-wertschöpfenden Aktivitäten
- Prozessstandardisierung: Etablierung von Best Practices und einheitlichen Vorgehensweisen
- Kontinuierliche Verbesserung: Systematische Optimierung aller Prozesse durch KVP/Kaizen
- Fehlervermeidung: Implementierung von Poka-Yoke-Mechanismen zur Prävention von Fehlern
2. Leistungsmessung und Transparenz
Die zweite Säule betrifft die Etablierung von klaren Kennzahlen und Messsystemen:
- KPI-Management: Definition und Überwachung relevanter Leistungskennzahlen
- Visuelle Management-Systeme: Transparente Darstellung von Leistungsdaten und Abweichungen
- Echtzeit-Monitoring: Kontinuierliche Überwachung kritischer Prozessparameter
- Datenbasierte Entscheidungsfindung: Nutzung von Daten als Grundlage für Verbesserungsmaßnahmen
3. Führung und Unternehmenskultur
Die dritte Säule fokussiert die menschliche Komponente von OPEX:
- Führungskräfteentwicklung: Befähigung von Führungskräften zu Coaches und Mentoren
- Kulturwandel: Etablierung einer Kultur der kontinuierlichen Verbesserung
- Mitarbeitereinbindung: Aktive Beteiligung aller Mitarbeiter am Verbesserungsprozess
- Teamarbeit: Förderung von bereichsübergreifender Zusammenarbeit und Problemlösung
4. Kundenorientierung und Wertschöpfung
Die vierte Säule stellt den Kunden und die Wertschöpfung in den Mittelpunkt:
- Kundenfokussierung: Ausrichtung aller Aktivitäten auf die Erfüllung von Kundenbedürfnissen
- Wertschöpfungsorientierung: Konzentration auf wertschaffende Aktivitäten
- Qualitätsmanagement: Sicherstellung höchster Produktqualität und Serviceexzellenz
- Time-to-Market: Beschleunigung von Entwicklungs- und Bereitstellungsprozessen
Die Evolution von Operational Excellence: Von der Werkshalle zur digitalen Transformation
Operational Excellence hat einen langen Entwicklungsweg hinter sich, der eng mit der industriellen Entwicklung verknüpft ist:
Phase 1: Frühe Grundlagen (Anfang bis Mitte des 20. Jahrhunderts)
Die Wurzeln von OPEX lassen sich bis zu Frederick W. Taylors Prinzipien des wissenschaftlichen Managements zurückverfolgen. Diese frühen Ansätze konzentrierten sich hauptsächlich auf:
- Standardisierung von Arbeitsprozessen
- Zeitstudien zur Effizienzsteigerung
- Spezialisierung von Arbeitskräften
Phase 2: Qualitätsrevolution (1950er bis 1980er Jahre)
Maßgeblich beeinflusst durch Pioniere wie W. Edwards Deming und Joseph Juran entwickelte sich die Qualitätsbewegung in Japan und später weltweit:
- Total Quality Management (TQM) als ganzheitlicher Qualitätsansatz
- Statistische Prozesskontrolle zur Qualitätssicherung
- PDCA-Zyklus (Plan-Do-Check-Act) als Verbesserungsmodell
Phase 3: Lean und Six Sigma (1980er bis 2000er Jahre)
Die Erfolge des Toyota Production Systems führten zur weltweiten Verbreitung von Lean-Prinzipien:
- Lean Manufacturing zur Eliminierung von Verschwendung
- Six Sigma zur systematischen Fehlerreduzierung
- Integration beider Ansätze zu Lean Six Sigma
Phase 4: Digitalisierung und Industrie 4.0 (ab 2010)
Die aktuelle Phase ist geprägt durch die digitale Transformation und die Industrie 4.0:
- Big Data und Analytics zur Prozessoptimierung
- IoT und Sensorik für Echtzeit-Prozesskontrolle
- Künstliche Intelligenz zur Vorhersage von Prozessabweichungen
- Cloud-basierte Systeme für unternehmensweite Transparenz
Methodenüberblick: Werkzeuge für Operational Excellence
Zur Implementierung von Operational Excellence steht ein umfangreiches Methodenportfolio zur Verfügung:
Lean Management-Methoden
Lean Management zielt darauf ab, Verschwendung zu eliminieren und den Wertschöpfungsprozess zu optimieren:
- 5S (Sortieren, Systematisieren, Säubern, Standardisieren, Selbstdisziplin): Methode zur Arbeitsplatzorganisation
- Wertstromanalyse: Visualisierung und Optimierung des Materialflusses
- Kanban: System zur Steuerung des Materialflusses nach dem Pull-Prinzip
- SMED (Single Minute Exchange of Die): Methode zur Reduzierung von Rüstzeiten
- TPM (Total Productive Maintenance): Ganzheitlicher Ansatz zur Instandhaltung
Six Sigma-Werkzeuge
Six Sigma bietet strukturierte Methoden zur Reduzierung von Prozessvariationen und Fehlern:
- DMAIC-Zyklus (Define, Measure, Analyze, Improve, Control): Strukturierter Problemlösungsprozess
- Statistische Analysewerkzeuge: Datenbasierte Entscheidungsfindung
- Ursache-Wirkungs-Diagramme: Systematische Ursachenanalyse
- Design of Experiments (DoE): Strukturierte Versuchsplanung
- Fehler-Möglichkeits- und Einfluss-Analyse (FMEA): Proaktive Risikominimierung
Qualitätsmanagement-Tools
Aus dem TQM-Bereich stammen weitere wichtige Werkzeuge:
- PDCA-Zyklus: Iterativer Verbesserungsprozess
- Quality Function Deployment (QFD): Methode zur kundenorientierten Produktentwicklung
- Balanced Scorecard: Ganzheitliches Kennzahlensystem
- Benchmarking: Vergleich mit Best Practices
- Prozessaudits: Systematische Überprüfung von Prozessen
Digitale Werkzeuge für Operational Excellence 4.0
Die digitale Transformation erweitert das Methodenspektrum um neue Technologien:
- Manufacturing Execution Systems (MES): Echtzeit-Steuerung der Produktion
- IoT-basierte Sensorik: Automatische Datenerfassung aus Produktionsprozessen
- Predictive Analytics: Vorhersage von Maschinenausfällen und Qualitätsproblemen
- Digital Twins: Virtuelle Abbilder zur Prozessoptimierung
- Cloud-basierte Plattformen: Unternehmensweites Daten- und Prozessmanagement
Implementierungsstrategie: Der Weg zur operativen Exzellenz
Die erfolgreiche Implementierung von OPEX erfordert eine strukturierte Vorgehensweise und einen langfristigen Ansatz:
Phase 1: Strategische Ausrichtung und Vorbereitung
- Vision und Strategie entwickeln: Definition einer klaren OPEX-Vision und -Strategie
- Leadership-Commitment sichern: Gewinnung der vollen Unterstützung des Top-Managements
- Ausgangssituation analysieren: Durchführung einer umfassenden Ist-Analyse
- Ziele definieren: Festlegung messbarer Ziele und KPIs
- Roadmap erstellen: Entwicklung eines mehrjährigen Implementierungsplans
Phase 2: Pilotprojekte und erste Erfolge
- Pilotbereiche auswählen: Identifikation geeigneter Bereiche für erste Pilotprojekte
- Teams bilden und schulen: Aufbau von OPEX-Teams und Vermittlung notwendiger Kompetenzen
- Erste Verbesserungsprojekte starten: Umsetzung von Quick-Win-Projekten
- Erfolge kommunizieren: Breite Kommunikation der erzielten Ergebnisse
- Lessons Learned sammeln: Systematische Erfassung und Auswertung von Erfahrungen
Phase 3: Skalierung und Institutionalisierung
- Rollout in weitere Bereiche: Schrittweise Ausweitung auf alle Unternehmensbereiche
- Governance-Strukturen etablieren: Aufbau von dauerhaften OPEX-Strukturen und -Prozessen
- Kompetenzen erweitern: Kontinuierliche Weiterbildung und Kompetenzaufbau
- Kulturwandel vorantreiben: Verankerung von OPEX in der Unternehmenskultur
- Managementsystem anpassen: Integration von OPEX in bestehende Managementsysteme
Phase 4: Kontinuierliche Weiterentwicklung
- Systematisches Monitoring: Regelmäßige Überprüfung der OPEX-Performance
- Benchmarking: Vergleich mit internen und externen Best Practices
- Neue Methoden integrieren: Aufnahme innovativer Ansätze und Technologien
- Reifegradmodell anwenden: Bewertung und Steigerung des OPEX-Reifegrads
- Langfristige Nachhaltigkeit sichern: Verankerung als Teil der Unternehmensstrategie
Erfolgsfaktoren und häufige Herausforderungen
Bei der Implementierung von Operational Excellence sind bestimmte Faktoren entscheidend für den Erfolg, während andere typische Herausforderungen darstellen:
Kritische Erfolgsfaktoren
- Leadership und Management-Commitment:
- Aktive Unterstützung und Vorbildfunktion der Führungsebene
- Bereitstellung notwendiger Ressourcen und Rahmenbedingungen
- Konsistente und nachhaltige Fokussierung auf OPEX
- Mitarbeitereinbindung und -befähigung:
- Aktive Beteiligung aller Mitarbeiter am Verbesserungsprozess
- Umfassende Schulung und kontinuierliche Kompetenzentwicklung
- Schaffung eines sicheren Umfelds für Verbesserungsvorschläge
- Ganzheitlicher und systematischer Ansatz:
- Berücksichtigung aller Aspekte der Wertschöpfungskette
- Systematische Methodenanwendung statt punktueller Maßnahmen
- Balance zwischen kurzfristigen Verbesserungen und langfristiger Transformation
- Kulturwandel und Change Management:
- Etablierung einer Kultur der kontinuierlichen Verbesserung
- Professionelles Change Management zur Überwindung von Widerständen
- Wertschätzung und Anerkennung von Verbesserungsinitiativen
Typische Herausforderungen und Lösungsansätze
- Widerstand gegen Veränderung:
- Herausforderung: Mitarbeiter und Führungskräfte halten an gewohnten Arbeitsweisen fest
- Lösungsansatz: Partizipative Einbindung aller Beteiligten, klare Kommunikation von Nutzen und Zielen, schrittweise Einführung
- Kurzfristiges Denken:
- Herausforderung: Fokus auf schnelle Ergebnisse statt nachhaltiger Transformation
- Lösungsansatz: Balance zwischen Quick Wins und langfristigen Zielen, Entwicklung einer mehrjährigen Roadmap
- Ressourcenmangel:
- Herausforderung: Unzureichende Zeit-, Personal- und Finanzressourcen
- Lösungsansatz: Priorisierung von Initiativen mit hohem ROI, Integration von OPEX in bestehende Aktivitäten
- Unzureichende Nachhaltigkeit:
- Herausforderung: Initiale Verbesserungen werden nicht dauerhaft aufrechterhalten
- Lösungsansatz: Etablierung von Governance-Strukturen, regelmäßiges Audit, Verankerung in KPIs und Zielvereinbarungen
Operational Excellence im digitalen Zeitalter: Industrie 4.0 und OPEX 4.0
Die digitale Transformation und Industrie 4.0 eröffnen neue Dimensionen für Operational Excellence:
Integration von OPEX und Digitalisierung
Die Verbindung von traditionellen OPEX-Prinzipien mit digitalen Technologien schafft erhebliche Synergiepotenziale:
- Datengestützte Prozessoptimierung: Nutzung von Big Data zur Identifikation von Verbesserungspotenzialen
- Echtzeit-Transparenz: Kontinuierliche Überwachung aller relevanten Prozessparameter
- Automatisierte Prozesssteuerung: Selbstregulierende Systeme mit minimalen manuellen Eingriffen
- Predictive Maintenance: Vorausschauende Instandhaltung zur Vermeidung von Ausfällen
- KI-gestützte Entscheidungsunterstützung: Automatische Analyse komplexer Zusammenhänge
Cloud-basierte OPEX-Plattformen
Moderne SaaS-Lösungen bieten umfassende Unterstützung für Operational Excellence:
- Zentrales Prozess- und Leistungsmanagement: Unternehmensweite Transparenz und Steuerung
- Digitale Shopfloor-Management-Boards: Echtzeit-Visualisierung von KPIs und Abweichungen
- Kollaborative Verbesserungssysteme: Digitale Unterstützung von KVP und Problemlösungsprozessen
- Mobile Zugänglichkeit: Standortunabhängiger Zugriff auf relevante Informationen
- Integrierte Analyse- und Reporting-Funktionen: Automatisierte Auswertung und Berichterstattung
Industrie 4.0 und Smart Factory
Die Smart Factory als Vision der Zukunft basiert auf der Integration von OPEX und Digitalisierung:
- Cyber-physische Systeme: Intelligente Verbindung von physischer und digitaler Welt
- Horizontale und vertikale Integration: Durchgängige Vernetzung aller Systeme und Ebenen
- Selbstoptimierende Produktionssysteme: Autonome Anpassung an veränderte Bedingungen
- Flexible und adaptive Fertigungsprozesse: Schnelle Reaktion auf wechselnde Anforderungen
- Digitale Zwillinge: Virtuelle Simulation und Optimierung realer Prozesse
Messung und Monitoring von Operational Excellence
Die kontinuierliche Überwachung des OPEX-Fortschritts ist entscheidend für den langfristigen Erfolg:
Zentrale Leistungskennzahlen (KPIs)
Je nach Unternehmenskontext und OPEX-Fokus sind verschiedene KPIs relevant:
- Effizienz und Produktivität:
- Overall Equipment Effectiveness (OEE)
- Durchlaufzeiten und Zykluszeiten
- Arbeitsproduktivität und Maschinenproduktivität
- Value-Added-Ratio (Verhältnis wertschöpfender zu nicht-wertschöpfender Zeit)
- Qualität und Zuverlässigkeit:
- First-Pass-Yield (Ausbeute im ersten Durchlauf)
- Fehler- und Ausschussraten
- Process Capability Index (Cp/Cpk)
- Mean Time Between Failures (MTBF)
- Liefertreue und Flexibilität:
- On-Time-Delivery-Rate (OTD)
- Lieferzeit und Termintreue
- Rüst- und Umstellzeiten
- Reaktionsfähigkeit auf Bedarfsänderungen
- Kosten und Ressourceneffizienz:
- Stückkosten und Gesamtbetriebskosten
- Bestandshöhe und Umschlagshäufigkeit
- Ressourcenverbrauch (Energie, Material)
- Return on Investment von Verbesserungsinitiativen
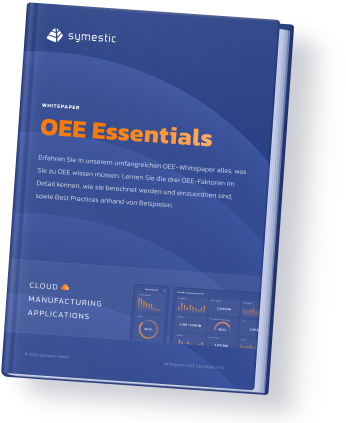
OPEX-Reifegradmodelle
Reifegradmodelle ermöglichen eine strukturierte Bewertung des OPEX-Fortschritts:
- Stufe 1 - Anfänger: Erste isolierte Verbesserungsinitiativen ohne systematischen Ansatz
- Stufe 2 - Fortgeschritten: Strukturierte Methodenanwendung in ausgewählten Bereichen
- Stufe 3 - Etabliert: Unternehmensweite Anwendung mit etablierten Strukturen und Prozessen
- Stufe 4 - Fortschrittlich: Tief verankerte OPEX-Kultur mit eigenständiger Verbesserungsdynamik
- Stufe 5 - Weltklasse: OPEX als strategischer Wettbewerbsvorteil mit kontinuierlicher Innovation
Balanced Scorecard für Operational Excellence
Eine ausgewogene Bewertung aller OPEX-Dimensionen erfordert einen ganzheitlichen Ansatz:
- Finanzperspektive: Kostensenkung, Produktivitätssteigerung, ROI
- Kundenperspektive: Qualität, Liefertreue, Flexibilität, Kundenzufriedenheit
- Interne Prozessperspektive: Effizienz, Durchlaufzeit, Fehlerrate, Bestandshöhe
- Innovations- und Lernperspektive: Verbesserungsaktivitäten, Kompetenzentwicklung, Kulturwandel
Die Zukunft von Operational Excellence
Die Entwicklung von OPEX wird durch verschiedene Trends und Innovationen geprägt:
Technologische Trends
- Künstliche Intelligenz und Machine Learning: Selbstoptimierende Systeme und automatisierte Entscheidungsfindung
- Advanced Analytics: Komplexe Datenanalysen zur Identifikation versteckter Verbesserungspotenziale
- Augmented Reality und Virtual Reality: Unterstützung bei Schulung, Instandhaltung und Prozessoptimierung
- Blockchain-Technologie: Sichere und transparente Supply-Chain-Prozesse
- 5G und Edge Computing: Echtzeit-Datenverarbeitung direkt am Entstehungsort
Methodische Weiterentwicklungen
- Agile Operational Excellence: Integration von agilen Methoden in OPEX-Ansätze
- Design Thinking für OPEX: Nutzerorientierte Innovation von Prozessen und Systemen
- Sustainable Operations Excellence: Integration von Nachhaltigkeitsaspekten in OPEX
- Resilience by Design: Fokus auf Robustheit und Anpassungsfähigkeit bei Störungen
- Ecosystem Excellence: Erweiterung von OPEX über Unternehmensgrenzen hinaus
Kulturelle und organisatorische Entwicklungen
- Selbstorganisierende Teams: Höhere Autonomie und Eigenverantwortung in der Prozessgestaltung
- Remote und hybride Arbeitsmodelle: Anpassung von OPEX an neue Arbeitsformen
- Lebenslanges Lernen: Kontinuierliche Kompetenzentwicklung für OPEX 4.0
- Purpose-Driven Excellence: Verknüpfung von OPEX mit übergeordnetem Unternehmenszweck
- Co-Creation mit Kunden: Gemeinsame Wertschöpfungsoptimierung mit Kunden und Partnern
Fazit: Operational Excellence als strategischer Erfolgsfaktor
Operational Excellence ist kein einmaliges Projekt, sondern eine kontinuierliche Reise zur Prozessoptimierung und Leistungssteigerung. In einer zunehmend volatilen, unsicheren, komplexen und ambivalenten (VUCA) Geschäftswelt wird OPEX zum entscheidenden Wettbewerbsfaktor.
Die erfolgreiche Integration von traditionellen OPEX-Prinzipien mit modernen digitalen Technologien eröffnet völlig neue Möglichkeiten zur Effizienzsteigerung, Qualitätsverbesserung und Kundenorientierung. Unternehmen, die diesen Weg konsequent verfolgen, schaffen die Grundlage für nachhaltigen Geschäftserfolg.
Entscheidend für den Erfolg ist die Kombination aus methodischer Expertise, technologischer Innovation und kulturellem Wandel. Nur wenn alle drei Dimensionen gleichermaßen berücksichtigt werden, kann das volle Potenzial von Operational Excellence ausgeschöpft werden.
In diesem Sinne ist Operational Excellence nicht nur ein Managementansatz, sondern eine fundamentale Unternehmensstrategie für die Herausforderungen des 21. Jahrhunderts.
Verwandte Themen:
Exklusives Whitepaper
Lernen Sie die modernsten Ansätze der Industrie 4.0, die Sie in Ihrer Produktion schon morgen umsetzen können, um innerhalb von 4 Wochen Ihre Kosten um gut 20% zu reduzieren.
mehr erfahren