Statistische Prozesskontrolle (SPC) – Definition & Bedeutung
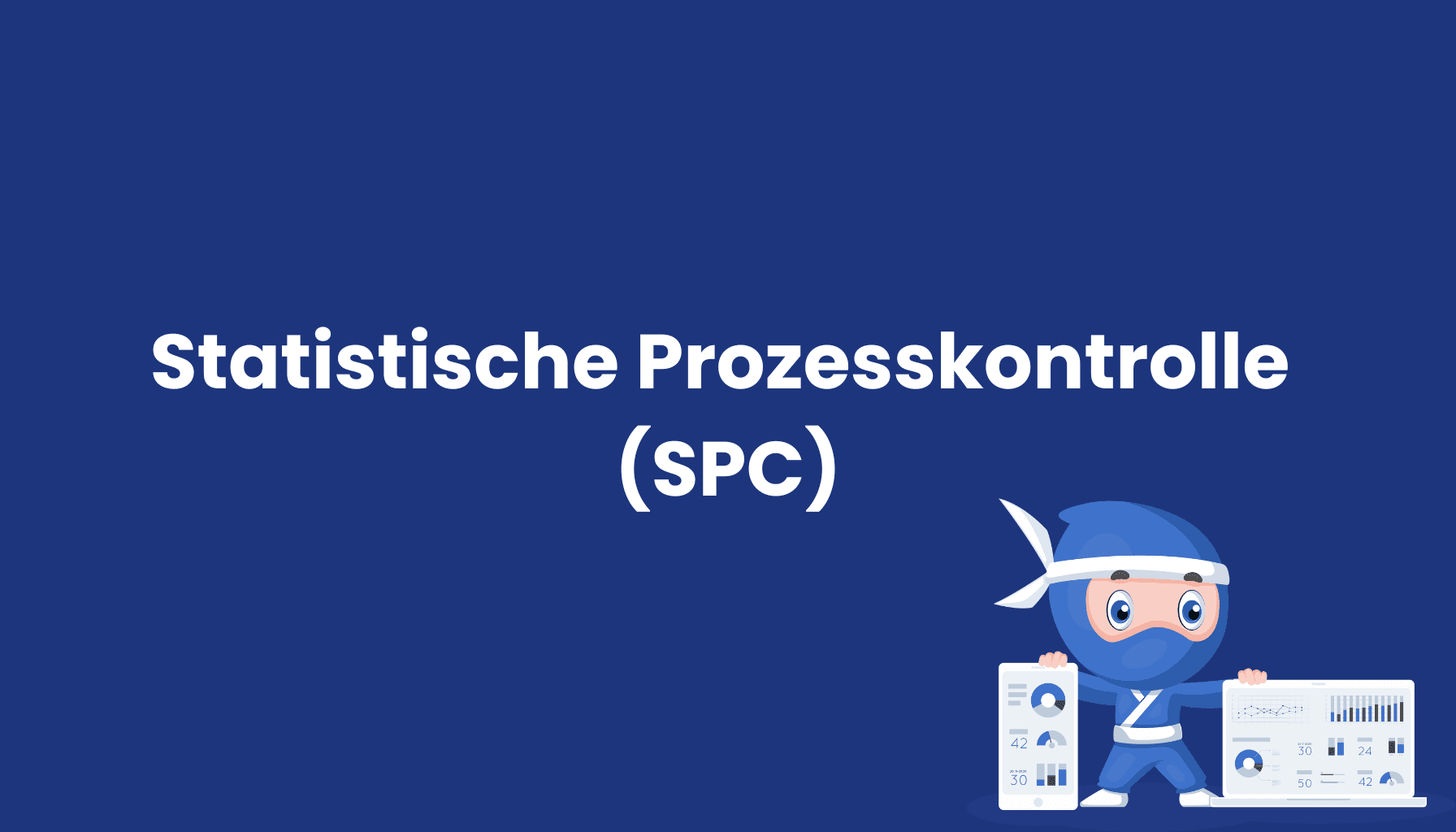
Die Statistische Prozesskontrolle (Statistical Process Control, SPC) ist eine etablierte Qualitätsmethode zur präventiven Überwachung und Steuerung von Produktionsprozessen. Im Gegensatz zu reaktiven Qualitätssicherungsansätzen ermöglicht SPC die frühzeitige Erkennung von Prozessabweichungen, bevor diese zu Ausschuss oder Qualitätsmängeln führen. Diese proaktive Methodik hat sich besonders in Branchen mit hohen Qualitätsanforderungen wie der Automobil-, Elektronik-, Pharma- und Lebensmittelindustrie als unverzichtbares Werkzeug etabliert.
Grundprinzipien der Statistischen Prozesskontrolle
Die Statistische Prozesskontrolle wurde in den 1920er Jahren von Walter A. Shewhart bei den Bell Laboratories entwickelt und später von Qualitätsexperten wie W. Edwards Deming weiterentwickelt. Shewharts grundlegende Erkenntnis: Jeder Produktionsprozess unterliegt natürlichen Schwankungen, die statistisch beschreibbar sind.
Die zwei Arten von Prozessschwankungen
Ein zentrales Prinzip der SPC ist die Unterscheidung zwischen zwei Arten von Prozessschwankungen:
- Zufällige Schwankungen (auch "allgemeine Ursachen" genannt):
- Natürliche Variabilität, die jedem Prozess innewohnt
- Vorhersagbar innerhalb statistischer Grenzen
- Führen zu einem stabilen, beherrschten Prozess
- Beispiele: Minimale Materialunterschiede, geringfügige Temperaturschwankungen, normale Werkzeugabnutzung
- Systematische Schwankungen (auch "spezielle Ursachen" genannt):
- Außergewöhnliche, unnatürliche Einflüsse auf den Prozess
- Führen zu einem instabilen, nicht beherrschten Prozess
- Erfordern ein Eingreifen in den Prozess
- Beispiele: Defekte Maschinen, Materialwechsel, ungeschultes Personal, Werkzeugbruch
Die Kernaufgabe der SPC besteht darin, zwischen diesen beiden Arten von Schwankungen zu unterscheiden und nur dann in den Prozess einzugreifen, wenn tatsächlich systematische Abweichungen auftreten. Dieses Prinzip verhindert das "Überregeln" von Prozessen, bei dem Anpassungen auf Basis zufälliger Schwankungen zu einer Verschlechterung der Prozessleistung führen würden.
Der PDCA-Zyklus in der Statistischen Prozesskontrolle
Die SPC folgt dem Plan-Do-Check-Act (PDCA) Prinzip und ermöglicht einen strukturierten Ansatz zur kontinuierlichen Prozessverbesserung:
- Plan: Definition der zu überwachenden Parameter, Festlegung von Prüfintervallen und Stichprobengrößen, Auswahl geeigneter Regelkartentypen
- Do: Systematische Datenerfassung im laufenden Prozess
- Check: Statistische Auswertung und Bewertung der Daten mittels Qualitätsregelkarten
- Act: Einleitung von Korrekturmaßnahmen bei Erkennung systematischer Abweichungen
Diese zyklische Vorgehensweise ermöglicht eine kontinuierliche Überwachung und Verbesserung der Prozesse.
Die statistische Basis: Prozessstabilität und Prozessfähigkeit
Für das Verständnis und die erfolgreiche Anwendung von SPC sind zwei fundamentale Konzepte entscheidend: die Prozessstabilität und die Prozessfähigkeit.
Prozessstabilität
Ein Prozess gilt als stabil (oder "beherrscht"), wenn nur zufällige Schwankungen auftreten und keine systematischen Einflüsse wirken. Die Stabilität eines Prozesses wird mittels Qualitätsregelkarten überprüft:
- Ein stabiler Prozess zeigt ein vorhersagbares Verhalten innerhalb der Kontrollgrenzen
- Die Datenpunkte folgen keinem erkennbaren Muster, sondern sind zufällig verteilt
- Es gibt keine statistisch signifikanten Trends, Zyklen oder Sprünge
Die Prozessstabilität ist eine notwendige Voraussetzung für jede sinnvolle Prozessfähigkeitsanalyse, da nur bei stabilen Prozessen eine zuverlässige Vorhersage der zukünftigen Prozessleistung möglich ist.
Prozessfähigkeit
Die Prozessfähigkeit beschreibt die Fähigkeit eines stabilen Prozesses, Produkte innerhalb der spezifizierten Toleranzgrenzen zu fertigen. Sie wird durch Prozessfähigkeitsindizes quantifiziert:
- Cp (Prozessfähigkeitsindex):
- Verhältnis der Toleranzbreite zur Prozessstreuung (6σ)
- Cp = (Obere Toleranzgrenze - Untere Toleranzgrenze) / (6 × Standardabweichung)
- Berücksichtigt nicht die Lage des Prozesses zur Toleranzmitte
- Cpk (kritischer Prozessfähigkeitsindex):
- Berücksichtigt zusätzlich die Lage des Prozesses zur Toleranzmitte
- Cpk = min[(Obere Toleranzgrenze - Mittelwert), (Mittelwert - Untere Toleranzgrenze)] / (3 × Standardabweichung)
- Ist immer kleiner oder gleich Cp
Typische Anforderungen an die Prozessfähigkeitsindizes sind:
- Cp, Cpk ≥ 1,33 für bestehende Prozesse
- Cp, Cpk ≥ 1,67 für neue Prozesse in kritischen Anwendungen
- Cp, Cpk ≥ 2,0 für Prozesse mit Sicherheitsrelevanz
In der Automobilindustrie werden oft noch höhere Anforderungen gestellt, bis hin zu Prozessfähigkeitsindizes von 2,0 und darüber, insbesondere für sicherheitskritische Merkmale.
Qualitätsregelkarten als zentrales SPC-Instrument
Qualitätsregelkarten (auch Control Charts genannt) sind das wichtigste Werkzeug der SPC. Sie visualisieren die Prozessentwicklung über die Zeit und ermöglichen die schnelle Identifikation systematischer Abweichungen.
Grundstruktur einer Qualitätsregelkarte
Eine typische Qualitätsregelkarte besteht aus:
- Einem Mittelwert oder Sollwert (Zentrale Linie)
- Oberer und unterer Eingriffsgrenze (OEG/UEG, meist bei ±3σ)
- Oberer und unterer Warngrenze (OWG/UWG, meist bei ±2σ)
- Den chronologisch eingetragenen Messwerten oder Stichprobenstatistiken
- Zusätzlichen Informationen wie Datum, Schicht, Prozessparametern etc.
Wichtige Typen von Qualitätsregelkarten
Je nach Art der zu überwachenden Merkmale und der gewählten Stichprobenstrategie kommen verschiedene Regelkartentypen zum Einsatz:
- Regelkarten für kontinuierliche Merkmale:
- x̄-R-Karte: Für Mittelwert und Spannweite (bei kleinen Stichproben, n < 10)
- x̄-s-Karte: Für Mittelwert und Standardabweichung (bei größeren Stichproben, n ≥ 10)
- x-MR-Karte: Für Einzelwerte und Moving Range (bei Einzelwertmessungen)
- Regelkarten für diskrete Merkmale:
- p-Karte: Für Anteile fehlerhafter Einheiten (variable Stichprobengröße)
- np-Karte: Für Anzahl fehlerhafter Einheiten (konstante Stichprobengröße)
- c-Karte: Für Anzahl von Fehlern bei konstanter Prüfmenge
- u-Karte: Für Anzahl von Fehlern pro Einheit bei variabler Prüfmenge
Die Wahl des richtigen Regelkartentyps ist entscheidend für die Effektivität der SPC und hängt von der Art des Merkmals, der Produktionsrate und der Stichprobenstrategie ab.
Interpretation von Qualitätsregelkarten
Neben dem offensichtlichen Überschreiten der Eingriffsgrenzen gibt es weitere Muster in Regelkarten, die auf systematische Prozessänderungen hindeuten können. Die wichtigsten sind:
- Trend: Sieben oder mehr aufeinanderfolgende Punkte, die stetig steigen oder fallen
- Verschiebung: Sieben oder mehr aufeinanderfolgende Punkte auf einer Seite der Mittellinie
- Alternation: Vierzehn oder mehr Punkte, die regelmäßig auf und ab schwanken
- Stratifikation: Fünfzehn oder mehr aufeinanderfolgende Punkte innerhalb der 1σ-Zone um die Mittellinie
- Zwei von drei Punkten: Zwei von drei aufeinanderfolgenden Punkten außerhalb der 2σ-Warngrenzen
Diese Muster, auch als "Western Electric Rules" oder "Nelson-Regeln" bekannt, helfen bei der frühzeitigen Erkennung systematischer Veränderungen, bevor diese zu Überschreitungen der Eingriffsgrenzen führen.
Typische SPC-Kennzahlen und ihre Bedeutung
Neben den bereits erwähnten Prozessfähigkeitsindizes Cp und Cpk gibt es weitere wichtige Kennzahlen in der SPC:
Kurzzeitprozessfähigkeit (Cm, Cmk)
Diese Indizes beschreiben die Prozessfähigkeit unter optimalen Bedingungen über einen kurzen Zeitraum:
- Cm (Machine Capability): Äquivalent zu Cp, aber für Kurzzeitbetrachtung
- Cmk (kritische Machine Capability): Äquivalent zu Cpk, aber für Kurzzeitbetrachtung
Die Kurzzeitfähigkeit wird typischerweise bei der Maschinenabnahme oder Prozessvalidierung verwendet.
Langzeitprozessfähigkeit (Pp, Ppk)
Diese Indizes berücksichtigen die Prozessleistung über einen längeren Zeitraum unter realen Produktionsbedingungen:
- Pp (Process Performance): Äquivalent zu Cp, aber für Langzeitbetrachtung
- Ppk (kritische Process Performance): Äquivalent zu Cpk, aber für Langzeitbetrachtung
Die Differenz zwischen den Kurz- und Langzeitindizes gibt wichtige Hinweise auf die Prozessstabilität. Eine große Differenz deutet auf erhebliche Schwankungen im Prozess hin, die untersucht werden sollten.
First Pass Yield (FPY)
Der First Pass Yield gibt an, wie viel Prozent der produzierten Einheiten beim ersten Durchlauf alle Qualitätsprüfungen bestehen:
- FPY = (Anzahl fehlerfreier Einheiten / Gesamtanzahl produzierter Einheiten) × 100%
Ein hoher FPY-Wert ist ein Indikator für einen stabilen und fähigen Prozess.
Overall Equipment Effectiveness (OEE)
Der OEE ist eine übergreifende Kennzahl, die die Gesamteffektivität einer Produktionsanlage beschreibt:
- OEE = Verfügbarkeit × Leistung × Qualität
- Ein OEE von 85% oder höher wird oft als Weltklasseniveau angesehen
Die SPC trägt durch die Verbesserung der Qualitätsrate direkt zur Steigerung des OEE bei.
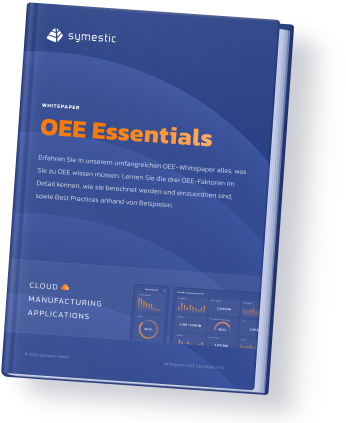
Implementierung von SPC im Produktionsumfeld
Die erfolgreiche Implementierung von SPC erfordert einen strukturierten Ansatz und die Berücksichtigung verschiedener Faktoren:
1. Vorbereitende Maßnahmen
- Prozessanalyse: Identifikation kritischer Prozesse und Parameter
- Prüfplanerstellung: Festlegung von Prüfmerkmalen, -häufigkeiten und -methoden
- Messsystemanalyse (MSA): Sicherstellung der Mess- und Prüfmittelfähigkeit
- Schulung der Mitarbeiter: Vermittlung der SPC-Grundlagen und praktischen Anwendung
2. Pilotimplementierung
- Auswahl geeigneter Pilotprozesse mit hohem Verbesserungspotenzial
- Sammlung von Ausgangsdaten (Baseline) zur späteren Erfolgsmessung
- Erstellung und praktische Erprobung der Qualitätsregelkarten
- Feinjustierung der Stichprobenstrategien und Eingriffsgrenzen
3. Standardisierung und Ausweitung
- Dokumentation der erprobten SPC-Verfahren in Arbeitsanweisungen
- Schrittweise Ausweitung auf weitere Prozesse und Bereiche
- Integration in bestehende Qualitätsmanagementsysteme
- Einrichtung regelmäßiger Reviews zur Überwachung der SPC-Effektivität
4. Kontinuierliche Verbesserung
- Regelmäßige Überprüfung der SPC-Prozesse und -Parameter
- Analyse der gesammelten Daten zur Identifikation von Verbesserungspotentialen
- Anpassung der Prüfpläne an veränderte Prozessbedingungen
- Weiterbildung der Mitarbeiter zu fortgeschrittenen SPC-Themen
Eine erfolgreiche SPC-Implementierung erfordert sowohl technisches Know-how als auch kulturelle Veränderungen in der Organisation. Die aktive Unterstützung durch das Management und die konsequente Einbindung der Mitarbeiter sind entscheidende Erfolgsfaktoren.
Herausforderungen und häufige Fehler bei SPC
Trotz der weitreichenden Vorteile gibt es bei der Implementierung und Anwendung von SPC einige typische Herausforderungen und Fallstricke:
1. Messystem-bezogene Probleme
- Ungeeignete Messmittel: Zu geringe Auflösung oder Genauigkeit der Messgeräte
- Fehlende Messsystemanalyse: Keine Validierung der Mess- und Prüfmittelfähigkeit
- Inkonsistente Messmethoden: Unterschiedliche Vorgehensweisen bei der Messung
- Fehlerhafte Kalibrierung: Nicht oder falsch kalibrierte Messgeräte
2. Stichproben-bezogene Probleme
- Zu kleine Stichproben: Führen zu geringer statistischer Aussagekraft
- Nicht repräsentative Stichproben: Systematische Verzerrung der Ergebnisse
- Ungeeignete Stichprobenintervalle: Zu seltene oder zu häufige Probenahme
- Fehlende Rückverfolgbarkeit: Keine Zuordnung zu Produktionschargen oder -parametern
3. Statistische Fehler und Fehlinterpretationen
- Falsche Regelkartentypen: Verwendung ungeeigneter Regelkarten für die jeweilige Anwendung
- Falsch berechnete Eingriffsgrenzen: Führt zu übermäßigen oder unzureichenden Prozesseingriffen
- Ignorieren von Mustern: Fokus nur auf Überschreitungen der Eingriffsgrenzen
- Überinterpretation zufälliger Schwankungen: Unnötige Prozesseingriffe bei normalen Schwankungen
4. Organisatorische und kulturelle Hindernisse
- Mangelndes Management-Commitment: Unzureichende Unterstützung durch die Führungsebene
- Widerstand gegen Veränderung: Ablehnung neuer Methoden durch die Mitarbeiter
- Unzureichende Schulung: Fehlende Kenntnisse der SPC-Prinzipien und -Anwendung
- Isolierte Betrachtung: SPC als separate Initiative statt als integraler Bestandteil des QM-Systems
5. Technische und Ressourcen-Herausforderungen
- Unzureichende IT-Infrastruktur: Fehlende Systeme zur Datenerfassung und -analyse
- Personalmangel: Zu wenig Personal für die Durchführung der SPC-Aktivitäten
- Zeitdruck: Vernachlässigung der SPC-Aktivitäten bei hoher Produktionsauslastung
- Inkompatible Systeme: Keine Integration mit anderen Systemen wie ERP oder MES
Die Überwindung dieser Herausforderungen erfordert einen ganzheitlichen Ansatz, der sowohl technische als auch organisatorische Aspekte berücksichtigt.
SPC in der Industrie 4.0 – Digitalisierung und Echtzeit-Analyse
Die digitale Transformation und die Prinzipien der Industrie 4.0 eröffnen neue Möglichkeiten für die Anwendung von SPC:
1. Automatisierte Datenerfassung
- Inline-Messtechnik: Direkte Integration von Messsystemen in die Produktionslinien
- Sensor-Netzwerke: Umfassende Erfassung von Prozessparametern in Echtzeit
- IoT-Geräte: Vernetzte Messgeräte und -systeme für kontinuierliche Datenerfassung
- Barcode- und RFID-Technologie: Automatische Erfassung von Produkt- und Chargendaten
Diese Technologien eliminieren manuelle Eingabefehler und ermöglichen eine 100%-Kontrolle statt Stichprobenprüfung.
2. Fortschrittliche Analysemethoden
- Big Data Analytics: Analyse großer Datenmengen zur Identifikation komplexer Zusammenhänge
- Machine Learning: Selbstlernende Algorithmen zur frühzeitigen Erkennung von Anomalien
- Multivariate SPC: Überwachung mehrerer Prozessparameter und ihrer Wechselwirkungen
- Predictive Quality: Vorhersage von Qualitätsproblemen vor ihrem Auftreten
Diese Methoden gehen über die klassische univariate SPC hinaus und ermöglichen ein tieferes Verständnis der Prozesse.
3. Cloud-basierte SPC-Systeme
- Standortübergreifende Analyse: Vergleich und Optimierung von Prozessen über mehrere Standorte
- Skalierbare Rechenleistung: Bewältigung großer Datenmengen ohne lokale IT-Infrastruktur
- Echtzeit-Dashboards: Aktuelle Qualitätsdaten jederzeit und überall verfügbar
- Automatische Updates: Stets aktuelle Analysemethoden und -tools
Cloud-Lösungen ermöglichen eine flexiblere und kosteneffizientere Implementierung von SPC.
4. Integration in die digitale Fabrik
- Vernetzung mit MES und ERP: Nahtloser Datenaustausch zwischen allen Systemen
- Digital Twin: Virtuelle Modelle der Produktionsprozesse für Simulation und Optimierung
- Geschlossene Regelkreise: Automatische Prozessanpassungen basierend auf SPC-Ergebnissen
- Mobile Anwendungen: SPC-Informationen und -Alarme auf mobilen Endgeräten
Diese Integration ermöglicht eine durchgängige Qualitätssteuerung vom Shopfloor bis zur Managementebene.
Wirtschaftliche Vorteile durch SPC
Die konsequente Anwendung von SPC führt zu messbaren wirtschaftlichen Vorteilen:
1. Kostenreduktion
- Verringerung von Ausschuss und Nacharbeit um 20-50%: Durch frühzeitiges Erkennen von Prozessabweichungen
- Reduzierung von Kundenbeanstandungen um 30-60%: Durch verbesserte Produktqualität
- Senkung der Prüfkosten um 10-30%: Durch optimierte Stichprobenpläne und effizientere Prüfprozesse
- Verringerung von Gewährleistungs- und Haftungskosten: Durch verbesserte Produktqualität und -sicherheit
2. Produktivitätssteigerung
- Erhöhung der Maschinenauslastung um 5-15%: Durch weniger ungeplante Stillstände
- Steigerung des First Pass Yield um 10-25%: Durch stabilere Prozesse
- Verkürzung der Durchlaufzeiten um 10-20%: Durch weniger Nacharbeit und Wiederholungsprüfungen
- Optimierung von Rüst- und Einstellprozessen: Durch besseres Verständnis der Prozessparameter
3. Strategische Vorteile
- Verbesserte Kundenzufriedenheit: Durch höhere Produktqualität und Liefertreue
- Stärkere Marktposition: Durch Differenzierung über Qualität
- Erfüllung von Kundenanforderungen: Nachweis der Prozessfähigkeit für Automotive und andere anspruchsvolle Branchen
- Bessere Erfüllung regulatorischer Anforderungen: Dokumentierte Prozessbeherrschung für Audits und Zertifizierungen
Die wirtschaftlichen Vorteile von SPC übersteigen die Implementierungskosten in der Regel deutlich, mit typischen ROI-Zeiten von 6-18 Monaten je nach Anwendungsbereich und Ausgangssituation.
Best Practices für nachhaltige SPC-Implementation
Für einen langfristigen Erfolg mit SPC haben sich folgende Best Practices bewährt:
1. Strategie und Planung
- Ausrichtung an Unternehmenszielen: Integration von SPC in die Qualitäts- und Geschäftsstrategie
- Priorisierung kritischer Prozesse: Fokus auf Prozesse mit hohem Einfluss auf Produktqualität und Kosten
- Definierte Implementierungsroadmap: Strukturierter, phasenweiser Ansatz mit klaren Meilensteinen
- Messbaren Erfolgsmetriken: Dokumentation des Status quo und Festlegung von Zielen
2. Technische Umsetzung
- Sorgfältige Messsystemanalyse: Validierung aller Mess- und Prüfmittel vor SPC-Implementierung
- Angemessene Stichprobenstrategie: Balance zwischen statistischer Aussagekraft und Aufwand
- Geeignete Regelkartentypen: Auswahl basierend auf Merkmalsart und Produktionsbedingungen
- Regelmäßige Überprüfung der Eingriffsgrenzen: Anpassung bei Prozessverbesserungen oder -veränderungen
3. Organisatorische Aspekte
- Aktives Management-Commitment: Sichtbare Unterstützung durch die Führungsebene
- Umfassende Mitarbeiterschulung: Vermittlung sowohl der Theorie als auch der praktischen Anwendung
- Klare Verantwortlichkeiten: Definition von Rollen und Zuständigkeiten für SPC-Aktivitäten
- Regelmäßige SPC-Reviews: Überprüfung der Wirksamkeit und Anpassung bei Bedarf
4. Kulturelle Aspekte
- Förderung einer datenbasierten Entscheidungskultur: Entscheidungen auf Basis von Fakten statt Vermutungen
- Etablierung einer Fehlerkultur: Fokus auf Prozessverbesserung statt Schuldzuweisung
- Einbindung der Mitarbeiter: Nutzung ihres Prozesswissens bei der SPC-Implementierung
- Kommunikation von Erfolgen: Sichtbarmachung der durch SPC erzielten Verbesserungen
5. Technologische Integration
- Skalierbare SPC-Software: Auswahl einer Lösung, die mit dem Unternehmen wachsen kann
- Integration in bestehende Systeme: Anbindung an MES, ERP und andere relevante Systeme
- Automatisierung der Datenerfassung: Reduzierung manueller Eingaben wo möglich
- Benutzerfreundliche Visualisierung: Dashboards und Reports für verschiedene Zielgruppen
Die Beachtung dieser Best Practices erhöht die Erfolgswahrscheinlichkeit von SPC-Initiativen signifikant und fördert deren nachhaltige Verankerung im Unternehmen.
Fazit: SPC als strategischer Erfolgsfaktor
Die Statistische Prozesskontrolle ist weit mehr als nur ein Qualitätswerkzeug – sie ist ein strategischer Ansatz zur Prozessoptimierung, der messbare wirtschaftliche Vorteile bietet:
- SPC ermöglicht die frühzeitige Erkennung von Prozessabweichungen, bevor diese zu Qualitätsproblemen führen
- Sie fördert ein tieferes Verständnis der Prozesse und ihrer Einflussfaktoren
- SPC unterstützt datenbasierte Entscheidungen statt subjektiver Einschätzungen
- Sie schafft die Basis für kontinuierliche Prozessverbesserungen und Effizienzsteigerungen
In Zeiten zunehmender Produktkomplexität, höherer Qualitätsanforderungen und steigenden Kostendrucks wird SPC zu einem entscheidenden Wettbewerbsfaktor. Die Integration moderner Technologien im Rahmen der Industrie 4.0 eröffnet dabei neue Möglichkeiten, SPC noch effektiver und effizienter einzusetzen.
Unternehmen, die SPC konsequent und methodisch korrekt anwenden, profitieren von stabileren Prozessen, höherer Produktqualität und geringeren Kosten – ein Dreiklang, der direkt zur Stärkung der Marktposition und zur langfristigen Unternehmenssicherung beiträgt.
Exklusives Whitepaper
Lernen Sie die modernsten Ansätze der Industrie 4.0, die Sie in Ihrer Produktion schon morgen umsetzen können, um innerhalb von 4 Wochen Ihre Kosten um gut 20% zu reduzieren.
mehr erfahren