Condition Monitoring
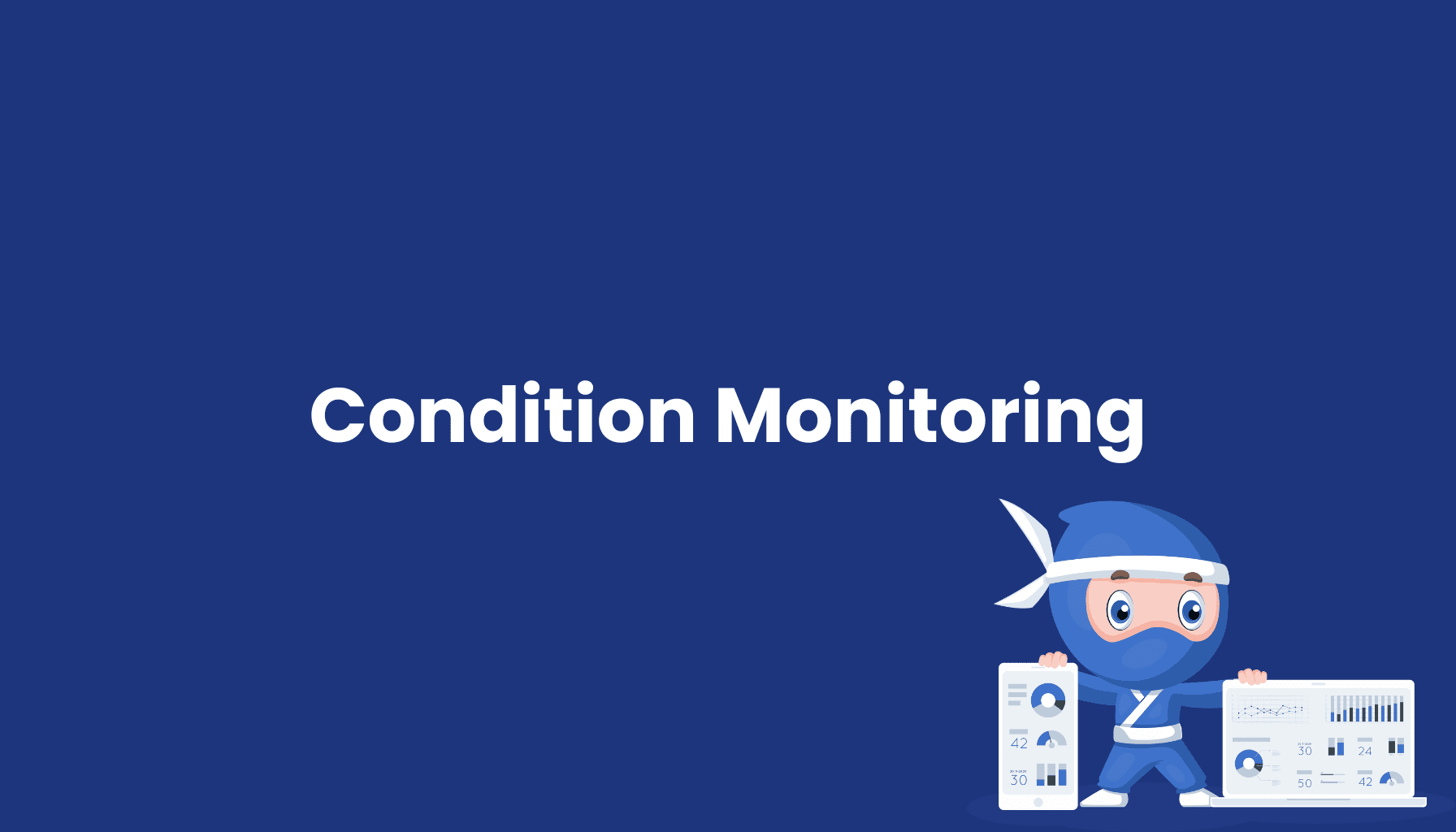
What is Condition Monitoring?
Condition Monitoring refers to the continuous process of monitoring and analyzing the condition of machines and equipment to detect potential issues early, predict failures, and enable preventive maintenance. By leveraging advanced sensor technology and data analytics, companies can monitor critical parameters such as vibrations, temperature, pressure, and more to maintain machine efficiency and minimize downtime.
How Does Condition Monitoring Work?
Condition Monitoring relies on sensor technology to gather real-time data on the operational status of machines. This data is then analyzed using sophisticated monitoring systems and algorithms that detect anomalies and deviations from normal operational conditions. When a potential issue is identified, the system can forecast future failures, allowing for proactive maintenance measures that prevent costly breakdowns.
Key Methods in Condition Monitoring
-
Sensor Technology: Sensors measure vital parameters like vibrations, temperature, and pressure, providing crucial data on machine conditions. These sensordata form the backbone of the condition monitoring process.
-
Data Analysis: Collected data is analyzed through advanced algorithms to identify patterns and predict failures, allowing for precise condition monitoring and supporting predictive maintenance strategies.
-
Monitoring Systems: Software solutions, often displayed on dashboards, enable continuous monitoring and provide real-time insights into the state of production assets. These systems consolidate condition data and present actionable information.
-
Diagnostics and Prognostics: Deviations are identified through diagnostic tools, while prognostic systems predict future failures, allowing maintenance processes to be efficiently planned and machine availability to be maximized.
Benefits of Condition Monitoring
-
Reduced Maintenance Costs: By detecting issues early, condition monitoring helps avoid expensive emergency repairs, thereby lowering overall maintenance costs.
-
Increased Equipment Availability: Condition monitoring minimizes unplanned downtime, ensuring that machines are available when needed, thereby enhancing production efficiency.
-
Improved Safety: Continuous monitoring of equipment enhances workplace safety by identifying potential hazards before they result in accidents.
-
Extended Asset Lifespan: Regular monitoring and timely maintenance based on real-time data extend the lifespan of machines and equipment, improving return on investment (ROI).
-
Regulatory Compliance: Condition monitoring assists in ensuring compliance with industry regulations by documenting maintenance activities and performance metrics.
Applications of Condition Monitoring in Industry
Condition Monitoring is a key component of Industry 4.0, where it plays a vital role in integrating IoT and advanced monitoring techniques for comprehensive real-time condition monitoring. Machine builders and operators of production facilities utilize condition monitoring to increase efficiency, ensure safety, and maximize overall productivity. Moreover, it is crucial for predictive maintenance—where maintenance is scheduled based on actual machine conditions rather than on fixed intervals—leading to significant cost savings.