One-Piece Flow
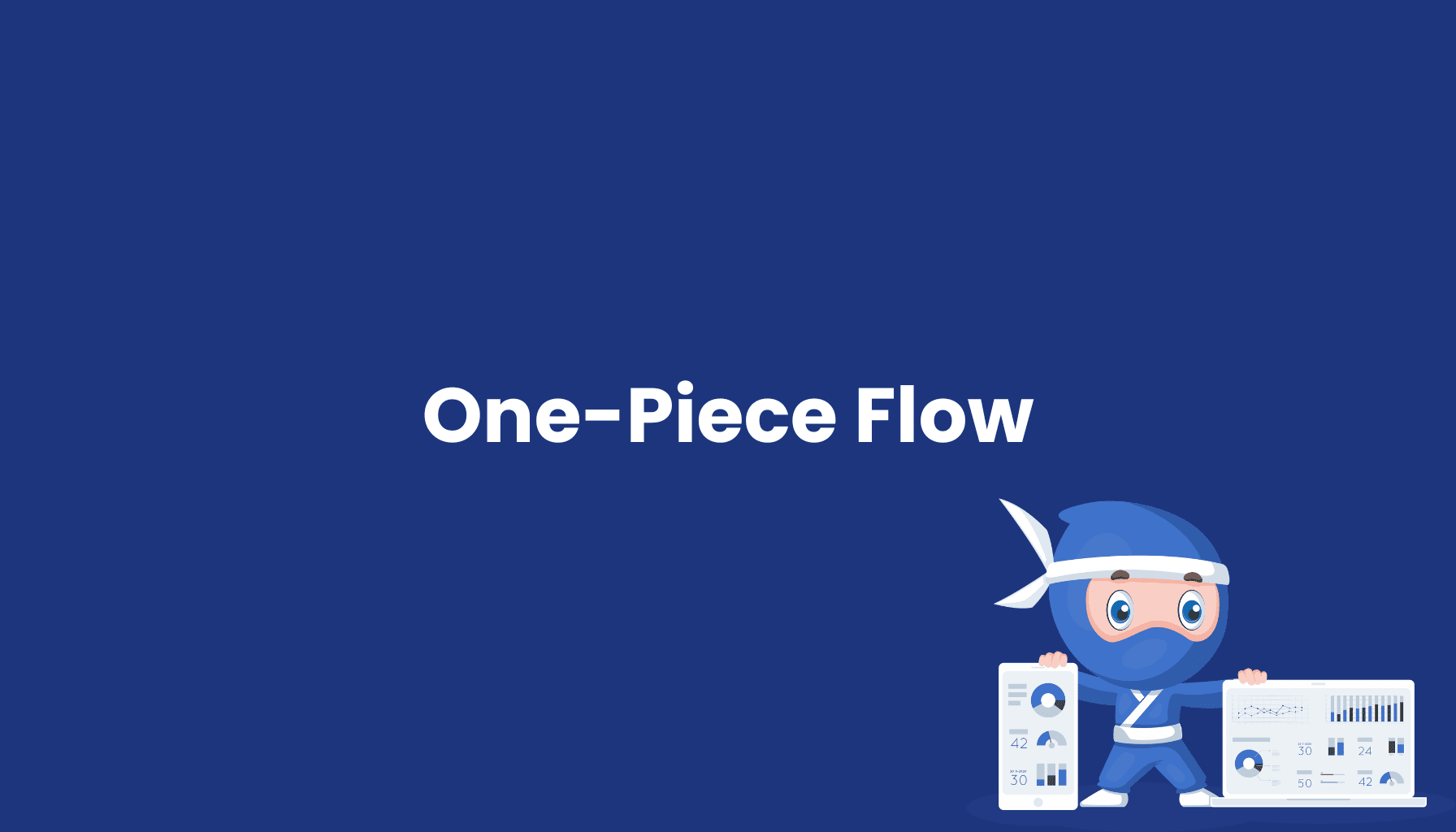
What is One-Piece Flow?
One-Piece Flow is a Lean Management principle that focuses on moving products through the production process individually rather than in batches. The goal is to reduce lead times, minimize inventory, and eliminate bottlenecks in the production line. By shifting from batch production to single-piece production, a more streamlined and efficient production process is achieved.
Key Features of One-Piece Flow
- Single Production: Each product moves individually through the production process. This means that each work step is completed sequentially for each piece before starting the next one.
- Lead Time Reduction: Producing items one by one significantly shortens lead times because products don't need to wait for the completion of entire batches before moving to the next stage.
- Inventory Reduction: As products are processed immediately, there is less need for large inventory levels, leading to lower stock levels and reduced storage costs.
Advantages of One-Piece Flow
- Increased Efficiency: Continuous production of single units reduces the downtime between different production stages, which shortens the overall production time.
- Flexibility: Producing items one at a time allows companies to quickly adapt to changes in customer demand and adjust production capacity.
- Quality Control: Errors can be detected more quickly since each product can be inspected after every step, leading to better quality control of the finished goods.
Application in the Manufacturing Industry
In the manufacturing industry, One-Piece Flow is particularly useful for making production processes leaner and improving efficiency. This approach can help avoid bottlenecks and ensure optimal use of production capacity. When combined with a Manufacturing Execution System (MES), companies can use real-time data to monitor and optimize the production flow. This integration makes the entire material flow more transparent, leading to better decision-making and a more efficient production process.