Root Cause Analysis (RCA)
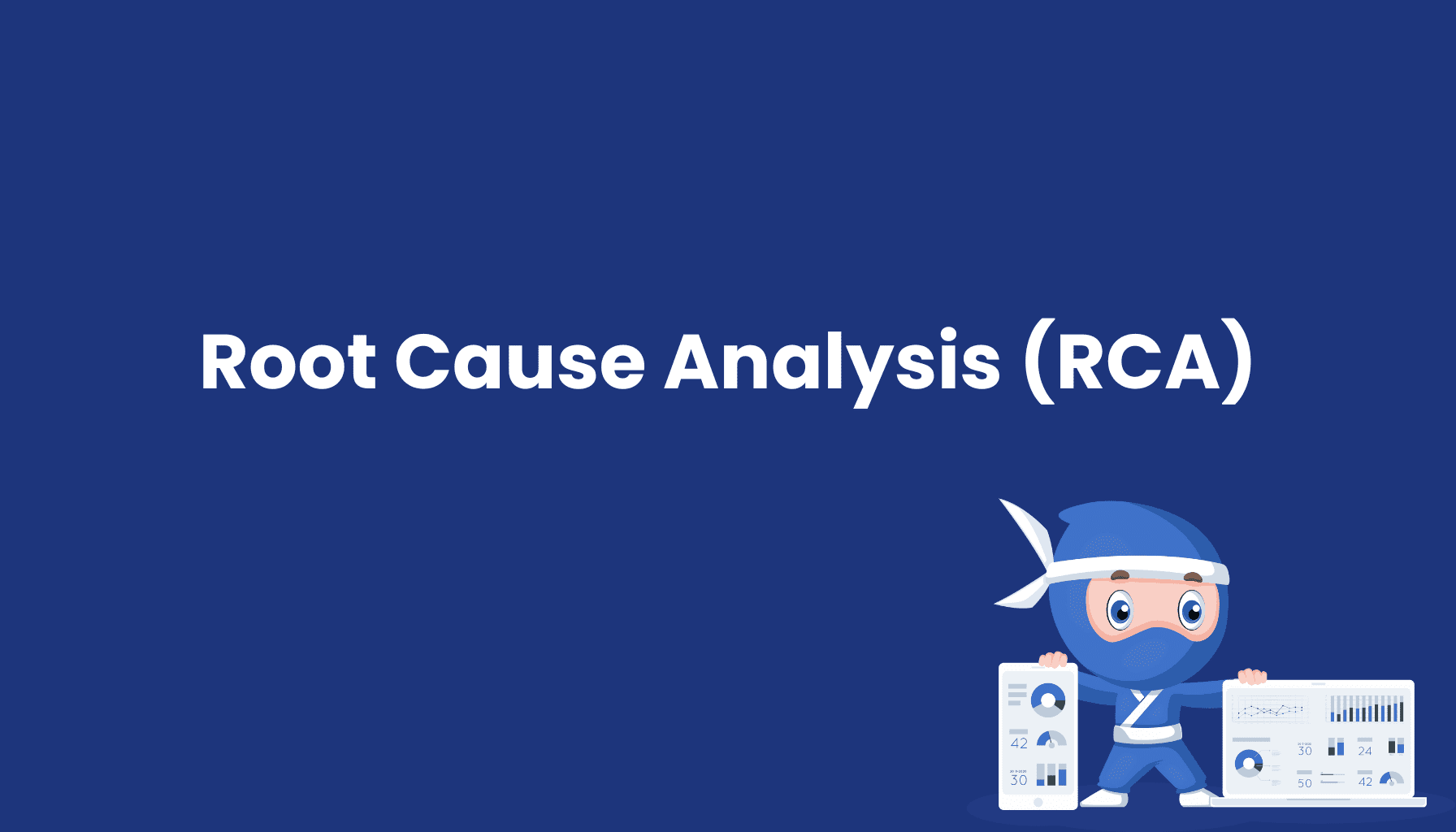
What is Root Cause Analysis (RCA)?
Root Cause Analysis (RCA) is a systematic method for identifying the underlying causes of problems or errors within processes. Rather than merely addressing symptoms, RCA aims to uncover the root causes to prevent future occurrences.
Benefits of Root Cause Analysis
- Permanent Problem Resolution: Eliminates the root causes, preventing recurrence.
- Cost Savings: Reduces costs by minimizing repeated errors and inefficiencies.
- Improved Efficiency: Streamlines processes, boosting productivity.
- Enhanced Quality: Improves product and service quality by addressing the real issues.
Steps in Root Cause Analysis
- Problem Definition: Clearly define the issue to focus the analysis.
- Data Collection: Gather relevant data to identify patterns and causes.
- Cause Identification: Use tools like the 5 Whys or Ishikawa Diagram to pinpoint root causes.
- Solution Development: Create measures to eliminate identified causes.
- Implementation and Monitoring: Apply solutions and continually monitor their effectiveness.
RCA and Overall Equipment Effectiveness (OEE)
Root Cause Analysis is crucial for improving Overall Equipment Effectiveness (OEE) by identifying and eliminating causes of downtime, performance issues, or quality defects. This enhances the availability, performance, and quality of equipment, directly boosting OEE.
Conclusion
Root Cause Analysis (RCA) is an essential tool for sustainable process and product quality improvement. By systematically addressing root causes, businesses can increase efficiency, reduce costs, and enhance customer satisfaction.
Start working with SYMESTIC today to boost your productivity, efficiency, and quality!